Standing-Seam Metal Roof Over Mineral Wool Board Insulation

I am planning a metal standing seam roof over 2 1/2″ of mineral wool insulation above an unvented roof assembly with batts between rafters. At one of the builder shows it was suggested that be done similar to a rainscreen wall assembly, with rigid board on top of the WPB and roofing fastened through the insulation and WPB to the structural sheathing below. Seemed good, as the insulation would protect the WPB from solar heat and also protect the wood substrate from wildfire in the rural California landscape, and any moisture that got in from condensation could boil out through the metal roofing snap lock seams; this system was featured in a Fine Homebuilding house in 2018. Now I’m ready to build and the technical department for the mineral wool won’t recommend the assembly unless a second layer of plywood is installed over the mineral wool, followed by a second layer of WPB. That sounds like a recipe for trouble in a few years if the second layer of wood is sandwiched between two non- breathing membranes. Was there a change in the industry, maybe some leak problems that would change their policy, or am I speaking to the wrong technical rep? It seems like I should go with rigid polyiso instead, possibly topped with some Dense Shield to keep a degree of fire resistance. Has anyone else run into this and found a solution?
GBA Detail Library
A collection of one thousand construction details organized by climate and house part
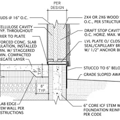
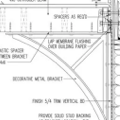
Replies
Brian,
Another alternative is to strap the roof over the mineral wool.
You can also install say 2x4 purlins on edge at 90deg to your rafters and use regular mineral wool batts. Since the purlins are perpendicular to the framing bellow it reduces thermal bridging almost as well as continuous insulation. Much simpler to install and significantly cheaper than rigid mineral wool. I've done this for over-roof and it works great.
Make sure your roof panels are rated for spanning, not all are.
Akos and Malcolm both: would strapping, whether flat or on edge, be installed over the WPB, and would there be any problem of the 90 degree strapping forming dams for minor condensation build-up?
Brian,
Whether the strapping is set into the exterior insulation, or above it, the underlayment should be directly under the roofing panels. Any incidental pooling of water will easily dissipate.
Hey Brian, here is an active thread posing similar questions from neighboring Napa County that may be of some help:
https://www.greenbuildingadvisor.com/question/feedback-on-wall-roof-assemblies
I'm curious to hear more about what you heard from the mineral wool manufacturer. Notably I've not found any documentation on Rockwool's site recommending sandwiching their material between sheathing layers. (i.e. a site-built nail base.) Everything from Rockwool seems to propose strapping/furring above the mineral wool (which seems to be more trouble than it's worth given local ordinances and practices.)
Adam
Attached is some commentary from Rockwool; my issue was complicated this year by the sudden unavailability of their product in thickness required to meet code, so we kept 1" comfortboard that we were able to obtain, for fire protection, but addressed the unvented attic by using spray foam on the underside of plywood. The only one of the options offered below that uses comfortboard for fire protection of sheathing is #4.
Rockwool's technical support comment:
In a typical roofing system, we would recommend one of the following approaches:
Approach number 1 – somewhat similar to the roof system on page 16 of the attached brochure:
Metal standing seam roofing,
Vapor impermeable roofing underlayment, installed as a water-resistive barrier,
Sheathing,
1.0" ROCKWOOL Comfortboard® 110 (R-4.0),
5/8" plywood sheathing,
1-3/4” closed-cell spray foam (R-10.5), installed as an air and vapor barrier between 2.0” x 8.0 wood rafters @ 24.0" o.c.,
5-1/2” ROCKWOOL Comfortbatt® (R-23.0), between 2.0” x 8.0 wood rafters @ 24.0" o.c.,
Plywood ceiling panels.
Approach number 2:
Metal standing seam roofing,
Roofing underlayment, installed as a water-resistive barrier,
Sheathing,
Air cavity between 2.0” x 3.0” wood furring at 24.0” o.c., fastened through the insulation to the rafters,
1.0" ROCKWOOL Comfortboard® 110 (R-4.0),
5/8" plywood sheathing,
1-3/4” closed-cell spray foam (R-10.5), installed as an air and vapor barrier between 2.0” x 8.0 wood rafters @ 24.0" o.c.
