Balancing Soundproofing and Potential Moisture in Double-Stud Wall

Hi all,
First, thanks for the wealth of knowledge on here. I’ve learned a ton from the forums. Apologies for the long post ahead..
Long story short, my goal of building my recording studio has been essentially put on hold because of having to balance sound isolation requirements and double stud wall moisture concerns. This has left me essentially in analysis paralysis and unable to decide how to proceed for years now. I’m sick of it! I’ve decided I’m just going to proceed with my construction, whether it’s foolish or not (and please feel free to tell me if it is!) and deal with the consequences down the road if need be.
So with all that out of the way, I’d like to describe my proposed construction in hopes to get some feedback from you knowledgable folks to make sure there aren’t any glaring problems that I’m not considering.
I’m in eastern Ontario, so climate zone 6 I believe. I have a 26’x 26′ standalone building that I’d like to build a recording studio in. It is built on a concrete slab with radiant heating in the slab. The current wall construction of the building from outside to in is:
– vertical plank cedar siding
– Tyvek wrap
– 7/16″ OSB sheathing
– 2×6 stud walls 16″ O.C.
– pink fluffy fibreglass batt insulation in stud bays
– 6 mil poly vapour barrier
What I’d like to do is build two standalone “rooms within rooms” inside the space as a control room and live studio room (see attached pic). These rooms would each have their own walls and ceilings completely isolated from the exterior structure (except the concrete slab). In order to do this, I would remove the existing poly vapour barrier and put it on the interior side of the new rooms. I’m also considering replacing the fibreglass bats in exterior wall with Rockwool Comfortbatts because my understanding is that mineral wool is more resistant to moisture and pests than fibreglass (please correct me if I’m wrong).
So with the construction of the new rooms, my overall construction from outside to in would be
– vertical plank cedar siding
– Tyvek wrap
– 7/16″ OSB sheathing
– 2×6 stud walls 16″ O.C.
– Rockwool Comfortbatt in studs
– 4 1/2″ gap between exterior and interior stud walls filled with fibreglass insulation
– 2×4 stud walls 24″ O.C.
– pink fluffy fibreglass batt insulation in stud bays
– 6 mil poly vapour barrier
– 5/8″ Type X drywall
– green glue
– 5/8″ Type X drywall
Also to note, because my goal is sound isolation, extreme care will be taken to ensure air tightness of just about all aspects of construction. For example, all exterior stud bays will be caulked between studs and sheathing, as well as any other gaps caulked and sealed. Electrical outlets will be sealed with putty pads, drywall layers will be caulked at the seams etc.
My questions are:
1. Does it makes sense to use Rockwool mineral wool for the exterior most insulation layer instead of the existing fiberglass? My thinking is that it would be slightly more moisture and pest resistant. I would use the existing fibreglass in the space between the walls.
2. Should I invest the time and effort into retrofitting a rain screen gap between my existing siding and sheathing? Maybe I only do this on the north side wall? I don’t fully understand how this can be done considering my cedar siding is vertical strips. Can this even be done without too much expense? For example, how is the existing soffit dealt with?
3. Can anyone confirm that my vapour barrier is installed in the correct place? Please see the attached image of how I’m considering installing it. The vapour barrier is the green outline. Note how it sort of snakes from the interior walls of the isolated studio rooms back to the exterior wall where there is no double walls. Does this make sense?
4. Is there any type of relatively inexpensive wall sensors I could install, maybe just in the north side wall, so that I could monitor the moisture content and then potentially take action if it were to get too bad?
5. Lastly, just a thought but, because I have radiant heating in the slab I was wondering if this may help mitigate the cold sheathing problem, because the space between the walls will get some form of heating, even if minimal, just by way of the new walls being constructed on the slab. Can anyone comment on this? Thoughts?
Thank you so much to anyone who has taken the time to read through all this and can comment. I really appreciate any and all advice. Cheers!
