Recommendations for Easy, Budget-Friendly Exterior Insulation

We’re planning to add insulation and new siding to our 100 year old zone 6 home next summer. We’re in Montana and its quite dry here.
The exterior walls are old dimensional 2×4 with a mix of drywall and lath and plaster inside. Some of the wall cavities have blown-in cellulose and I imagine some of bays have little to no insulation. I’ve pulled off a few areas of exterior siding and it looks like there is shiplap over the studs.
I’d like to add insulation to the exterior. I’ve been considering simply fastening zip r panels over the shiplap. IRC 702.7.1 suggests that R7.5 would suffice given my wall thickness. With zip’s r panels this would suggest that a 2inch (R9) panel would be appropriate. I’d then be putting hardiboard over the top of the zip-panels. Any concerns on this configuration?
Any other suggestions for a better insulation spec given my wall depth etc? Budget and ease of install take priority. I am open open to foam board and can make up for the negative impact on other aspects of the project.
GBA Detail Library
A collection of one thousand construction details organized by climate and house part
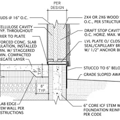
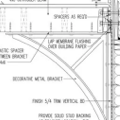
Replies
ZipR is not cheap, usually used when install cost is high and when it also is your structural sheathing. In your case, you already have a solid building, so the structural aspect of the ZipR doesn't add all that much.
The right insulation answer depends a lot on your windows. If you are keeping the existing windows, the better approach is a layer of peel and stick WRB to seal up your shiplap, flash you windows to this layer and install rigid over that. Since you only need R7.5 (~1.25" of polyiso) you can nail up the rain screen strapping with standard 3 1/2" framing nails and hang your siding on that. You'll have to do a bit of extra trimming to extend out your window trim past the foam to the new siding layer.
If you are installing new windows, you can go with ZipR or small window bucks and move your WRB plane and windows to the outside (I'm a big fan of outie windows). If you are dealing with 3 1/2" studs with 2" foam (or real 2x4 with 1.5" of foam), you can then go with standard flanged windows with jamb extensions for 2x6 studs. Very quick install. Also works great for doors.
Assemblies for rigid insulation tend to be very expensive, so there is very little ROI for much thicker foam. Something around an R20 to R25 assembly gets you most of your energy savings (2x4 with batts + R7.5 to R12 of rigid).
You may be able to source reclaimed rigid foam from someone like Insulation Depot. This approach is much more affordable from a materials standpoint and much greener as well.
My biggest concern is how to manage moisture.. where does my vapor barrier go etc?
>"The exterior walls are old dimensional 2×4 ..."
--------
>" IRC 702.7.1 suggests that R7.5 would suffice given my wall thickness. With zip’s r panels this would suggest that a 2inch (R9) panel would be appropriate."
The R7.5 prescriptive presumes R13 fiber-fill in the wall cavities, typical for mid-density fiberglass or cellulose at 3.5". But in a full dimension lumber with mid density fiberglass or cellulose you'd be at R15. The ratio of the exterior R to total R is what determines the temperature and peak moisture of the susceptible sheathing layer, so with R15 cavity fill it's prudent to go with at LEAST R7.5 x R15/R13= R8.7, not R7.5.
R9 ZIP-R would really be pretty much the absolute minimum, though fairly expensive compared to sheet foam + furring. While the hygric buffering of cellulose would add a bit of margin (you might even get away with R6 if dense packed with cellulose), unless you're running a competent WUFI simulation on it just go with the ratios implied by the IRC, and pad it R1 or more.
If using reclaimed roofing polyiso it needs to be derated to R4.5-R5 inch due to temperature and age. So 2" would be enough (labeled R11.4, but R9-R10 when properly derated). In this stackup Type-II (1.5lbs per cubic foot density) or Type-VIII (1.25.lbs) can be UP-rated to R4.5- R4.7/inch at temperatures that matter from a dew point control perspective, which again takes 2" to have minimally adequate dew point control at sheathing layer. If using 1.5" foil faced 1lb density polyiso (labeled R9), it doesn't need to be derated IF it's strapped in place with furring, with a shiny foil facer next to the 3/4" cavity, which increases it's average performance by about R1.
If using XPS (don't use XPS- it's the worst thing for the planet), derate to R4.5-R4.7/inch, the same performance as EPS. Even though it's labeled R5/inch, that's only a temporary condition derived from it's HFC blowing agents. As the HFCs slowly diffuse out over a few decades (doing it's environmental damage) it's performance drops inexorably toward EPS of the same density.)
If you're in a high fire-risk zone you might consider using rigid rock wool instead. Since rigid rock wool is vapor permeable it doesn't really matter how thick it is- the sheathing will always be able to dry toward the exterior. From a thermal performance point of view 1.5" (R6) would get you close to current code-min performance, and 2" (R8) would usually take it all the way there if it's balloon framing (due to the smaller framing fraction than current standard 2x4 construction.)
@Dana
Thanks for weighing in. So if I do end up using either the zip-r or sheet foam + furring, do I need any other moisture barriers in my construction? Can I just add the sheet foam or zip-r directly over my shiplap and then my hardie board siding?
>" So if I do end up using either the zip-r or sheet foam + furring, do I need any other moisture barriers in my construction? Can I just add the sheet foam or zip-r directly over my shiplap and then my hardie board siding?"
