Stone basement wall seal and finish

I have a field stone Foundation circa 1905. I believe it’s Lime based mortar, or at least a very soft mix more like a type O. (The tuck point on the cut stone above grade and hard brick walls is cement based. The SE corner seems to be slightly higher than the rest of the basement and has no visible moisture. I’d like to partially finish this portion of the basement. Some mortar is crumpbing and a cement based mortar was applied at some point (probablt in 1980’s) along with a footer at the base of the wall. Here’s was the detail I’d like to attempt:
1) Patch any suspect moisture locations with hydraulic cement.
2) Parge the wall with Type N Mortar to make it a nearly flush surface. Might add in some extra lime putty to the mortar mix to soften it just a little bit more and extend working time.
3) Wait 7 days
4) Bond roughed up 1″ XPS foam board with Large Tile/Stone modified thinset.
5) Use a latex based mortar caulk between joints.
6) Allow 48 hours to cure.
7) Rough up the interior face and use a Foundation coating mortar designed for foam board.
8) Apply an acrylic masonry paint.
9) Use dryloc or similar masonry coating on any floor cracks to seal out Radon. (levels are 0.5 – 3 depending on wind and seasonal stack effect) Paint with acrylic latex floor/porch paint.
I’d like to get some insulation value, but want to avoid moisture sensitive framing.
I’ll probably do one wall first as a test area as proof of concept. There’s only about 175 sqft of exterior wall area to cover. So about 6 sheets of board, so not much risk if it doesn’t stick.
Alternate was to use Go-Board. A little more expensive but it had a fiberglass surface designed to bond with thinset. R value is only about R3. But R3 is 1/3 less heat transfer than R1 and would be a partial vapor barrier. But R6 from the 1″ board would be better and the board is cheaper.
To get more resilience, I thought about using 1/2″ Cement Board on the lower 3′ first. But not sure how i’d be able to anchor it to the wall. Not sure how well I can drill a hole in stone.
Overall, it’s sort of a reverse stone masonry wall assembly. The advantage is avoiding using separate wood framing and drywall and risking moisture issues. In this situation is there still is moisture, there’s no damage to the assembly so long as it’s below the frost line.
Downside is I’m no longer allowing the stone to dry towards the interior.
Secondary goal is further reducing my heating load so when I replace my steam boiler in 1-5 years, I can downsize it a little. It’s steam, but a vapor system, so it will still balance OK with a undersized boiler on the load so long as I over vent the main and control down the vent rate on the radiators so it’s distributes evenly.
GBA Detail Library
A collection of one thousand construction details organized by climate and house part
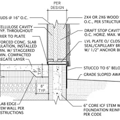
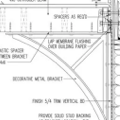
Replies
Moto Guy,
I don't have enough experience with lime mortars to evaluate your approach. But my first reaction is that you are reinventing the wheel. There is a standard approach to dealing with this kind of wall, and the standard approach differs from your approach.
The standard approach is to install dimple mat against the interior of the foundation wall -- in some cases, the dimple mat leads to an interior French drain that connects to a sump -- and then to install closed-cell spray foam against the interior of the dimple mat. For more information on this approach, see "Rubble Foundations."
Correction, it's cut stone. It's locally sources, lower grade limestone I think. Mortar might be a softer cement base same as outside the home. Whatever they used is amazing. I have no evidence the exterior has been tuck pointed(too perfect looking, no inconsistencies in color or damage to brick) and it's in near perfect condition 110+ years later.
I'll look at the dimple mat. Challenge there I there's already a 6"x6" "curb" poured at the base of the wall. In the dryer space I'm trying to finish it won't be an issue. Dimple mat will work great in 2 spaces where I already have a sump pit, and another 2 where I have a sewer drain nearby I can utilize (water volume is probably <5 gallons per major rain event).
Thanks for the feedback.