GBA Detail Library
A collection of one thousand construction details organized by climate and house part
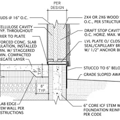
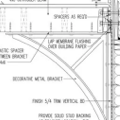
Replies
We constructed a film/recording studio in my commercial building about 5 years back using a furred air space assembly retrofit in an existing structure. The difference is that it was on the 2nd floor, so had about 18" of dense pack cellulose in the floor. It was a double stud wall, but only to the interior with resilient channel both sides. Double entrance doors with automatic jams, etc. Exterior walls were furred air space assemblies. From the outside - Metal cladding - 5/8' OSD - 2x6 walls with fibreglass - 2" EPS foam - radiant reflective vapour barrier, 2x3 horizontal furring - 5/8" drywall. The STS performance of that room was outstanding but as you might guess, it was not decoupled from the exterior envelope. Thermal break for that wall assembly is therefore on the inside, with a radiant chamber (warm side) where all electrical and plumbing etc. was run. Very few envelope penetrations this way. I opened up the wall about 5 years in with zero issues (to install a few windows) when the film studio became a Pilates studio (long story).
This is in Zone 7A, with -35 C temps in winter.
Your outside wall with OSB, Tyvek and cedar can dry to the outside, so not sure if I'd remove all that and add furring but if you want further assurance, do it. You can strap it, but you would run vertical, then horizontal strapping over that, then your siding. The air gap would be 1 1/2" if you use 3/4" material.
You will be air sealing the interior "cavity" much more carefully than most home owners, mitigating risk, and code will require that poly anyway on the interior. From my viewpoint, you would be pretty low risk for moisture issues. Hopefully the B.Sci. gurus will pipe on on this one :-)
Thanks Dennis, appreciate your input!
Regarding the insulation, do you think it would be beneficial to have rockwool as the outermost layer up against the sheathing? I'd rather go pink fluffy for the cost savings but if Rockwool will be more resilient to moisture and pests I'll go that way.
I can't comment on recording studio specifics, but from what I've heard the two best things you can do about moisture concerns in double stud walls are 1) install a ventilated and drained cladding layer (rainscreen with gap) and 2) install a "smart" vapor throttle on the interior, e.g. taped plywood, taped and painted drywall, Intello/Membrain/Majrex.
Apparently the main risk for double stud walls is that they are typically so thick that that rate at which heat passes through them is too slow to dry them out well if they get wet. So the main concern is preventing moisture from getting inside in the first place. Since bulk water usually comes from the outside, this is why the ventilated and drained cladding is a priority.
I did some brief searching and found this channel about building recording studios: https://www.youtube.com/watch?v=6xTFjD6xDcw
Mineral wool is a little better about pests/critters, but if you haven't had issues in the past I probably wouldn't bother replacing the existing fiberglass just for that. Moisture resistance with mineral wool is also a bit better, but you're better off detailing your wall so that moisture doesn't get in to begin with. If the existing fiberglass is in bad shape, then I'd replace it, otherwise I'd leave it alone.
I would use the "Safe n' Sound" version of mineral wool in the interior wall since it is a little better for sound isolation compared to fiberglass. Note that you want a small air gap between the studwalls -- that air gap will help control sound transmission better than if the entire wall is packed with insulation in most cases. The usual way to do this is to build the two studwalls spaced an inch or so apart, then insulate the two walls but leave the 1" gap between clear as an air gap.
It looks like you have double opposed doors in your drawing, which reminds me of the studio I worked in decades ago. You'll want heavy, solid doors, and very good weatherstripping too to control sound. You need the mass here -- don't use lightweight or hollow core doors. Solid slabs are the way to go, and if you want a window, you want LAMINATED glass for sound proof doors.
As far as I know, poly is required by Canadian code in essentially all areas. We have some members that work in Canada who will know for sure, so I'd wait for one of them to post before you begin your project.
