Radiant floor heat: Insulation for first floor and basement

Hi There,
We are installing hydronic radiant heat in our (to-be) finished basement subfloor and the first floor above the basement. I have a few questions on best practice for insulation.
1) My plumber says that staple up radiant tubing is fine and we don’t need the heat transfer plates – Is that true or should I insist on them?
2) What is the best way to insulate below staple up radiant heat if there is finished space below it (but space not used nearly as frequently as the main floor)? Another consideration is that the insulation can ideally provide soundproofing simultaneously.
3) We have 4″ of rigid foam planned above stone before we install the radiant and pour the slab. Do I need a plastic vapor barrier above or below the rigid also? If so, how do I deal with rain if that happens during the process? Lastly, do I need to insulate the side of the slab (where it meets the walls) too somehow? We are planning to spray foam the interior slab walls.
Thanks so much for your advice in advance!
Ali
GBA Detail Library
A collection of one thousand construction details organized by climate and house part
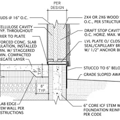
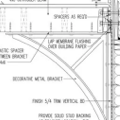
Replies
I'll give you my experience. I did staple up, as a retrofit, and used the transfer plates. Many here will tell you that they are a night/day difference in response time. I cannot speak to that, but it seems logical to me. Not sure what your layout is, but I'd recommend two runs per joist bay to minimize heat "striping" in the floor above. If you're running a lower temp in this zone, plates will definitely be valuable to your satisfaction.
For insulation I purchased radiant barrier foil and cut it into 17" wide strips and stapled it to the underside of the subfloor. Then I installed fiberglass batts in the remaining joist depth.
The insulation isn't necessary from a heat loss perspective, but I justified the expense by knowing that the floor would respond faster, result in a more even warmth to the floor, and I would only be heating the area i wanted heated, rather than a different zoned area of the house.
1) My plumber says that staple up radiant tubing is fine and we don’t need the heat transfer plates – Is that true or should I insist on them?
Heat transfer plates are recommended . Conduction is King and suspended or w/o plates will require higher water temps , less efficient . Will also eventually stripe hardwood floors if that's what you are using .
2) What is the best way to insulate below staple up radiant heat if there is finished space below it (but space not used nearly as frequently as the main floor)? Another consideration is that the insulation can ideally provide soundproofing simultaneously.
The more R value , the less downward loss . More heat to the room and faster . R13 minimum , I suggest R19 however and use something like Roxul Safe and sound .
3) We have 4″ of rigid foam planned above stone before we install the radiant and pour the slab. Do I need a plastic vapor barrier above or below the rigid also? If so, how do I deal with rain if that happens during the process? Lastly, do I need to insulate the side of the slab (where it meets the walls) too somehow? We are planning to spray foam the interior slab walls.
I would place the vapor barrier on top of the foam . In case of rain and retention you'll be able to use a pump to remove bulk moisture . You absolutely need edge insulation unless your slab is decoupled from the wall .
Thanks so much for the response, Pete. We're in Vermont Zone 6. Your solution seems to make sense. I was thinking of doing something similar but with blown in cellulose instead of fiberglass as I thought that would help more with airborne noise transfer (the finished basement space below will be an accessory unit).
"I was thinking of doing something similar but with blown in cellulose instead of fiberglass as I thought that would help more with airborne noise transfer (the finished basement space below will be an accessory unit)."
I used batt insulation because I wanted to be able to get at the underside of the floor in the future (I also installed a drop ceiling) without a major mess, and cellulose would be messy.
I've used Rock wool (fka Roxul) with great results for sound-attenuation. I think the Comfort-batt has better insulating capabilities than Safe-n-Sound, for the same sound attenuation qualities, but I could be wrong.
Heat transfer plates (even the inexpensive stamped sheet metal versions) improve the amount of heat you can get through the floor at any given water temperature. There are many staple-ups without plates that are under-designed and can't quite heat the space even with 180F water, other houses that can get there with suspended tube and 120F water.
What is the design heat load and square footage of the space being heated with the staple up?
What are you using for a heat source?
