WRB and wall assembly in a historic home

GBA,
I’m looking for some assistance / recommendations on wall assembly in an old farmhouse. First priority is maintaining the integrity and longevity of the house, second priority is making the building as efficient and comfortable as possible.
I moved into an old balloon framed italianate farmhouse in Western NY, climate zone 5, about 4 years ago. We’ve been slowly renovating the house. In the next few years we will be tackling the exterior of the home. House is two stories with basement (field stone foundation) and attic, approximately 3500 square feet, new high efficiency boiler w/radiator heat and no house a/c. Currently the walls consist of likely asbestos / cement siding, original clapboards (4″ reveal 0.5″ thick at the bottom), shiplap sheathing (9.5″ wide), true 2×4 balloon framing, and blown in cellulose insulation. Some, but not all, of the walls are being opened up, insulation replaced by mineral wool batts and fireblocking installed. We’ve worked on the bulk water management and the basement stays fairly dry, humidity gets to 50 or 55% at worst in the summer. Likely going to install a whole house dehumdifier in the basement. House has nice big overhangs on the walls.
Plan for the exterior of the home is to remove the asbestos siding, if the clapboards are in bad shape remove them, replace and rehang. While I have the siding removed I was looking at making any improvements to the wall assembly. My highest priority is to not cause any direct harm to the structure (by tightening up an envelope that has maintained the structure for 140 years by being leaky). Secondary priority is to make the building more comfortable and energy efficient. To maintain the historic details of the home I’m not planning on adding any exterior insulation. Removing the shiplap sheathing and replacing with a modern sheathing could be a possibility but I’m not sure the cost would ever be recouped by the efficiency improvements. Something I was thinking about was adding a WRB. If I’m going to do this it made sense to me to add something with higher perms such as tyvek housewrap (water vapor management is not perfect in the older home and if the water vapor is there than best to let it escape).
To my questions: any specific WRB recommendations for an older home as outlined above? Higher perms or lower perms? Particular products? Any other wall assembly details you’d recommend?
Thanks for the assistance.
Andrew
GBA Detail Library
A collection of one thousand construction details organized by climate and house part
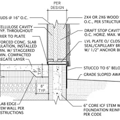
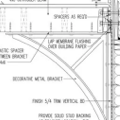
Replies
I had a very similar situation with our 110 yr old structure in Eastern MA. Do no harm meaning allow drying to the exterior. Air barrier solution to our gapped board sheathing was self adhered Blueskin which struck a nice price / perm balance. Outboard of that we did a 1/4" air gap (vented at bottom) and then cedar clapboard siding. Inboard of the sheathing we did dense pack mineral wool, Membrain, and skim coat plaster with latex paint. The pic shows the gapped sheathing, the WRB, and the 1/4 ply strips used to provide the air gap for the clapboards.
I wouldn’t bother replacing the shiplap sheathing with a new plywood layer.
I’d use either VP 100 (as mentioned above) or Siga Majvest SA. I’d lean toward blown in cellulose or blown in mineral wool for the cavity insulation. If you’re opening the interior walls, it’s worth installing a smart vapor barrier like Siga Majrex or Intello.