Slab-on-Grade vs. Pier Foundation for Conditioned Shed

Planning to construct a new 10×12 shed that will be finished, conditioned and utilized as a permanent work from home office. Heating and cooling will be via a ductless mini-split, and supplemented with a pellet stove. I am currently working through foundation details and debating between a slab-on-grade or pier construction tradeoffs. The site is level, and fairly-well drained, but Pennsylvania can get and stay wet.
Option 1: Slab on Grade: I would install a layer of rigid foam below the slab (similar to GBA detail sheets), but I am concerned that the slab floor would still be very cold throughout the winter (radiant heat sink?). I live in Pennsylvania so winters can get quite cold. Would it be best to also insulate on top of the slab? Possibly with a 2×6 framed floor? Temperature is important as this is to be an office (mostly stationary) work space.
Option 2: Pier Construction: This option is attractive in that thermal bridging would be greatly reduced. I could sheath the under-side with rigid foam (under the joists) and then a layer of pressure-treated plywood below the foam. The joist bays could then also be filled with rockwool. My concerns are a) moisture from below (rotting the plywood over time – PA is very wet usually) and 2) rodents chewing from below to make nice cozy homes in the joist bays.
I like the slab option the best for durability, but the space needs to be comfortable.
Thanks in advance for any advice on best route to take.
Ken
GBA Detail Library
A collection of one thousand construction details organized by climate and house part
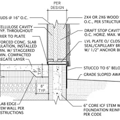
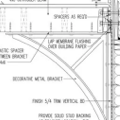
Replies
At 10x12 you may not need as much heating as you're thinking. Do a decent job air sealing and you could probably get by with a space heater.
As far as the foundation, a slab will be cold, especially at that size since it's a lot of perimeter exposure. The pier built shed can mitigate the rodent and moisture issues if detailed for it. I've built quite a few sheds here in the very wet PNW without moisture problems. Sheet plastic and course gravel usually does the trick as long as you don't put the floor joists in direct contact with the ground.
Although I haven't done this particular assembly, I'd consider a sandwich of Advantech with rigid foam or rockwool between the floor joists. Advantech on the bottom will keep the critters out and it's fairly good at moisture resistance.
Ken,
As Andy said, I don't think you will be able to find a mini-split or pellet stove with small enough output for a shed that size. with good levels of insulation and air-sealing a small space-heater will be all that's necessary.
If you go with a pier foundation, the easiest way is to frame the floor upside down. Once you have the foam and plywood installed (remember to block where the beams bear) You can flip it into place, without ever having to work underneath in a cramped space.
Thanks Andy and Malcolm. Those are helpful responses. I will certainly look into the mini split sizing. And Malcolm, very good thought on constructing upside down!
Is there a rule of thumb about not using the “fluffy stuff” insulation in a joist bay on an exterior building? I seem to recall reading this one time, but I could be mistaken. It was in reference to avoiding rodent habitat.
Also, Andy you had mentioned plastic and course gravel. I assume the plastic is under the gravel...can you give more detail on that? I would assume under 3 or 4” of gravel, and make the gravel 12” wider than the structure?
Also, how high would you ideally set the joists above grade? Maybe a 12” gap?
I appreciate the help.
Ken
TBH, I don't even think the plastic is worth installing in most cases as course gravel is a capillary barrier, but homeowners usually can't wrap their heads around that so we'd put plastic down because then they think it's waterproof...but oh well, it still works especially if slightly sloped.
A 12" gap plus the floor thickness is going to make for a big step into the office and necessitate a couple stairs or a small deck. You only need an inch or two really. Just enough to not be in direct contact with the ground. With enough gravel, you could be in contact and be fine, but I like the gap so that air can circulate and allow drying.
Andy thanks, that’s really helpful. I think I will forgo the plastic. I have a very flat spot and very rocky soil with decent drainage. The plastic may end up working against me by retaining water. But I do like the gravel idea and get that typically you would slope the plastic.
Can you explain the capillary break concept? That’s new to me. I assume you mean that it keeps water from wicking up onto the structure from below?
Good clarification on height too - just enough to give some airflow.
Thanks
Ken
A capillary break is something that stops the wicking of water. In this case the course gravel can drain water through it, but ground water won't rise up through it like it would through wood or concrete or a sponge. Not a very sciencey explanation, but that's the practical application.
If you go with pier construction, this article should interest you: Air-Sealed and On Piers.
Thanks Kiley - great reference!
Ken
Is a slab on grade with insulation above ground an option here? It's arguably less work, and you're not wasting energy heating / cooling the mass of concrete.
Compacted soil -> fabric -> gravel -> vapor barrier -> concrete -> XPS -> subfloor -> flooring.
With the price of lumber, those joists / posts would certainly add up quick compared to about 2 +/- yards of concrete for the slab. You still need the subfloor in either case, and the insulation is really just in a different place.
One of the big reasons we never did slabs on sheds or backyard offices was because they'd then be considered permanent structures and require permits. Here, that could cost as much as the build in some cases. Placement was a little more lax too with less concern about setbacks being enforced on smaller in city lots. Another benefit of building on blocks or small piers was that the structure could be moved or removed when the owners needs changed. As much as everyone thinks that what they build will be there forever, these small outbuildings get taken down quite frequently.
I’ve never built a sub floor on top of rigid foam. Would it be spongy? How would you build it? I assume you mean something like two offset layers of 3/4” subfloor directly on top of the foam? How thick XPS? 2” maybe? What about EPS with foil (foil side up?). It’s a very good thought - worth some consideration.
Although Andy does raise a good challenge about permanence. If built right, and probably with some heavy equipment, it could be relocated, even sold if the need changes.
I've never built one like that either, just used rigid foam in between joists/sleepers. Different foams have different compressive strengths and XPS is used under slabs all the time. Granted the concrete is strong, but with a spread load the foam shouldn't compress much. Interesting idea and I'd like to hear from someone who's done it before I'd try it.
Also a note on foam types...XPS has a huge global warming impact compared to other types of foam. There is a "greener" variant available or coming soon, but you should consider the alternatives if this is important to you.
For a given amount of floor insulation, slab on grade will result in a warmer floor than piers. A "rug heater" will make the floor warm for an office/desk situation.