There needs to be at least some insulation between the subfloor and basement space as zone isolation, otherwise heat from the radiant for the floor above can overheat the basement under some weather conditions. If there are heat transfer plates R13-R19 fiberglass snugged up to the subfloor, in contact with the plates is the way to go. With no heat transfer plates it needs a gap to limit temperature striping on the surface of floor above that would be dead-obvious in bare feet on a cold day.
The slab will need a continuous vapor barrier place above the foam. Placing it above the foam avoids potential moisture reservoir pockets from forming on top of the vapor barrier (which could damage finish floors if there's a lot of trapped liquid water), and keeps the foam from "iceberging", floating up and sticking out of the concrete during the pour.
Thanks to everyone that replied. When I asked for the heat transfer plates, my plumber is insisting that the manufacturer specs that they're not needed.
His response: "The only time we use the heat transfer plates is when we cannot get the amount of tubing required to heat the space. We install our radiant on 1” hangers with a 1” air space between the tubing and the required R-19 non faced insulation. This is the installation method specified by the manufacturer. We will be installing our tubing on 8” centers. We also use 1/2 “ tubing instead of the typical 3/8 tubing that is used with the plates, as the lager tubing has a greater BTU output than the smaller size. "
Do you think he's just trying to cut costs on his bid?
Thanks,
Ali
Statements such as
" We also use 1/2 “ tubing instead of the typical 3/8 tubing that is used "
...are counter to my experience. Almost all plated radiant designs I've seen used 1/2" tubing to allow longer loop lengths.
Again, what is the heat source for the water, and what are the heat loads?
Also what manufacturer was being referred to in the statement:
"We install our radiant on 1” hangers with a 1” air space between the tubing and the required R-19 non faced insulation. This is the installation method specified by the manufacturer."
The manufacturer of what? The tubing clips? The tubing?
If the tubing is EPDM (Onix, etc) and not PEX, the tubing type has a pretty lousy track record with class action lawsuits going back to the 1990s. The manufacturers claim they've fixed the problems, but there are still reported instances of "mystery goop" messing up boiler heat exchangers and pumps on systems installed after the alleged fixes. It's easy to work with, installs more quickly than stiffer PEX tubing, but I'd be reluctant to install it in my house. YMMV.
As usual Dana you are correct . No manufacturer of radiant systems , tubing recommends a suspended tube application , they only list suspended tube as an application for those that are more interested in first cost than anything most people who want radiant are looking for . You know , COMFORT , Control , increased equipment efficiency .
I attached 2 reports , same building , same Insulation , same conditions . 1 is the proposed installation and the other is with Plates , you can see the difference .
Ali , you should read , " Plateless in Radiantville " article by John Siegenthaler . Your contractor seems more concerned with getting less of your money than steering you in the proper direction and if this is not his motivation he plain and simple has no idea why radiant is done in the first place and you might want to seriously consider finding another installer who actually gets it . Try HeatingHelp's , Find a contractor feature .
Ali,
Heat transfer plates make a big difference in the amount of heat you get. The two things to watch for:
-nails. Existing and future flooring nails as any touching the pipe will cause trouble (less of a problem with extruded heat plates)
-squeaky pex (lot of 02 barrier pex), these make a lot of noise unless you are running outdoor reset
I've found a nice in-between is the clip on heat transfer plates (Ultrafin). You don't get as much heat out as with the nail up plates but much better then staple up. It also avoids the issues with nails.
For insulation, any batt insulation works both for both heat and sound, just go with the cheapest. Safe and sound is slightly better for sound but slightly less R value (~R12) then regular Rockwool.
Hi Akos,
Sorry for my lack of knowledge here but can you explain more about what 02 barrier pex is and what outdoor reset is? Thanks so much!
O2 barrier pex has a special layer to keep oxygen out. This is needed otherwise the components made from steel will corrode. Typically this is what is used for heating pipes.
The issue is some of the pex pipe has this layer on the outside, which makes it squeaky. You can test by grabbing a piece of pipe and rubbing it against a wood stud. If it squeaks, then you have to be careful with routing (bushings, clips) otherwise it will make noise as your heat cycles.
Outdoor rest is a system to match the water temperature to the houses heat load. This means your heat will cycle less and heat will be more even. The side benefit is the water in the pipes stays at a constant temperature, no temperature change, no expansion noises.
P.S. I have a feeling that your boiler is oversized for your house. My gut feel is that the lowest fire on it is well above your house heat load.
