Radiant ceiling heating and cooling questions

I’m in the process of designing an addition and complete renovation for my current ranch home. I live in Connecticut and I currently sit on an existing slab on grade with no insulation (1950). I will be adding slabs in both the front and back of the house along with a second floor to a total square footage of roughly 2500 sq. ft. I plan on insulating the old and new slabs with 2″ XPS to 2′ below grade along the entire perimeter.
Since this will be a gut renovation I will be saving some of the existing 2×4 walls while framing the new walls the same. I’ll be putting R-15 in the walls and 1.5″ XPS board on the exterior achieving roughly R-22+. I haven’t decided on which vapor barrier I’ll be using under the rain screen siding yet, most likely Tyvek drainwrap or Prosoco-R guard. I’ll also aim for R-49 at the roof line and floor insulation 1st to 2nd is TBD based on the truss design.
Since I’ve worked through most of the exterior and insulation details I’ve started working on the heating and cooling systems. I’ve been really attracted to the idea of hydronic radiant ceilings, but solid information has been a bit difficult to find on design and technical aspects of the system. The best method of installation I can see is to install a breathable radiant barrier below the floor insulation, stapled to the bottom of truss, bellowed slightly between truss bays to accommodate the aluminum transfer plates and tubes. Has anyone seen a installation similar to this? Would it be typical to cover the entire square footage of the ceiling or just enough to provide the correct heating/ cooling? The only pre-manufactured drywall panels I can find for sale in the U.S. is the Raymagic panels by Messana. I don’t fully trust the panel connection and I’d assume the panel cost would be pretty high compared to the plates and pex piping.
Last question relates to cooling with a radiant ceiling. I know based on humidity radiant cooling isn’t the best option for my area. I would need a full house dehumidifier with possible additional duct work while I’d only planned on some duct work for the HRV. In the interest of keeping costs down is radiant cooling viable as an option? Would I be better off installing a multi zone mini split system? I’m really trying to find the best balance for initial costs vs operating costs for my cooling system.
GBA Detail Library
A collection of one thousand construction details organized by climate and house part
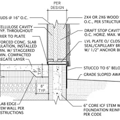
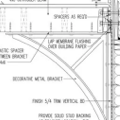
Replies
Radiant ceilings and radiant cooling are definitely "out there" on the edge of what can be done in houses. you aren't finding much information because nobody does this. That's not to say it can't be done, but it's challenging, expensive and very non-standard. Meaning, you're on your own.
Mechanical Engineers are all over radiant cooling for commercial buildings, with chilled beams, radiant ceilings and all sorts of interesting stuff. But these buildings have cooling demand driven primarily by internal heat loads and not latent humidity loads. Humidity is dealt with by dehumidifying, usually in the makeup air system. You can do this in a houst, but it's complicated.
Among other challenges, if you are hoping to put radiant tubing on teh backside of the top floor ceilings, this means that the cold tubing is potentially exposed to hot/wet attic air. That's very bad. If you do this, you MUST encapsulate the radiant tubing in enough closed cell foam insulation to prevent any contact with attic air. Among other things.
Sounds like a fun science project. Let us all know how it turns out.
Usually you’d put radiant heating in a floor, not a ceiling, but I suppose either could be made to work. Radiant cooling in residential settings isn’t really a thing. It isn’t really a thing commercially either — cooling systems using chilled water ususally work with chilled water coils in air handlers, not regular passive radiators. It can be made to work with passive radiators though. I can tell you that cooling with chilled water, which is usually around 42-45 degrees or so, dehumidification doesn’t work very well with out a reheat system (heating the air before it hits the cooling coil to increase the temperature differential). You might make your ceiling sweat, but you’ll end up with a cool, muggy house.
I’ve never seen a residential-size chiller, either, but that’s not to say they don’t exist. The smallest I’ve ever worked with was several tens of tons, most are hundreds or thousands of tons. Chillers aren’t normally used in small plants. If you go with radiant heating, I’d put in something else to handle the cooling load. You could use either a regular air central air setup with an air handler (a blower in a box without any heating function), or possible some mini splits.
BTW, go with polyiso instead of XPS for your rigid foam.
