Sealing up rim area on brick veneer house.

Working on re-insulating the ceiling of the tucked-under garage on a 50 year old brick-veneered Cape Cod in the Philadelphia area. Ceiling demo was done earlier this week. On inspecting the rim areas I find that the 2×10 joists sit directly on the cement block wall with only some slate pieces under most ends, perhaps for leveling and alignment. There are no wood sills and no rim joists. Looking in, I am seeing the backs of the brick veneer with small piles of dropped mortar from the brick laying process. Overall, the bricks and mortar look fine. The joists end with about a 1″ gap to the bricks.
My intention had been to seal the rim areas with 2″ solid xps foam blocks sealed with Great Stuff Pro Gaps & Cracks foam. This will not sit well towards the outside of the foundation because of the mortar piles. I could back this assembly up closer to the mid-foundation position or to the inner foundation edge, but that would leave part or all of the joist ends in a potentially damp spot. Had thought about using closed cell spray foam, but current temperatures make that problematic. Then I listened to this week’s FHB podcast about insulating old brick houses and realized that I had better ask some questions before I proceed on my own.
Is there a best practice for this situation?
GBA Detail Library
A collection of one thousand construction details organized by climate and house part
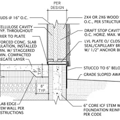
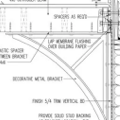
Replies
Some pictures would be useful, but I think I understand the construction
It's probably worth jacking up the house a smidge long enough to slip in in some sheet EPDM (membrane roofing material) as a capillary break, then going ahead with a cut'n'cobbled rigid foam approach. This type of project sounds worse that it really is, but it's easier since you don't have a band joist and the joists can be lifted one or two at a time. The capillary break keeps ground moisture and wet brick moisture from wicking directly into the joist, which would be far riskier than just having the joist exposed to the cavity air behind the veneer. As long as the wood isn't in contact with masonry it's pretty safe to go ahead.
Leave at least an inch between the brick veneer and the exterior face of the rigid foam, but if it has to be 3- 4" that's fine too, as long as they're all about the same distance, and there's a capillary break between the wood & masonry.
Instead of XPS, which is blown with HFCs with extreme global warming potential (> 1000 x CO2) use EPS, which is blown with pentane (~7x CO2). Better yet, use reclaimed roofing foam (any type), which doesn't use any new blowing agents or new polymers. It's ideal for a cut'n'cobble project, since it doesn't need absolute geometric perfection. It's very cheap too- less than 1/3 the cost of virgin stock goods.
If using polyisocyanurate foam it's better if the cut edges aren't in contact with the masonry, without a capillary break. But with EPS or XPS it's fine.
If you're going to insulate the whole foundation (recommended) run this search every now & again- there's almost always somebody demo-ing a commercial roof with low priced EPS or polyiso for sale (like the reclaimer in Allentown selling polyiso by the pallet load):
https://philadelphia.craigslist.org/search/sss?query=rigid+insulation
https://reading.craigslist.org/mad/d/polyiso-rigid-foam-insulation/6375903662.html
Dana,
Thanks for your quick reply. I had posted this question a few days ago, directed towards a GBA advisor, but had not received any answers.
Trying to add a photo of a typical joist bay to this note, but it does not seem to be loading.
Last weeks FHB podcast featured a discussion of rim area sealing and insulation on old brick buildings with the brick walls being multilayer, structural and weight bearing. Apparently there have been some disasters with adding interior insulation to these walls causing trapping of moisture and ultimately crumbling of the brick due to freeze/thaw cycles. Also concerns about rotting out the socketed wood beam ends.
From there, I went on to read Martin Holladay's article on the GBA site about "Insulating Old Brick Buildings" (March 19, 2015). I came away from that thinking that I should use a thin (1") layer of spray foam insulation against the bricks and behind the joist ends. Messy and expensive, but doable.
Went to the Home Depot site and found that their available 2 part spray kits (Touch 'N Foam) state that they need to be used when the air and walls temperatures are over 60 degrees. Well, our weather is not cooperating. Looked up the Dow product (Froth-Pak spray foam sealers and insulation) via Lowes, but they are not giving any application temperature guidance on line and Dow's phone customer support lines are down today (!).
As you can't see from the photo, the joists are all elevated off the cement block by about 2 slate roofing shingle pieces. There is no evidence of any moisture damage to any of the joist ends, so this must be working for the last 52 years. If I jack up the joists and place EPDM under them, they will each loose about 1/2 inch without the slates. (Lots of the slates are cracked and will not be able to be slipped out and replaced.)
Not planning to insulate the garage walls at this point. Insulating the ceiling will make the garage unconditioned space. Mostly want to seal and separate this area from the living spaces above. I do plan to insulate the basement walls in the future.
Appreciate your experience and input.
Jeff