To use Tyvek or not?

I am in the process of designing my second Post&Beam house using SIP panels for the exterior walls and Roof. There seem to be some controversy regarding using TYVEK or similar material on the exterior side of the walls, what is your advice?
The house will be build in quite a cold climate, Mid Hudson, New York to be excact.
Thank You,
Hanne Michell
GBA Detail Library
A collection of one thousand construction details organized by climate and house part
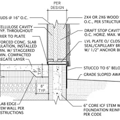
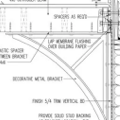
Replies
What controversy are you referring to?
Code and good building practice requires a secondary weather resistant barrier (WRB) behind the cladding. Among the plastic WRBs, I prefer Typar since it has more than enough vapor permeance but not the excessive permeance of Tyvek. Too vapor open and it allows radiant solar inward moisture drive.
The two other issues with polymeric WRBs are 1) that they require slitting and taping over upper window flanges (and tape is not a reliable weatherseal), and 2) they can trap liquid moisture behind them unlike old-fashioned #15 felt, which is preferred by some prominent building scientists.
Installing a gap between the cladding and WRB will improve the performance of the WRB. A "rain screen" installation seems to be in fashion, but I prefer to use 'cedar breather' type gap material because it's much cheaper and doesn't complicate flashing details.
Tyvek has its advantages, personally I prefer it to typar because it's more durable on site in my experience.
Felt is preferred by some but I've seen a lot of felt that has crumbled into dust so I prefer other things. Who knows what Tyvek, Typar, or the random "felt" you get at a random supplier tomorrow will do over the next 100 years though!
That's not necessarily true. If the WRB is used as an air barrier (which was it's original purpose), then it cannot be allowed to deflect under variable wind pressure. And if it is not tight to the sheathing, it can create air pockets which are condensation traps, and once water vapor condenses into liquid it cannot pass through the WRB and will saturate the sheathing. Organic felt does not trap condensation and it has the perfect vapor permeance - 5 perm - for a WRB and is, in fact, the code standard against which all other WRBs must be compared.
I've heard other people tell about felt that has "crumbled into dust", but in 30 years of building and renovating I've never seen this. Both felt and rosin paper are amazingly durable, and Paul Fisette of the UMass Building Technology Department says he still prefers felt over all the plastic WRBs. I agree.
Doug Cedar Breather is not at all inexpensive. Last I priced it, it was more expensive per sq ft than OSB. I like being able to tape all the seams easily in Tyvek wrinkle wrap but usually cover that with a layer of 15 LB felt.
I just finished removing some vinyl siding installed in 1987. Tyvek was used underneath, very poorly installed. On all walls, and all exposure conditions, there were large areas of the Tyvek which were deteriorated to the point of tissue paper. Several areas where the Tyvek had shrunk and torn, mainly at window corners.
Due to the relatively large overhangs, and very loose detailing of vinyl siding, (IMHO) there were few areas that could not dry out quickly, so the amount of sheathing deterioration was almost zero. Consequently, the Tyvek also was not subject to long term wetting. There were also walls which received no sun exposure. Location is in the PNW, near a shorelline.
It appeared to us that the Tyvek had deteriorated due to off gassing of the vinyl. Any other Ideas?
We installed 15lb felt, including unfastening the windows to get the paper under the flanges. The only place I have used Tyvek in the past few years is the crinkly version under some rigid foam with lightweight stucco. Even then I'm not too comfortable with it. I have not seen felt deteriorated to the point of failure, over my 20 years of experience.
Tyvek is not vinyl, it's spun-bonded polyethylene. I can't remember the dates, but when it was first introduced as an "air barrier" material to save on heating costs (?!?) it was not UV stabilized and had to be quickly reformulated so it wouldn't lose its market share.
The early Tyvek had to be covered in three days, otherwise the UV breakdown would continue even after covering.
One of the chemists at Dupont who came up with the Tyvek housewrap, left to manufacture what he believed was a better option, and that came on the market as Typar - the first competitor to Dupont's monopoly on polymeric housewraps. It was marketed as a UV-stabilized more tear-resistant alternative to Tyvek, and I've prefered it ever since. I also prefer it because it's more than adequately breatheable without being excessively so, like Tyvek. Too vapor open and it allows solar driven moisture an easy path inward.
Ironically, the ideal vapor perneance for a WRB is 5 perms, exactly what #15 felt provides, and which is why the IRC prescribes #15 felt and requires that any substitute at least equal its performance.
Robert,
I understand your preference of Typar over Tyvek. I have also noticed from previous posts that you have used Typar on many projects. Do you also prefer Typar over #15 felt, or do you feel that there are certain circumstances that fit one material better than the other?
Ben,
Actually the only reason I've used plastic housewrap on recent projects is because they have no exterior sheathing, just my Riversong Truss exoskeleton, Typar, and horizontal 3/4" novelty drop siding (spruce, prefinished on six sides). So the housewrap is the only secondary rain/air barrier between cladding and cellulose insulation. I also tape the horizontal lap joints and any vertical overlaps as well.
But, if I used sheathing (preferably sawn lumber boards for breatheability and durabiity), then I always prefer #15 felt, and preferably ASTM D226 #15 felt (11.5 – 12.5 lbs per square). Most building supply houses seem to stock ASTM D4869 #15 felt (8.0 – 9.7 lbs per square), while unrated #15 felt might be only 7.6 – 8.8 lbs per square.
