Wall and attic rigid foam

I am asking an overly beaten question but would like to think my scenario is different. I am considering installing rigid foam insulation in my wall cavities, between my rafters, making roof vent baffles and above my rafters in my attic floor for added R value. I live near buffalo New York, zone 6. My house has cedar clapboard, homasote sheathing (no exterior vapor wrap), then the wall cavity has cellulose blown in that was definitely added sometime after the house was built since they missed many cavities. Interior walls are gypsum board with metal lath and plaster. The product I have access to is the following:
https://www.foam-control.com/design-resources-foam-control/
Product is foam control 100. My friend makes it at his business and he said he can cut it to any width and and thickness up to 36” (and get me a good price). The thought that makes this better is I won’t really need to do the cut and cobble method being I will get 3-1/2” thicknesses for the walls and 5-1/2” for the ceiling. I will then add another 9” for my attic floor to get a little over r60. Is this a good idea? Do I still need to add a vapor retardant (certainteed membrain?) behind the drywall? Is condensation an issue or is the perm rating of 5 sufficient? My thoughts are it has to be better than the cellulose in the walls now and the compressed and very old fiberglass in the attic. Thank you all in advance for reading all this and I am excited to hear your responses.
GBA Detail Library
A collection of one thousand construction details organized by climate and house part
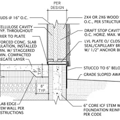
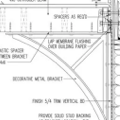
Replies
If it’s cheap enough you could use it like batts in the walls I suppose. I don’t think it would be noticeably better than cellulose though.
I wouldn’t use it in the attic unless you have to convert the attic to conditioned space for some reason. I would use blown cellulose on the floor here where it’s really an ideal material. Blown insulation is the best option for attic floors, far easier to install than anything else, cheap, and very effective in part because it all settles into one big blanket with no gaps or voids.
Bill
Foam only makes sense for two purposes:
1) vapor/ dew point control
2) use as a continuous sheet without thermal bridging
Are you tearing out the interior or exterior to install insulation?
Installing foam between framing will still require spray/can foaming the edges.
Cellulose is a much better option from a carbon standpoint and likely cost even with a foam discount.
The plaster is coming down on the interior walls touching an exterior. Exterior siding/sheathing is staying on the house. I am only doing this to one bedroom for now based on some water damage. The reason why I think it will be better than the current cellulose in the walls in because I have noticed settling and the installers (past owners or contractor) missed half the stud bays when blowing in from the outside. Therefore my guess is half of my wall cavities are probably uninsulated. I also thought I read somewhere that the cellulose in an older house isn’t great in the northern climates when it comes to moisture from condensation. The foam board will be a complete fill in between stud and ceiling joists due to custom thicknesses that can be provided. All edges would be sealed with a foam product since the boards will be cut 1/2” less than the stud bay width. Another reason why I like the product is there will be no settling in the cavities, retains r-value, and stands up to moisture. Even though the hope is my insulation won’t get wet, there is always the possibility and at least it wouldn’t be destroyed where as other products would be.
Vito
Having the foam custom cut (if there's not a large extra charge) does seem to make it better than cut-n-cobble. I may be tempted to downsize closer to 3/4" than 1/2" if you go that route, depending on your wall lumber conditions.
But your mention of water damage in your last post is concerning and most likely no type of insulation is going to fix that. Where did the water come from? You need to address that first and foremost.
Also, the issues you think exist with cellulose, by and large, don't. The settling only occurs if not installed to the proper density. If bays were missed, that's hardly the fault of cellulose as a material. Cellulose won't be destroyed by water any sooner than the rest of your wood framed walls would be. It actually offers some hygric buffering in this way.
The advantage I see to your foam is mostly that it may offer higher-R, but I doubt the cost to R works out (guessing not calculating on that). If you get it sealed well, arguably the air tightness could be better, but you can make efforts to air-seal your drywall or add an interior air-membrane with cellulose if you wish.
If you are set on using the foam somewhere, I would say use it in the walls, but not the attic. As Bill points out. But either way, first identify and address the water issue.
I’d probably just use mineral wool batts in the walls. It’ll probably be cheaper to use regular batts, and you’ll probably find that every stud bay will be a little different size so you’ll need every foam piece custom cut. Mineral wool to to fit a 2x4 wall is R15. Foam at best is going to be around R21 or so for polyiso, for EPS you’re about R14-15 or so. Your product is probably going to be around R17 or so so not significantly better than mineral wool (or dense Fiberglass batts), and with batts you can press fit everything to minimize custom cutting or spray foam needs. After thermal bridging of the studs is factored in, your foam product is not even a 10% improvement over batts.
The way to look at this is could you take the cost savings and use that money to improve something else for a better overall benefit to your home? I’d suggest putting the savings towards some air sealing work in other areas, or maybe getting a blower door test done or some IR camera scans to find other areas lacking in insulation.