5-1/2” ROCKWOOL Comfortbatt® (R-23.0), between 2.0” x 8.0 wood rafters @ 24.0" o.c.
Plywood ceiling panels.
Approach number 3:
Metal standing seam roofing,
Roofing underlayment, installed as a water-resistive barrier,
Sheathing,
Air cavity between 2.0” x 3.0” wood furring, perpendicular to the rafters
5/8" plywood sheathing,
ROCKWOOL Comfortbatt® to the required thickness, between 2.0” x 8.0 wood rafters @ 24.0" o.c.,
Plywood ceiling panels.
Approach number 4:
Metal standing seam roofing, sealed as the water-control layer,
1.0" ROCKWOOL Comfortboard® 110 (R-4.0),
5/8" plywood sheathing,
1-3/4” closed-cell spray foam (R-10.5), installed as an air and vapor barrier between 2.0” x 8.0 wood rafters @ 24.0" o.c.
5-1/2” ROCKWOOL Comfortbatt® (R-23.0), between 2.0” x 8.0 wood rafters @ 24.0" o.c.
Plywood ceiling panels.
Approach number 5:
Metal standing seam roofing,
Roofing underlayment, sealed as a water-resistive barrier → In this case, it is loose laid over the insulation but it is not easy to detail, and this approach is not compatible with any standing seam metal roof,
1.0" ROCKWOOL Comfortboard® 110 (R-4.0),
5/8" plywood sheathing,
1-3/4” closed-cell spray foam (R-10.5), installed as an air and vapor barrier between 2.0” x 8.0 wood rafters @ 24.0" o.c.
5-1/2” ROCKWOOL Comfortbatt® (R-23.0), between 2.0” x 8.0 wood rafters @ 24.0" o.c.
Plywood ceiling panels.
From the other thread. Looking at the CA Building Code - R806.5 Unvented Attic and Unvented Enclosed Rafter Assemblies. found here https://up.codes/viewer/california/irc-2018/chapter/8/roof-ceiling-construction#R806
It needs to fit the requirements of the code section. It has a section on a vapor diffusion port and discusses the issues of vapor permeable insulation.
It's unfortunate in the way that's written that it seems to negate all of the codes allowing for impermeable insulation above the roof deck. It seems like 5.2.10 was meant to allow for mechanical abatement of attic vapors, but was written poorly.
Re-reading this again, section 806.5#5 says: “Insulation shall comply with Item 5.3 and _either_ Item 5.1 _or_ 5.2.”
So it would seem a vapor diffusion port is not required by code *if* conforming to section 5.1 which seems to allow for rigid impermeable insulation above the roof deck in an unvented assembly with permeable insulation below the roof deck so long as it conforms to 5.1.4:
“Alternatively, sufficient rigid board or sheet insulation shall be installed directly above the structural roof sheathing to maintain the monthly average temperature of the underside of the structural roof sheathing above 45°F (7°C). For calculation purposes, an interior air temperature of 68°F (20°C) is assumed and the exterior air temperature is assumed to be the monthly average outside air temperature of the three coldest months.”
Curiously, in Napa County, the average air temperature per the code books calculation is never below the minimum sheathing temperature threshold. (~47º vs. 45º) 🤷♂️
Edit: Also just realized section 806.5.2 (discussing vapor diffusion) speaks to climate zones 3-15. Napa & Sonoma are in climate zone 2.
Deleted
Thanks Adam for grappling with this. You are right, my project in Sonoma County is Zone 2.
I'm thinking I should try and use a vapor permeable membrane between standing seam roof and its nailbase; contractor recommends peel and stick, which generally seems to be impermeable in both Grace and Henry, and I have not yet found one that has a "breathable" texture that keeps some space behind the smooth bottom of metal roof pans.
Brian Rawlinson
Thanks for looking at that code section- it hurts my brain -
The metal roof needs a layer under it to make it have a class A fire rating. Versashield is a fiberglass roll underlayment that works. Or densdeck gypsum type rigid board. The GAF Versashield is listed as 3 perms min under water vapor transmission, so maybe
Forgive a rookie question: If the metal roof is unvented, what might a permeable membrane solve for between the metal and a nailbase? Wouldn't all drying need to be inward since the metal itself is impermeable?
