Through-wall frost-free condensate drain

I am planning a heated utility building in a cold climate with no water, and consequently no drains. Nevertheless the building needs to deal with condensate from the HRU and the condensing tankless water heater used for in-slab heating. A proposed DIY solution for a through-wall frost free condensate drain is diagrammed here:
CondensateDrain-ThroughWall-FrostFree-V00.png
It seems to me that two features are highly desirable. The first is an auto siphon (the assembly inside the 4″ pipe) that will drain the water in pulses of 1 quart or so rather than in small trickles. The Worchester Bosch CondenseSure product is commercially available the UK for this application:
https://www.worcester-bosch.co.uk/professional/products/accessories/condensesure
I did not investigate how practical it would be to purchase and install this product into a project in North America.
The second feature is a robust version of the technique frost-free hose bibs use to drain water from the pipe from a point inside the building envelope to the point of discharge into the open air. I propose running two parallel, vertically offset pipes at a 45 degree downslope through the insulated wall, terminating several inches from the wall and two feet or so above ground level. I expect this will minimize residual water in the lower drain tube when water is not flowing, and the upper vent tube should maintain the wall’s air seal. I propose using open channels to further direct the water away from the wall; those will likely become large icebergs over the course of the winter.
I still have the option to run a drain pipe down through the foundation, but I didn’t see any good termination choices for that. On my site I could run the drain to daylight, but the termination is going to get covered in snow for sure, so I expect it to plug with ice. I could run the drain to my foundation drain, which would hold quite a bit of volume before backing up when it also plugs with ice where it drains to daylight, but sealing the system to radon then becomes an issue.
The simple option is to drain to a large water tote and manually dump that outside when it gets full.
GBA Detail Library
A collection of one thousand construction details organized by climate and house part
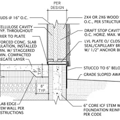
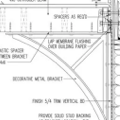
Replies
Greg,
What do you mean by a "cold climate"? Is that Virginia or Minnesota?
Deleted
I think your system is clever, but will only delay the inevitable freeze up. I would either drain to daylight with a heat cable in the drain line, drain underground to a dry well below the frost line, or drain to your perimeter drain with a trap to prevent radon from entering your structure. I would not try to build a fancy anti-freeze vented tank like you’re proposing (and I’m an engineer by profession who spends his days designing stuff). I think the custom creation is likely to have many unforeseen problems and possible issues with code enforcement and insurance companies if anything does go wrong.
Bill
This seems like an insignificant amount of water for a foundation drain -- whatever freezing issues that has will probably be essentially unaffected by this tiny addition.
Sealing against radon is as easy as putting in a P-trap or a SureSeal.
The building is in Missoula County, MT, IECC Zone 6 Moisture Regime B.
My understanding is that auto siphon is a very old technology and is commonly used in septic tanks. It only a bit more complicated than a P trap. I see very little risk in trying it, either the DIY version or the commercial product from the UK, since it is only modest amounts of water at atmospheric pressure. And with PVC construction and no moving parts it will likely last just about forever. And the worst case of having to rip it out and add heating tape to the exterior drain line is a small job. It is the simplest to install and easiest to fix.
The only significant downside I see from the through-wall drain is the potential maintenance issue of the iceberg formation. I am not sure how that would compare to the existing maintenance issue of snow removal on the property's 800 ft driveway.
I see the point that a p trap will solve the radon concern for a drain through the slab.
In my case I will be burning propane. Based on these three links (I didn't check their math) one might expect 0.73 gallons of condensate per gallon of propane with a maximum theoretical of 1 gallon per gallon. My 2000 sq. ft. house burns about 700 gallons of propane over the winter months, which would generate typically 500 and maximum theoretical 700 gallons. I certainly hope my utility building burns much less than that (fewer windows, better insulation, less than half the size, no hot water or cooking) but 500 gallons per winter looks to me like a reasonable design value.
https://yorkcentraltechtalk.wordpress.com/2012/10/15/furnace-condensate-new-d-o-e-rules-part-2/
http://mathscinotes.com/2018/01/dealing-with-furnace-condensate-at-low-temperatures/
https://dea.human.cornell.edu/sites/default/files/pdf/compareheatfuels.pdf
It might be helpful to realize that the through wall option generates a surface water management challenge whereas the through slab option generates a subsurface water management challenge
Greg,
In Missoula, Montana, I imagine that an outdoor temperature of 10 degrees F -- or even much colder -- isn't particularly unusual in winter. If your drain is penetrating a wall, the outside of the drainpipe is at 10 degrees F in this situation. So when condensate starts flowing through the pipe, a film of ice builds up. As the condensate continues to flow, this ice gets thicker and thicker until the pipe is blocked by ice.