Could the Riversong truss system (with no sheathing) be used in the pacific northwest with our seismic concerns?
Michael, thanks for your response on this thread about Cedar Breather.
I also loved your suggestions on the other thread: https://www.greenbuildingadvisor.com/community/forum/green-building-techniques/19287/flashing-windows-vent-screen
The sill-sealer-strip concept seems very worthwhile, inexpensive, and simple.
We pay $135 for a 200 sf roll of cedar breather, or 68 cents/sf, which is not exactly cheap, but compared to the labor for a fully strapped 1x rainscreen I'm sure it's much cheaper installed. Also it is very easy to explain and execute in the field. If someone like you is the lead carpenter, a more complicated system might make just as much sense, but for subcontracted framing and siding crews, we've found cedar breather has its charms. You really change almost nothing about your building techniques (from flashing to nailing to anything else) other than adding the cost of the material and maybe a tiny bit for labor.
Not saying it's perfect but it seems more sensible than 1x rainscreen at any rate.
Also, we have found other similar drainage-mesh materials for lower costs at times.
NW Builder,
The Riversong Truss system is a framing system independent of type or shear bracing. I've used it both with and without exterior sheathing. Though, for a highly breatheable wall system, my first preference for sheathing would be diagonal sawn lumber and then (if that doesn't meet local seismic codes) CDX plywood (never OSB, let alone ZIPwall).
But to have the advantage of the deep single insulation cavity AND exterior shear bracing, the outer framing skeleton must be supported by - and tied to - the foundation and it should also be supporting the roof assembly. This can be done with the truss wall, but a double wall may be more appropriate.
When I design double wall homes (2 independent 2x4 24" oc walls where code permits), both walls are supported on the foundation, the inner wall supports the floor assemblies and the outer wall supports the roof. Keeping the floors on the inner walls eliminates the air-sealing and thermal bridging issues at the band joists. And, if either the subflooring extends to the outer wall plates or a secondary CDX top plate connects the inner and outer walls, then the floor assemblies also serve as lateral shear elements for the outer wind & seismic resisting walls.
There are many variations to my approach to building deep, double-framed walls that eliminate thermal bridging while distributing the gravity loads and still providing shear bracing. As long as they meet local codes, are dense-packed with cellulose, and are breatheable in both directions (with the exterior being, ideally, five times as permeable as the interior), then they meet my standard.
Doug,
As much as I hate to advocate yet another plastic material, I agree with you that the textured housewrap membranes are much less fussy and more sensible (and probably less expensive) than most rainscreen systems.
But neither are necessary if the entire wall assembly can breathe. We make them necessary by using impermeable and non-hygroscopic materials like OSB or exterior rigid foam or interior spray foam.
Robert,
You're probably right--and I guess we'll find out sooner or later--if permeable wall construction is adequate defense against the moisture that gets through WRBs.
I will say that for certain claddings, a drainage gap seems like an absolute necessity to me. Stucco and lick-n-stick stone seem to experience problems in cold climates, per Martin's recent post https://www.greenbuildingadvisor.com/blogs/dept/musings/install-stucco-right-include-air-gap
and BSC's "Mind The Gap" article: http://www.buildingscience.com/documents/insights/bsi-038-mind-the-gap-eh/
Based on my experience with the large amount of water that penetrates them, vertical and diagonal sidings are also leaky enough that I'd prefer the benefit of a drainage gap.
It seems clear that a gap between cladding and WRB will make the WRB perform better, by facilitating drainage, reducing the chance that hydrostatic pressure will push water through penetrations, and facilitating drying. To me these mechanisms work independently of the behavior of the wall behind the WRB and are made important more by the selected cladding and weather than by the wall construction.
A narrow point to be sure, but I wouldn't want to use stucco without a gap, over any type of wall.
Doug,
I completely agree that a gap is needed with any reservoir cladding (and has been traditional with brick facing for generations). But I don't consider those claddings part of a breatheable wall system. For instance, cementitious plasters on straw bale walls will often result in rot while earthen plasters almost never do. Masonry and cement wicks water well but does not allow sufficient vapor permeance for a wall to truly breathe, and they absorb rather than deflect water.
And I fully agree that vertical and diagonal siding creates water intrusion problems, and for that reason alone should be avoided. They are used for idiosyncratic aesthetic reasons, not because they work as required. They offer yet another example of the need for additional - and more complex - water management systems when simple, traditional approaches are discarded for the sake of architectural vanity.
Plastic WRBs do require some means for drainage or evaporation, but the issue is not hydrostatic pressure - that's cause by "head", and is a problem for foundations. It's wind pressure and vapor pressure that both the weather barriers - cladding and underlayment - must resist, as well as kinetic forces, liquid diffusion pressures (temperature-driven), surface tension and capillarity.
The best weather barriers are those that cooperate with gravity, meaning horizontal lapped elements that don't absorb much water but allow vapor diffusion outward. Traditional lapped claddings, such as clapboards, also create staggered cavities behind them which allow evaporative drying and a capillary break.
Asphaltic felt underlayments don't rely solely on gravity for water redistribution. They can also absorb and redistribute moisture to other breatheable hygroscopic elements adjacent to it. Inevitable water intrusion is less problematic if it can be quickly redistributed over a wider area and a greater volume, which reduces its local concentration and diminishes the probability of failure.
There are reasons that these simple technologies have been in use for thousands of years.