Hey Akos, Thanks so much for this info. Judging by my plumber's carefulness thus far, I would doubt he is careful on the pex selection but I will verify to be sure. He is saying it will be the uponor pex-a. I haven't yet found where/if it specifies that later you reference.
As for the boiler, it will be supplying our hot water also (for 3 baths - including the basement accessory apartment that will be rented), so I think that is why the capacity is so big. Do you think that's an issue? Thanks again! Ali
Ali,
150k instant combi is a bit small for 3 baths. You probably ok with low flow shower heads, but closer to 200k is better.
For sure your 3rd floor baseboard loop is too small for the min output of the Bosh 150. If that is zoned separately, the boiler will short cycle (bad for efficiency and durability).
The options are either go with the 150/low flow shower heads and add a buffer tank on the house heat side to reduce cycling, or go with the Bosch 100 and add a buffer tank on the DHW side. The Bosch 100 is still too large for your heat loads, but if you combine the 1st and 2nd into a single zone, it might get by.
To actually figure out what would work, somebody needs to do a heat loss calc. Without it, it is all just guessing.
P.S. For a 3 unit rental, I use a 200kbtu tankless for DHW. and heat. The min fire on it is 15k, which is much better for smaller zones.
Uponor HePex (pex A) has the o2 barrier applied inside and outside the tubing , for sure
Thanks so much everyone for all the extremely helpful ideas and advice.
To answer some of the above questions: the planned heat source will be a Bosch Greenstar 151 combination heat/hot water boiler and the planned tubing is wirsbo heat pex by uponor. Can you use any brand/type of heat transfer plates that fit the standard 1/2" tubing? We will have engineered hardwood floors above that will have a combo or glue/staple (I assume), unless we could glue only to keep out the nail risk??
I'm unfortunately not sure of the heat load, but the house will have spray foam r50 in the roof, r25 in the walls above grade and r15 on the below grade cement walls.
Basement finished square footage is about 750 (slab radiant with rigid underneath and tile flooring), first story 1150 ft2 with engineered hardwoods, and third story bedroom area 820 square feet with baseboard hot water. All new double pane argon windows.
Is the Bosch Greenstar 151 already installed? (Hopefully not.)
That combi boiler (and most other combi-boilers) are at once too much (heating boiler) and not enough (hot water). Even the 36,000 BTU/hr minimum firing rate of the Greenstar 151 is nearly the entire heat load of my sub-code 2400' antique 2x4 framed house (+1600' basement) at 0F outdoors, and would short cycle like crazy at condensing water temperatures on zone calls unless there were a lot of thermal mass in the radiation (which you don't have with a staple-up or baseboard). Combi boilers usually only make sense in houses with low to moderate hot water needs, but a large space heating load. A high-R house has a low heating load, and at the 137, 500 BTU/hr high fire the Greenstar 151 won't support more than one low-flow shower at a time with any margin.
Read this bit o' bloggery for the napkin-math version of why a low mass boiler with a minimum firing rate of 36,000 BTU is almost certainly a bad fit for your house:
https://www.greenbuildingadvisor.com/article/sizing-a-modulating-condensing-boiler
There are boilers out there that modulate to well under 10,000 BTU/hr that would probably be more appropriate. Without a heat load calculation and a more complete description of your radiation, zone by zone (how many feet of baseboard?), there's no telling what makes the most sense for your house. The likely heat load of your better than code house is probably under 25,000 BTU/hr @ 0F outdoors, and could even be under 20K. Your 0utside design temp could be warmer than that (where are you?) which would also lower the load numbers.
Thank you so much Dan. Wow, it's crazy how much I took for granted when talking to the plumber/HVAC guys around here (Burlington, VT). I've worked with 4-6 and not one of them has mentioned a manual J calculation. I guess I naively assumed that they knew what they were doing and would make the best choice.
The Bosch is not yet installed but he was planning to start at the end of the week. I sent him a message yesterday to not purchase anything yet! My other quote from the competitor came in for a NTI TX 151c, but again, I'm not sure if that is better as I doubt that he did any calculations.
I'm not certain of the 3rd story (816 ft2) baseboard length since they didn't specify, but it's 2 small bedrooms (9'x11'), two small/medium baths, and a master bedroom that is about 18'x14' with a walk-in closet. I would assume that he would do something like 6' of baseboard in each small bed, a 3' in the baths and then another 8' in the master?
