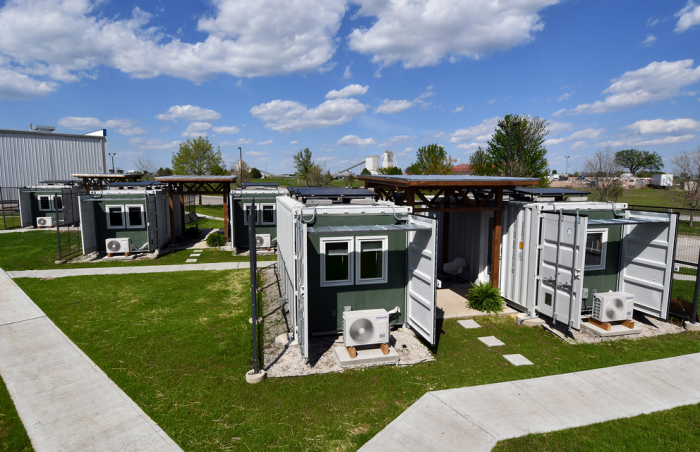
This article originally appeared in the United States Green Building publication, USGBC+ magazine. Photos courtesy of Studio 804.
It was a confluence of factors that led to the retrofitting of 12 shipping containers to serve as private housing for people experiencing homelessness during a pandemic. Located at the Lawrence Community Shelter, 45 minutes from Kansas City, Missouri, Monarch Village is a response to the need for quarantining. When COVID-19 hit, the shelter’s congregate housing (a large warehouse filled with bunk beds) made isolating impossible, which compounded the health safety risks to the already-vulnerable population.
Meanwhile, Dan Rockhill was looking for his next student project. Rockhill runs the nonprofit Studio 804, a hands-on design-build program offered through the University of Kansas School of Architecture and Design that runs for nine months. Each year, a cohort of Studio 804 graduate students designs and builds a LEED Platinum project; Monarch Village is the studio’s sixteenth.
The 2020 project was unique in several ways. First, one of its key objectives was to provide a safe space for people with COVID-19 infections to isolate. Second, it was a series of buildings rather than just one, which is typical for the program. Additionally, it involved donations from a long list of product manufacturers [including 475 High Performance Building Supply, Pella Windows, Benjamin Obdyke, and Simpson Strong-Tie]. Finally, it was a “feel-good project”—one, it is hoped, that will be a precedent supporting the movement away from housing the homeless in gymnasium-like facilities. The outfitted shipping containers provide much-needed privacy for families in crisis, while allowing them access to critical services at the shelter. Post pandemic, the housing units will be an important addition to those services.
Tiny homes for families
“Dan came to us with such a completely pure heart,” explains Meghan Bahn, the shelter’s director of community engagement. “He really wanted to help, and our main issue was the fact that when you are isolating, you need to have your own kitchen and bathroom.” That’s when they hit on the notion of tiny homes. “The nice thing about that idea was even if the pandemic was resolved quickly and isolation was no longer necessary, we still have a need for facilities to accommodate families with children.”
“The folks at the shelter were in tears when I said I would donate a dozen units that would provide relief from the virus as well as the generally chaotic environment of the shelter,” Rockhill recalls, noting that pandemic-related dealays made getting construction underway difficult. He began applying for a special use building permit in March 2020, long before his students were able to be involved (typically they are part of the process from the start). The permit didn’t come through until November.
The original intent was for the units to be residential but local code required they be commercial, which meant meeting regulations related to fire protection. This added to the complexities inherent in converting containers into safe and healthy housing. Construction on the units began in August in Studio 804’s warehouse, they were moved to the prepared site in March, and by graduation in May of this year the project was complete. The total cost was just under $500,000—roughly $40,000 per container.
The 12 units are grouped into six pairings to accommodate shared patios and protected entries. They sit to the southeast of the main shelter and adjacent to a 900-sq.-ft., open-sided commons area just north of the community vegetable garden. Each 135-sq.-ft. container includes accommodations for four with two separate sleeping areas—a bunk bed in one and a pull-out sleeper couch in the other—plus a full bathroom, and a kitchenette. One unit is ADA-compliant.
