Where is the “warm side” ?
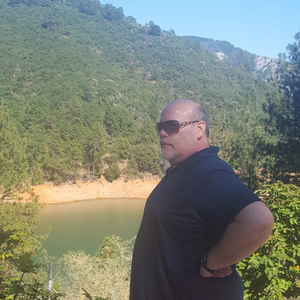
Seems simple. Before the advent of exterior insulation or double stud-walls, if a building code required a class I or II vapor retarder on the “warm side of the insulation”, that would obviously mean covering the interior studs with poly prior to drywall or using an airtight drywall approach. But many people including Martin H. seem to frown on polyethylene under drywall, even in climate zones 6 or 7. How to interpret “warm side” when there is insulation on both sides of WRB+sheathing layers ?
Besides … if there is sheathing, WRB, and R20+ insulation outside a stud wall, that WRB is already on the “warm side” of a lot of insulation, so should it be a class I/II ? Does an interior class I/II vapor retarder under the drywall still make sense ? Is this where that Canadian rule of thumb about 2/3rds of R-value being outside the VB is still good ?
If building a double stud wall with the interior wall being structural and requiring structural sheathing, it would seem natural to place a vapor retarder there before building the non-structural exterior wall to hold more insulation and cladding. Then separately insulate that interior wall cavity from the exterior cavity including the gap between walls. So, once again, there would be a vapor retarder on the “warm side” of a lot of insulation. This seems to be what happens when people retrofit by adding Larssen trusses to hold more insulation — lots of new insulation outside a new VB attached to the existing sheathing.
Building Science’ Joe L. “Perfect Wall” claims a vapor retarder on the exterior sheathing then exterior insulation works in any climate, so no interior vapor barrier should be used. Keeping the whole house interior, including the studs and sheathing, inside the VB and insulation layer makes so much sense, but this whole “warm side” verbiage is bugging me when we now have insulation on both sides of what would have been exterior sheathing in the olden timey days.
Thanks for any comments,
Kirk
GBA Detail Library
A collection of one thousand construction details organized by climate and house part
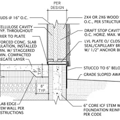
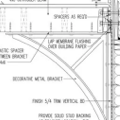
Replies
Kirk,
Our code here in BC defines the vapour barrier location as having to be as "sufficiently close to the warm side of the insulation to prevent condensation at design conditions."
So it is the dew p0int of the assembly that determines how far towards the exterior the vapour barrier can go.
Note that smart retarders must be fully on the interior side to have the normally expected perms vs interior humidity. Move them towards the middle and the amount of moisture entering the wall goes up. At some point, this becomes a problem {edited}.
Also note US code - which says "interior side" (not warm side or middle).
https://www.continuousinsulation.org/content/2021-ibc-irc-adopt-improved-vapor-retarder-requirements
Jon, thanks for that link. That pretty clearly shows a WRB (but permeable) sandwiched between exterior insulation and sheathing with cavity insulation inboard of it and a vapor retarder just behind the drywall. And that is in a 2021 IRC/IBC code. I really thought interior poly was in bad odor now, but guess not.
So in my proposed California Zone 16 (which I think equates to national Climate Zone 6), mountains with 9,000 HDD it sounds like this would be a safe assembly ?
1. Drywall
2. Poly or smart retarder
3. 2x6 wall filled with cellulose
4. OSB sheathing
5. Delta-Vent SA WRB
6. R15 Rockwool
7. 2x4 furring strips
8. R6 Rockwool ComfortBoard
9. Open porcelain cladding
This sounds like the wall assembly would only be able to dry to the outside if using poly but both ways with a smart product under the drywall ?
A WRB -- Water Resistant Barrier -- is not a vapor barrier, it's not even a vapor retarder. WRBs are intended to block bulk (liquid) water, but be open to water vapor. That's the important distinction. A typical WRB is NOT a sheet of polyethylene.