The 1st floor will be very open floor plan (the radiant floor) but with R25 walls and energy efficient windows (and some south solar gain).
The basement will have radiant also, very few windows, and r15 below grade and r25 below grade (all insulation will be closed cell foam).
Should I try a calculator online? I did a quick search online for someone that does these calculations in the Burlington area and didn't find one. Is this calculation work a service that you can use an out-of-state contractor for?
Thanks again SOOO much for your help. While it's overwhelming to find this out now, I'm very happy that I did it while there is time to act vs be stuck with the wrong system.
Best,
Ali
The NTI TX 151c has a minimum firing rate of 18,900 BTU/hr, so it's a better choice than the Bosch, but still not a great fit. (No low-mass combi heaters are.) To run the top floor zone with that boiler without any cycling on/off at condensing water temperatures would take about 90 feet of baseboard, but that's better than the 175' or so it would take with the Bosch.
With some tweaking of the setup parameter cycling could be tamed to at least not short-cycle with as little as 60' of baseboard (NTI) or 115' (Bosch), but with a Navien NHB-055 (or -080) or HTP UFT-080W it would only take 35-40' of baseboard to run the zone at condensing temperaures without cycling. But those aren't combi-boilers- it would need an indirect fired water heater for the domestic hot water.
The easiest quickest online calculator that delivers consistent results (but still overshoots reality) is loadcalc.net. With that tool be aggressive on R-value assumptions, and assume that the house is super-tight (even if it's not) to get close. (They use the 99% outside design temp for the Burlingon airport, which is -6F.)
When I went to get a quote for a boiler for my home renovation, all 3 guys wanted to measure the length of baseboard in the house.
[sigh]
I like and respected the last guy, who had worked for me before. I told him the model number of the boiler he was going to install, end of story. I still ended up with an oversized boiler, because we got to do more insulation than I thought we were going to do, and because I didn't have the guts to go with the lowest firing rate available.
You plumber is not a great heating guy. Get used to doing research and telling people what they are going to do. It is your house
this site is a great resource, but specifically on hydronic heating issues, try heatinghelp.com, they can point you in the right direction
>"When I went to get a quote for a boiler for my home renovation, all 3 guys wanted to measure the length of baseboard in the house."
That's a GOOD thing- very important for the heating system design. Without the zone by zone baseboard lengths you can't predict the firing rate at which it will short cycle the boiler at condensing water temps. But it's not the ONLY thing for sizing the boiler.
No, no it is not
It is about sizing the boiler, a very neanderthal way of determining boiler size
besides the fact that the house was radiated for 1 inch of foam in the roof, 800 sq ft of single pane glass, and R11 walls
I am sure you are thinking as part of a proper system design one needs to know feet of baseboard. After a manual J, after sizing a boiler.
In a retrofit situation when an installer walks in and wants to measure the feet of baseboard, it means one thing, he is intending to size the boiler by reversing the radiator output to deduce the 'proper' size for a boiler.
It is the only thing they will do, and there are still far, far too many who operate this way
>"It is about sizing the boiler, a very neanderthal way of determining boiler size"
Not at all- it's an ESSENTIAL aspect of sizing the boiler. Knowing the zone by zone radiation puts an upper bound on what the minimum fire output of the boiler can be. Without knowing that number it's easy to miss the mark.
>"In a retrofit situation when an installer walks in and wants to measure the feet of baseboard, it means one thing, he is intending to size the boiler by reversing the radiator output to deduce the 'proper' size for a boiler.
It is the only thing they will do, and there are still far, far too many who operate this way"
While that is often the case, it's not always the case. Even though 19 out of 20 might be incompetent, they're not ALL idiots.
A COMPETENT installer of modulating condensing equipment needs both the design heat load AND the radiation size to be able to make reasonable proposal. Beyond the minimum firing rate issue they need to determine first if condensing equipment makes any sense at all (without first upgrading the radiation), whether it's sufficiently broken up into zones that it might need a buffer tank or combining some zones, etc.
Seriously, those who DON'T measure up the radiation for at least part of the initial analysis go straight to the back of the line.
Those who measure up the walls & windows for at least some sort of heat load calc, look at the historical fuel use numbers, AND measure the radiation move toward the front of the line.