Bill
Bill,
Our codes just call for an interior vapour-barrier. It can be a variety of materials (including a smart membrane) as long as they are under 1 perm.
Bill, the caveat here is that an air gap can actually be a bad thing for sound transmission at low frequencies, particularly if solid membranes are configured in a triple leaf. My guess is that Cody is aware of this given his plan.
On the double doors, I would add a note to use automatic jams (pretty amazing devices when it comes to sound transmission). We used them on our studio and tenant doors, along with exterior grade weather seals. Commercial code required fire rated doors, but we ensured they were solid.
Yes I've been looking into that for the doors! Fortunately the doors I have seem to already have the auto drop seal installed in them at the bottom, I just need to find the appropriate sill plates. These doors were removed from a Pilchner & Schoustal built pro studio and are purpose built for sound isolation. I got very lucky to score these.
Thanks Bill, I appreciate your advice.
Moisture is my main concern so if mineral wool will handle it a bit better then I think the relatively small investment for the first layer makes sense. Existing insulation doesn't seem to bad so I'll reuse it for the second layer.
On the exterior walls I'll have a 4 1/2' air gap as the interior walls need to clear the foundation. Because of this I plan on filling that gap with loosely packed insulation as it should help reduce resonances in the wall cavity. The interior walls between the control room and live room will be built though as you mentioned. Separated by a 1" air gap with insulation just in the studs.
Yep, double doors is right! I was actually fortunate enough to acquire 8 solid heavy doors with full 3/8" laminate glass inside each of them, as well as a 7' x 4' double studio window with 3/8" and 1/2" laminate glass. They were installed in a well known artists pro studio in Toronto. The place was built by Pilchner & Schoustal and they spec'd all these doors for the build. They are seriously heavy!
I don't think the 4.5" gap is buying you much. From what I remember it only adds a couple of points in the STC value, extra space lost and work/material for not much gained. Do keep a 3/4" to 1" gap between walls, you definitely don't want the insulation touching. In terms of energy efficiency, a 2x6+2x4 stud wall is already very good.
Off the top of my head, going with mineral wool over fiberglass increase your STC by 1, so not enough to matter. I would leave the batts in the walls and focus extra energy on air sealing, trust me the backer rod install is more work than it seems, gets very annoying quickly.
Gap or no gap, the vapour barrier and batts can stay. Most codes allow for the vapour barrier to be towards the outside provided the insulation ratio is met. In zone 5 that means 30% of your R value needs to be outside the VB. The OBC has a table that shows this in case your inspector asks. If you leave the VB in the middle of the wall, you won't need anything else on the warm side. If you are still worried about your assembly, you can run it through:
https://www.ubakus.com/en-ca/r-value-calculator/?
Takes a bit to set up but not too hard if you don't mind metric units.
Since this is a studio, it is not occupied full time plus there is no cooking or showers. This reduce the amount of interior moisture that is generated making any wall assembly much lower risk.
Hey Akos, thanks for your reply.
Hmm, very interesting about keeping the vapour barrier where it is. I did wonder if that was acceptable but nearly everyone I've spoke to has said that it must go on the warm side. Because I'm going to have to tear it down anyway to seal up all the stud bays, I figured I might as well go with the conventional approach and put it back up on the interior wall. Although there is an existing 1/2" drywall ceiling that I'm planning on leaving up as my "outer shell" that has a vapour barrier behind it so my plan is to go into the attic and cut it out between all the joists so that I can install the new vapour barrier on the new interior ceilings. Definitely not looking forward to that! I'll definitely check out that calculator though and give this some more thought.
The reason for the 4 1/2 inches is because the interior walls need to clear the foundation, and that's the gap I'm left with. Because of this I believe it's recommended to fill the entire space loosely with insulation as it'll help reduce resonances within the wall cavity.
Regarding the mineral wool, my main concern here is definitely moisture over any extra sound isolation it might provide, and I'd be happy to use only pink fluffy fiberglass to save some cost. The walls will definitely be air sealed extremely well, so maybe I'm worrying too much about this?..
