Filling Old Walls With Pour Foam

Hi There,
I live in Toronto, Ontario, Canada and I own an older home built in 1912. As many of you likely know, back a century ago the majority of these homes were built without insulation and the walls simply consisted of brick and plaster. My home isn’t much different. It is a brick home, with a 2 x 4 structure, that has open/empty stud bay cavities that are 16″ apart, with zero insulation. In-between the brick and the 2 x 4 framing is the sheathing and I believe a small gap in-between the sheathing and the brick. The sheathing as far as I can tell is horizontal planks of wood, which I believe has tarpaper on the side facing the brick. Recently, I signed up for a retrofitting winterizing program our Natural gas utility company is offering for homes that meet specific criteria, helping resident to decrease utility costs due to inefficient insulation and help to lessen our carbon foot print overall. I have qualified for the program and as great as the program is and sounds, in many ways, I do have reservations.
My concerns are, how long has this retrofitting practice for pouring foam into old home wall cavities be around for and how safe and effective is it? I’ve heard of horror stories where people have retrofitted foam in their wall and/or cellulose and it has impacted how the house is able to properly drain/air dry through condensation build up and water filtration causing mold and rot to develop in behind the plaster walls creating hazardous conditions for your health and homes structural integrity. I’m not knowledgable enough on this topic to know if this is indeed the case for pour foam, same as it can be for retrofitting spray foam or cellulose.
We can get some harsh winters here and my home is definirtely most cold come January through March. Gas costs are certainly higher than they would be if it was properly insulated but I do not want to move forward with such retrofits if in the future it poses serious risks to my health and slowly (if not quickly!) deteriorates the structure of my house. If that is the potential risk I’m presented with here, I’d much rather decline the offer and at a later point in time, tear out the plaster entirely, insulate with batts, add a proper vapour barrier and re-dry wall.
Anyone who could shed some light through experience and knowledge on this topic, I would very much appreciate that. I’m not sure how to proceed but hoping with the right advice, I can make an informed and correct decision.
Thank you!
Peter
GBA Detail Library
A collection of one thousand construction details organized by climate and house part
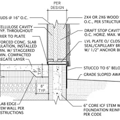
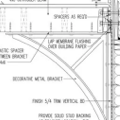
Replies
Hi Peter,
I’m giving your question a bump. As with so many things, installation is key to the success of “injection foam.” Take a look at that section of this article: Insulating Stud Cavities in Existing Homes.
Yeah, there are a lot of "what-ifs" here to give a definitive answer. One other concern with a house this old is what the wiring is inside those walls. If it's old knob and tube, then you can't really insulate until that's replaced anyway.
Look into Rockwool and Thermacork. Both have loosefill insulation that might work for your application.
if your thinking of filling the void between brick and sheathing, DONT. thats a windscreen and needs to be there. its vital to weeping, venting and reducing air pressure.
when wind beats on a home, that void allows air to circulate thus reducing force and prevents air and water from pushing through cracks and seams.
I have an extensively retrofit older home, and recently had the opportunity to perform a "post mortem" on some pour foam walls that were done a few years back.
One thing that was obvious (and pour penetration was good) is that the foam they used was a lot less dense (and maybe open cell) vs typical spray foam. So R value was not nearly as good as the spray foam (closed cell) that I have used for every renovation. I opted to do DIY cellulose which is a lot cheaper, but works quite will with old walls. Our home was built 105 years back, and wall construction is similar to yours. 20 years after cellulose, zero issues with mold, etc. My advice would be to use cellulose if you're "injecting" (cheap and you can do it yourself for low cost with a rental blower and 1 helper) and closed cell spray foam if you've opened up the wall at all. Contractors will likely point you to glass (because it's not as dusty) but cellulose is a far superior product when it comes to slowing air infiltration and convective loss at very cold temps in a wall cavity, or attic.
The challenge you may have with foam or cellulose would be making sure holes are drilled (it may be 2 or 3 per stud cavity) to ensure the horizontal fire break bracing (common in balloon framed structures) cavities are all filled.
The other issue that I see with these older walls is that each stud cavity will have a pile of plaster in the bottom which cannot be insulated by injection. You really need to open the wall to address this essentially solid concrete thermal bridge...these result in pretty obvious cold spots if you thermal image the wall after.
If you do hire a contractor, I'd 100% strongly suggest you pick up a thermal imager (like FLIR) for your phone and image the wall before the contractor leaves the site. This gives them a chance to pick up any missing voids.