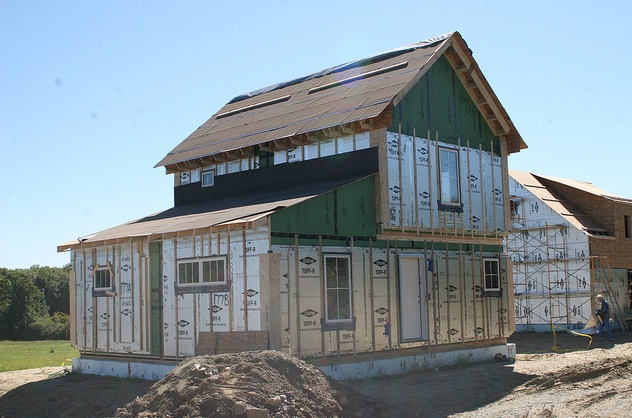
Image Credit: Katie Palmer
So far, Sullivan County Habitat for Humanity, based in Harris, New York, has completed two homes for families in the county, which is about 75 miles northwest of New York City and known to many people as a Catskills vacation destination.
But this Habitat affiliate’s third project, now in the planning stages, could become one of the region’s affordable-housing landmarks if it meets the expectations of its design-and-construction team and a joins Habitat’s emerging portfolio of homes built to the Passivhaus standard. As noted in a recent edition of The River Reporter, the affiliate’s president, Pat Pomeroy, has been collaborating with architects Michael Chojnicki and Buck Moorhead; project coordinator Stephen Stuart, who owns a construction firm called Sustainable Solutions; and construction manager Bert Echt, whose building company is called Evergreen Design. The River Reporter story portrays this group as devotees of green building — a portrayal confirmed by GBA’s conversation with Stuart.
Crafting design and materials strategies
As currently envisioned, the house would include 1,230 sq. ft. of conditioned space, four bedrooms, and two baths. It will be built on a half-acre lot in South Fallsburg, near the eastern border of Sullivan County.
Stuart told GBA that Passivhaus modeling still has to be done to determine what R-values will be needed for the exterior walls and roof, although preliminary plans call for about 9 in. of extruded foam insulation under the slab, for a thermal resistance of about R-45.
The development team is leaning toward using 2×4 advanced framing for the exterior walls, with studs spaced 24 in. on center, and dense-packed cellulose insulation. The siding would be fiber-cement or stucco, Stuart said. “We’ll see how [a stucco exterior] fits in in the neighborhood,” he added.
A budget target has yet to be set, although Stuart pointed out that, in addition to benefiting from Habitat’s volunteer labor force, this project will save money in part through its use of recycled material (including the foam that will go under the slab) and through the building’s two-story design, which will reduce the size of two cost-intensive components: the slab and the roof. The windows for this house likely will be Pella argon-filled double-pane units with fiberglass frames and sashes.
If planning progresses as hoped, Stuart said, the project should break ground in June. By September, it should be far enough along for Stuart to bring students in Sullivan County Community College’s green-building program out to the site for a tour – and maybe a little volunteer labor.
Weekly Newsletter
Get building science and energy efficiency advice, plus special offers, in your inbox.
0 Comments
Log in or create an account to post a comment.
Sign up Log in