As long as there is reasonable dew point margin you don't need any vapor barriers, but you DO need a weather resistant barrier (WRB) lapped correctly with your window flashing. ZIP-R has a fluid applied WRB on the exterior side of the assembly, but your existing window flashing would probably direct bulk water at the windows only out to the #15 felt or rosin paper or whatever is between the siding & ship-lap (?), which may or may not drain/dry correctly when a foam layer is applied over the siding.
If installing a WRB between the foam & structural sheathing it's generally better to use a crinkle type WRB (eg Tyvek Drain Wrap) to get at least some capillary break and drain space, but with ship-lap sheathing the air leakage can still be huge- #15 felt can't be detailed as a true air barrier. It's usually worth the up-charge using a fully adhered vapor permeable WRB such as Henry Blueskin VP100 or Vycor enV, etc. (stripping the #15 felt), even if dense-packing the wall cavities cellulose to achieve high air-retardency.
But whatever you use for WRB, make sure the window flashing extends out & over the WRB layer. Do a bit of archeology on the details on at least one window to see what you're dealing with. Many 100 year old houses have no window flashing whatsover, something that needs to be dealt with prior to blowing insulation in the stud bays adjacent to & under the windows. More than one house that age has been damaged by rain-soaked cellulose under unflashed windows. Empty stud bays can dry pretty rapidly, but wet insulation holds on to moisture much longer, and with a low-permeance foam on the exterior it's much MUCH longer.
Three considerations are air sealing, insluation, and moisture control.
Even though you are in a dry climate, the moisture inside the house is the source of moisture in the winter. One way to deal with that is with plenty of exterior foam, and R9 should be adequate. Another way to do it is to use vapor permeable exterior continuous insulation such as mineral wool boards. That has the advantage of being more fire proof if you are in a possible fire zone (who isn't these days?).
Mineral wool board isn't air tight--a "blueskin" self adhering membrane under the insulation could be a good way to to that.
My siding contractor tells me that even with r10 foam, moisture will condensate on backside of foam and walls will rot. This seems a little dramatic. I understand the concept but is there any evidence of a wall build like this (2x4 walls, r10 foam) failing ?
Sample of 1, but I recently opened up sections of a 30 year old wall with interior poly, 2x4 with batts, sheathing+R4 rigid finished with brick veneer on the outside. The wall was pristine, just as if it was built yesterday. This is in Zone 5, so not as cold your area.
Of course, you can take the same wall and install some badly detailed windows or siding and it will be a mess.
Generally if you get a well air sealed assembly (Dana's suggestion of a peel and stick is the way to go with old houses), flash your windows well, you'll have no issues.
Akos,
You have described my house exactly only it is 42 years on. One word of caution on this. As I understand it, 1 " of XPS does have some perm to it so some moisture movement to the cold side is possible, not the case with thicker foam and certainly not with foil face Polyiso. I am in Minneapolis and when I opened my walls I used the same word, pristine. Yours and Dana's advice to the poster of a peel and stick and then adequate outsulation sounds like a working formula to me. This essentially what Harold Orr did in Saskatchewan. Existing 2x4 walls covered with 6 mil polyethylene, then a Larsen Truss type outer wall. They excavated on the outside of the foundation wall and continued the superinsulation here too.
See my last post on Cold Climate Air Sealing. Our neighbors to the north (Canada) have covered homes like yours in detail. There will be some information available to you if you do a search.
For recycled foam call industrial roofers doing large flat roofs. They usually have stockpiles that they need to get rid of. Around here in WI I get new looking (15-20 year old) EPS for 14cents a square foot or better. Usually $4 for a 4x8'.
I think 2" of rigid rockwool comfortboard 80 is a better way to go than foam.
Two words: Vapor Permeable!
It's also greener and cost less vs XPS.
From a dollars and cents point of view as long as the current siding is still keeping the water out this update is very very unlikely to save enough money to pay for itself.
The pay back when upgrading the current R13 wall will be very long and the cost of residing will be very high.
Even from a carbon point of view this upgrade is unlikely to ever save more carbon that was expended making, transporting and installing the new insulation and siding.
I never spent a winter in Montana but maybe this upgrade is worthwhile from a comfort point of view.
Walta
I am in the midst of just such a process. I am adding 3” Type 9 EPS to FG blown 2x4walls with board sheathing. The WRB will be on the outside held in place by the furring strips for plank siding installation. With more than 50% of the thermal resistance on the outside my sheathing stays plenty warm. The unfaced EPS is semi-permeable at 1 to 3 perm depending on which story I read. Zip R does not offer a built in rain screen like furring does. I am also installing new windows, probably an in-between position. No nail flanges.
I’m estimating $15k for materials which includes basement floor and wall insulation, subfloor and wall board. Walter is correct that energy cost savings in and of themselves have a long payback (especially if professional labor is involved) . However, for many of us, the siding is tired and another coat paint is just life support. And double hung wood windows can only achieve so much. Payback assessment needs to include increased value of your home, greater comfort, ease of maintenance, ease of use.
If we recognize the real cost of our energy, not just the dollars we pay, but the environmental cost, the ROI is much higher and more satisfying.
I’ve heard a story that an energy refit can add 15% to the value of a home. We’ll be able to report on that in the near future. It can’t be a simple 15% . But that’s a rabbit hole for another day.
“I’ve heard a story that an energy refit can add 15% to the value of a home. We’ll be able to report on that in the near future. It can’t be a simple 15%”
I wish this was true but from my experiences in real estate the only things that matter are location square feet and visual appeal. Insulation that is hidden in the wall can’t be seen and add no value.
Walta