Strapping screws: to angle or not to angle?

For 4″ of XPS, with a 3/8″ airspace and 3/4″ plywood strapping, is it sufficient to screw in straight, or do I need to screw in at an angle? I’ve read where both are “recommended”. From my small-scale mockups, screwing straight through seems adequate, but I’ve never done this before so I don’t want to screw it up (sorry :P). The screw pattern I’m using comes from the manufacture’s data sheet, and it doesn’t specify a screw angle.
Exterior sheathing will be board and batten, white pine, painted. I’m sort of regretting the wood siding idea, but I wanted board and batten and wasn’t happy with cement siding options.
(I’m putting a screw in every 12″, furring strips are spaced 24″ O/C).
GBA Detail Library
A collection of one thousand construction details organized by climate and house part
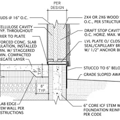
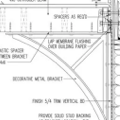
Replies
Hi John,
With only 4" of XPS and only light loading due to the siding, it probably doesn't make a lot of difference. That being said, it is a simple matter to angle the screw very slightly which does help prevent the possibility of a slight sag when the siding is installed. But don't angle the screw too much or it will tend to move the strapping (and the foam) out of position as it is tightened.
John,
I don't think it matters whether you angle the screws or not. Install them at 90 degrees if you want.
I'm somewhat confused by your stackup (not that it matters). You said that your "exterior sheathing" will be board and batten -- but I think you meant siding. Also, if you are using 3/4 inch plywood for your furring strips, how do you end up with a 3/8 inch air space? Finally, if you are installing furring strips 24 inches on center, how are you attaching the board and batten siding to the furring strips? Are the furring strips horizontal?
Sorry wrote that question a bit too quickly.
My stackup outside of my OSB sheathing is as follows:
Ice+Water shield + 4" foam + 3/8 aluminum spacer + 3/4" horizontal plywood + vertical board and batten siding
I'm not a builder, so if I'm not paying attention to the terms I can sometimes use the wrong words.
John,
No need to apologize. Your explanation clears up the uncertainties. Good luck.
The aluminum spacer needs to have sufficient surface area in contact with the foam to not dent in a bit over time, especially in windy ares. Even at 12" o.c. they should be at least 3"inches in diameter, and probably even bigger.
The more common way to do this is to skip the spacers and make the girts out of 1x4 milled strapping, with pancake head timber screws. The strapping distributes the pressure out over 10s of square inches of foam.
If you feel the need for the space behind the girts to provide drainage space, consider using 4" x 4" squares of 3/8" plywood for spacers (for 16 square inches of pressure distribution on the foam.)
I'll post a picture tonight - the aluminum spacer is a long strip of corrugated aluminum - it runs the length of the strapping. So while there will be point loads at each screw, the aluminum should provide enough surface area not to creep (based on my limited testing) since the force is being distributed by the strapping between screws. Plywood seems to be pretty stiff when short (12").
If I had to do this over again I'd do vertical strapping and a horizontal siding, but I'm already invested in materials quite a bit.
After looking at this carefully in the context of a previous discussion, I concluding that very slight variation in the angles of the screws, what you might get when trying to make then straight but not having any jig to get them perfect, substantially improves the vertical rigidity of the assembly, and explains why the measured performance is usually better than the calculated expected performance. So I would recommend aiming for making having the angle be close to 90 degrees, but err on the side of having point of the screw slightly higher than the head rather than the reverse. But certainly don't worry about it--if it were important to have the screws at exactly 90 degrees, it would be very difficult to do that, and the natural scatter you get will be plenty.
I think I understand the aluminum thing--the channels through the corrugation run vertical, whereas the strips run horizontal? Another material that is sometimes used for that, and is probably cheaper, is corrugated plastic.
Yes - corrugated plastic would have been cheaper, and probably what I should have used. I was concerned about degradation, but since UV light won't hit it, the stuff will last practically forever. Lesson learned!
I installed a small section yesterday - just enough to get a feel for the process. This is a top-down view of the furring strip:
I feel I have a long road ahead of me (and I though the ice+water shield was a chore!). The vertical gap to the left is an unsecured piece of foam at the corner - but I am taping all seams:
Furring strip with spacer, top-down view
Foam install start
John P.
I am getting ready to do this on my new house that I am building. Thank you for sharing your pictures and questions.
John - What are you drilling into? At a 12" spacing horizontally, it's probably not your studs. Just curious.
Bill - this is a bit unconventional - and I certainly don't recommend it - but I'm screwing into 2x6 horizontal girts (or purlins, it seems the terminology is mixed). They are actual dimension - 2" x 6" - not 1.5" x 5.5", so the screw is going into 1.5" of wood. I'm a bit concerned that the screw is .5" from the inside face of the wood - time will tell if that poses a problem or not (heat conductivity, etc...).
Also - I agree with Charlie in not using a guide - the screws going in at slightly different angles is probably a good thing.