Troubleshooting Mold at Top of Stud Bays

We’ve been in our new home I built for maybe 3 months and I’ve found evidence of mold forming at the top of the exterior wall stud bays on the interior side of the sheathing.
We’re in Maine, climate zone 6. And I’ve built to be air tight following a lot of details I’ve found on this website and others. We have a walkout basement, with one story on top of that for living and a standard ventilated trussed attic outside of the living space. The wall assembly from inside to out is 1/2 Sheetrock, 2×6 studs 24oc, roxul comfortbatts r23, green zip sheathing with taped joints, 2” of roxul comfortboard r8, with strapping and screws then vinyl siding. My primary air barrier is the zip system, and I carried that over the wall beneath the trusses with grace ice and water shield, then taped to that on my ceiling with Intello plus to create my envelope.
The issue I have is that I’ve found remnants of mold mostly at the top of my stud bays and since it’s still winter here, the interior side of my sheathing is cold and somewhat damp, not bad but slightly. I was
hoping my exterior insulation would keep it above dew point but I don’t think it’s enough during these temperatures.
The mold isn’t in every stud bay as I’ve opened up several and so far found the southern facing side to not have any and more dry sheathing but the colder walls seem to.
I have a couple theories, one being since I didn’t install a smart vapor retarder behind the drywall I’m now getting too much vapor drive into the walls, even through the latex painted drywall.
My other theory is that we did have a significant humidity event when we spray painted the house. The plastic over the windows were drenched in water and you could tell there was a lot of moisture in the air from spray priming. And the mold and moisture buildup is remnants from that and since it’s winter, the walls just haven’t completely dried giving the mold a chance to grow.
Our interior humidity is pretty normal, ranging from 30-50’s rh.
I just want to know if I’m going to need to take exterior wall drywall down to install a product like Intello on the walls so that the vapor drive isn’t so bad, or if the walls will eventually dry out more in spring and this problem won’t be a repeating cycle every cold season.
I didn’t think I needed the Intello on the walls because it was a redundant air barrier, but I didn’t think about the vapor drive in winter. The roxul isn’t paper faced so I’m really relying on the painted drywall, but is it enough in my climate to keep
healthy walls. Or am I just freaking out over an issue that came from the building process and will resolve itself instead of remodeling.
Thank you.
GBA Detail Library
A collection of one thousand construction details organized by climate and house part
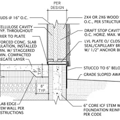
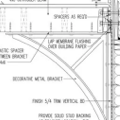
Replies
equalizer,
Not sure, but a few questions and thoughts:
1) How have you discovered this mold? You busted into a finished wall out of suspicion of this mold or something?
2) Are you sure there is no interior air flow to the sheathing?
3) Your exterior insulation doesn't meet the code recommended R value for using only a class III retarder, but the idea is that it shouldn't matter since you used roxul and its so vapor open.
4) I have no experience with it, but they do make special vapor retarding paints that can get you to class II. If you have a wall open, you could consider putting a moisture meter in there against the sheathing to monitor, if that's your kinda thing.
equalizer07,
Tyler has given you some good suggestions.
If I had to guess I'd say it was due to a) the walls being closed up before they were dry enough, and b) the time of year, meaning they they stayed cold and damp. I doubt the lack of a vapour-retarder was a major factor, and the problem will probably stop once the walls have had the chance to dry in the spring.
Thanks for the reply, I opened the wall in one of my closet walls out of suspicion because I had insulated my walk out wall without putting any barrier or drywall on it and I found lots of mold behind that insulation. Kus the sheathing was cold and had condensed with moisture.
To your air flow question, I’m fairly positive I’m air tight on the zip sheathing, but on the interior drywall I didn’t take any special precautions to “seal” out the the interior air. My assumption was the zip sheathing being air tight wouldn’t draw any air flow through the walls. For example my electrical boxes aren’t sealed. But trim is on etc so there’s no gaping holes anywhere.
And yes on the exterior the roxul is vapor open, which is why I used it so it was safer and I didn’t have to pay for more insulation. It was quite expensive as well as the increased difficulty of details for going more than 2 inches.
And yes I’ve seen the paint in my searches.
