Tiny Home subfloor, proper layers for long lasting system

I have seen multiple techniques out there being used regarding how the “builders” are stacking the layers for weatherproofing and insulating the sub-floors on the trailer of a tiny home. I believe the variety of solutions being used are sometimes letting the maximum trailer height dictate alternative building techniques, which are possibly sacrificing structural stability over the long term. I’ve read that the builders are applying metal pans to underside, some to top side, some are adding a 6-mil vapor barrier atop of this, then adding plywood or OSB, or doing insulating within the steel trailers sub-floor, etc…
I’m looking for a straight forward path to doing this correctly every time. For me, simplest solution is a SIP system atop the trailer, and not bothering with working on the underside of the trailer, its just more trouble than its worth.
I think the “experts” agree with utilizing a SIP system (bottom layer of AdvanTech 23/32 floor panel, 3.5″ rigid foam, then 23/32 plywood, for example). My suggestion is regarding the additional layers done prior to the SIP placement (or if they are even necessary).
Would it be appropriate or necessary to cover the top of the steel trailer platform with a thin grade aluminum sheeting prior to attaching the SIP? My proposal was to use 36″ wide .011″ gauge Al sheets which the overlaps are sealed using a ASTM C1311 rated sealant. You would essentially have a barrier system in place to prevent moisture intrusion to the subfloor from underneath the trailer under normal road driving conditions in snow and rain. With the AdvanTech panel atop of this, it would be nearly bullet-proof.
If it was me, I would extend the flashing a few inches beyond the trailer foot print so as to wrap it up the SIP sides, and then a final flashing layer would be applied atop the periphery of the SIP system so as to run down the SIP’s sides, overlapping the underside. This would prevent any moisture from running down into the trailer’s aluminum floor pan and getting trapped.
Is this even necessary? Or is the simple solution going with the AdvanTech flooring panels for the bottom of the SIP and leave it at that to handle the road conditions? I am looking at this from the aspect of longevity. My building practice would be one that says I can guarantee a home 50 years from rot if it was up to me!
Would the aluminum pan become the vapor/air barrier in this case, and the SIP my insulated floor system to reach the desired R value? This to me seems like an air tight, moisture free solution.
GBA Detail Library
A collection of one thousand construction details organized by climate and house part
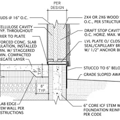
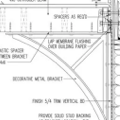
Replies
Cody,
Just to be clear: are you actually talking about using SIPs (a structural insulated panel) or just a sandwich of sheathing with foam in between? I ask because most of the trailers I've seen have wheel wells that need building around, and consist of a steel frame that needs some additional structural infill to support the floor.
I agree it doesn't make much sense to include the trailer structure in your floor system. There are too many thermal bridges and it is almost impossible to seal the underside. Whether you need a metal pan underneath depends on how you see using your home. Most tiny homes on trailers are very awkward to move - and do so only infrequently to get to their site. Protection agains road damage might not be necessary.
Another reason to try and keep the trailer structure as separate as you can from the home above is that if, as you say, you would like to build something that lasts 50 years, you will be looking at replacing the trailer at some point. Anticipating how to do this now might save you a lot of grief later.
These would be considered DIY SIPs, as I'm not forking the cash for certified SIPs (not yet anyways, and I'm only doing a sub-floor this way, so the structural load will be passed down the walls into the plywood and 2x4s, down into the steel platform in this instance, and the foam is only serving as the R value to prevent cold feet as much possible). Though its worth mentioning I could easily roll adhesive on each side of the sheathing to make my SIP and vacuum bag a panel to achieve similar results as the big boys at a fraction of the cost. Having worked in the metal bonding aerospace business, its not at all complicated to do.
The wheel wells in my instance are not a factor, so you can ignore worries with that. Just assume we are working with flat decks or trailers specifically built with a deck to support building a sub-floor system and tiny home atop of the sub-floor. Let us also assume the home will see some travel time on the road and as such variable weather conditions, be it salty iced roads to desert rain storms, whatever the condition is, moisture would be a concern. Hence the question of what the best system would be without including redundancies in design or possibilities of moisture entrapment.
Maybe the trailer see's road time, maybe it is in a Zone 5 or higher environment where you'll see lots of rain and humidity, salt exposure near the ocean, bugs, all gametes of what can deteriorate building materials... so if the trailer subsides to the conditions before the home, I've done my job as I see it :) My question remains though, is the aluminum pan serving a purpose in my proposed plan, or am I creating additional issues?
If you can afford it I think pan is a great idea and as long as the perimeter is well protected will not introduce any moisture issues.
Thanks Malcolm. I know thermal bridging and ending up with multiple vapor barriers is always an issue some seem to somehow do, even in the best of intentions. This always seems like a topic where multiple answers or procedures exist or are in use. I see the pan as being no different than the floor pan of your car in that is it sealed from water intrusion in much the same way during assembly. This is the foundation of the tiny home, so for me, building a solid foundation which will last as long as the steel on the trailer is important to minimize how many of these things end up in a landfill when they start to fall apart from rot. Not sure where you stand on tiny homes from a green aspect, But I am excited to begin on these as I see potential for a lot of people by downsizing to smaller homes (not just on a trailer, but also with small footprint homes on permanent foundations).
I forgot, you mentioned cost. It is about $1/ft to do an aluminum pan, so a 40ft trailer would run $400 in materials. Small cost to pay for longevity if it works as designed on paper and protects the underside of the sub-floor.
I helped a nephew build one a few years ago. It didn't go well. Unlike you he really only approached the building science aspects from a hard-green point of view, so with no air-sealing, and only lamb's wool batts in the walls, it was very uncomfortable.
I don't see tiny houses on wheels ever being anything but a very small niche choice for people. Whether we really need a lot of tiny houses on foundations, or just smaller houses all round is open to debate. That isn't to say you shouldn't build or live in one. If you find it works for you that's great. Good luck with the project.