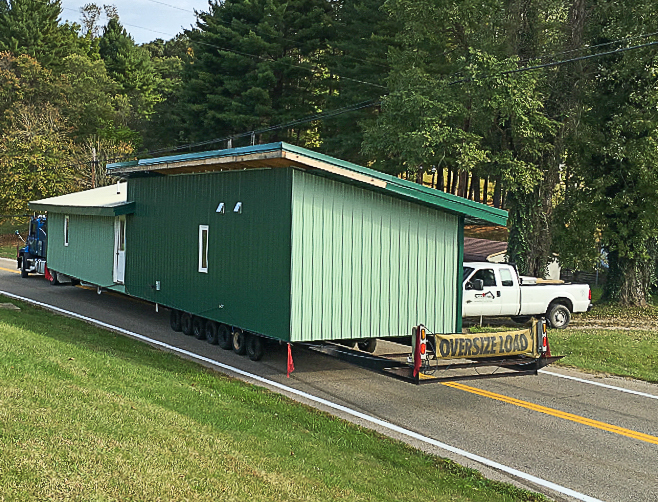
Jason Morosko is the lead engineer for UltimateAir, a manufacturer of whole-house ventilation equipment, and the only Certified Passive House Consultant in Athens, Ohio. Morosko built a Passive House duplex for his own family a few years ago, regularly consults with builders, and rarely skips the annual conferences of the Passive House Institute U.S.
In short, the 39-year-old Morosko is completely invested in high-performance building, even when it comes to the handful of rental properties he owns with his brother Jeremy, 43, in the not-so-highfalutin southeast corner of Ohio.
The two of them late last year completed their first superinsulated modular, what they’re calling a “Modular Passive House,” for well under $100 a square foot. They hope the modest building can become an example of what can be done on a shoestring budget for families who want comfortable, energy-efficient accommodations but can’t afford steep rents.
“From a business standpoint for rental units, the math is terrible,” he said in a recent telephone interview. “But, on the flip side I hate seeing a poor family living so uncomfortably in a terrible single-wide mobile home.”
Taking over a family-owned business
Athens is a city of 24,000 close to the West Virginia border, an area Morosko describes as “economically deprived” where paychecks often fall below national averages. The Morosko brothers, both of whom work as engineers, got into the rental business through their parents. Although not by any means wealthy, the elder Moroskos had over time accumulated 10 or so rental properties.
When their parents wanted to retire, their sons bought them out, providing the nest egg their parents had never been able to set aside. The rentals included a mix of properties, but it was the manufactured housing that Jason Morosko especially loathed.
“With my history of Passive House and building science and the building industry, oh my gosh, I despise a mobile home for everything it stands for,” he said. “It’s a damned piece of Swiss cheese you’re trying to heat and cool.”
The brothers, doing business as Sustainable Path, owned one mobile home that was ready to fall apart. They originally planned to renovate it, but then decided to replace it with a more efficient, better insulated building of roughly the same size, about 850 square feet.
Their first step was to visit a local modular home manufacturer to buy a standard 13-6 by 70-foot steel frame on wheels. The seven-axle trailer had been used to deliver modular homes. Once a crane lifted the modular unit off the frame and placed it on a permanent foundation, Morosko said, the trailer was no longer needed. The modular builder had 30 spent trailers lying around and was happy to sell one of them.
Soon afterward, Sustainable Path started work on the first, and so far only, of its modulars. Morosko described the building as a wood-framed structure whose 2×6 exterior walls were insulated with cellulose in the stud cavities and an additional 4 inches of polyiso rigid foam on the exterior. The 2×10 shed roof, as well as the floor, were insulated with a mix of polyiso and cellulose. In all, the specs sound something like a “Pretty Good” house and a lot more attractive than a built-to-code house: R-40 in the walls, R-50 in the roof, and something like R-40 in the floor. Windows are triple-paned, and the all-electric house came whole-house ventilation system using an UltimateAir ERV.
A blower door test for airtightness has not been done.
Good, but not Passive House and not upscale
It took a crew of one or two carpenters about seven months to build the house in a local parking lot. When it was finished, the Moroskos swapped it for the dilapidated mobile home, with the tenants temporarily storing their belongings in a container on the site. What the tenants got was a snug, two-bedroom, two-bath house that is heated and cooled with a single 9,000 Btu/h ductless minisplit head even in sub-freezing weather.
The Sustainable Path website claims that power bills will average $65 a month.
What the new tenants didn’t get was much in the way of expensive interior or exterior finishes. Exterior walls are clad in sheet steel. Interior walls are 1/4-inch thick lauan mahogany plywood, the seams between sheets covered with strapping. Flooring is vinyl plank. The house still sits on its original steel frame, and although the wheels and axles have been removed it is the steel frame that supports the building, not the concrete block skirting that has been built to disguise it.
That last detail has been something of an issue, not only with Morosko’s insurance company but with county assessors. Buildings permanently attached to trailers are defined as manufactured housing; those trucked to the site on a trailer but then placed on a conventional foundation are modulars. The distinction, Morosko said, has made financing and the appraisal “a little hairy.”