Martin,
Being west of the continental divide this area does not typically see extended periods of temperatures below 10 degrees.
My guess is you are correct when flow begins, but by cooling and especially freezing the flowing water the pipe will warm up. So long as flow continues the pipe will tend toward a steady state temperature profile across the pipe wall determined by the rate of heat transfer to the outside air and the rate of heat transfer from the flowing fluid. Finite element modeling could calculate the expected temperatures over time. Or one could experiment: cap a short length of drain pipe, put it vertical in the freezer overnight, then fill it with water and see how long it takes for ice to block the pipe. I can't imagine this taking anything less than several minutes for say 1/2" galvanized, and longer for PVC. So if the pipe is initially open at the beginning of condensate flow, it should remain open so long as there is more than a slow trickle. So the draining system must avoid that by accumulating a significant volume of water and then discharging it at more than a fast trickle; I imagine 1/4 gallon per minute would be more than enough. And after completing the water discharge the pipe needs to completely drain of water, other than a few small droplets here and there. It will help if the discharge extends over many minutes so that the pipe warms up to something close to indoor air temperature, so that it stays above freezing for a time after flow stops allowing it to drain more completely. Insulation on the exposed drain pipe should further reduce the chance of freeze-up.
I have some real-world evidence of this. We were about a month or two into freezing temperatures when I discovered an iceberg that had formed below a frost-free hose bib. Obviously the bib had been dripping very slowly, but the water remained liquid until after it dripped out of the bib. It didn't freeze until it hit the ground, or the top of the iceberg once that formed. I think we had temperatures as low as the teens during this period.
The other evidence is that frost-free hose bibs apparently work.
In Vermont, drains exposed to exterior air freeze solid. (Ask me how I know...)
Martin,
Do frost-free hose bibs work?
Greg,
Frost-free hose bibs work, because the valve is located in the conditioned space, and they almost never have any water in them in freezing weather. (Few people water their lawn or their garden during very cold weather). A few ounces of water drains out of the hose bib in October, and then the hose bib is rarely used until April.
Problems arise, however, with a cold drain that sees a steady trickle of liquid, or liquid that flows daily.
Martin,
I agree that the drain will freeze if there is a slow trickle of water. I expect a drain will not freeze provided 1) when there is flow it is substantial, and 2) when there is no flow all cold segments of the pipe drain completely. What I propose, with the auto siphon as in my diagram, or with a condensate pump as I discuss below, will accomplish 1) and the through-wall drain/vent pipe combinations in my diagram will accomplish 2). Or at least I expect that.
I don't think daily liquid flow is by itself a factor. I suspect that there are numerous livestock operators in Vermont and elsewhere that use frost-free hose bibs routinely all winter.
I suspect that we may have to agree to disagree.
Upon further Internet searching I am no longer completely ignorant of condensate pumps, one of which could replace the auto siphon assembly (the stuff in the 4" pipe) in my diagram, with the advantage that the discharge through the wall could be higher than the condensate drain on the heater. Further, there are condensate pumps with 1 gallon reservoirs, which I think would be preferred in this application over those with the more common 1/2 gallon reservoirs.
At this point in my mind the leading option is an off-the-shelf 1 gallon reservoir condensate pump and the through-wall drain pipe / vent pipe arrangement in my diagram, although the piping between the pump output and the drain/vent assembly probably needs some optimization. There may be formation of an iceberg under the discharge end of the drain pipe that causes issues at times. An upgrade would be to use 55 gallon drum for the condensate reservoir and automated pump to discharge 40 gallons at a time. At those volumes I expect a skating rink to form outside rather than an iceberg.
