Roof Assembly for Post-and-Beam House

I am building a post and beam house in New Brunswick, Canada next summer. I have decided not to use SIP for the roof because of potential problems down the road. I will be using 3 layers of 4” Sopra-XPS thermal insulation panels on top of T/G pine boards. Attached is a picture of the structure. To properly seal the roof from leaking, I plan to put an ice and water self adhesive membrane on the pine boards. Then start laying down 3 layers of 4” insulation panels. OSB will be placed on top of the final insulation panel. Then 1” strapping and steel roofing. Is the ice shield membrane in the right place or should that go on last before strapping? Any suggestions/comments?
GBA Detail Library
A collection of one thousand construction details organized by climate and house part
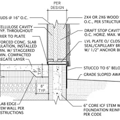
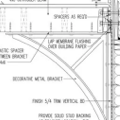
Replies
How are you going to prevent shifting of the layers? You need to tie everything back into the timbers. What potential problems are there with SIP's? When installed properly there are no problems. Highly recommended to install a cold roof assembly over the top of the insulation layer, osb flat 2x4s another layer of osb, roofing membrane and sheet metal. If you are going with a built up insulation system, tape each layer and then no ice and water is needed on the pine, if you have water under the sheet metal you have bigger problems.
The insulation panels will have to be screwed down into the purlins which are 24” oc and taped. The problems with SIPs came up several times in this forum over the years. Apparently it is difficult to completely seal the seams so small cracks can develop as the panels contract and expand. As warm air condenses against OSBs, it will rot after a few years. Experienced installers are highly recommended and we don’t have those here.
By staggering the XPS panels I hope to get a complete seal. Also by putting an ice and water membrane on the pine boards, I want to prevent any air from passing through the joints. That may be overkill but I don’t want to fix leaking and rotting problems down the road.
I will definitely use 2x4 flat on OSB to allow for ventilation before putting down steel roof.
I think I read here not to use ice & water against pine board ceilings, due to possible odor or goo leakage concerns. You may need to overlay the pine ceiling with roof sheathing to create the roof shear diaphragm.
There are many peel & stick products that may be better.
EhvC,
I haven't done a roof with that thick rigid exterior foam, so my concerns might not be justified, but it seems like a bit of a challenge to do in three layers.
Each one will have to be secured to the roof decking to allow you to walk the roof and complete the assembly, meaning an awful lot of long cap screws of various lengths.
Also - especially with an impermeable membrane below - it's susceptible to wetting for an extended period of time during construction, and would be next to impossible to get dry if moisture did get into it.
Like you I'm very wary of SIPs, and if you can get the roof built as you have designed I think it would perform well, but it sounds difficult to get done to me.
Having multiple layers of insulation is a concern to me as well. I would prefer 2 layers of 5 or 6” thick.
If you go to a roofing supply store that serves commercial roofers you can get polyiso in thicker pieces. I know GAF is available up to 4.6".
Thank you.
12" of exterior rigid makes no sense except of you are trying for a certification such as passive house. In most colder climates, you'll get most of your energy savings with about an ~R30 roof.
The only way additional insulation makes financial and environmental sense is if you are using inexpensive insulation material such as cellulose. It could be possible with your roof, but won't be as easy as the rigid install.
With T&G ceiling, it is important to have a solid air barrier. You are on the right track with peel and stick as it is really the simplest. I would avoid any of SBS modified bitumen products as they can react with pine sap and could ooze. Something with an acrylic adhesive (VP100, Adhedro, EnVs etc) is your best bet. Since most rigid foam panels are low permeability, you don't need an additional vapor barrier.
Make sure to figure out how to seal the grooves between the T&G as they cross over your top plates. Since your T&G is already up, the simplest is to drill a 3/8 hole from the top about half way across the wall top plate and fill the hole with flexible spray foam or a flex caulk. Those small gaps between dozens boards can add up to a pretty big hole.
Above your final roof deck and bellow your metal panels, you'll need a synthetic underlayment. This doesn't need to be self adhered, anything rated for high temperature will work, I prefer to use a permeable one as it allows for a bit of extra drying capacity.
With a decently sloped metal roof, you don't really need any ice and water, but if you want, you can add it to the bottom of the roof or any questionable areas. It should go above your final roof deck not over the T&G. Make sure the ice and water is a high temperature, non granulated one. No point in covering the whole roof with it.
I am in zone 7 thus need R49.
I haven’t started building yet. The picture shows the same type of building as an example.
A peel and stick type of membrane should take care of the openings between the T/G joints, hopefully.
EhvC,
Unfortunately the Peel & stick membrane only stops the air leakage upwards, not horizontally at the exterior walls. You need to use foam or caulking to seal both the bottom of the boards to the top plate, and the t & g joint between the boards.
It is probably best if I put down 3/4” plywood first so I can prevent any air from moving upward. Stick the ice and water membrane on top of the plywood for added insurance. The pine boards will then have to be cut in 24” lengths and nailed to the plywood in between the purlins. Then look for 2 x R25 layers of insulation to go on top of the plywood. OSB on top of the insulation panels. 2x4 next and another layer of OSB. Steel roof can then go on last
With continuous exterior insulation, your roof preforms much better than most roofs. Most codes make a provisions for this and allows for compliance based on performance or U factor. This means less insulation and you might only need an R38 roof assembly.
