Will Cold Deck and Solar Panels Crush Supporting Polyiso Insulation Over Time?

First let me say thanks to all the contributing members for the wealth of information I’ve found here! It’s been a huge help in my roof odyssey. After much iteration, we’ve settled on two approaches, but have concerns about the durability of the polyiso over time in approach #1. Would love your input, so please read on….
Background: We’re renovating our 40 year old log home, which has a full cathedral ceiling, with 2×4 tongue and groove placed over exposed interior log purlins. Due to condensation and roof age issues, we’re tearing off everything above the T&G. We need to keep the roof thickness down for a variety of reasons that I’ll spare you. We live in the 4c climate zone in Portland, OR. Roof pitch to 6/12 on one side, closer to 9/12 on the other.
Approach #1: From the bottom up, existing T&G, ice and water shield, 2″ polyiso, 2×4 rafter boards to create ventilated space, plywood deck, underlayment, standing seam metal roof.
Approach #2: From the bottom up, existing T&G, ice and water shield, build out ventilated rafter bays with 2×6’s on edge, block with 2×4’s, 2″ polyiso between blocking/rafters, plywood deck, underlayment, standing seam metal roof.
Once or twice a year we get about a foot of heavy wet snow, and we’d like to cover the majority of the roof in solar panels.
Approach #2 is a durable, rigid assembly that won’t care one bit about snow or added weight of panels, but has a lot of thermal bridging and is about 10% more expensive than Approach #1. This will still be better thermally than the roof it’s replacing, and our heating/cooling bills are already tolerable (and will be zero with solar panels, as we’re full electric).
Approach #1, being the cheaper and more thermally efficient option, is really appealing, but I’m a bit leery of putting the polyiso in compression under the weight of the entire roof, especially transferred through the 2×4’s (although the will be wide face down). We’ll have timber screw connections prescribed by an engineer to resist shear, but what will happen to the polyiso over time? The old polyiso we’re removing is totally shot, all crumbly, but it’s also been wet. I’d hate for the new polyiso supporting a whole lot of roof to slowly crumble as well….
I know over-roof insulation with polyiso is common, but in those scenarios there isn’t typically a ventilation space above the polyiso. In my case, it’s the 2×4’s focusing the load into the polyiso that’s concerning.
Would love to get the group’s input!
GBA Detail Library
A collection of one thousand construction details organized by climate and house part
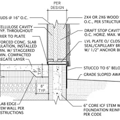
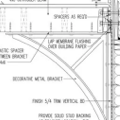
Replies
If you want to spread the load out more, put plywood over the polyiso, then 2x4s, then another layer of plywood. You can use OSB instead of plywood if you want too. The extra layer will help distribute the load. With 10PSI rated polyiso, an 8 foot 2x4 on edge is good for 1,440 pounds (144 square inches of contact area on the polyiso) of distribute weight. You could also put a 2x4 on the flat against the polyiso with a 2x2 in the center of that on top to create a 3" vent channel that has 336 square inches in contact with the polyiso for 3,360 pounds of allowable loading. That 2x4+2x2 arrangement is probably cheaper than a second layer of plywood or OSB, and might also be easier to build.
Another possibility is to put "hard points" in to secure the solar panels. With this arrangement, you put rigid structure through the roof in a few key spots that will go up through the roof and tie into a structural frame above the roof that is there to support the solar panels. In this system, the roof insulation doesn't carry any of the weight of the solar panels. Some solar panel manufacturers make racking that will work for this, otherwise it's common to build the rack with steel strut and associated fittings. This might be another option for you that will also help to cut down on thermal bridging compared to putting in what amount to "mini rafters" on top of the roof deck.
Bill
PNW Rancher, I like to refer to GBA articles.
Unless I have misunderstood, you are planning to only put 2 inches of polyiso 12-13 of R-value.
I reference this really well written GBA Article
https://www.greenbuildingadvisor.com/article/how-to-install-rigid-foam-on-top-of-roof-sheathing
The article keeps it really simple with just two options:
Option 1: You can install all of the insulation above the roof sheathing (in which case the rigid foam has to meet minimum code requirements for ceiling R-value); or
Option 2: You can install some of the insulation above the roof sheathing, and the rest of the insulation underneath the roof sheathing (and in direct contact with the roof sheathing).
While we know that zone 4 requires R49 on the roof, you mentioned that R12 Polyiso is better than what you have and you expect to have very low energy bills with the solar panels.
This is what I would do if it were me (this does not meet code) and I explain why below:
- From the bottom up,
- existing T&G,
- ice and water shield,
- 1st layer of 2″ polyiso taped air tight
- second layer of 2" polyiso with seams overlapping the seams of the 1st layer and seams taped
- 2×4 rafter boards laid on the flat to create 1-1/2" ventilated space,
(Option to put 2x6 if I was concerned about pressure on the polyiso)
- plywood deck,
- underlayment,
- standing seam metal roof.