And that makes sense about it being lower risk than a normally occupied home with cooking and showers. I do plan to keep the humidity at around 40% though in the winter for the benefit of the instruments, likely with small space humidifiers.
Great score on the doors and window. Huge dollars for those these days. I finished an ATMOS theatre project 2 years ago and the acoustic profiling and treatments were a lot of fun to play with…very satisfying when you get it all sorted.
I like the Roksul products and would use them in your walls, with no gaps.. Rockboard 80 is what I used in my interior sound treatment panels, screen wall etc.
You are very low risk for moisture issues…don’t lose sleep on that one.
I’m using a few Fibaro Smart Implants which host up to eight external DS18B20 temperature sensors or one external DHT-22 (does humidity and temps) which are pretty low cost ways to monitor temps if you like. I use them for my pool solar system and heat exchanger system. You would need a Smarthings or Hubitat hub to use them. These bits have been 100% reliable so far.
On your existing ceiling, I would open up that vapour barrier as you suggested so you can go to code on your inner rooms with poly with no worries. I have found that blown in cellulose is surprisingly effective at dampening noise, so I would go to R60-80 in your existing attic if you can. It's going to be a lot cheaper than Roksul and far easier to install. 2-3 hours as a DIY project if you like with a rented blower. The one from HD is likely fine as you are just blowing it in loose.
@Codyg
you've gotten some awesome responses so far. I find soundproofing in renovations is a bit of witchcraftery, mostly because the best advice comes from people with experience and generally I can only find those people on the internet. There doesn't seem to be solid studying on soundproofing specific material like green glue or MLV like there is on quantum physics for instance. Mostly all I find are paid studies like from insulation or soundproofing product companies which may be biased. However, there is solid knowledge on general simple assemblies with standard building products (See Akos's post below for the NRC studies) Also, Soundproofing and its specific products can get VERY expensive. its hard to tell what's the best bang for your buck when you're not testing every combination objectively.
Despite all this, I am particularly interested in soundproofing. Even though I never thought of or designed a studio, hopefully I can contribute to this conversation.
This is my advice, for what its worth:
-Leave the existing exterior wall. Your fiberglass and poly is fine.
-Install 1-2" of rockwool comfortbaord onto the ext. studs. Since you need a space to decouple from the ext wall, this high density board fills the gap and add density.
- install 3.5" steel stud interior wall up against the rockwool. steel studs flex and absorb sound, vs wood studs that are stiffer and reverberate. Moreover, steel studs are C shaped, you can fill the inside of the C with more dampening insulation. not to mention they're always straight.
- Fill steel stud bays and inside the studs with safe n sound.
- *Consider* adding Mass Loaded Vinyl INSTEAD of Green Glue. This runs into the soundproofing specific products/snakeoil category. given that, MLV dampens but also adds mass vs green glue just dampens (allegedly). I forget what kind of price discrepancy there is between the two, but MVL is easier to install.
- Add 2 layers of 5/8" Type X or C drywall. You can even add polyurethane sealant to the steel studs (and have a wider screw spacing) for extra dampening. Caulk all the seams of the first layer of drywall with acoustical or PU caulking, the 2nd layer of drywall can then be mudded and finished as usual.
- add more mass/another layer of drywall to the existing ceiling. add more insulation above the ceiling.
- Pay special attention to outlets, switches and ceiling fixtures.
This assembly meets the four elements of sound proofing: Decoupling, Damping, Absorption, Mass and flanking (The secret 5th element).
But More to your original question: I also live in Ontario. I personally don't think you should bother with tearing out your existing exterior walls just for the sake of caulking studs to sheathing. I've been there, it sucks, for no real gain. The whole point that our OBC prescribes poly is to protect against that (cause at the time, no one in their right mind would tape or caulk the seems of sheathing, or use an air barrier wrb). But, If you're going to do it anyway, consider using tremco's Exoair Flex Foam for the stud bays. it'll really speed things up.
