Re-insulating a 1989 house
Hi,
I’m in climate 4 (Seattle), re-insulating a 1989 house and would like advise on best way to do it. It has woodcladding and no sheathing (siding nailed to the studs), water barrier is tar paper, insulation is faced fiberglass batts in 2×4 framing.
Main goal is to better air seal it but increase in R value would be nice. I did a lot of reading of other questions and blog posts, and I guess I’ll be pointed to the airtight drywall method. I plan on following that but have questions:
1. Is there anything else I can do while the wall are open? I see people sealing the stud bays, but I don’t understand how that will help
2. Can I use a thin layer of spray foam then put batts? Avoiding spray foaming the whole thing it’s a 1-way route. Is rockwool better? Dense-packed cellulose?
3. Current batts are R-11. There are R-13 and even R-15 available for 2x4s, is this marketing? How can they “stuff” more R-value using the same material in the same space?
4. Is my house too old to air seal? I read horror stories of air sealing old houses
Thanks!!
GBA Detail Library
A collection of one thousand construction details organized by climate and house part
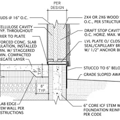
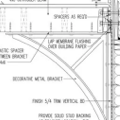
Replies
>" It has woodcladding and no sheathing (siding nailed to the studs),..."
That's a problem.
>"1. Is there anything else I can do while the wall are open? I see people sealing the stud bays, but I don’t understand how that will help"
Yes- you MUST establish an air barrier on the exterior side of fiber insulation for it to perform, otherwise air, moisture, and heat will move freely through the insulation. There are several ways to go about that. Start here as a primer:
https://www.finehomebuilding.com/2016/05/17/insulating-walls-no-sheathing
https://www.greenbuildingadvisor.com/article/insulating-walls-in-an-old-house-with-no-sheathing
>"2. Can I use a thin layer of spray foam then put batts? Avoiding spray foaming the whole thing it’s a 1-way route. Is rockwool better? Dense-packed cellulose? "
There needs to be an air gap (even 1/4" is huge, 3/8" is code minimum in western British Columbia) as a capillary break between the exterior layers and the insulation's exterior air barrier.
>"3. Current batts are R-11. There are R-13 and even R-15 available for 2x4s, is this marketing? How can they “stuff” more R-value using the same material in the same space?"
The density of the fiber has a huge impact on it's performance. It's the same material, but more of it crammed into the same space. An R15 weighs more than twice as much an R11, and impedes air convection within the batt by more than an order of magnitude better. An R19 batt weighs the same per square foot as an R13. When the ~6" thick R19 is squished to 3.5" in a 2x4 stud bay the performance is R13.
>"4. Is my house too old to air seal? I read horror stories of air sealing old houses"
No, there is no age limit, but how one goes about it is construction-specific.
While you have the walls opened up, be sure to run a bead of polyurethane caulk on the seams between doubled up framing such as top plates, jack studs, window & door headers, etc, as well as between the bottom plate and subfloor.
Hi user-7586255 (it would be great to get your real name).
Some builders detail the air barrier on only one side of the wall, the sheathing or the drywall for example. Others, particularly when using fibrous insulation like fiberglass believe that stud bays should be sealed on all six sides. There is merit to doing as much air sealing as possible, particularly in retrofits where there are tons of hidden pathways for air to move.
If you go with a flash-and-fill assembly use HFO-blown foam, which is much more environmentally friendly than the common types of foam (which have a super-high global warming potential). In these assemblies, many builders prefer dense-pack cellulose for the fill insulation because it forms to the irregular shape of the cured foam surface. Over-sized batts are another option as they will have to be pressed tight to the surface for a snug fit.
The reason batts can have different R-values at the same thickness is because they are made with different densities.
Your house is not too old to air seal, but you have to consider everything so that the building works as a smart system.
Dana's advice about the airspace is good.
You may find these article helpful:
Insulating Walls with no Sheathing
The Four Control Layers of a Wall
When is a house tight enough to need ventilation?
How'd they get way with no sheathing in 1989? I'd have thought seismic requirements would've necessitated it. Is there some other bracing in place? If not, think about that while you have the walls opened up, too.
>"If you go with a flash-and-fill assembly..."
Flash & fill is NOT really an option here, since there is no sheathing, only tarpaper. A flash & fill would almost certainly cause the paint to fail in short years (maybe even months), followed by the wood cladding itself. The extreme air permeability of the low density R11s protected the siding, but in a re-do it needs a proper air barrier with a rainscreen gap.
In climate zone 4C there is no need for air-impermeable insulation on the exterior of a fiber insulation layer, but it does need an air barrier. If that air barrier is made with half-inch foil faced polyiso (R3) with half inch air gap it leaves 2.5" for fiber insulation.
Compressing an R11 into that space would deliver R9 performance, compressing an R13 would deliver R1o, so the net performance would be comparable to a typical 2x4/R13 type wall. That's already a huge upgrade from the air-leaky R11 structure. See:
https://s3.amazonaws.com/greenbuildingadvisor.s3.tauntoncloud.com/app/uploads/2018/08/08074629/Compressing%20fiberglass_0-700x310.jpg
If you're willing to give up an inch of interior space, cutting 1" foil faced polyiso into edge strips for the framing (long-nailing/screwing the wallboard to the studs trough the stud-edge foam) would more than double the R-value of the framing, and leave enough room for a full-depth R13 or R15, for R16-R17 total at center cavity. Even though that's less than the current R20 code minimum the R6 thermal break over the framing fraction brings the total performance nearly up to current code-minimums on a U-factor basis.
Thanks for the recommendations and links. I'll go with the polyiso and compressing some fiberglass as I think it a good balance of cost/time/benefit.
BUT, as the demo progresses, I actually noticed there are 2 different insulations.. There's the tarpaper in the garage (see picture, a section is teared and you can see the siding behind it) AND there's a section that has a cardboard-like "sheathing" in the living room (see picture, there's a section teared down too and you can see the siding, no tarpaper). Googling shows "thermo-ply".
Is that better than tarpaper alone and is it "typical"? Can it benefit from another method of insulation? Do I still need to leave a gap still and have a rain screen?