Bill
Building,
First of all, can you tell us your name? (I'm Martin.)
You wrote, "I haven’t decided on which vapor barrier I’ll be using under the rain screen siding yet, most likely Tyvek drainwrap or Prosoco-R guard."
You don't want to install a vapor barrier behind your rainscreen -- you want a water-resistive barrier (WRB). Most WRBs aren't vapor barriers -- they are vapor-permeable.
Q. "In the interest of keeping costs down is radiant cooling viable as an option?"
A. No. For a residential project, "radiant cooling" and "keeping costs down" don't belong in the same sentence.
Here's the standard information that GBA should automatically post when the keyword "XPS" appears in a question--in this case I am copying and pasting Dana's recent good articulation of the issue, edited a bit to match your situation.
XPS is one of the least-green commonly used insulation materials due to the high polymer weight per R and more importantly the HFC blowing agents used (soon to be banned under the Kigali amendment to the Montreal Protocol.) As it loses the HFCs over several decades performance eventually drops to that of EPS of similar density.
Both polyisocyanurate and EPS are blown with comparatively very benign hydrocarbons (usually a pentane variant). Polyiso has a higher R/inch and greener polymer, vut since it can potentially wick moisture it shouldn't be used on the outside of the foundation below grade.
Charlie,
Your suggestion is a good one. Much of the information that you and Dana highlight is also contained in a GBA article, "Choosing Rigid Foam."
Martin sorry about the name I thought I setup my profile, I'm Sean.
Some great information here, thank you. I used the term vapor barrier in a general sense, since that's just what we call it on site, but I'll have to correct that. I work in commercial construction so we address by trade and spec sections which both the interior and exterior moisture protection fall under.
Charlie, I had not considered the manufacturing of XPS vs other forms of rigid insulation. I'll have to dive into that and look at which product is going to work the best in the long run vs. cost vs. environmental considerations. It is very likely that this house will one day be in the hands of my children so I'm taking into consideration the long term.
My initial thought was to install radiant floors, but with the existing slab I'd have to install rigid insulation, tubes and gypcrete which would shrink my floor to ceiling height too much considering existing conditions. I was able to find an article from an architect that built a house in CT about 30 minutes away from me that used the Raymagic panels for heating and cooling recently. It seems like the method they used to control condensation was sensors in every room. That just seems like a head ache and a problem waiting to happen.
I'm trying to avoid forced air heating and cooling for a list of reasons, but most notably is efficiency and my oldest daughters severe allergies to certain types of trees, pollen and mold. We've noticed that houses with forced air tend to make it worse.
Maybe I have to start over and consider other options like Runtal units or hydronic forced air for heating and ducted cooling.
If you're considering the long term, factor in that the blowing agent in XPS gradually leaks out, so that 50 years down the road the effective R-value is more or less the same as EPS.
I’m not so sure about the efficiency advantage to a radiant system. With radiant systems, there is a LOT more complexity and a lot more to tweak to get a system running at peak efficiency. With a forced air system, you have either on or off, or some relatively limited modulation with the newest variable speed units. Hydronic systems have valves, pumps, zones, modulating boilers, thermal storage, and everything needs to be balanced and optimized. I’d bet most hydronic systems are suboptimally designed and/or operated and probably run at an overall efficiency no better than, or even worse than, a typical forced air system.
My wife has chronic sinus issues so I’m familiar with the air quality concerns. Use a higher efficiency filter, at least MERV 13. Aprilaire now has MERV 16 filters that they advertise for “asthema and allergies” and I’ll be replacing my current MERV 13 filters with MERV 16 filters this year. You can also use an electrostatic air filter to get anything that remains after the pleated filter (electrostatic air filters don’t introduce much back pressure to the system).
I would also avoid using any natural fiber carpeting, or any carpeting at all if possible. Synthetic fiber carpets are less prone to produce dust due to the very long polymer chains that make up the synthetic fibers. Try to keep dust to a minimum.
At work, I deal with ventilation systems in datacenter facilities. These systems run the fans continuously and only cycle the cooling part of the system on and off to maintain temperature (there is no need for heat). The result is a constant air turnover and it all goes through the filter. The air in the room is pristine, and there is not dust accumulation anywhere. The filters catch everything. You can do the same thing in your home if you set the blower to run on a cycle regardless of if the heating or cooling functions are needed.
