Sound transmission in strapped service cavity?

Has anyone experienced increased room-to-room sound transmission in a house with a strapped service cavity (either ceiling or wall), and no insulation in the service cavity?
I am not facing this issue currently, it is just a concern I had when reviewing potential wall assemblies.
GBA Detail Library
A collection of one thousand construction details organized by climate and house part
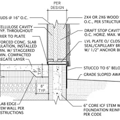
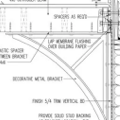
Replies
Yes, kinda... I'll explain:
I've had issues with some tenant spaces in office buildings where the walls for offices don't line up with the mullions for the windows (these are buildings where the entire exterior wall is glass). The walls stop, leave a gap of an inch or two near the glass between the windows, and that leaves a "sneak path" for sound that is very noticeable.
Since you'll have drywall over those gaps on the strapping, you should have less issue than the commercial buildings with the problem I described earlier, but you'll still have more sound leaking through than you would without the gaps between strapping. I would do one of two things here: run a vertical piece of strapping so that the interior goes all the way up to the exterior wall with a solid connection, then run the horizontal strapping out from that vertical piece. That is maybe a little more cutting of strapping, but not too much.
Second option is to pack -- and pack it HARD -- mineral wool into the gaps between strapping to act as a sound block. I suspect this would probably work just as well as the vertical strapping, since you're only dealing with the sound that is resonanting the unsupported span of the drywall between the strapping, which should be much less than if the "hole" was open between the air spaces INSIDE the two rooms, instead of just inside the wall itself.
Bill
mack_m,
Service cavities are really just more interior walls - just like the ones you have separating the rooms in a house. So it makes sense to treat them the same. If you aren't insulating the interior partitions, there isn't much point in insulating the service cavities.
I would think the service cavities need to be fireblocked, which is all the sound blocking that residential interior walls typically have.
Hmm. That's an interesting thought that I didn't think of. Usually fireblocking goes in VERTICAL cavities, but horizontal cavities between rooms could potentially pose a problem too. Either "stop up the hole" method I detailed above would work as fire blocking though, so it's very simple to add.
Bill
Excellent point about fire blocking, I did not consider this. Furred spaces like service cavities are specifically called out in the IRC code:
"Fireblocking shall be provided in wood-framed construction in the following locations:
1.In concealed spaces of stud walls and partitions, including furred spaces and parallel rows of studs or staggered studs, as follows:
1.1.Vertically at the ceiling and floor levels.
1.2.Horizontally at intervals not exceeding 10 feet (3048 mm)."
mack_m,
Don't forget that you can use batt and cellulose insulation as fire blocking (R 302.11.1 (7) and (8), which may solve both your problems.
I completed a 9000 square foot commercial project with the furred air space assembly (service cavity) on all exterior walls. This included tenant spaces and a dedicated film studio, all which needed to be sound isolated. Service cavity was created using 2x3's horizontally fastened at 16" centers over 2" of EPS. The studio area in particular had an STC 70 target, so the shared service cavity was a flanking noise issue only on one exterior wall.
No fire blocking was required with furring in the horizontal orientation, but 5/8" type X was required at interior.
All we did is ensure that the service cavity was insulated at wall partitions. The bulk of flanking noise attenuation was dealt with by using dedicated HVAC, and acoustically lined ducts for all tenant partitions with shared HVAC. The studio was build with double walls, resilient channels on both sides of that assembly and a floor that was dense packed with 18" cellulose. The building performed extremely well with respect to sound attenuation.
Heating efficiency of that 9000 square foot space exceeded our 1800 sq/ft retrofitted home.
An important question is whether the service cavity should end at partition walls or continue through them.
It seems to me that the only situation where you would want a continuous service cavity is if you're using continuous interior foam insulation, because you would avoid bridging by doing so. Otherwise it seems that there are a lot of advantages to not having the service cavity continuous. The big one is constructability, if the service cavity isn't continuous you can put up the exterior walls and partitions and then come back and do the service cavity.
If the service cavity isn't continuous there is no concern about sound transmission or fireblocking.