I suppose it would come down to what might happen to any moisture between the metal and the membrane? To which, I imagine it would condense, find it's way down the WRB of the roof, and then leak off the drip edging (ideally into the gutter system)?
Noting: Locally, the most common roof assembly these days seems to be:
- Unvented
- Standing Seam Metal
- Polystick XFR
- Plywood Decking
- Closed-Cell Spray Foam
In that common assembly, the roofing would similarly be unable to release vapor. But also any water that potentially made it's way between the membrane and the interior insulation would have nowhere to go…
I guess we are assuming that metal roofing is vapor tight. The seams might be but it is not sealed at the top and bottom of the metal panel, the are lapped or bent to prevent water entry. So, gaps are located along the bent up seams and at the top & bottom. Is this enough area for the panel to let water vapor escape when the sun is heating the panels?
Metal panels themselves are vapor barriers but the install is never air tight. The profiles usually allow for a fair bit of air flow along the striations and the snap feature. Since the flashing is never air tight, this allows for enough air movement plus a bit of sun that any moisture that makes it underneath the panel quickly evaporates. This is the reason you always want an underlayment under the panels to catch this bit of moisture and allow some time for it to evaporate without getting into the structure.
As an overall design philosophy, I find what works is to allow for some drying path for any assembly. So if you have rigid above the roof, best is to use something permeable (fiber faced polyiso, unfaced EPS/GPS or mineral wool) with a permeable underlayment. This way any moisture that does make it into the roof deck has a drying path to the exterior.
Since you are looking at a milder climate, I think the simples is a unvented roof with a vapor diffusion port. As long as you have the required slope and diffusion area, this would be much simpler and cheaper as the whole thing has only batt insulation. You can use something like exterior gypsum sheathing for the diffusion port (ie Densglass) and a rated roof vent which would provide fire protection.
The next simplest would be unvented with a bit of exterior rigid. Polyiso or mineral wool would both be good for this. Polyiso is probably the simplest and works pretty well as it doesn't burn but chars. By the time the polyiso is gone you have much bigger issues. You can strap out the rigid, install purlins or a 2nd roof deck to attach the metal panels. They all work just as well.
There are also bearing plates you can get search (search "Metal Roofing Bearing Plates") that work with snap locks that use a clip. These can go directly over the rigid, no deck or strapping required, don't know if it would with rigid mineral wool though.
Akos,
Keep In mind they are required to have a class A fire rating on the roof assembly.
I'm not in a wild fire area, so not very familiar with fire ratings.
Quick google says you need a UL rated assembly, it seems that most metal panel manufacturers offer a UL rated assembly where the panel is installed either directly over polyiso, CDX/OSB over plyiso or or just CDX/OSB. Underlayment can be any Ul listed underlayment (ie GAF Deck Armor if you want permeable).
Unless I'm missing something both vapor diffusion roof and exterior rigid assemblies will work.
I guess the notion of mineral wool directly under the metal roofing is a no-go, even if it was touted a couple of years ago. The fire resistive aspect of mineral wool played a big part in my wanting to protect the plywood from "burning brands" etc in wildfires. Could the membrane be adhered over Densglass to get the fire resistance, but rely on screwing through the Denglass and insulation (either Rockwool or polyiso) into the 5/8" ply structural deck?
Brian , The Class A rated roof will protect the roof from easily burning.
Go to the metal roof mfg website and look at the ICC- ES Evaluation Report for the product you plan to use. That will give you the tested assembly. The mfg can also give you the UL rate assembly specification number- I have had a plan checker want the it.
for example - her is a random metal roof mfg that is listed on the GAF Versashield ICC Report.
https://www.custombiltmetals.com/resources/testing-approvals/
ICC Report https://www.icc-es.org/wp-content/uploads/report-directory/ESR-2048.pdf - see the installation requirements in the report.
Thanks Akos & Tim, your comments are extremely useful.
Brian, based on this discussion, my research, and my speculation (far from an experienced expert on this subject), I'm fairly convinced that the main limitations on using mineral wool in your proposed assembly are (1) unclear recommendations from the manufacturer (e.g. I'm not seeing Rockwool endorse any assembly that doesn't include (a) furring/venting or (b) spray-foam under the deck) and (2) few if any local roofing contractors wanting to work with the stuff in the way proposed.