Polyethylene is a vapor BARRIER, not a vapor RETARDER. Vapor retarders are usually a good idea, but you have to be careful with vapor barriers. That's why poly is usually not recommended in wall assemblies, but vapor retarders are either recommended or mentioned as "extra insurance" against moisture problems within the wall. Smart vapor retarders and polyethylene are NOT interchangeable -- they are very different products.
Your assembly has one problem and one special case. The "special case" is your #2 -- poly here is not a good idea, but a smart vapor retarder is. A smart vapor retarder will "close up" to help keep moisture out of the wall, but "open up" to allow drying when needed. What happens when is based on the mositure conditions in the wall. You are correct that the poly would prevent inward drying.
The problem is that you have R6 comfortboard on the exterior of your rainscreen, which is what I assume the 2x4 furring strips are for on line 7. You don't want a ventilation channel between insulation layers since it will cancel out the insulation towards the exterior of the gap. If you transpose lines 7 and 8 so that your insulation is all stacked together, then you'll be OK BUT regular rockwool is too squishy to work here -- you'd need either rigid foam (polyiso, EPS, etc.), or more rigid rockwool, which is what Comfortboard is.
BTW, the usual rule for us denizens of the frozen North is that the vapor retarder goes on the "warm in winter" side, which would be the side closest to the interior of the space. The reason is that the goal is to keep the moisture in the relatively moist, warm interior air from getting into the wall and condensing on the interior side of the cold exterior sheathing.
Bill
Bill,
Yes, I understand the difference between vapor barriers like poly and smart vapor retarders. I was referencing the document Jon linked to that included poly as one of the possibilities in that interior position. I am still amazed that a 2021 version of the code suggests poly there. Kind of the root of my posting this question was thinking interior poly was a bad idea but the code seeming to require it in my CZ.
There would be no gaps in the exterior insulation layers, and no squish. My intent was to use a 2x2x2 squash block between the 2x4 furring and the wall placed ever 16" with 6" lags going all the way through from furring into wall studs behind the sheathing. So no "squish", but a very solid connection at the cost of som small area of thermal bridging . The R15 ComfortBatt would be horizontally stuffed behind those furring strips continuous except for the squash blocks, compressed to 2" thick under the 2x4, but slashed to allow them to uncompress to full 3 1/2" thickness everywhere else. Then the R6 ComfortBoard would be a continuous layer outside the 2x4s. Yes, the squash blocks are a small thermal bridge, but there is still the R6 continuous even there. Maybe I shouldn't call them "furring strips" because they would almost be a very shallow Larssen Truss, with one chord being the stud behind the sheathing and the 2x2x2 block the "ladder rung".
The furring strips are there to support the weight of the cladding via ZMax brackets and attach the ComfortBoard without needing really long screws. I realize there would not be a rain screen gap this way, but since the ComfortBoard won't hold water, and the open cladding should ventilate well, it seemed like it would be preferable aesthetically. I like open cladding, but I don't like seeing the furring strips. I also like the idea of the furring strips being behind a fire resistant and termite resistant layer of ComfortBoard. Silicate mineral paint should bond well to the ComfortBoard and be very UV resistant, so I might just paint those areas behind the gaps in the cladding, or I might use Forta Quattro over the ComfortBoard. I suspect the Quattro would actually make the assembly less fire resistant than using the Silicate mineral paint, and I may like the texture of black painted ComfortBoard better in those gaps than the flat smooth Quattro marred by occasional tape strips.
Interior poly IS required in some areas (notable in Canada). It can work, it's just that smart vapor retarders are safer. The general idea is that it's always better to allow for some drying potential, since moisture always seems to be much better at sneaking into a wall than it is at getting out.
I wouldn't worry too much about the thermal bridging of your squash blocks. The total area of the wall covered by those blocks will be relatively small, so they won't contribute much in the way of thermal losses. I would be careful what you make those blocks from to avoid splitting though. Stacked pieces of plywood, ideally glued together, would likely hold up much better than pieces cut from framing lumber.
Have you considered using exterior polyiso instead of mineral wool here? You'd probably save quite a bit on labor that way, and the materials may well be a bit cheaper too.