Just my thoughts,
Jamie
Jamie,
I think the opposite is true.
There is too much information about soundproofing and lot of it is wrong or misrepresented to push specialty products. The worst offender for this is MLV which has no place in a sound isolated wall partition.
Luckily our NRC does a lot of good testing and provides the results for free. You can look at these (there are more if you search):
https://nrc-publications.canada.ca/eng/view/ft/?id=04ac8069-a5d2-4038-8787-da064b073e7f
https://nrc-publications.canada.ca/eng/view/ft/?id=bd0ee4e8-155e-4a79-9aaa-83aaa117d6da
https://nrc-publications.canada.ca/eng/view/ft/?id=7c9971a9-227a-433a-8c06-cd00af83a236
One thing to note, that all the assembly consist of simple elements. All you see is steel/wood studs, drywall and insulation. That is it, no magical snake oil soundproofing elements.
Akos,
That is fare. I value your opinion. Looking back at my wording, I will edit my post.
Thanks for posting the NRC studies. If you notice, most of my assembly recommendations are the same principals used in the NRC studies. However, I guess my ineloquent point was more that they don't test the snakeoil things products which many commercial interior contractor use in renos like greenglue (which apparently is regarded highly) or MLV which at least my commercial soundproofing supply shop likes. So hard to know for sure if its snakeoil or not when its not tested objectively by NRC. We only have the private tests that the soundproofing snakeoil companies provide which may be biased.
Now, don't get me wrong, I don't like MVL, and I don't like its price. I'd rather build new and do a proper assembly just as the NRC's assemblies. However, where the snakeoil products come into play are in tight circumstances. The only reason I suggested MLV, is to add mass given the circumstances of the build, without creating a triple leaf. In a new build, I would be saying add 2 layers of 5/8" gyp on either side. Unfortunately, that's not practical here. Also, we can't practically do 4 layers on the inside, or at least I've never tired it or seen it be done.
The OP wanted to use green glue, I suggested considering MLV in lieu for the sake of extra mass.... shoot me... with an LRAD :)
If you look the last link, they have a nice graph of STC vs mass. When it comes to partition wall STC values, the only thing that matters is the weight of the each surface. MLV could be used to add weight but that is very expensive mass. A layer of drywall is way cheaper. 5/8" type X is 2.2lb/sqft about 2x that of the common 1/8" MLV.
MLV is very good when used properly and for the right application. It does wonders for noise reduction when hung as loose sheets around a loud piece of equipment such as a generator or compressor. Unless you have one of those in your basement, I would save your money.
Green glue is one item that does work. It only work though if your assembly is already built properly with no flanking paths, no acoustic short circuits and good air seal. This means in almost any residential application it is a waste of effort.
For an ordinary residential application e.g. shared bedroom walls, what would you say is the best value for effort/cost on noise reduction, e.g. just doing 2x 5/8" drywall with no green glue and sealing the drywall edges and electrical outlets?
Even less.
Single layer of 5/8 on both sides with edges caulked plus batts. The most important part is to make sure the drywall actually goes down to the bottom plate and it is fastened there, drywallers tend to take shortcuts with this.
Unless you get gasketed solid core doors, the door will always be the weak point so there is not much point to go overboard.
If you want a very quiet wall, build a 1 5/8" metal stud wall offset 1/2" from 2x4 wall. Same single layer of 5/8 caulked and batts. On paper walls with resilient channel have similar STC value but somehow this works much better and not much more expensive to build. I think the reason is that the low frequency isolation is much better. I've also tried staggered stud on 2x6 plate which is about the same width but somehow it also doesn't work as well. This is very much subjective as I didn't measure them.
Jamie,
Recording studios may be one of the few situations where more exotic or specialized materials make sense. Most acoustic attenuation research is understandably geared to the much more common problem of building good party walls and floor/ceiling assemblies in multi-unit residential buildings, where using common techniques and materials that all the trades are familiar with seems like a better approach.
