Revisit: Insulating a wall from the outside — but for a 200-year-old home

I stumbled upon a question from a fellow who wanted to insulate his walls from the outside and add more foam board too. This intrigued me as it was inline with my thoughts on a similar project. The problem was, I could not ascertain from the feedback whether it applied well to my situation.
So, I wanted to throw the question out there.
Our home was built around 1820. That means big fireplaces that have long been closed and a 1964 peerless boiler burning 300 gallons monthly to keep it warm. The interior walls for the kitchen and dining area have been redone with traditional fiberglass batts and drywall. That leaves many more rooms and we are trying to live there. Add to this, the realization that preserving the history of the house, notably, the plaster walls, should be a consideration. In some places, the plaster keys are in rough shape.
What I found in opening the other walls, was an inner wall of plaster and split board lathe which was likely a pretty good air chamber (insulator) back in the day.
What I would like to do, since the siding is not original, is insulate from the outside with an inch or two of spray foam and then fill the cavity with Roxul. Sheath and apply Hardi Plank according to standards and be warm.
My line of thinking, and this is why I am asking here, is that the spary foam will lock the plaster into place while providing a vaper barrier. The Roxul, chosen because it is fire retardent and less expensive than more foam, will fill the rest of the cavity.
Am I on the right track? Nobody else seems to argue with me, but nobody else seems to be doing it either..They fill the walls with blown-in or they put two inches of fowm on the outside and re-side.
My concern is where will moisture happen? Between the plaster and the foam? On the surface of the walls? Between the Roxul and the foam?
My understanding is that it occurs where warm meets cold. That puts it between the Roxul and foam, but only if there is airflow.
Any ideas? Thanks! LesNewsom
GBA Detail Library
A collection of one thousand construction details organized by climate and house part
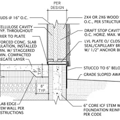
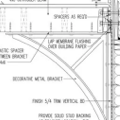
Replies
Unless you strip the sheathing, how are you going to get the Roxul in the wall cavities?
Homes of that antiquity rarely have framing spaced with cavities sized correctly for batt insulation. You'll have much better shot at it going with blown fiber insulation, which will conform to all widths depths and anomalies without voids, and will partially plug infiltration paths.
Spray foam on the exterior isn't necessarily the best option- rigid foam is more consistent and makes the exterior finish siding detailing easier. Once applied, spray foam is difficult to remove, should it cause unforseen moisture trapping issues in your final stack up. Or is the siding nailed to the framing without sheathing, and you're talking about spray-foaming the back side of the lath holding the plaster?
Whether and where condensation/adsorb moisture with insulating foam sheathing is a function of the ratio of foam-R to cavity-R, and the local climate. It takes a higher ratio of exterior-R to total-R to prevent excessive moisture adsorption at the sheathing in cold climates than it does in warmer climates. Where are you located?
The IRC gives some guidance on this, but it based on their minimum total R requirements for the climate zone. You have to do a bit of depth measuring and arithmetic to figure out what it needs to be for your cavity-R and location.
http://publicecodes.cyberregs.com/icod/irc/2012/icod_irc_2012_7_sec002_par025.htm
Using rigid rock wool instead of rigid or sprayed foam gives the assembly MUCH better drying capacity toward the exterior, and if you can't hit a sufficient R-ratio at a reasonable thickness, it's better to use rock wool than foam, which impedes drying. If the wall framing cavities are open to the floor joist cavities it's important to figure that out ahead of time or you'll be putting more insulation in to the floor bays than the walls. There are standard methods for blocking the floor bays that don't involve ripping open the floors or ceilings, but you may have to drill a few 1-1.5" holes in the ceiling (or floor) near the walls in places where they can't be otherwised plugged.
Homes of that vintage rarely have window flashing. When the framing cavities are empty the drying capacity is huge, and minor bulk water incursions did not cause a problem. But when you fill those cavities with insulation it's time to consider the bulk -water management at windows & doors very carefully. With deep roof overhangs you can sometimes get away with minimal retrofit water management, but details matter.
Your 50 year old Peerless is likely to be oversized for your existing heat load, and WAY oversized for your post-insulated heat loads. Is it hot water, or steam?
Les,
First of all, it would be good to know your location or climate zone.
Second, like Dana, I'd be interested to know if your house has any exterior wall sheathing.
If you have full access to the stud cavities from the exterior, and you want to install an inch or two of spray polyurethane foam against the lath and plaster, followed by mineral wool batts, you can. You won't have any moisture problems if you do that.
Of course, your walls still need OSB or plywood wall sheathing to provide bracing, and a vented rainscreen gap between the sheathing and the siding is always a good idea.
Dan and Martin,
Thanks for the fast and helpful replies! I am pleased that my line-of-thinking was not met with "Danger Will Robinson" answers.
To answer a few questions that came up and provide more info: I am in Maine, zip code 04428. Yes, there is exterior wall sheathing, in the form of rough-sawn boards 1" thick. Some measure 26" wide! I will reclaim those and use plywood to re-sheathe and also install fire-breaks. Those will give the plywood seams a nailing surface. Finish off with tyvek and the vented rainscreen then HardiPlank. The wall cavities are 48" OC with 4x6 studs. They are mortise-tenon joined to both the top and bottom beams, the floor caivity is open to the basement, not the wall. The 6" depth is plenty for the foam over the keys followed by 4" of mineral wool batts which I can order in 48" widths.
The original windows were gone when we bought it, we replaced what was there with Andersens. The final trim for those on the interior side (mating up to the original woodwork) has not been done, so they will be R/R with the new sheathing.
The old Peerless boiler is baseboard hot water. It has sat idle and we have relied upon a pellet stove rated for 2200 sq ft and an on-demand propane unit for DHW for the past few winters.
Given the type of construction, I can safely strip one full side of the house at a time without worries.
Here is an aerial photo from 1963 http://vintageaerial.com/photos/maine/penobscot/1963/MPE/7/31
The attached summer kitchen is gone.
Les