Rebuilding the roof on a Deck house

We own a 1970s type post modern Deck House. As we found out the hard way in our first winter in the house, the roof doesn’t have any insulation. We have cathedral ceilings throughout the house (no attic) with tongue and groove 1 3/4″ deck boards on the ceiling, a layer of plywood, and shingles. Low pitched roof and we are in Zone 5 so less than ideal with an R-value around R-3. See attached.
We are looking at rebuilding the roof to accommodate rigid insulation over the roof deck boards. Both quotes we are entertaining are recommending: 6 inches of Hunter Poly Iso and 1/2 inch CDX Plywood than Shingles.
One quote is recommending an Grace Ice & Water Shield directly on top of the Roof deck boards, then rigid insulation, Plywood, and another Grace Ice & Water Shield for the full roof.
The other quote is recommendation, Ice and Shield only on top of the 6″ of Hunter Poly Iso and only for 9 feet to leading roof edge. The rest of the roof would have a Synthetic underlayment. Note that we have 2 feet of overhang on our roof.
The total R value of insulation would be R-34 plus the minimal R-value of the tongue and groove decking that we currently “enjoy.”
Our #1 goal is to ensure no more water penetration from ice dams. I’m curious what everyone thinks of this overall approach for a Deck House and which Grace Ice and Water Shield approach seems most appropriate.
Thanks for your insights!
GBA Detail Library
A collection of one thousand construction details organized by climate and house part
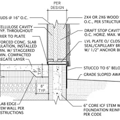
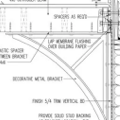
Replies
Kill,
What you want is Ice & Water Shield directly on top of the existing tongue-and-groove boards. This peel-and-stick is your air barrier.
Then you want the rigid foam layer. The foam seams should be taped.
Then you want a layer of plywood roof sheathing.
Then you want roofing underlayment (as required by code). This could be asphalt felt, or it could be synthetic roofing underlayment.
Then you want your roofing -- in your case, asphalt shingles.
For more information, see this article: "How to Install Rigid Foam On Top of Roof Sheathing."
Note that your type of house has an unfixable problem. I'm talking about the thousands of air leaks at the perimeter of your tongue-and-groove ceiling. (If your type of house has roof overhangs, and the ceiling boards penetrate the wall air barrier and extend to the overhangs, you're kind of doomed -- unless you cut off the roof overhangs using the "chainsaw retrofit" approach.)
There is no good way to seal these air leaks -- all you can do is learn to live with them. But your insulation retrofit work will definitely reduce heat loss through your roof assembly.
Hi Martin,
Picking up on this comment "If your type of house has roof overhangs, and the ceiling boards penetrate the wall air barrier and extend to the overhangs, you're kind of doomed -- unless you cut off the roof overhangs using the "chainsaw retrofit" approach."
We do have two feet of overhang and I'm quite sure the same ceiling boards extend to the overhangs.
What does the "you're kind of doomed" comment mean. Our #1 concern is addressing ice dam problems and second is energy efficiency. Is the "doomed" comment purely related to energy efficiency concerns or do you mean that the current proposed rebuilt will still be subject the ice dams concerns because of this "unfixable problem?"
This roof rebuilt is astronomically expensive (especially considering that the shingles were replaced by the last owners and are only a few years old) so I want to be sure we are doing everything we can to address the ice dam problem caused by the non-existent insulation in our current roof.
Thanks!
Hi Martin,
Thanks for taking the time to answer my question.
What is the purpose of the "Ice & Water Shield directly on top of the existing tongue-and-groove boards?" Is that to keep house moisture from reaching the insulation or to prevent exterior moisture from reaching the ceiling boards?
We received the attached recommendation from the Deck House building company. Is the approach recommended here just outdated?
Kill,
Q. "What is the purpose of the Ice & Water Shield directly on top of the existing tongue-and-groove boards?"
A. As I wrote in my first response, the main purpose of the Ice & Water Shield is to act as an air barrier.
Q. "Is that to keep house moisture from reaching the insulation or to prevent exterior moisture from reaching the ceiling boards?"
A. An air barrier in that location prevents interior air from entering the roof assembly through cracks between the boards. The interior air carries moisture with it, and the moisture in the interior air can condense on cold surfaces.
The Ice & Water Shield also acts as a vapor barrier, preventing moisture diffusion. This is much less important than its function as an air barrier, but it's still helpful to stop outward diffusion in winter.
Q. "We received the attached recommendation from the Deck House building company. Is the approach recommended here just outdated?"
A. The illustration you shared depends on the rigid foam layers as its air barrier. This can sometimes work, if the people who install the rigid foam are unusually conscientious (and if they tape each seam perfectly and if their work is verified by a blower door), but this approach has often led to failures. One of the most famous failures was at Joe Lstiburek's barn. Read about that failure here: "Complex Three Dimensional Airflow Networks."