Jamie,
Thanks for your insight and advice! I definitely agree that soundproofing is a tough field to navigate. Lots of landmines lurking and conflicting advice. It's certainly not intuitive, that's for sure. I do feel though that I've got a fairly good grasp on it at this point. I wouldn't consider myself an expert by any means but I've spent A LOT of hours reading and researching from what I know to be legitimate sources. I've also been involved in a couple studio builds in the past so I've got a bit of first hand experience.
I think with my existing plan I'll likely end up somewhere in the ballpark of an STC 60-62. My existing structure is definitely going to be the weak point. I've considered adding mass to the exterior walls by way of installing 5/8" drywall in between the stud bays, which is a commonly done for sound isolation purposes, but ultimately I'm too concerned about the potential for moisture problems given our climate. Plus I'm going to be leaving the exterior windows be, (and adding another set of interior windows) which will lower my isolation but natural light is important to me and I'm willing to sacrifice a bit of isolation for it.
It's interesting though that you recommend leaving the poly where it is. I've definitely considered that and gone back and forth on it. I'd rather not create extra work for myself where I don't have to! Ultimately though I think it's prudent to remove it to inspect the existing state of the sheathing, then caulk and seal as best I can if I find some areas of concern. Even small gaps can significantly lower my overall isolation, plus I think by code I need to have the barrier on the warm side. I might be being overly cautious but it'll give me peace of mind. I also hate the idea of any bugs or critters getting in between my walls and living it up in there!
Regarding the green glue, while it is expensive I think I'm gonna use it to hopefully make up for some of the weakness in the exterior shell. I've actually got about three quarters of a 5 gallon pale of it from a previous build (hopefully it keeps, not actually sure about that but would assume so..) so I'll need to buy I think two more buckets which'll add around $500 extra to the build. In the grand scheme of things I think it's worth it. The other thing I have working for me is the 4 1/2" gap that'll be the result of having to clear the foundation with the interior walls. That should provide a bit of extra low frequency isolation.
Akos, I do love me some NRC studies :-) That first link does a good job of explaining the triple leaf effect I had referenced earlier in the thread.
When doing my basement theatre (a full gut) I did actually measure sound levels generated from a reference computer and speakers in several key locations on the first and second floor in the home. I did this during the reconstruction at several stages to see how well the measures I had put in place were working. This was completely apart from the acoustical treatments and profiling to set up the 11 channel ATMOS system. I can post up a link to my thread at the avs forum if anyone is interested.
Theatres here just use a lot of drywall...like four layers on each side.
I'm not a fan of MLV for wall assemblies, but used and would recommend dual layers of 5/8" type X with green glue. You are basically replicating commercially available laminated drywall on site with green glue. Couple that with resilient channel (and steel studs are definitely better than wood for sound attenuation) and you have a pretty simple wall system that works. I used the double layer drywall/GG approach for the theatre ceiling, along with resilient channel and sistered steel studs to deal with very uneven floor joists. My one mistake was insulating the floor joist at the periphery a bit too well with Roksul as this lowered 1st floor temps (at the floor itself) right at the foundation walls. If you spray foam the basement walls and joist blocking, and then insulate that ceiling, you need to leave a mechanism for heat to get to the floor above...unless you're using radiant heat.
My reference signal was 94db of pink noise, which was reduced all the way down to 42db measured on the 1st floor right above the basement theatre after all the work was done. Keep in mind that the theatre is in an essentially an open basement, and there are no partition doors between the basement and 1st floor. I had to build custom duct mufflers to address all the HVAC leaving the basement area to the 1st and 2nd floors of the home, and treat the return air ducts with acoustic liner.
It sounds like Cody has done a good job researching his studio setup with respect to sound, including the foundation treatment. Flanking via the slab is a tough one when dealing with low frequency amelioration.