Note that in our facilities at work, most of the dust the filters collect is from paper fibers or dead skin cells. You can do anything about the skin cells since that’s a natural fact of life for people in a building, but if you open packages outside or in a seperate room that makes a big difference in dust buildup. We require our customers to open cardboard boxes in a special room for this reason (a common requirement in the industry).
Bill
Sean,
You wrote, "I'm trying to avoid forced air heating and cooling for a list of reasons, but most notably is efficiency and my oldest daughters severe allergies to certain types of trees, pollen and mold."
Concerning efficiency: A forced-air heating and cooling system can be as efficient as, or more efficient than, a hydronic system. If you install ductless minisplits, you don't have to give up efficiency.
Concerning limiting exposure to allergens like trees, pollen, and mold: The best advice will come from a doctor, not me. That said, what you need to pay attention to are the airtightness of your building envelope, the quality of your ventilation system, and attention to moisture issues. These issues have nothing to do with whether you distribute your heat with ducts or hydronic tubing.
I've always been under the impression from publications and talking with the designers of the various buildings I've worked in that hydronic unless extremely poorly designed will out perform forced air. I realize that commercial systems are different in respect to residential systems but the potential with hydronic should remain the same.
Assuming I pay close attention while sealing the home with R values that would meet climate 5 minimum standards is there a particular heating or cooling system that you see as superior?
>"I've always been under the impression from publications and talking with the designers of the various buildings I've worked in that hydronic unless extremely poorly designed will out perform forced air."
Most of the inefficiency of forced air heat/cool delivery has to do with duct design/implementation and duct losses, and air handler driven outdoor air infiltration. That's not an issue with ductless mini-split, no more lossy than any non-ducted hydro-air console heater.
Duct systems that are well balanced by design (and verified with a manometer to detect room to room pressure differences) and located completely inside the insulation and pressure boundary of a code-minimum tight house aren't very lossy at all. At the low static pressures and low cfm of mini-ducted mini-splits those losses are even smaller than with "full sized" forced air.
>"Assuming I pay close attention while sealing the home with R values that would meet climate 5 minimum standards is there a particular heating or cooling system that you see as superior?"
At the high end a modulating full VRF system with radiant floor heat + domestic hot water and ductless /mini-ducted cooling is arguably "...superior...". In your house your loads (including hot water) would likely be within range of a 3-5 ton LG Multi V S + Hydro Kit.
But a combination of ductless & ducted mini-splits (and no radiant) would probably be a better bang/buck, spending the difference in cost on a slightly better building envelope &/or rooftop PV solar.
A typical 2500' code minimum 2 story house in Hartford would have a design heat load of ~25-30,000 BTU/hr @ +6F and a cooling load of 20-25,000 BTU/hr. A tighter house with slightly better than code-min windows & R values and better thought out slab-on grade design with heat recovery ventilation could come in around 22-24,000 BTU/hr.
A dumb 1 or 2 stage 2-3 ton heat pump with auxiliary heating strips could heat and cool the place, spending the cost difference in mechanical systems on rooftop PV to more than cover the cost difference of more efficient mechanical systems. But if you want steady quiet efficient comfort with some amount of zoning control, a combination of ducted and ductless modulating mini-splits is an upgrade. It comes with an upcharge , but it's arguably "worth it"- more so than the even higher cost of a full-on radiant heating & cooling approach.
Since you're adding a second floor it makes sense to zone it by floor and since the second floor is all new construction you have an opportunity to optimize the design for efficiency, comfort, and if need be, to accommodate ducts completely inside the building envelope.
BTW: Though it might be difficult to retrofit insulate the existing slab, on the new slabs it's cheap and easy to install 2-4" of reclaimed roofing EPS under the slab. There are multiple reclaimers selling used foam board at less than a third the cost of virgin stock goods operating in southern New England, and a few selling factory seconds at half price or less. The biggest is Nationwide Foam/Insulation Depot in Framingham MA, followed by Green Insulation group in Worcester MA, but there are others. (Green Insulation Group usually has range of factory seconds foil faced polyiso in stock, to take some of the wallet-sting out of your wall-foam too.)