Installing some type of peel-and-stick air barrier over the entire surface of your ceiling boards is a much safer approach.
Martin,
Thanks again. The builder that is recommending the Ice and Water shield above the ceiling boards and on top of the plywood roof sheathing is also recommending a Shingle-Vent II ridge vent with external baffles (or equivalent). Is the a ridge vent the correct approach here with the rigid insulation sandwiched between two full layers of Ice and Water shield?
Thanks!
Martin,
Any final thoughts on the ridge vent dilemma?
Thanks!
Kill,
This is an unvented roof assembly. You don't need or want a ridge vent.
That was my understanding as well. Thanks for the confirmation. Super helpful.
Deleted
Martin
Would a layer of house wrap over the T&G be an acceptable air barrier?
Walta
Most housewrap doesn't cut it for use on roofs, but vapor-permeable adhered membrane WRBs such as BlueSkin are fine:
https://www.finehomebuilding.com/2016/09/14/self-stick-wrb
Thanks for the info. How does that compare price wise to a Grace Ice and Water shield type product?
We love our 1970 Deckhouse. We've been on mission to improve the efficiency, and we've cut heating demands by nearly 50% since we moved in 5 years ago, so that now (per the benchmarking provided by our utility) claims we're in the top 10-15% of efficient homes of similar size. I've kept a detailed spreadsheet of updates and tracked improvements normalized by BTU/HDD to see what items move the needle, and which have no traceable impact.
Your current roof stack sounds suspect. My roof (as built in 1970) was ~2.5" T&G decking, some sort of an aluminized asphalt paper air barrier, 1" of polyiso, a layer of plywood, followed by roofing felt, shingles, etc. Then during re-roofing through the years, most owners tack on another layer or two of foam insulation, 25 years ago the previous owners of my house added another 2-3" of insulation between the existing foam and the plywood. When i re-roof in the next few years, i'll add a few more inches. Steve at Deckhouse can give you the dimensions to measure the thickness of your roof to estimate the current amount of insulation - i would be surprised if there were truely none (not that 1" of 40 year old polyiso is much, but no point in throwing it out if you find it there). Note with our 3-4" of polyiso insulation, we have no ice dam problems, even with the 3' snow storms of a few years ago - unless you have a roof R value of 1020, you will get an ice dam when the outside temperature is 31 degrees and you have R30 of snow on your roof, but the 2' of roof overhang means that the water behind of the ice dam does not extend past the 5' of ice dam protection our roof has (at least before enough snow melts that you no longer have 3' of it).
Replacing the aluminized paper layer with peel and stick seems like a good idea that will make the stack more robust. Really pay attention to how well they air seal the peak. Deckhouse as a image of how to install overlapping the insulation. I have one 2' section that absorbs moisture over the winter, and will weep briefly when the sun hits it in the spring (not to mention attract carpenter ants to the foam - which then cut more holes in the insulation further decreasing the air barrier, attracting more the next summer)
Jonathan,
Thanks for your insights. It's comforting to hear that adding 6" of poly iso will likely solve our ice dam problem in most scenarios.
I should say that we don't believe our house is an actual Deck House brand. It is however a very similar post modern type house. We've been told it's possibly a Core House or a TechBuilt. It shares a lot of the same challenges as Deck Houses and same construction principles. There are several similar houses in our neighborhood. One of our neighbors rebuilt the roof on theirs and were shocked to find absolutely no insulation in the original roof construction so I wouldn't be surprised ours is the same.
What are your thoughts on breathability for such a roof constructions/house? One contractor (recommended by Acorn Deck House) is recommending not covering the plywood with a full Ice & Water shield layer for that reason. Only 9 feet up from the edges of the roof (so 7 feet past the overhangs).
In terms of priorities to improve your house efficiency and winter comfort. Below are my findings from our improvements:
1) As you state, your roof. I'll be adding more insulation when we re-do our roof, but i would think this would be a big improvement.
2) Single glazed windows. About 1/3rd of my windows were still the original Hope steel sash windows + 3/16" single pane fixed window. Applying plastic shrink film over the whole window made a huge difference in both comfort and energy loss. Replacing the glazing with IGUs didnt make as much of a difference as i hoped, but they look much better, and make my wife happy. I've been replacing ~5 window units per year with the beautiful retrofit sash units by deckhouse, they perform well (argon filled center glass u = .25), and you can get any PPG low-e coating you wish, the standard solarban-60 is best (has the lowest U factor) for areas that are not getting sun (which none of my windows get), but you can ask for coatings with higher solar heat gain factors if you get sun). Note that it is dependent on your installation to ensure you get a good air seal between the sash and the existing frame. On the fixed windows, you can just have a commercial window glazer re-glaze them with an 3/4" thick IGU without having to do any carpentry, or order glass from Deckhouse and do it yourself - noone else would sell IGUs to me at comparable specs and prices.