Bill
Bill,
Thanks for the idea about not using framing lumber for the squash blocks. I hadn't even considered that. I was going to cut 2" lengths of 2x2 douglas fir and drill an oversized hole thru it, creating a large "washer", partially filled with acoustic caulk during installation. I expected the pre-drilled hole to prevent splitting, and the end-grain to shrink less than flat pieces stacked. You think stacked IPE would be better ? It is nearly waterproof and fire resistant. I'll be using IPE for window and door jamb extensions. Might be hard to work with for creating so many stacked blocks.
I did consider polyiso, which by itself is half the cost per R- of ComfortBoard, but I worry about fire resistance in this dry mountain forest environment. Plus I am trying to avoid foam anywhere. I would want a drainage mat between polyiso and cladding, which would add cost, whereas the ComfortBoard is its own drainage mat. There is also the issue of texture visible thru the 3/4" gaps in the cladding. If I had to cover the polyiso with a UV resistant Quattro, the combined cost would be close to ComfortBoard + silicate mineral paint.
Here's a silly question for you: An interior vapor retarder on the walls (and ceiling, I suppose) already has the difficulty of sealing around electrical boxes, etc. and the long-term issue of punctures from hanging pictures, etc. But what about the floor rim joist area ? I plan a closed, conditioned crawl space with Grace Ice & Water wrapping the top of the stem walls and taped to Poly covering rockwool over crushed stone crawlspace floor and inside face of stem wall. The Delta Vent SA would be taped to the Grace on the exterior side. But ... Where the wall base plates sit on the subfloor creates a break in the interior vapor retarder layer, doesn't it ? Vapor could theoretically come up from the crawlspace along the rim joist and up into the wall I so carefully sealed with a smart vapor retarder.
2x2s like you describe are very likely to split. I would not trust them for this. You'll also find that compressing the end grain (drilling through the end of the 2x2 instead of the side) will increase the chances of splitting, at least it has in my experience. I always drill through the side, across the grain, for a through bolt. Plywoods layers have the grain alternating with every other layer, so there is much, much less risk of splitting that way. Regarding IPE, I think you'll find that any hardwood is more resistant to splitting that pine framing lumber. The downside is the cost of the hardwood. You'll probably end up needing more than you think -- you'll have a bazillion squash blocks to make.
Polyiso is the most fire resistant of the rigid foams, but it's nothing like mineral wool -- mineral wool is fireproof. I suppose you could use Dow Thermax with the beefier fire resistant facer on one side, but that's still not as good as mineral wool. I think you'd have less issue with a texture with polyiso though, at least assuming you want a smooth texture -- painting a faced sheet of polyiso will be like painting a piece of glass, or at lest drywall, in terms of appearance. The foil facer is very smooth.
You could use kraft or fiberglass mat faced polyiso, which is vapor open -- a little -- but no where near as vapor open as mineral wool. Kraft facers are going to increase fire risk too, so it's a tradeoff.
If you stay with mineral wool, I would try to do it all with comfort board, which I think will be easier to work with in your application compared to the batts. The tradeoff is obviously increased materials cost.
I've never put a vapor retarding in the rim joist area. I've always done rim joist insulating in one of two ways, either spray foam or foamed-in rigid foam panels. My own home I did with foamed-in panels of 2" EPS, since I wanted a bit of inward drying (there is foil faced polyiso on the exterior, so zero drying to the exterior for me).
If you seal between the sill plate and subfloor, you don't really have a break in your air barrier. All you have to do to do this is to lay down a bead of sealant prior to setting the sill plate (or more likely, prior to standing the wall up). I like polyurethane caulk for these kinds of things because it holds up very well. You do need to seal any penetrations though (wires, pipes), which I do with canned foam.
Bill
You're right, 1500 squash blocks needing 750 linear feet of ipe 1x3 would be expensive and scraps left over from making the jamb extensions wouldn't be enough, but I'll undoubtedly have lots of scrap ply and OSB as well.
I guess I am unusual in that I think I might prefer the rough texture of painted ComfortBoard over the smooth texture of the other options. I might not like it once I try it, and I'll end up with Quattro over the ComfortBoard in that case.
