Why isn’t porcelain cladding common ?

Most porcelain, from wood-look planks to large format stone-look tiles, are impervious to moisture and are insect proof, rot proof, frost proof, fireproof, and highly UV fade resistant. All these properties for a material that can be as inexpensive as $1.50/sf. It would seem to be a great cladding material for single family homes, yet most examples I see are commercial, and the few residential examples are set in mortar on concrete/block walls.
Porcelenosa and a few others offer what appear to be extremely expensive furring attachment systems that seems to be geared toward commercial (again, concrete substrate) walls with thicker, heavier slabs. These seem to require heavy gauge aluminum and PVC tracks along with special mounting clips and “biscuit” cut slots in the slabs for the clips, as in StoneClips dot com. Anything involving heavy gauge aluminum angle on a 24×24 grid must be mongo expensive.
This seems like overkill to me, considering the relatively light weight, especially if you are going for an open cladding look. Wouldn’t a simple clip similar to plywood clips for roof decking, screwed to 1×4 or 2×4 furring strips be ample ? Or a board and batten look using 8×48 porcelain planks horizontally with a vertical cedar or ipe batten every 48 inches retaining the planks to the furring strip and hiding the vertical joints.
I did find another reader question here from 2017 in Ontario who tiled and grouted porcelain tiles as cladding over concrete backer board attached to furring for a rain screen gap. That had been waterproofed and tiled like a shower wall. That sounded like asking for trouble by bonding an impervious porcelain to porous materials that will shrink and expand in extreme temperatures, but was apparently the recommendation of the thinset mortar mfr.
I would think each tile being able to move a bit independently within its clip attachment points and wood furring strips that might move a bit over exterior insulation would making cracking and broken tiles less likely than a mortared application. Just the porcelain alone, mechanically trapped with clips or the heads of trusshead screws hidden by trim seems like such a simple solution that there must be flaws that keep it from being common. So hit me with those flaws !
GBA Detail Library
A collection of one thousand construction details organized by climate and house part
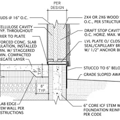
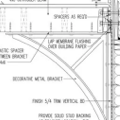
Replies
Too heavy and brittle?
Cost of base materials is one thing, fasteners and labor another. I tend to approach things the other way around, preferring more expensive materials that are easier to fasten and install; a lot of stuff eventually requires maintenance, and while one might endure a first application, a second time around might not be so "fun" (if someone else is doing the work then figure you're going to be paying for their "fun").
For me, I'm looking at metal. It's equally as resistant to the elements and pests. I'm guessing that it's lighter (an important thing for me as a one-man-builder-to-be is thinking about how I alone can manage materials). Sheets/panels can be ordered to length (not sure the max, but can be pretty long; wanting to say 40'?).
Thanks, Mark.
I thought 10mm porcelain tiles were considered pretty tough. A 24x48in tile does weight 35-40lbs, so they are heavy to manhandle, but I wouldn't think beyond one guy handling one tile at a time. There are lots of specialty cladding products and specialty fasteners, even some porcelain bonded to foam insulations, but they all come at very high costs per square foot. A definite consideration when talking about 3,000+sf of exterior wall. Also with all the questions about the continued availability of the product, warranty and support, with a specialized product. If generic porcelain tile could be attached simply with two ten cent fasteners directly to wood framed walls or furring strips, the cost per square foot could be as low as fiber cement siding, with all the non-porous and zero maintenance advantages of porcelain or steel.
Here are pictures I saw that made me ask this question about simple clips like the Simpson PSCA clips.