Operable windows at each end of the unit allow for natural cross ventilation, and greenscreens on the south-facing side support native vines intended to shade the containers and cool the steel surfaces, while also lessening the mechanical cooling loads. The interior spaces are conditioned using heat pump technology with ductless mini splits, and Lunos e2 ventilation fans bring in fresh outdoor air and exhaust stale indoor air.
Three 320-watt solar panels mounted on each roof provide clean supplemental energy, and all units have sprinkler systems. The containers are elevated 6 in. off the ground and bolted to concrete foundation piers; they were designed to be moved, if needed. In the same vein, the electric and water hookups are at the outer walls and can be readily disconnected.
A student-built success
Rockhill says the project was a challenge every step of the way. In addition to the pandemic-related complications, there were innumerable on-the-spot innovations needed to solve for the complexities involved in converting steel containers into housing units, since each one was slightly different in dimensions. Cutting openings for the windows and doors, for example, required working with the corrugation of the steel. It had to be done such that the walls would be supported by 2×2 steel studs, meaning the windows needed to be installed to the outermost of the corrugation, which was something of an engineering feat.
With the exceptions of the plumbing and HVAC installations, the work was performed by students. “The detailing of the project was in their hands, with my guidance,” Rockhill explains. “Many students have never worked at that level, which is why they sign up for Studio 804. They get an immersive experience. They learn how much more there is to architecture than what you see from the outside.”
Kelsie Hancock was one of the students on this project. She speaks to the educational value of the experience and of the prestige of Studio 804 but homes in on the humanitarian effort that drove the work. “On top of all that I learned design and building-wise, it was an opportunity to give back to a community that had given me so much when I was a college student. I had been involved with the downtown area and knew the situation with the homeless population and what they were facing with COVID. Seeing that and knowing we were doing something that was going to make an impact on that situation meant a lot.”
She also appreciates knowing what goes into designing, constructing, and certifying a LEED Platinum building. As a young architect, she brings to the table an understanding of the level of planning and precision of execution required when building a high-performance structure.
Hancock led the LEED certification process (it was submitted as a “bulk single-family home” project), helmed all efforts related to detailing the building envelope, oversaw the site work involving concrete pours, and aided in the fabrication of bunk beds and sofas with a trundle rollout.
She describes the difficulty of detailing the constricted space to meet code for thermal insulation as a lesson-rich construction challenge. Meeting the indoor air quality requirement for LEED was another. To maintain structural integrity, it was important to limit the number of penetrations made in the containers, so mechanical ventilation (over more windows) was key to a healthy indoor environment, which the high-efficiency Lunos e2 heat-recovery system provides. Two fans were installed on the end-cap wall by the open steel doors; this negated the need to cut additional holes into the steel walls. Keeping all plumbing within the thermal envelope to prevent it from freezing was another problem to solve. By adding a step up into the bathroom, the team was able to get a sweep under the toilet and fit the plumbing beneath the units with pipes running up the insulated outer walls.
Beyond pandemic safety
Bahn makes a point that is often overlooked when it comes to facilities for the homeless, saying, “I hope for more projects that recognize how aesthetics can affect people’s moods and how privacy is something everybody needs.” She explains the shipping container housing units at Monarch Village are far less traumatizing for people than staying at conventional shelters, attributing this to the fact that the converted containers were designed to be pleasant to be in. “People have said they appreciate the beauty of the interiors,” says Bahn. “When they see them and realize that is where they are going to be staying, they are very excited. You can see on their faces a feeling of pride in being able to stay there.”
The containers have proven their value. At one point, all 12 were occupied and used as safe spaces when it was discovered a shelter guest had tested positive for COVID. The units were filled with people who had been exposed. The fact that four people can comfortably occupy each unit is a powerful testament to the design’s integrity and the construction’s execution.
The last of the required building permits were recently approved for 10 more units, construction for which is set to begin within the year. “This project was extremely well received by the community,” Rockhill notes. “The knee-jerk response at the beginning was, ‘Containers—how can that be dignified?’ I think with Monarch Village we have demonstrated they can be.”
__________________________________________________________________________
Kiley Jacques is senior editor at Green Building Advisor. She can be reached at [email protected].
Weekly Newsletter
Get building science and energy efficiency advice, plus special offers, in your inbox.
0 Comments
Log in or create an account to post a comment.
Sign up Log in