It seems to me that whether or not the service cavity is continuous you're going to need to block the corners for drywall, which effectively makes the cavity discontinuous, fireblocked and sound blocked any way.
In our case, there was a continuous internal layer of 2" foam on the interior, the radiant reflective vapour barrier, then the furring strips, so the partition walls were all framed after. This makes a continuous vapour barrier a lot easier to manage. Wiring was also pretty straightforward, and all done with near zero cavity penetrations. When you drywall etc. there would still be an opening at the service cavity, unless you insulate it. The code fire barrier in this case is the interior drywall. None of the interior walls were corner blocked to the cavity as you've got horizontal furring every 16" on the exterior service cavity.
In wood framed construction the drywall doesn't meet the requirement for horizontal fire-blocking every 10 feet.
But the horizontal 2x3 furring every 16" does. Between the architect, our rather stringent commercial fire code, structural engineer and numerous inspections, no one raised any issues.
The floor structure went straight to wall structure, so was in place before the service cavity / interior foam work, and none of the walls exceeded 10 ft in height either. That said, in a fire, having a 2" layer of foam on the inside of the structure would not be ideal (IMHO)...regardless of the fact that it passed code.
The loading bay was 20 ft high, with 2x3 horizontal furring in place over the foam (again, installed horizontally) at 16" intervals on exterior walls.
Since it's commercial, are you using steel studs? Because read what post #5 above says.
Although that's IRC. But I can't imagine commercial codes are less strict.
Commercial fire codes are MORE strict, but sometimes in different ways. An example is that commercial buildings often have real firewalls -- you'll see those in office buildings with a double door that is held open by electromagnets on the walls. Those doors will automatically close (the electromagnets will release) if the fire alarm goes off. If you open the ceiling and look above the door, the wall will go all the way up to the structural ceiling (the floor of the level above), and not just stop at the ceiling grid the way many other walls do. That wall will be all taped and mudded up there, and every penetration for wires and pipes should be firestopped with red fire caulk. The idea of that fire wall is to slow the spread of fire past that point. Interior stairwells are also built to high fire ratings, I think either 2 or 3 hours (I'd have to check to be sure which).
Commercial buildings are usually built with noncombustible materials, primarily concrete and steel. You don't have the issue of fire burning up in a "chute" formed by wooden studs. I don't see normal steel studs being fire blocks though, since steel studs typically have many holes punched in them at the factory, so they tend to be open. Not ALL are that way, but most are.
Where commercial fire code is much more strict is in those fire barriers, especially penetrations. As an example, I had a recent project with a floor penetration between the 6th and 7th floors. It was sleeved with 3" EMT conduit, and a large number of data cables passed through. We sealed the perimeter of the conduit to the floor using fire caulk, then we stuffed the conduit with mineral wool until it was packed tight. Last step was to cover each end with moldable fire stop putty to seal the ends of the conduit around the cables. That's what is supposed to be done to pass. The idea is to stop the spread of fire AND SMOKE through the penetration.
The stupid thing is that the floor boxes (power outlets in the floor) just press fit in the holes with no gasket and no fire stop caulk needed.
I think the big difference is that in residential wood framed construction, the structure itself will burn relatively easily, so there is a lot of emphasis on stopping the spread of the FIRE. In commercial concrete and steel construction, the structure itself is realtively fireproof, so it's primarily the stuff inside that burns (furniture, etc.), so the emphasis is on stopping the spread of SMOKE, although also stopping the spread of fire. Commercial fire stop stuff is thus supposed to be air tight.
Bill
DC,
I think Dennis Wood is up here in Canada under the OBC.
Yep.
No, this is the wall structure...no metal studs. Fire code on this project was a major PITA with the five air handlers, shared spaces, etc. A lot of money was spent on single and dual layers of Type X, along with a pile of fire dampers for all the HVAC penetrations. Ontario, Zone 7A, commercial code..about 8 years back.
If vertical blocking at 10 feet was required, there would be quite a few who missed that detail between the design team, permit process, and on site fire inspection. Doing it again, I'd have spec'd rock wool instead of foam for that interior 2" thermal break.