I haven’t finished all the siding so I could maybe add another inch of foam to the strapping but I just didn’t like the idea of having foam outside and running the risk of retaining moisture.
I'm not sure adding thin foam outside your roxul is a good idea as it creates a condensation plane inboard of the foam.
If it is truly vapor diffusion, the simplest solution to me seems to be adding vapor retarding paint.
Yeah, I agree but my thought was since it would be sitting on the strapping I used to hold the roxul on it would be back vented from top to bottom. Granted it still could condensate but at least it had drying potential. But I’m also not convinced just one more inch of insulation would do the trick. Maine is mostly climate zone 6 but up north is 7 so it’s not like we don’t see those conditions here.
William_07,
Unfortunately if the foam is mounted to strapping with a vent space behind it, there will be very little increase in the R-value added to the exterior.
Yeah that crossed my mind
That venting would more or less obviate the R value...so I would not do this.
Appreciate the confirmation
Hi William,
Have you conducted a blower door test?
Are you monitoring the interior humidity levels?
Do you have a ventilation system (ERV/HRV) in operation? Is it balanced?
I do have an hrv but I haven’t finished the system so it’s not running. And I have been monitoring the humidity level as of a couple days ago and it seems to range from 30-50’s. We’ve been running wood heat and it’s less humid nearest the stove.
Maine's building code requires at least R-11.25 exterior insulation over a 2x6 wall if you want to eliminate the class 1 or class 2 vapor retarder. Those rules are derived from Building Science Corp research, which also assumes that the interior relative humidity is kept within a normal range--I forget the specifics but I think it's a maximum of 40-45% in winter. While Comfortboard is vapor-open, the Zip sheathing is only semi-vapor-permeable so without better interior moisture control, and with elevated humidity, I am not surprised that you see some mold.
If you did not have the exterior insulation you would have similar or perhaps worse results. If you had more exterior insulation, or a variable permeance membrane on the interior, and if you controlled your indoor humidity, I don't think you'd see the mold.
Thanks Michael, what would your best advice be on how I should proceed? I’ve considered taking drywall off and installing Intello. Or add like an inch of foam on the outside to get above that threshold. I haven’t finished siding and most of the house is just comfortboard and strapping. I could add an inch of foam on the strapping. What do you think?
No I haven’t done a blower door test, I always wanted to, but never followed through.
And for further information if there is mold it’s always at the top 2 feet of the wall and steadily disappears down the wall to nothing.
Moist air rises, so it makes sense that the mold would start near the top and be less in the lower areas -- the upper areas are probably the most wet.
The reason I always build exterior walls with air tight drywall and a smart vapor retarder (typically MemBrain, since it's least expensive) is because I've seen mysterious mold problems before that are similar to what you're seeing. I like to go belt and suspenders in the beginning in an attempt to head off problems down the road that can be difficult to fix.
I'd keep an eye on things, since you might have just had an excessively moist season due to the work you've been doing, which is a worst case scenario for those walls. If they show the issue next season too, then it might be time for more drastic measures. My first thought is to try a vapor barrier paint to see if that helps, and I'd check for air leaks too. More exterior insulation will also help, but even then I'd still try to seal up the interior drywall to minimize the chance of problems down the road.
Bill
Thanks for the reply Bill, I think you’re right as to what’s happening. That seems to be the trend as I’ve opened up a few areas to discover what’s going on.
The painted drywall has done some resisting to the moisture but near the tops of my walls is warmer and more humid for sure so it’s more susceptible and any moisture will congregate up.
For example I had a walkout shower planned for my master bathroom so I had some durock screwed onto the exterior wall where the tile was to go. Knowing that the durock is pretty vapor open being cement board, I had a feeling that wall would be wet, and it was. Then I opened a stud bay to the left of it which had painted drywall and it was no where near the same.
As I said before I had put Intello membrane on my ceiling mostly because it was my air barrier and figured my taped zip sheathing as my primary air barrier would be fine. I didn’t think about this vapor drive situation so I completely neglected that science. I was real close to putting Intello on the walls because why not, but it was time and money and we were eager to move on. Definitely kicking myself for that now.
With all of the evidence I’ve gather from this post and some testing at our house the smart membrane is necessary for the longevity and health of the walls. So for now, I think we’re going to tackle one room at a time with exterior drywall removal so we can still live here. I’ll put up the membrane and seal my drywall and electrical boxes.
