What kind of insulation would you recommend for a 20′ shipping container being renovated into a home/studio space?

I’m renovating a 20′ shipping container into a home/studio space and am wondering what would be the best “green” insulation to use. I will be doing some interior framing so would like to insulate the inside walls and floor. As well, I am building a green roof/deck that is framed using the structural strength of the container (no weight on the center of the roof) and would like to add insulation between the joist supports and deck floor (approx 3″ – 9″ above the container roof) and the steel roof. This “deck” area will be waterproof sealed for the green roof so the insulation will be enclosed and not exposed to the elements, but will probably be subject to some moisture.
Thanks!
GBA Detail Library
A collection of one thousand construction details organized by climate and house part
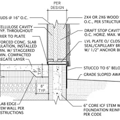
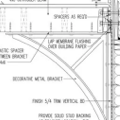
Replies
Sarah,
Because the steel container is such a good conductor (thermal bridge), 100% of the insulation has to be either on the exterior or the interior of the container. You can't mix and match (with exterior insulation on the roof, for example, and interior insulation on the walls).
Shipping containers have low ceilings, so you don't end up with much room inside if you choose interior insulation. So these containers require exterior insulation (usually rigid foam or spray foam).
Of course, you end up having to build a building around the shipping container to hold the insulation -- which makes the whole idea a little crazy. That's why I don't believe that it makes much sense to live or work in a shipping container.
For more information, see:
Low carbon and low cost?
Can I build a Passivhaus using recycled shipping containers?
I'm considering this same scenario, except I am looking to clad the exterior with a shingled Craftsman Bungalow compatible traditional finish. As Martin points out, building an outer box to support the insulation doesn't make sense, however, there are other considerations and means to arrive at a container based space.
Other mitigation considerations:
1) The reuse aspect of used shipping containers is a worthy green consideration. Reuse is the highest form of conservation.
2) Containers are a complete and self-contained structural system. As such in a non-occupancy application (storage and occasional spaces), they have very limited foundation requirements, which represents a significant cost, energy, and material savings. Directly related to reduced scopes of work for the foundations is a compressed construction timeline and linked labor costs. This is a big deal: 20' shipping container = ~$2,100 and 8' x 20' SOG foundation =~$1,500 - $2,000 or more. For weather tightness, longevity and maintenance, containers do require some sort of foundation, like either CMU "soap" corner pedestals or a compacted gravel base, or pressure-treated timbers, but those come in at <$500 - $1,000.
3) The self-contained structural nature of containers also means that once the unit(s) are placed and secured, the rough-in and drying-in are complete, including sealing.
4) Containers are portable/temporary and depending on one's jurisdiction, current zoning regs do not govern portable structures in the same manner as "permanent" structures and this can imply a reduced or eliminated permit process, which represents a huge time and cost savings. Enlightened communities encourage the use of recycled and reused building materials/systems.
5) Containers are well suited to rain-screen cladding systems.
This brings up my question, which is an insulation/installation question: It seems that an insulated sheathing system would be a good way to render a container into a more traditional form while adding insulation's benefits. My sense is that a system of insulated sheathing over wrap over simple 2 x 2 nailers would provide insulation and an acceptable substrate for traditional cladding, and the only difference between this system and a wood framed system would be the pretty minor added cost of the 2 x 2 nailers. Right? Have I missed something?
From what I've learned from people in my region who are doing DIY small scale container buildings, the costs are about the same for containers as for traditional wood framing, but it isn't clear whether that includes foundation costs. The DIY element seems tricky too, because while one would pay a lot for labor to build a small wood framed box, one might also incur some minor added costs for the cladding scope simply because tradesmen might have to adapt to the different frame system.
-- Thanks
Bradley,
Go ahead with your plan if you want. I'm not sure what you mean by "insulated sheathing," but I would investigate the minimum code R-values in your climate zone before specifying this product.
Once you get done using a cut-off saw to cut window openings and door openings in your steel box, I don't think you will see any savings compared to a simple stick-framed rectangle.
A shipping container doesn't even give you a sloped roof -- so if you want the water to shed, remember to spec some rafters.
All the usual other costs apply: roofing, siding, plumbing, wiring, kitchen, bathroom, interior finishes. All you are really getting with a steel shipping container is a guarantee that cutting holes is difficult -- and low ceilings, of course.