Since this building is still a plan on paper. I think you should install a 50 gallon dry well that’s top is below your local frost depth. Feed the well with a 3 inch drain pipe that is below frost depth that comes up as a floor drain near your furnace.
By your own calculations should you burn a full tank of fuel during a cold spell that stayed below freezing, you would have a 4000 pound ice ball pressing up against your wall.
X 100 for the drywell. you can even do it below the floor of the building.
fool proof
0 moving parts
0 maintenance
UPDATE:
After consulting my county health department is has become clear that based on a strict interpretation of the current health codes it is unlawful of me to pipe condensate anywhere except my septic system. After getting a permit of course. It is legal for me to collect it in a bucket and empty the bucket on the ground outside, but not if I put a pipe through a wall. The health department agrees that the code needs to be fixed. I am not sure how to get that to happen.
Usually code changes are requested in writing to whatever body is responsible for the codes. For example, in the US the NFPA publishes the national electrical code. You can write letters to them to start the process for changing/amending/modifying the code. After a fairly lengthy peer-review like process, your request *may* make it into the next version of the code.
Your health department would probably be more likely to get the code changed than you personally. You could ask them to put a request in.
Bill
Bill,
It appears that this code is written by the county health department. It isn't clear to me what their change process is; I suspect that on occasion they submit changes to the health board for approval. Submitting a request for change with documentation and references would make it easy for them. That would probably be the easiest and fastest, but no telling how long before they would be inclined to follow through. I'll use a bucket until I get the certificate of occupancy. After that, who knows.
While I agree it is silly to require condensate to drain into the septic system, what is your objection?
My boiler has been doing so[through a charcoal and limestone device] for 9 years with no ill effect
Keith,
I would do that too if having water and drains in the building were important to me, or if the septic tank was close to the building. But I am constructing a dry utility building to use as a woodworking shop so I don't need water except for the odd bucketful, and there is a long distance of more rocks than dirt between the build site and the septic tank.
Just a thought, but would the health department people be ok with you draining the condensate to a drywall if you treated the condensate with a biocide? Commerical cooling towers have to flush periodically to avoid mineral buildup, and the water is treated with a biocide (primarily to avoid issues with legionares disease). Often times the cooling tower flush cycle drains down a storm drain.
Note that this may be a local code issue, I don’t know the specifics in your area. You might try asking though. The biocide used in cooling towers is pretty cheap so maybe that is another option for you.
Bill
The fact is code enforcement cannot trust that you or the next owner will not pee in a floor drain connected to a dry well. If they did allow a drain how can they be sure the next owner will not connect a toilet to that drain? Welcome to the nanny state.
Sounds like an 80% furnace would be the low cost code compliant solution.
Walta
Bill - Nope, and for the reasons Walta mentioned. The land sanitarian said so.
Walta -
Health code enforcement is the only mechanism to keep an irresponsible neighbor from literally crapping up my well, my land, and its surface water. Building code enforcement is the only mechanism to keep an irresponsible builder from constructing a dangerous building. This winter there was 1 roof collapse in Missoula and 2 on Montana State campus. The system was constructed because people used to die regularly from sanitation and building practices that weren't up to snuff.
The system is far from perfect but having no system would be far worse. For example, wildfire risk is in my area is considerable. As I understand the research, one of the 3 most likely reasons your house would burn down in one is that a neighbor's house close to yours catches fire. If there is a major fire, even if it is a mile away, most of the buildings in the neighborhood next to my property are going to burn down because several of them are basically ready-to-light bonfires. They will promptly ignite from the wildfire ember shower and will subsequently ignite the neighboring houses because of the narrow lots. The responsible property owners can't do a thing to protect their homes from this risk created by their irresponsible neighbors.
IMHO, the government most resembles a nanny state on issues other than related to building, and as this isn't a politics forum I'll leave it at that. Certainly there is no shortage of specific building-related regulations that are unnecessary or even counterproductive. And code enforcement is a fertile environment for corruption. But a general characterization of building and health code enforcement as "nanny state" reflects short-sightedness and/or selfishness, IMHO.