Wish me luck.
William,
So how long has drywall actually been up and fully painted? As pointed out, your original high moisture content could be of significance.
Your proposal to remove all the drywall to install intello strikes me as a bit extreme, but it's your choice!
Is there a reason vr paint is out of the question?
Count me as one that's SLIGHTLY skeptical that the mold is at the top of the bays simply due to 'warm humid air rising'. So is convective looping in single story exterior walls standard? I'm not saying it's not the reason but it's interesting it would manifest to such a degree.
Hey Tyler, so far it’s the only answer that has made the most sense. I don’t discount that we had a seriously high moisture event to begin the house. And there was probably a month or so where we had insulation and no drywall during the cold season. Our heating system wasn’t officially in but I had a wood stove hooked up to heat some.
The other thing is our walls are 10 feet tall, (we wanted tall ceilings) so when you get up to the upper 2 feet of the wall the temperature is noticeably warmer and obviously more humid.
Since we’ve been living here I don’t think our humidity has been out of control, seems to range from 30-50 in different areas but I still plan to finish my hrv etc.
It certainly could be that the mold is a remnant from an extremely wet period and it just hasn’t had time to dry. I don’t expect the sheathing to be bone dry with my current setup, but there does seem to be enough vapor getting through to at least wet the sheathing. And it seems evident from opening up some drywall at the top of the wall that any wetting is concentrated as you move up the wall.
When I took off a piece of durock cement board it really showed to me how having a more vapor open material can significantly increase the water diffusion. So with that evidence to me it seems like water diffusion is the culprit.
It gives you a pit in your stomach to see mold in a house that you’ve spent a lot of time building and just moved in. And I’m just not one to let things be so maybe that’s why I want to remove drywall. But honestly so far it just seems like no vapor retarder is the issue.
I could paint it, but then you have something that’s stuck at that perm rating when comparing to something like Intello that is vapor variable.
The only other thing I can think is that it could be concentrated over our radiator panels where there’s more convection.
Michael's reply in post #6 pretty much lays out the options. Yes you can do a better job air sealing, but keep in mind that the bottoms and tops of the stud bays, floor/wall plate interface, electrical penetrations in the top/bottom plates etc. will continue to leak warm/moist air into the wall cavity if they have not been properly dealt with.
However, if you add another 2 inches of exterior insulation, all these issues go away. I'd look at labour and costs, but the exterior insulation taken to R12-16 would be a safer wall long term, no? That said, with siding and strapping already installed, I can see why you'd want to focus inside.
50% is too high for interior RH which is not helping. You'll want that HRV running sooner than later as new construction comes with all the VOC issues too on top of moisture loads.
Hey Dennis, I agree with you that sealing penetrations will be important. I’ve got a continuous air barrier with the sheathing that I’ve been careful to keep sealed. But I can agree the moist air can still navigate through holes into stud bays. If I do remove drywall I’ll be sure to seal those up.
Im always a fan of more exterior insulation, before I started the house it was my hope to have more than what we put on, but because of cost and just the fact that wall details start getting harder the thicker your exterior insulation gets we settled for 2 inches of comfort board and I felt safe because it wasn’t foam and it was vapor open.
I don’t have all the siding done, just 2 walls and they’re not huge so I could remove it. My only concern is my window bucks and penetrations are sized for my current insulation depth, so those details could get a little wonky. One thought I had was attaching 1 inch of eps onto the strapping which would allow me to still get siding through the foam into the strapping. Bringing the insulation up to r12. I’ve got extra 2” comfortboard but adding 2 inches just seems like it could be a pia. I dunno.
It boils down to cost/labour. Redoing all your drywall/class II vapour/sealing , vs the exterior work.
Something not mentioned so far is the water coming from the concrete slab/foundation. How long has it been since the concrete was poured? There is a tremendous amount of moisture that works it's way out of the concrete early on in the life of a house. Get your HRV going and monitor your indoor humidity level, then decide if any further action is needed.
Doug
Hey Doug, the concrete was definitely dry. Our basement isn’t sealed off from the main house so we could be getting higher humidity from having an open stairwell to the basement. But I agree with you. My first plan is to get the hrv going starting this weekend.