Radiant Floor Heating Over Unconditioned Garage
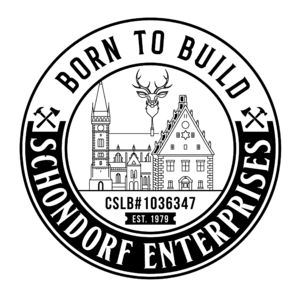
Hi all,
When it comes to best practices, right when I think I’ve got a strong general sense of the correct way of doing something, I go ahead and read a conflicting approach.
I’m looking to add radiant floor heating to the underside of sheathing where the bottom floor is an unconditioned parking garage. Uponor recommends that I go direct to the aluminum heat transfer plates with the insulation, while Joe Lstiburek says this: https://www.buildingscience.com/documents/insights/bsi-064-bobby-darin-thermal-performance#R3
I suppose what I’m looking to better understand is what assemblies call for including an air gap.
Cheers,
GBA Detail Library
A collection of one thousand construction details organized by climate and house part
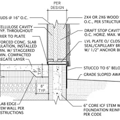
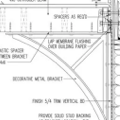
Replies
Aluminum heat transfer plates and an airspace are not mutually exclusive. You can certainly do both. The main point of Joe L's article is that the airspace between the insulation and the underside of the floor makes the floor warmer without significantly increasing heat loss, all other things being equal. But note that he does recognize that you can reduce heat loss further by filling the entire floor cavity with insulation, at the risk of cooler, or at least more uneven temperature floors. The combination of spreader plates and an airspace will minimize thermal "striping" best. Super Important: this entire discussion is premised on the requirement that the floor cavities be sealed airtight. This is a safety requirement for living space over a garage anyhow, but still very important. No garage or outside air should be able to blow into/through the floor cavities or all bets are off.
So my advice: First, you have to meet code for insulation, or code plus if you are shooting for better-than-code energy performance. Once you select your insulation material and thickness, you see if there is extra space in your floor system. If so, you can leave the airspace above the insulation to make floor temps more consistent. If the local muni inspectors give you a hard time, tell them that the garage ceiling is your air barrier and make sure that it really is.
One final nice detail: If you use I-joists for the floor framing, there is less thermal loss through the webs than solid sawn lumber. Also, you can use 1/2" foil-faced (or thicker) foam insulation nailed against the underside of the top flange to create your airspace. Fill the space between the foam and the ceiling drywall with fluffy insulation. The foil acts as a radiant barrier and improves both energy performance and comfort. Might make the spreader plates unnecessary, but it would take some pretty serious modeling to tell for sure.
Cheers. Got you. Was thinking the same thing with the rigid foam. We’re actually using floor trusses. Will air seal the cavity , than air bottom of the trusses.
In general , where else would a sealed air gap in instillation make sense?
Can you put it on top of the floor, inside the apt?
We're looking at that option as well. It's new construction. Feels like it might be more cost prohibitive. Originally, was really trying to understand the difference in performance: Under sheathing with heat transfer plates vs above sheathing in say a Warmboard type of product.
You can still use transfer plates on top....warmboard isn't your only option...
I thought about your input. Looking at going on top again. Planning on engineered wood floor; what in your opinion is a cost effective option here.
I'm sure I'll get some slack for this but if you don't want to pour a thin slab and use engineered wood flooring instead, I would put down a layer of rigid insulation with a reflective coating (1/2 inch stuff), I would then use similar insulation on which to lay the transfer plates, basically strips between the tubing with the transfer plates on top. Add a layer of cement board in contact with the plates,(an optional thin slurry of mortar could be applied to tie it all together or just for the joints), a layer of luan, then your wood floor.
Before you secure the cement board, walk on it to make sure it's not to squishy, you can add strapping or strips of plywood for more support if necessary or you could skip the second layer of insulation if necessary also....
Lots of good info over here ... https://forum.heatinghelp.com/
There are a lot of over the top options.
I used Climate Panel (from Viega, same as the Uponor product) for reasons of it being thinner, able to survive a splash (kitchen), mid price range. Retrofitting the underside was not practical, requires higher water temperature, etc.
If you choose over the top, be super careful that the floor installer does not hit the tubing with a nail.
With floor trusses, blown-in cellulose seems like a natural fit. If you are clear spanning the garage, your trusses are probably at least 14" deep. That's a LOT of room for insulation. Celllose is by far the cheapest per R-value and naturally fills around the truss elements. You can make up for the lack of a radiant barrier on the airspace with more cellulose and still save $$. The trusses also make looping the radiant coils super easy. I'd go with staple-up with or without the spreader plates
Agreed. The advantage of the air space is only if you look at things from a very specific narrow perspective, and you'd be using more different materials and dealing with fussy details. Just fill it up with cellulose and get good performance cheaply and easily.
If you are trying to decide between suspended staple up tube radiant floor heating or a tube & plate system and you want a quality job, I would recommend you read the following article: https://www.hpacmag.com/features/higher-performing-heated-floors/
TLDR; choose tube & plate
My preferred option is Ultra Fin. These have most of the benefit of heat plates while keeping the tubing away from the subfloor so you can install standard nail down flooring.
The drawback is that you need a gap between the insulation and the subfloor above and you need to air seal (which you should do anyways) otherwise lot of the heat from this cavity can be lost.
Quicker install, uses much less tubing and you can also adjust the spacing to match your water temperature. This means that you don't need a separate low temperature loop and can run it at the same temperature as standard rads/baseboards.
That has its advantages, but I don't like its reliance on high-temperature water. We are going to want to change over to heat pumps soon, and that will be easier and more efficient with floors that can work with low-temperature water.
It can run at low temp but does reduce the BTU output. If you look at any decent construction, you are around or under 10btu/sqft which is doable with low temperature water (sub 110F).
That is a excellent point about designing a new build with heat pumps in mind.