Why?
> You said you did not want to exceed a certain roof thickness, so I take that into account.
> Since the code requires R49 on the roof in Zone 4, I would get closer to that if I could and reduce the size of the air gap.
> I don't think you need a ventilation gap that is 4-1/2" wide so I would lay the 2x material on the flat. That is exactly what the article I reference recommends. The air gap does reduce the risk of ice damming.
> I have read to about SIPs panels and how the single layer of foam insulation has caused problems with cold air hitting the "warm deck" through the seams. Therefore, having 2 layers of polyiso with seams overlapping would give me much more confidence in the assembly.
>> Various articles on the GBA search about the single layer of SIPs:
https://www.greenbuildingadvisor.com/?s=sips+roof+failure
Air barrier
You will have a pretty good air barrier over your deck with the peel and stick ice/water shield. If I were getting into this much retrofitting, I would look at whether I could make the air-barrier from the walls connect to the air barrier of the roof. This may be too difficult to take on with a log home and we can only ever do so much.
Attaching roof elements can get tricky when we have really thick layers over the roof. The article talks about this and I have seen it first hand. Plan ahead how you will find your log purlins below, assuming you don't just want to hit the 2x4 deck.
Building code insulation value table
TABLE N1102.1.2 (R402.1.2)INSULATION AND FENESTRATION REQUIREMENTS BY COMPONENTa
https://codes.iccsafe.org/s/IRC2015/chapter-11-re-energy-efficiency/IRC2015-Pt04-Ch11-SecN1102.1.2
Polyiso's compressive resistance is usually 15 psi, or sometimes higher. That's for 10% deformation. In other words, with a load of 15 psi, 2" polyiso will "squish" about 0.2". For sustained loads, there is an additional "creep factor" of 33%, which can be equated to saying that a load of 5 psi will result in 0.2" deformation.
Deformation of 0.2" is on the high side of what I would want to see on a roof, though it would probably be fine, I might limit it to 0.1" (about 1/8"). Deformation vs load in foam is roughly linear, so to get half the deformation, you need half the load, so let's say 2.5 psi is the maximum design load.
You don't mention spacing but let's say you want to use 2x4s on the flat, 24" o.c.. So for every square foot of roof area, you have 21 sq.in. of 2x4 bearing on the foam. 21 sq.in. x 2.5 psi = 52.5 lbs/sq.ft.. That's the most load you would want to keep foam deformation to 0.1".
In Portland you probably have next to no snow load. PV panels weigh around 2.25 psf. Round up to 3 psf or even 5 psf to account for the installation racks. The other dead loads on the roof will be less than 10 psf. So you'll have a total of about 15 psf for a roof assembly that can handle over 50 psf.
Thanks for the quick replies, especially the details on loading! Yes, we were considering 2x4s on 24" centers, 3.5" face against the polyiso for a 1.5" air gap. The log purlins are 40-48" on center, and not consistent, so I'm hoping to have an engineer prescribe a fastener solution that can land in the T&G only.
We're trying to avoid penetrations through the standing seam panels, and plan to mount the solar panels using S-5 clamps.
Any thoughts on how the polyiso will do over time? Will it's compression resistance or load bearing capabilities lessen over 10, 20 , 30 years?
Thanks again!
Just going from my experience with old polyiso in old assemblies, I would say that polyiso doesn't really change physically over time in terms of compressive strength. Mostly what I see is the exposed edges tend to yellow, so instead of the new white-ish color, it ends up a yellow/orange color over time. Structurally, the old panels feel about the same to me. I'm not aware of any formal testing for "aged compressive strength", but my understanding is that that particular property of the material is not expected to change significantly over the years.
Bill
This is not exactly what you are looking for but thought it might add to the general understanding of compression strength and stresses.
https://www.facilitiesnet.com/roofing/article/Deflection-Crushing-of-Roof-Insulation-Can-Contribute-to-Single-Ply-Roofing-Failures--12987
I did further reading and found that polyiso is one of the 2most popular insulation products for liquid natural gas pipes. In reading the install guidelines for this application, I found that they speak about pipe hangers that hold pipes in the air. There 2 types of installations: 1) hangers are in contact with the underside of the metal pipes and 2) the hangers/saddles are placed under the polyiso that is around the pipe.
https://www.dyplastproducts.com/installation-isoht
If the LNG industry is able to hang polyiso insulated pipes in hanger saddle without degrading the insulation, then I would expect that the pressure from your 2x4 on the flat would not pose a significant risk of degrading the polyiso on your roof deck.
I have not yet found documents that talk specifically about 2x4 on the flat. I will keep you posted.