Zone 3-Finishing /Insulating an Unfinished Bonus Room

Hello , I am in the planning phases of insulating and finishing an upstairs (above-garage) bonus room (Zone 3- Gwinnett, GA) for an existing home and I am trying to validate my approach in terms of insulation needs and requirements. My goal is to convert this space into an official bedroom. However, I am running into a few gray areas (as far as understanding compliance) and some guidance would be greatly appreciated so that I can plan my materials accordingly and ensure I am on the right track when it comes to passing inspections (when it gets to that point) as will be homeowner as contractor and will be doing the work myself
(Ventilated Attic/Bonus Room)
While the bulk of the ceiling space is ventilated (at both the soffit and ridge vents 24 o.c) as shown in the picture, there are approximately 5 bays (16 o.c) that do not extend to a soffit (in a valley) but are ridge vented. I do not want to go the spray foam route for a few reasons and am trying to be as cost-effective as possible with this project.
Moreover, to save headroom space I also want to minimize the amount of furring that will need to be done on the rafters. Here is my plan…As I understand (but am looking for validation here) minimum code for the cathedralized-vented ceiling (with trade-offs) per Table R402.1.6 (2015 IECC) indicates a minimum of R-20.
My plan is this: Furring the rafters approx 2″, installing a.) foam baffles from soffit to ridge, b.) R21 fg batts-unfaced, and then c.) seal/encapsulate the rafter cavity from bottom to top with .5″ Rmax Matt Plus 3-Polyiso (either in between the rafters or on top of rafters-one or other.) I already purchased the rigid sheets years ago so want to utilize the sunk cost of the rigid foam.
The R-value on the polyiso is 3.2… so this combo (w. FG batts) and factoring some minor compression of the fg of .5-1″ would get me close to R-value of say R-22 (give or take).
Does this seem like a feasible approach that will pass code, permitted that I will be making some trade-offs and using Rescheck to ensure compliance (beefing up R-value in front facing wall and/or knee walls/flat ceiling portion)? For as I gather, Rescheck will be required if using trade-offs and for permit/inspection purposes but am admittingly not entirely sure what is required there- considering this is an existing home.
Next, I need to determine how to best treat the (5) rafter bays at valley that only have a ridge vent and no soffit intake. My thought is that this portion of the roofline would be considered vaulted/unvented per table R402.1.6 (despite having a ridge vent with no intake vents). My thought here is to seal the ridge vent on this portion of the roof and apply 2-layers of the .5″ polyiso sheets on hand, directly against the underside of sheathing, and than unfaced R21 on top of that (which seems to be the recommended approach per code). However, the presence of the ridge vent throws a wrench in my thought process in terms of the best way to handle it. Should I just seal it off considering there is no intake? I would prefer to not go through trouble of adding eyebrow vents etc as is a pretty small portion of the space overall.
I also need to consider if an ignition barrier is needed for the polyiso in the rafter areas behind the knee wall, and above the flat portion of the ceiling. While Rmaxx seems to have a good fire rating, it is my understanding that there may possibly need to be an ignition barrier but not 100% certain. In that, 1/2 inch sheetrock will be going directly on top of the rigid for exposed portion of the ceiling but will still leave the polyiso exposed on the rafters behind the knee wall and above the small “flat” portion of the ceiling. Therefore, since sheetrock will be covering majority of the rafter space, I wasn’t sure if the areas where the rigid is exposed needs to be covered as an ignition barrier.
Then, considering the entire rafter bays will be encapsulated and sealed, would’nt this mean that the small flat portion of the “ceiling” would technically be considered an interior wall (only requiring a minimum of R-13)? The same goes for the knee wall… for under table R402.1.6, there appears to be an exception noted that when the building roofline is insulated, a knee wall is classified as an interior wall which is confusing.
In any event, planning is everything, and in terms of scoping out materials and the costs associated, I want to make sure I plan this right the first time around, and as far as ensuring my approach regarding code compliance any assistance/guidance would be greatly appreciated.
In addition, there seems to be mention in code about the requirement for a mandatory compliance certificate with regards to energy code, but this is an existing home so not entirely sure if this piece will be needed or not. Especially concerning considering that somewhere along the way the attic insulation card that came when the home was built got tossed along the way so have no idea how many bags of blown-in were used in the house, who applied it, etc. but that’s a different issue all together
Thanks in advance!
GBA Detail Library
A collection of one thousand construction details organized by climate and house part
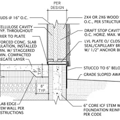
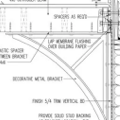
Replies