For example, in your case, assuming 2x6 T&G roof deck this can be as little as 6" of plyiso. You can try different options with an online calculator such as this one that can give you assembly R values:
https://www.ekotrope.com/r-value-calculator
Assuming you are around 10000 heating degree days, each 1000sqft of R38 roof looses over a season 63 Therms. An R49 roof would only bring that down to 49 Therms. No matter what you are using for heat, with rigid insulation, the payback will be measured in centuries.
Your money is better spent on reducing air leaks or getting better windows.
It sounds like what your are trying to do is something like this Joe Lstiburek house:
https://www.buildingscience.com/documents/insights/bsi-081-zeroing-in
He does a layer of 3/4" plywood over the insulation, held on with screws that are 2-1/2" longer than the insulation is thick. In your case that means 14-1/2" screws. He also does 12" of fluffy insulation below the roof between the rafters and only 5" of rigid insulation over the roof.
Would you consider running 12" i-joists above the pine boards filled with batts or blow-in? Then basically the Lstiburek roof over that? I know it's more layers but I worry that you're going to have constructability problems. I also worry about shear loads and wind loads with 12" of foam.
I had not considered I joists. I will look at all of the options
I can't tell from the picture what size the purlins are but they look really small for the span. In that application they should be sized the same as rafters, and in zone 7 I imagine you have significant snow loads. Another reason to think about some sort of structure over the tongue and groove.
I am not sure about the purlin size however a local engineer stamped the design.
"OSB will be placed on top of the final insulation panel"
I would recommend using nailbase for that top layer, where the OSB is bonded to the rigid insulation. It simplifies and speeds installation. Some brands even have an option for integral furred ventilation channels between the foam and OSB/plywood layer all bonded together. Not cheap panels by any stretch, but you have to weigh it against the big labor and time savings.
It seems that with the pine ceiling and a peel & stick over the pine - that would stop the air flow problems that kill the SIP panels. That would allow a 12" thick SIP panel to be installed over the Pine board & air barrier. The SIP panel would be much easier to install than multiple layer roof.
Right, but at that point it can be an 'IP' rather than a more expensive 'SIP'. With nailbase, OSB or plywood is bonded to one side only.
I like that idea
Another factor to consider, not all panels are the same size. I used 8' by 24' panels which came from out of state. The more locally available panes are only 4' by 8'. Bigger panel, much less seams.
Can you get nail base panels in 12" thick? The SIP would cost more for material but less in labor to install. The SIP would come with a screw fastening schedule. The Nail Base panel with additional layers would need engineering.
Not in all brands, but quick search shows Thermapan has 11.75". Most manufacturers will provide a similar fastening schedule to SIPs. I've never specified that thick in one layer though--to reduce convective looping at the seams, I still prefer to call out a separate layer of rigid insulation underneath with seams offset. Last project we did like this i think ended up about R35 total.
I stand corrected.
I have not heard of that but this is all new to me. Doing lots of research this winter to make sure it is done right!
Post and beam is a lot like pole building. Which is a fraught thing to say because pole building is pretty much the cheapest way to build and P&B is close to the most expensive.
Pole buildings are a great way to get a lot of square feet out of the elements at a low price. The reason pole building is so much cheaper than conventional framing is that the metal skin acts as a structural member and you can omit a lot of the framing. Where a lot of pole builders run into trouble is that if you want to insulate the exterior and add interior finishes it turns out those framing members are necessary for supporting the insulation and finish materials, and if you end up having to add them back anyway you don't come out ahead with the pole building.
The reason I say that is that looking at the pictures, those purlins remind me of something you'd see on a pole barn. As I alluded in post #12, they don't look appropriate for standard construction. I haven't ever worked with SIP's but from what I can gather they are structural (hence the S in the name), and carry the actual weight of the roof. I don't think those purlins are structural, they just hold the pine boards, which aren't structural either, they're just an interior finish.
What I'm getting at is if you have a roof that is designed with SIP's, you can't just replace the SIP's with another form of roofing, they're part of the framing of the building. If you don't want to use SIP's I think you're going to have to go back and come up with new design for the roof support framing. My guess is the simplest way is to have conventional rafters, which has the added benefit that you can then get most of your insulation from fluffy insulation and generally use more conventional construction techniques.
Using 3/4” plywood on top of the purlins should do it but a local engineer has to approve it first. The building in my picture is all done but is being used as a garage instead of a house.
Does that garage have a SIP roof or something else?
If the purlin spacing in the picture is 24" it looks like they're spanning about 12'. With a 50 lb snow load you need at least a 2x10 to span that far with 24" spacing. In the picture it looks like 2x4 or maybe 2x6. The span tables assume the roof has sheathing so adding 3/4" plywood isn't going to make a difference.
I'd believe that a SIP can span 12', especially one 12" thick. Then the pine boards are just interior finish and the purlins just support them, they aren't structural.
This building has 2” or 4” insulation panels but not SIP. As far as I know the purlins are large enough to support a snow load but I will know more after the holidays.
The purlins are a true 4” x 6” and 24” OC. The pine is 1” with 2 layers of 2” R10 panels. OSB layer next followed by steel.