3) Adding insulation under the floor overhangs. This really improves barefoot comfort, although it was unnoticeable in my energy tracking. You can squeeze in 1" of foam where windows open below, and several inches elsewhere.
4) Adding wall insulation on the lower level between the concrete foundation and drywall. My concrete walls had minimal insulation, and this improved economics pretty significantly.
5) Optimizing programming (heating curves) of the boiler + adding an internal air temperature sensor (which offsets the heating curve estimated by your outdoor temperature sensor based on internal house temperatures) surprising decreased energy usage by 5-7% and cost $104 for my boiler's sensor. This enables lower water temperatures (which increases boiler efficiency) but switches your circulator pumps to go continuously, so you need to switch to ECM circulators (at ~$100 a pop for Taco's 7 series) or your electric bill will go up.
Some 'improvements' that had no real noticeable difference to comfort or energy usage:
1) Caulking / air sealing: I went nuts with silicone when i first moved in, calking every exterior T&G joint on overhangs, and every interior and exterior junction between walls, rooflines, beams, floors, ceiling, concrete foundation walls, etc, etc, etc. But it didnt impact heat usage nor change the interior winter humidity, which stays ~40% (even when it drops below 0F), so my takeaway is that everything was well sealed when it was built, and it is much easier to seal with this building style with floor and ceiling joists spaced at 96" on center vs. 12-16" on center and filling your ceiling with can lights.
2) Wall insulation: I opened the walls up in one room to inspect the insulation, and i replaced it with a stack of XPS and polyiso in a cut-and-cobble approach to squeeze in the highest possible R value in the wall as possible. But it didnt change that room's temperature, nor could i see the difference on a cold day imaging with a thermal camera. Note that the wall insulation was installed by the builder, and the person who did my home did an unbelievably tenacious job stapling the insulation every inch between each 2x4 bay, your builder could have done differently.
I worked on a Deck House roof a few years back (Zone 5). The owner had it reroofed by a roofer who didn't know what he was working with, and had crazy condensation and ice damming issues. We reroofed using peel & stick on the T&G deck, and 2 layers of polyiso with taped seams. No problems since.
Thanks for the info Peter. How did you proceed above the insulation layers? Plywood and then...? Did you use any Ice & Water shield on top of the plywood or just roofing fabric? We've got one contractor advising on a full roof Grace Ice & Water shield on top of the plywood and another that is adamant about letting the plywood breath and only having 9 feet of Ice & Water from the edges of the roof.
As far as I can recall, we used Ice&Water only at the eaves and valleys, up to about 3' inside the exterior walls. The rest was 30# felt. Plywood sheathing as a nailbase, though I would have been comfortable with OSB. Either way, it will be a sacrificial nailbase if any water gets in.
The plywood doesn't need to "breathe", and it won't get any significant drying through the fiberglass shingles anyhow. There just wasn't any good reason to use another layer of Ice&Water over the whole roof. Waste of money.
Our contractor is suggesting using this product Deck Armor instead of the BlueSkin as an air barrier directly above the tongue and groove deckboards. This product doesn't appear to be intended as an air barrier and is definitely not a peel-and-stick membrane.
Is this the wrong product to act as an air barrier over the tongue and groove?
https://www.gaf.com/en-us/roofing-products/residential-roofing-products/roof-deck-protection/synthetic/deck-armor
Thanks!
You are looking for a fully adhered membrane. Deck armor is a good underlayment but it won't seal up your T&G. You can get a decent air barrier by taping the seams of the foam, but won't be as good as an adhered membrane over the T&G.
Grace Ice and Water, Blueskin products. You are looking for something that is a vapor barrier as well.
Thanks, Akos!
Our contractor came back with a different product: Grace Select, similar to the Grace Ice and Water, just not as thick. Seems to have all 3 qualities: air and vapor barrier and fully adhered membrane. Any reason not to go with this product above the tongue and groove?
The only precaution that stood out was "Due to its slight asphaltic odor, do not apply where the membrane is exposed to interior living space. Refer to product literature for more complete information." Would this be a problem above the tongue & groove? (Grace Ice & Water has the same note.)
RE: Interior odor from I&W - considering that the T&G ceiling boards are not airtight, I would not recommend using any product with that warning label. I don't know about the Blueskin, but 475.com has non-asphalt self adhering membranes whichi would probably work great.
This is a super helpful post. We too have a deck-house style home in a developed in NH. Since purchasing the home 7+ years ago we've struggled with water leakage both during the winter due to ice dams, as well as occassionally during high-wind rain storms. We've had several different companies try to "fix" the leaking, but the problem persists.
After reading this post (thank you all) we are considering a roof rebuild. Given the scope of the required work, would anyone have recommendations on a contractor/roofer in the Upper Valley area of NH (Lebanon, NH/ White River Junction)?
I used to work for Henri Fennel at Foam-Tech in North Thetford.
He is a spray/injection foam insulation contractor, as well as, an architect.
I'm sure - if you are still dealing with this problem - he could consult for you ...