Retrofit Basement Insulation Details

Hello,
Basement in our house was already finished when my family moved in. Finished area is mostly 1/2 poured foundation walls with daylight. Some is full depth. 2×4 framing with no insulation with no/minimal gap between framing and concrete (see attached). I’m considering removing drywall to add insulation, but I’d like to avoid bumping the framing out to allow room for continuous foam board as that seems like a mess. I’m interested in more details on Dana’s comments here:
“Yanking the studs and installing 2′ of EPS or polyiso against the foundation, then reinstalling the studs turned 90 degrees, with split R13-R15 batts compressed into the 1.5″ cavities”
1. Would this work with existing electrical?
2. I’m picturing that the foam would meet the bottom/top plates and studs at the ends. Would the rigid foam be cut short at each side and filled with canned spray foam?
West Des Moines, IA
Climate Zone 5A
Thank you!
GBA Detail Library
A collection of one thousand construction details organized by climate and house part
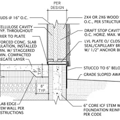
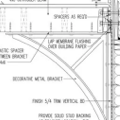
Replies
Incorporating insulation into your already finished basement without extending the framing can indeed be challenging, especially with the constraints you've mentioned. Based on Dana Dorsett's advice on Green Building Advisor and considering your specific situation in West Des Moines, IA (Climate Zone 5A), here are some insights tailored to your queries:
1. Working with Existing Electrical
Adding insulation around existing electrical fixtures requires careful planning. Electrical codes generally prohibit foam insulation from being in direct contact with electrical boxes unless they are specifically rated for such contact. You'll need to:
Use electrical box extenders to bring outlets and switch boxes flush with the new insulation surface.
Ensure that wiring is safely rerouted and protected, adhering to local electrical codes.
2. Fitting Rigid Foam and Sealing Gaps
Your understanding is correct. The rigid foam insulation would be cut to fit between the framing members and against the concrete walls. At the ends, where the foam meets the bottom/top plates and studs:
Yes, the rigid foam should be cut precisely to fit as snugly as possible between the studs.
Gaps at the edges and around any penetrations (e.g., for electrical wires or pipes) should indeed be sealed with canned spray foam. This creates a continuous insulation barrier and air seals the assembly, which is crucial for both thermal performance and moisture control.
3. Alternatives to Spray Foam Insulation
Understanding your preference to avoid spray foam insulation, consider these alternatives:
Mineral Wool (Rockwool): This can be cut to fit snugly between the studs, offering good thermal performance and moisture resistance. While it doesn't provide the same air sealing capabilities as foam, it's a non-combustible and breathable option.
Fiberglass Batts: Another common choice, though it's less effective at blocking moisture compared to foam and mineral wool. To enhance performance, a smart vapor retarder could be installed on the warm side of the insulation to manage moisture dynamics.
Additional Considerations
Moisture Control: Before insulating, ensure there's a strategy for managing moisture. In basements, interior insulation can trap moisture against the concrete walls, leading to mold and decay. A continuous layer of rigid foam insulation helps by acting as both thermal insulation and a vapor barrier.
Local Building Codes: Check local building codes for insulation requirements and moisture barrier strategies in basements. This ensures compliance and safety.
Professional Advice: Given the complexities of retrofitting insulation in finished basements, consulting with a local building science professional or insulation contractor can provide insights specific to your home's construction and the local climate.
By carefully planning the installation and sealing of insulation, you can enhance your basement's thermal performance and comfort without major disruptions to the existing structures.
Thanks, Casey. I am definitely concerned about using batt insulation due to the risk of condensation. I will need to do some more research and confirm with an inspector on the electrical details to make sure everything is up to code, but it seems like this could work if done correctly.