Should I stay with tried and true?

(Apologies in advance for the long introduction and somewhat vague nature of my questions.)
About 18 months ago, my wife and I moved into our second custom house. (Green Building Advisor was a great resource throughout the process, BTW.) It has taken a while, but we are now close to getting our Earthcraft Platinum Certification. Hurrah!
We also are planning to sell the house and build again. Long story short, I have developed some health issues and a 1,500 square-foot, one-story house will be a better fit for me than our current two stories over a basement.
We have found a plan we like and will consult with the architect to determine how they would improve the design if building it again. This home is the architect’s personal residence, and it is constructed with a red iron structure (for large clear spans) and lots of rigid foam (to prevent thermal bridging and provide insulation). The exterior design and interior layout are very simple.
We could simply replicate the architect’s approach, but I’ve been reading about cross laminated timber and CNC precision lumber flat packs and wondering if these systems might be more cost effective, simple, and resilient. I tend to get excited about new systems and technologies, which can be a good thing and a bad thing.
After doing two homes, I really would like to avoid the traditional site-built process and prefab most or all of the structure in a controlled environment. Whatever the approach, I want components that are made with precision so they can be assembled by the kind of workers who typically work on mid-budget custom homes in our area. Framers and carpenters here usually have little or no formal training in their occupation and often don’t enjoy having to learn new ways of doing things. It is easier to find good subs among the licensed and certified trades.
However we build, the new house will be very efficient. I learned a lot while planning and overseeing our last build about green construction, sources for healthy materials, and where to go for technical advice.
So what do you think? Should we replicate the architect’s site-built strategy (with improvements), or should we potentially complicate the process by introducing new materials and/or seeking out ways to prefab some or all of the home?
PS. I literally don’t have the energy to manage and problem-solve this project the way I did with our last build.
GBA Detail Library
A collection of one thousand construction details organized by climate and house part
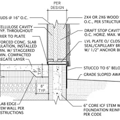
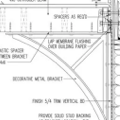
Replies
I think you might have answered your own question in the PS. But a few questions that come to mind are whether the architect is in your area, and where you are located, in case some of use know of resources in your area.
As usual Charlie's advice is sound. Building houses can be stressful in the best of circumstances. Perhaps this isn't the time to add complications to your life.
Easy solution: choose materials and methods that give you what you want without needing to be modified or altered or for the contractors to learn anything new (perish the thought). For example, ICF walls and tile floors.
Charles, Malcolm, and Nate.
Thanks for responding to my post on a Sunday.
We live south of Atlanta, and the architect who designed the house we admire lives in Miami. We will consult with him and have updated plans put together, but I do not think it will be affordable to bring him in for site visits.
This time around I am leaning toward hiring someone to do site checks and quality control monitoring. Over the course of my last build, I got to know someone who might be a good fit for that role.
While I am not articulating it very well, I think I am most concerned about going through another 9 to 12 month long conventional build process.
My preference, which may be unrealistic, would be to use a custom prefab or flat pack approach--if I could identify a quality manufacturer. One of my neighbors bought a high-end flat pack from a well-known company, and he had numerous problems with inaccurately cut pieces that had to be modified in the field.
If someone knows of a company that does quality, customized prefab or flat-pack work, I think that would be helpful. It would be even better if the company's production process is largely automated and computer-driven.
Steve,
Maybe it's a regional thing, or maybe there is a lot more complexity to the houses you have had built from the ones I do, but I never have had a project take more than five months. This summer two of us built a 2100 sf house with attached three bay garage in five months. we didn't have any help, except for the excavation, until siding and roof was on. I can't see how a simple, but well designed house should take any longer.
Malcolm:
I watched many homes go up in my community over the last five years. They always take 9 months to a year. Thing is, most of these houses are using "standard" construction methods. The builders aren't doing anything complicated or cutting edge. I agree that it should not take so long. It seems to have a lot to do with the mindset of the builder community.
You would think that the custom homes would be completed faster, but they seem to take as much time as the spec houses.
Steve, you might want to check out EcoCor High Performance Buildings: http://www.ecocor.us/.
They build flat-pack, mostly foam-free, panelized Passive Houses, use all zero-VOC materials, have designers who can work with you but they will build plans by others (with necessary modifications), etc. Full disclosure, I used to work there and helped develop the systems, and still consult regularly.
They build to the highest quality (framing tolerances +/- 1/16", routinely achieve air tightness of <0.3ACH50, and went through the stringent process to become the only manufacturer of Passive House building components outside of Europe to have their system and products certified by the Passive House Association.
If you are more interested in the "Pretty Good House" approach than full Passive House levels of performance, however, don't waste your time. I am still a "PGH" fan (I wrote the original blog posts about it) but EcoCor makes it easy to reach Passive House levels of performance. As for pre-fab vs. site-built, I've heard horror stories about modular homes. After building many houses and renovations on site, now that I have experience with panelized construction, as long as it's planned properly I would not want to build any other way.
Hi Michael:
I wish I had known about Ecocor before starting my current house. Many of the designs are very similar to our "modern barn." While our 1.1 ACH50 isn't bad, it would have been nice to achieve .3 ACH50.
Steve,
You list two options -- steel framing or cross-laminated timber -- as if they are the only options. My guess is that there may be other options.
You should at least talk to representatives at a truss company to find out whether floor trusses or roof trusses can provide you with the long spans you desire.
Hi Martin:
Just to clarify, I am open to all options but overall want a system that will deliver good results with less drama and a shorter build timeline.
Nice looking house, Steve! It definitely fits the EcoCor aesthetic. They use a mix of engineered wood products to provide large spans, rarely needing to resort to steel, although that's an option if necessary--as long as the steel is entirely within (or without) the thermal envelope. I don't have experience with CLT and I'm not convinced it makes sense on a residential scale.
Thanks, Michael.
My wife is responsible. She has been passionate about architecture and design her entire life (although working in another field). I am attaching a couple of photos of our first home.
As much as we like the Miami design, we probably could use one of EcoCor's standard models. The Short House and Long House are similar to another home that is on our short list. We really like clean aesthetics and efficient use of space. The building industry seems to really struggle with delivering designs that incorporate those qualities.
We will investigate and see if this approach will fit our budget.