Even paying full-freight for virgin stock goods there is a financial and comfort case for 1.5-2" of EPS under the full field of a new slab, not just a code minimum R10 at the slab edge. Your deep subsoil temps are in the low-50s, and even with slab edge insulation the floor is never really warm. At even 1" of EPS the risk of summertime mold growing under rugs, etc goes down without needing to resort to mechanical dehumidification, but it's as much about barefoot comfort in winter than summertime mold.
>" I plan on insulating the old and new slabs with 2″ XPS to 2′ below grade along the entire perimeter."
---
>"I’ll be putting R-15 in the walls and 1.5″ XPS board on the exterior achieving roughly R-22+."
XPS rates at the MOST environmentally damaging insulation material in common use today, largely due to it's HFC blowing agents. And it's labeled R overstates it's performance- it's only warranteed to R4.5/inch (=R9 for your slab insulation, R6.8 for the wall insulation), and even that is higher than the roughly R4.2/inch it will be at full-depletion of the HFCs from the foam.
EPS is blown with MUCH more benign pentane, with less than 0.1% the global warming potential of HFC134A, the primary blowing agent in XPS, and most of the pentane escapes the foam and is recaptured at the factory. EPS has a stable performance over it's lifecyle. It takes 2.5" of EPS to hit the R10 code minimum for your slab edge insulation instead of 2" for the labeled R of XPS but it's R10 now, and will still be R10 in 50 years.
Polyiso is also blown primarily with pentane, not HFCs, and has a higher labeled R/inch than XPS. In your stackup and location it may need to be derated a bit for temperature during the coldest weather, but at 1.5" it will exceed R7.5 even when it's in negative digits outside, and will exceed it's R9 labeled performance during most of the winter and shoulder seasons in a CT location. It can't be used in contact with soil without risking saturation with water over time, but it's great for exterior wall sheathing.
A dehumidifier converts a latent cooling load into sensible heat that would still need to be removed. In CT in a higher-R/lower gain house there many days where the latent load dominates, with almost no sensible load. It would be both cheaper and better to use a mini-split for cooling. Even chilled water coils would have more plumbing to insulate to avoid condensation and dripping while running.
Multiple single zone mini-split sized for the zone loads is usually cheaper and more efficient than multi-split solutions. Fujitsu's xxRLFCD mini-ducted versions are quite flexible, efficient, and powerful (for minit-duct cassettes, anyway)- they can be mounted in an 8-10 square foot "utility closet" (for ease of maintenance) with hard piped ducts in a ceiling utility chase or soffits below ceiling level if need be. A wall coil type cold climate mini-split or two for rooms/zones with sufficiently large loads and a mini-ducted mini-split to serve all the doored off bedroom/office/den spaces is usually more than adequate.
In most cases mini-splits sized for the cooling loads in CT will have enough heating capacity to cover the heating loads of an R13+ R5 code min type house, and your house is/will be slightly better than that. The 1.5 ton Fujitsu 18RLFCD would cover more than half your likely load at -5F, as would a 1.25 ton 15RLS3H wall coil. (There are other wall-coil options that would work.) In competitive bidding that would come in under 10 grand if the duct layout isn't too messy.
To get to the optimal system requires doing a careful room by room Manual-J or ASHRAE load calculation on the "after upgrades" picture, using aggressive rather than conservative assumptions on R-values, air tighness, etc. While single zone mini-splits can modulate over a wide range, efficiency and comfort falls off at anything more than 1.5x oversizing. With multi-splits the line is drawn at 1.2x, due to the smaller modulation range, and higher minimum modulated output (they generally cycle on/off more frequently.)
For ANY heating solution ASHRAE recommends 1.4 x oversize factor for the heat load at the 99% outside design temperature to allow for reasonable recovery rates on overnight setbacks and cover the 25 year Polar Vortex disturbance coldest temps, but for modulating equipment that isn't necessary. With mini-splits it can even be slightly undersized and have pretty good efficiency, even if it means covering teh difference during cold-snap temperature heat load peaks with resistance heating.