Morosko convinced insurers the building is a house, not manufactured housing, but his fate with appraisers is still up in the air. Their decision could have long-term consequences for the project.
“A mobile home depreciates in value,” Morosko said. “A piece of real estate appreciates.”
Adding it up: Best business move?
This property is rented with utilities included, and that could turn out to be a good deal for tenants. For example, the old manufactured home rented for $500 a month, with tenants picking up the cost of hot water, heat, and electricity for another $200 or so, depending on the season. Once moved into the new house, tenants will pay a flat $725 a month for everything, a predictable monthly expense for a much more comfortable dwelling.
The rent was enough to cover the owners’ costs. But as purely a profit-and-loss question, building the modular may not have been their best move.
“Did I succeed? From a landlord-economic-rental standpoint, it was stupid,” Morosko said. “My personal drive is I hate the thought of trailers. They’re a complete energy waste. A landlord loves them because they’re cheap, they rent for almost what you’d be able to rent a house out for, and they cost the tenant. They uncomfortable, and they leak and fail all over the place.”
He also recognizes he’s invested $80,000 in 850 square feet when he could have spent $15,000 on a new manufactured home and rented it for practically the same amount of money. Whether he and his brother recoup that money over time because the house is worth more than a conventional manufactured house remains to be seen.
But in general, Morosko isn’t especially upbeat about the prospects for high-performance modular housing.
“I have visited four modular factories that have tried to make a go of it, building some kind of net-zero or Passive House modular, and I have not seen any of them wildly succeed,” he said. “Selling a Passive House modular has not been a succeeding business model — yet.
“Why?” he continued. “Energy costs in the United States are still way too low, and there’s no incentive, and unfortunately I feel there’s going to be even less over the next four to eight years. “
No push to certify
An obvious question is whether certification from either PHIUS or Germany’s Passivhaus Institut would make any difference on the company’s balance sheet. Morosko doesn’t think so.
“Why did I not certify it? I’m a Certified Passive House Consultant,” he said. “I drank the Kool-Aid. I’ve lived it for more than a decade now. Shame on me. The realistic part of it is (a) it didn’t quite meet the metric and I couldn’t convince myself to put more R-value and more cost into it, and (b) my appraisal is not going to be any higher if that place uses $300 a month in utilities or $80.”
Nor would Passive House certification necessarily help him rent the house.
Certified or not, the house should be comfortable and easy to heat and cool. But the story of the tenants who went from a falling-down manufactured home to a plain-Jane superinsulated one has an odd ending.
The older couple loved the place at first, Morosko said. But Morosko’s decision to make bedrooms a little bigger than those in a typical manufactured home, thereby reducing space in the main living area, proved to be a deal-breaker.
“The tenants I had in the trailer for the last eight years were all psyched to get their new one,” he said. “They even camped for three weeks while we swapped them out. They moved in. They loved it. They loved the fact there was no heat stratification. It was warm all the time. But they couldn’t get their furniture situated. It is as simple as that, and I beat my head against the wall. They moved out. They moved out because the woman could not get her furniture situated. It was a completely different layout than the trailer they had.”
Three other potential renters are looking at the property. “We will have it rented within the next week or two,” he said.
Weekly Newsletter
Get building science and energy efficiency advice, plus special offers, in your inbox.
6 Comments
floor details
I commend the owners for spending the extra money to build this rental unit. What is the stack-up that was used in the floor? Did the polyiso go on top or below the floor joists?
Keep doing the right thing
You are doing the right thing by bringing a quality product at a reasonable price. As a landlord I understand its complex. A couple things that I've learned:
1.) Size the bedrooms small as you found out. This is top on my next units. My earlier ones where too big as well.
2.) Air sealing and adding attic cellulose r-value is more important than expensive wall insulation and HVAC solutions
3.) Always have tenants pay for utilities (outside of effeciency units). Tenant behavior trumps all.
4.) Use electric. Tenants living skills are questionable at best sometimes.
5.) If something breaks, then the landlord didn't make it well enough. This goes to qaulity of product issues.
6.) Washer/Dryer/dishwasher with master bathrooms include. Higher rental return.
floor
The floor from bottom up- treated half inch plywood (finished skin on bottom) PLASTIC (air seal) then 2x8 floor joist full of cellulose. 5/8 tongue and groove plywood. 2" polyiso... then commercial vinyl plank. And i might reverse the plywood/polyiso on the next one
A+ for efffort
Tremendously impressive effort.
Hopefully you can find like minded people in the area. Would be great to have a few developers pooling resources and helping promote the idea of simple efficiency.
They said it could not be done!
Bravo! You did the impossible-A Pretty Good House for $100 sf! Looks like you found a lot of ways to cut costs, yet this should last a lot longer than a mobile or modular. Was it about 1000 hours of skilled labor? Would 2" wall foam provide a significant cost savings? Could you satisfy the appraisal by dropping onto a pier foundation?
could not be done
1200-1400 hours i think... we did 4" exterior polyiso... it was the best cost per Rvalue in rigid insulation... that i found. Once you get rid of the thermal bridge- just use cellulose.... Appraiser wants to see it anchored to a permanent foundation. Not sure piers will do it.
Log in or create an account to post a comment.
Sign up Log in