I'd echo Martin's concerns, but for anyone who is committed to the idea of using a container, this recent article from Building Science Corp. is a must read.
Fully wrapped exterior insulation is the most sensible approach to living in an all metal box, and the steps and construction details are all outlined in this article:
http://www.buildingscience.com/documents/insights/bsi078-ship-shape/
First off, don't use the "green recycling " excuse to start with a shipping container.
Shipping container are made out of steel and wood.
Nothing special here, they get recycled 100% and easily.
Then, the only reason why you would be using the very "restricting" containers for buildings is because it needs to be transported to the site and dropped in easily from an pre-fab contruction.
OR you got them for free ( even there ).
That said,
if you look hard for them, you can get extra height models which will acomodate interior life much easier for a few hundred $$ more .
Using wood and steel beams is usually cheaper for the same size as a container
( if you pay 2-4K$ for the container ) .
The only real advantage i see to using a container is the lack of required foundations
( if installed unregulated, on concrete blocks or so ) as it self supporting.
The problem with insulating on the exterior, or even cladding a shipping container, is that the only good reason for using one is that they look cool and you like the idea. That's why Starbucks used them in Washington, that's why lots of young architects use them. Their value is more symbolic than practical. Nothing wrong with that, but it's worth acknowledging so you can get the most bang for your buck from the experience and not get bogged down trying to make it green.
Here is an interesting take on them:
http://www.tincancabin.com/2013/12/the-shipping-container-cabin-in-perspective/
To All Respondents: Thank you for excellent replies!
@Martin, Ha! The term "insulated sheathing" caught my attention when I read a BSC article about it; of course they used no trade name, but described that is it is made of 1 of the 3 usual suspect foams used for rigid boards +- radiant layer(s). I was hoping YOU would know the products. Now I'm guessing it must be just rigid.
@Mark Fredericks: Thank you for that great BSC article link. It is a good read, not the usual dry wonkishness from a PhD, it is funny, and it is useful info. The exterior envelope details he shared are pretty much what I was planning, plus a floating sloped roof because neither my wife nor I is keen on the industrial look in our Craftsman Bungalow's backyard.
My situation is somewhat unique. My local zoning regs don't cover container construction yet, so I want to be the best architect I can be and do it right, but all with the understanding that I won't have to pull a permit. Or pay for a permit. I intend to approach the topic as "portable storage." The corollary of this situation is that as the containers are discrete, linkable structural units, they don't need a foundation. That said, I'll be using 6 corner and midspan CMU "soap" block pedestals for leveling.
Fortunately, the site is the SF Bay Area, so our weather is extremely mild; as this is to be a workshop/studio space for my practice, the tempering needs are less demanding than for a home. The floor doesn't need insulation, but everything else does for both tempering and for late night noise control. Yes, we'll be cladding it because we want to fit in with the shingled main house and the neighborhood. Honor the neighbors!!
Given these other factors, despite the containers' 8' wide modular limitations, the cost deductions for no appreciable foundation and no permitting or inspection fees seems to really help offset the $5K cost of the containers [2 x 8'W x 9'-6" HiCube x 24'L "Reefer (refrigerated/insulated) box]. Yes, I'll have to pay for sheathing, wrap, siding, and a entire roof system, but it still seems like it will come in cheaper than the traditional approach.
In addition to Jin's comment that recycling a shipping container by melting down the steel is easy and routine, if it's in good enough shape to continue being used as a shipping container, that's at least as good. And if it's not in good enough shape for that use, is it really good enough to make your building out of?
Are shipping containers even that portable, especially if you sheath and side them? I mean, if you want portable, wouldn't a tiny house be better or an air stream or any number of other things?
@Charlie Sullivan: Seaworthiness at the bottom of a stack of 8 fully loaded containers is a far higher standard than needed for building a shed/workshop.
@Keith H: Portable?? Yes, that is the point of their existence -- they're equally portable on a ship, train, truck, military air transport, or trailer. I am not looking for something that I'll be moving about much at all, but for the sake of getting it installed at my home, it must somehow be named/classified something in order for the Building Dept. to know how to proceed, or not in this case.