Bill
So I didn’t mention that I did have the water issue fixed. Had a new roof put on which is where the water came from with ice damming from a terrible winter storm that we had. Now obviously ice damming can also be a byproduct of poor insulation but it also didn’t help that the past owners cheaped out on the roof and didn’t have any ice/water shield under the shingles. I understand there is some cutting that will be needed but I have a table saw. Those cuts will hopefully be limited though because my friend told me to measure every stud bay. I also understand the initial r value difference between wool, which was my initial choice will not be much but it was explained to me that over time it will loose r-value where the foam will not. At this point I have the wool priced out. My friend will give me the price after I give him the dimensions. If it is even relatively close I will go with foam.
My one question that I’m not sure was answered though do I still need the vapor retardant like certainteed membrain begins the drywall? Also is the perm rating of 5 sufficient to move moisture from potential condensation to the outside?
Mineral wool does NOT lose R value over time. If you're referring to natural wool, that I don't know for sure since I'm not very familiar with that product, but I suspect it does NOT lose R value over time either. Usually it's the polymer-based foams that lose R value over time as the blowing agents gradually diffuse out. This affects XPS and Polyiso, but not EPS.
I'd put up a smart vapor retarder like MemBrain. If nothing else, it's relatively cheap insurance, and it's not something that you can easily add on later if you find out you need it.
Bill
Don’t forget to factor in the cost and time to foam the edges. With 1/2 gaps all around you are looking at $1.50-$2.50 per 8ft 3.5” bay of foam. Smaller than 1/2 gap per side and it is difficult to make sure the spray foam filled from the back at 3.5” deep.
Rockwool will probably install 3-4 times faster as well in walls.
Use polyurethane caulk to seal top and bottom plates. Plan on air tight drywall. You May be able to seal the sheathing with tape and mastic.
If you really want to get benefit from foam, run full 1” sheets over the joists or use it to fur out the joists to fit more fluffy stuff.
Play with this calculator.
https://ekotrope.com/r-value-calculator/
So I have a little update to my scenario. The walls are down and I needed to fur out the studs so when I put up drywall, the face of the drywall will match the location of my window jambs. Therefore my stud cavity depth is a full 4”. This makes the foam scenario much better since I can get it in full 4” thickness. For the room I had my friend price out 4” thick in the walls, 5-1/2 in the ceiling joists and 9” above the joists in the attic for r60 total. He is also cutting them all at 14.5” x 8’ to limit some of my cutting. Grand total at $775 for this bedroom. Mineral wool, which would only be 3-1/2” thick in the walls, I priced out for comparison at $600. Foam board equivalent priced out at the big box store was $1300. I think I got a deal and I think it’s the right move.
I think you got a deal too, that’s pretty cheap! You might want to have him cut the batts just a touch oversize so that they make a tight friction fit in the studbays. It might also be worth making one “test batt” to test fit before you cut all the others. Be REALLY careful that all your studbays are the same, or allow for any differences since you’re essentially having everything prefabricated offsite. Measurements just get more critical in this situation is all.
Why not use blown cellulose in the attic space? I would normally recommend blown insulation in attics over batts of any type, or rigid foam. Blown insulation is both cheaper AND better (no seams/gaps, buries everything, etc) in almost all cases.
Bill
I do know what your saying but there is also a certain stubbornness to wanting uniform material. Maybe it’s a little OCD. Although the blown stuff has good properties, it’s also very dusty. I feel like if I need to get up in the attic for any maintenance reasons I will like the advantages of moving some foam around on top of the joists vs. digging around blown cellulose. In fact I wouldn’t even consider it. The only other option I had was to lay mineral wool batts down, but I would be compromising some R value unless I double stacked some thinner stuff. At 9” thick this is just one layer and it’s clean. I’m an engineer. I like things to look appealing and function well at the same time. Detail even when it won’t be seen.
I’m an engineer too. As you know, there are always tradeoffs. Blown insulation WILL perform better here, but you’re right: it is messier to work with.
If you’re committed to using custom cut batts in the attic, see if your friend can cut them with beveled edges so you’ll get a trapezoidal cross section. This will create longer air leakage paths and should help reduce the performance hit you get having multiple “batts” instead of a single homogenous layer of insulation like your get with blown cellulose.
Bill
Trapezoidal sounds cool and also would create a self locking feature. Although if I am putting the 9” “batts” perpendicular to the ceiling joists, I am also limiting the path for air to travel. Although what I might do is just have him cut them in wider widths. Enough to get up my pull down opening. It will actually be less work for him.
I would have him cut the widest “batts” possible that you can still fit. Fewer individual pieces will mean less installation work, and also less air leakage paths. You have the unusual ability here to pretty much spec whatever you want in terms of material dimensions, so I’d take maximum advantage of that, step back a moment, and think about everything you could do to both minimize your installation labor while maximizing performance. Slanted joints is one thing, extra-wide “batts” is another. There may be others, and Murphy’s Law dictates that some things will be glaringly obvious AFTER you do the job, but not before ;-)
Bill