I don't believe the Class A assembly requirement would be a limitation given your proposed design (metal over site-built nail base with fire resistant underlayment) as the Class A rating is “from the exterior” and, I believe, would be achieved with the combination of metal over Class A underlayment (e.g. Versashield or Polystick XFR) over plywood/OSB as that would meet all the criteria for a Class A (and be UL listed) no matter what's below it. (Note that there are Class A ratings [a reasonably fire-resistant from the exterior assembly] and Class 1 assembly ratings [very fire-resistant *complete* assembly, which is somewhat confusing.)
As such I'm feeling that polyiso is a better solution on our roofs here (assuming you're building in a defensible location that wouldn't otherwise be better served by a concrete bunker.) As Akos alluded, it stands to reason that if there was enough heat penetrating the Class A layers (metal, underlayment, plywood) such as to damage or smoke the polyiso, that the house would have much bigger issues than the poor fire resistance of the insulation itself at that point.
Noting too: The vast majority of homes being built here right now are Metal over singly-ply Class A underlayment over Plywood decking with Closed-Cell Foam under deck. From a fire resistance standpoint, these homes would seem to have an equal level of vulnerability to your proposed assembly if polyiso nail base was used. And be more unsafe given that any smoking of the polyiso would happen within the building envelope rather than outside the envelope. And yet this is best practice and CalFire's informally recommended assembly.
Here's more information on Class A vs. Class 1. https://cdn.ymaws.com/www.polyiso.org/resource/resmgr/Tech_Bulletins/tb111_Feb2017.pdf
Hi Very interested in what the end detail is?
I am in Sonoma, CA CZ 3 and looking to do a similar roof.
I wanted to do: Roof Pitch 10:12 Roof would be gable 17' wide at outside of wall and be a L shape with 2 valleys at back where a same width 17' wide gable intersects. The building foot print would be an L with 2' bump out at the back to create the intersection gable.
Option 1
Standing seam metal,
(Maybe a vent gap)
1.25"-2"rigid mineral wool - R5-R8
Permeable WRB
Sheathing - Vapor diffusion port at ridge
2x8 rafters at 24"OC With mineral wool batts - R30
Drywall or TG 1x6 wood - Vaulted ceiling / attic
Issues - It seems:
1 the vent gap may not be needed? (I like it to let the condensation and any moisture dry,plus other factors), If it is a good detail then I am also dealing with the fire rated issue? (what would be needed for compliance - a sheet of densrock instead of sheathing on top of rigid? or possibly nothing additional)
2 I may need a second layer of sheathing between metal roof and rigid insulation with a permeable WRB
3 I could add a vapor retarder at the interior between bottom of joists and TG / drywall
My biggest concern is the research that says (though the vapor diffusion port seems to address this) that a non vented detail like this will still get mold growth in the joist bays?
Going with CCspf under the sheathing would be better and the vapor diffusion port not needed?
Option 2
Standing seam metal,
(Maybe a vent gap)
4"rigid mineral wool -R16
Permeable WRB
Sheathing
perpendicular 2x6 rafters at 24"OC With mineral wool batts - R23
6x8 (or similar per engineering) beams from eave to ridge beam
Drywall or TG 1x6 wood - Vaulted ceiling between exposed beam
Issues:
1 this would not be able to have the vapor diffusion port that seems to make the mineral wool (fluffy stuff) detail work in a non vented detail.
2 I may need to notch the 6x8 beams by 1/2 to secure the 2x6. This would be a tedious task.
Option 3:
Standing seam metal,
(Maybe a vent gap)
1.25"-2"rigid mineral wool - R5-R8
Permeable WRB
Sheathing - with Ridge vent
2x10 rafters at 24"OC With mineral wool batts 7.25"- R30 and vent above
Drywall or TG 1x6 wood - Vaulted ceiling / attic
Issues:
1 Same concern / questions with gap under metal roofing
2 Same second layer of sheathing between metal roof and rigid insulation
3 would this detail be better / easier / cost effective to eliminate the continuous rigid insulation on top of the sheathing and install a rigid foam or mineral wool layer to the bottom of the joists? or even easier use 2x12 and R38 9.5" mineral wool batts?
Would any of this benefit from rigid foam instead of mineral wool?
Thanks for any input