A bead of caulk under the edge of the bottom plate isn't going to stop vapor moving through the OSB subfloor and right through the bottom plate, is it ? I suppose more than 2" of solid wood is not very vapor permeable anyway. Holes will probably be caulked with acoustic caulk so it never dries or shrinks. I haven't decided what to do about rim joist insulation in the crawlspace. I don't like foam, and besides, I've heard being able to inspect for termites is important. Removable batts are the only choice in that case.
Whether or not you like the texture is an aesthic call that only you can make. I suggest if you want a texture your might look into Densglass, which is a glass mat faced gypsum board product. It's commonly used for exterior facade work on commerical buildings, it can be exposed to the elements, and it's a very fire resistant material. It also has a texture that is a bit like window screen, so it would give you a consistant rough texture if you painted it.
A layer of wood that ends up being some 2-1/4+ inches thick isn't going to transport much moisture. A smart vapor retarder is likely to be more vapor open than the combination of 3/4" subfloor and 1.5" of sill plate. I wouldn't worry about moisture transport through the framing itself as long as you make sure all the holes are sealed.
Why are you against rigid foam? It's a good product here. It doesn't really add fire risk if it's indoors, and you could always put some mineral wool over it if you want a fire barrier. You can't use removeable batts against a rim joist (well, you shouldn't use them), because they allow moisture to get through and condense against the rim joist, which allows rot to set in. You need something to keep moisture from reaching the rim joist, which pretty much means rigid foam or spray foam. I would not attempt to use batts and a vapor retarder here.
It is possible to put in removeable rigid foam blocks, but it's tedious to seal them all. Typical termite inspection strips are actually UNDER the rim joist, since the termites build mud tunnels up from the ground. The inspection looks for those tunnels more than it looks for the termites themselves. If you are worried about termites, I would use treated wood for the rim joist (the BLUE treatment is for termites), or for an existing structure, a heavy coat of Coppercoat gives a little extra protection, although a borate treatment is what is usually used. Apply the borate solution, then put in your rigid foam panel. You seal in the termite killing compound that way.
Bill
I have used polyiso and EPS before as well as Great Stuff in a can. I have scraps in my garage that are ten years old, and I can still smell them. I don't care for the odor of any of them.
I'll have to look more into the alternatives for rim joist insulation. I did already plan on spraying everything within four feet of any concrete with Borate, including all sides of the rim joists, subfloor and floor joists. I've never seen any blue treated lumber at my local stores, but maybe HD can order it for the rim.
The blue treated lumber is most common in areas with a lot of termites. You see it a lot on Austrailian projects, and areas in the Southeastern US. It's probably not as readily available in areas with lower termite risk.
Bill
I thought we had a pretty serious termite problem here in southern California. I had to tent a house 3 years ago for it and repair $15K in termite damage. Hard to believe blue treated wood isn't on the HD shelves here if it is any better than Borate spray. Not that the house with the damage had that either LOL.
Jon, are you against the 'ideal double stud wall' design? That places the smart retarder somewhere around the 1/3 mark (from interior).
I'll edit #2 to be more specific.
I think it would work well with proper attention to Joe's "The permeance and location of vapor control is dependent on the climate zone". Eg, I'd be concerned about the poor perm ratio with Zip (reported to be 1 wet perm) on the exterior in Z6-8. The plywood/OSB vapor retarder being 1/3 in only makes it worse. Use fiberboard on the exterior and the concern goes away.
Perms:
https://foursevenfive.com/blog/why-the-vapor-curve-matters/
Recommended perm ratios can be derived from Table 2A:
https://www.appliedbuildingtech.com/system/files/abtg_rr_1701-01_moisture_control_guidelines.pdf
Seems like it would be easiest to keep the stud cavities empty, have no vapor retarder on the interior, put an actual vapor barrier like Grace on the OSB sheathing and put all insulation on the outside. The OSB would always be warm well above the dew point in winter, and in summer any humidity would condense against the Grace and either run down and out weeps or dry to the outside.