It doesn't always take a Manual-J to size the boiler, particularly when it's obvious that the load is smaller than the smallest available boilers. But it is always necessary to know the radiation.
All of that said, while I will respectfully listen to the arguments of HVAC contractors, in the end I've learned that I need to run the numbers myself, rather than trust that the contractor in front of me is the 1 in 20 that will actually get it right every time. In at least one instance in the past couple of years, when presented with the "I won't install or support a boiler smaller than xxx in this house" the contractor was informed they wouldn't be installing anything in that house then. Some contractors will listen to the client- the others you don't need to deal with.
Include zoning and even the smaller boilers will short cycle. But add a buffer tank and the over-sizing problems go away (you can use any of the suggested boilers and they won't short cycle even during mild weather).
Ali,
For your application, a better fit is a larger condensing tank water heater for your DHW and heat. You would need to add a plate heat exchanger to feed the house heat. The burner on these is more than large enough for house heat in your case. If you are worried about DHW, you can add controls to disable the floor heat until the tank recovers for larger hot water draws.
This would give you the hot water you need for the three baths and avoid any of the cycling and sizing issues with the combi units. Also there is no limit to minimum zone size, you can zone each floor separately without issues.
Probably the biggest problem is getting a plumber to install it.
Certainly a workable solution, but heating water to say 130F and then mixing it down to say 80F will cause a reduction in efficiency (perhaps 8%).
Jon,
With a condensing device, what matters for efficiency is fire rate and return water temperature. Supply temperature have little effect. You can mix it down all day long without effect.
You can have a tank at 140F and still get rated efficiency as long as the RWT is well into condensing range. This is why it is important to select the right flow rate when using a tank as a heat source.
I agree - say 8+% for the done wrong case and much less when done just right. Some mixing must occur in a tank water heater (certainly when cycling), reducing the amount of exhaust gas cooling (as compared to a condensing tank-less boiler with its perfect counter flow).
Jon,
I would be curious of where the 8% comes from. From my searching, the thing that matter is RWT and even then the efficiency hit is not as drastic:
http://htproducts.com/images/phoenixspecs.jpg
Even a standard power vent water heater gets around 80% efficiency when doing space heat.
If there is an efficiency hit for using a tank, it is not much.
Deleted
Thanks again so much everyone. This has been incredibly helpful and I'm so grateful for all of your knowledge and experience!!
I found a new plumber that is recommending using flat panels instead of baseboard on the second story so that the boiler can output at similar temperature across all floors with the other two using radiant. Is this true?
I've also had two plumbers tell me that the new boilers (not combi) can regulate themselves and fire lower so that oversizing is not really an issue. Is this true?
I tried the loadcalc.net calculator - not sure I did everything quite right but I did my best, and it's calculating 30,000 total btus heating. So then I would make that number the max range that a boiler would need to hit, correct?
Yes it's possible to specify panel radiators (or even cast iron radiators) sufficient to work at the same water temperatures as the radiant floors. The 7 -10" tall fin-tube convector baseboard have very non-linear output at water temperatures less than 115F or so, but panel rads can work predictably at temps below 100F.
It's also true that the lower the minimum firing rate the better, independent of the maximum firing rate. Even though an 80K boiler with a 10:1 turn down ratio might be 4x oversized for a 20K peak load, since it can modulate down to 8K it's still a pretty good fit. A 5oK boiler with a 3:1 turn down ratio (which used to be common) can only drop down to 16.7K, and would be a lousy fit for a 20K design load, despite having a lower maximum firing rate.
You can use baseboards at low temperature (see http://www.slantfin.ca/docs/620.pdf). The output is reduced so you need a more length. I have installed baseboard zones running off the same temperature as the floor heat, no issues.
The decision of panel vs baseboard is more about cost and design. Go with the one you prefer that is within your budget. The rest is just sizing it to your load.
At 80-95F (typical slab radiant water temperatures) even the low-temp Slantfin is very non-linear and inconsistent, affected by dust-kittens, proximate furniture and other factors. Note that below 110F AWT they don't specify the output. So it really matters just how low you're running the water temps for the floor as to whether the baseboard can run at the same temp.
Panel rads are still very linear in output with temperature even at very low temp.