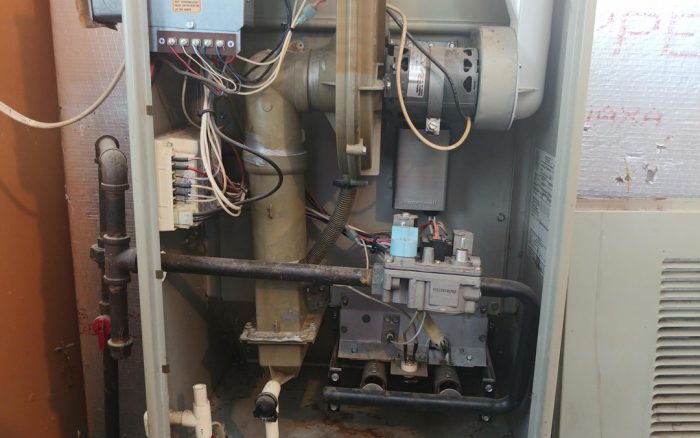
Andrew Bennett is giving his 1991 home in eastern Tennessee an efficiency upgrade, as time and budget permits. He has a long list of improvements he’d like to make—new windows, sealing and insulating the crawlspace, more air sealing around the house—but he’s also realistic enough to see it will not happen overnight. “As most normal people,” he says in a recent Q&A post, “I’m on a budget and it will take time.”
For now, he’s focused on the best way to replace an old gas water heater and his HVAC system. The 1900-square-foot house is currently served by a single-zone, 3.5-ton HVAC system with a gas furnace. Bennett has found a contractor who’s made some recommendations for new equipment.
“It took a while to find someone who actually knows how to size things and they are looking at a 2-ton unit with a variable speed blower,” Bennett writes. Plans call for a second thermostat upstairs, but budget constraints are forcing Bennett to reuse existing ducts even if they aren’t suited to the smaller HVAC system.
“My question on HVAC is should I go all electric or stay with gas heat?” Bennett asks. “I don’t have solar and have no plans or budget for going solar for electricity generation.”
Second, Bennett wonders what to do about his gas-fired water heater. Although it still gets water hot, it also “intermittently spews out a black, oily residue.” Should he simply replace it with another gas water heater? He’s not convinced that heat-pump water heaters will last 10 or more years without significant repairs along the way, and he’s leery of tankless heaters for the same reason.
That’s where this Q&A Spotlight get started.
Suggestions for a heat pump
David…
Weekly Newsletter
Get building science and energy efficiency advice, plus special offers, in your inbox.
This article is only available to GBA Prime Members
Sign up for a free trial and get instant access to this article as well as GBA’s complete library of premium articles and construction details.
Start Free TrialAlready a member? Log in
21 Comments
That COP explanation is overly simplistic. COP compared to combustion efficiency isn't really relevant. You are comparing a physical heat gathering process (HP), to a chemical combustion process. IMHO, COP isn't the way to do this.
$1 worth of heat from electricity resistance, is a way different BTU number than $1 worth of heat from natural gas. You may get 4x the heat for $1 of gas, versus electric resistance.
Which means a COP of 3-4 is probably where you start to break even with gas depending on rates.
This is totally dependent on utility prices but in my experience, you need a heat pump COP between 3 and 4 to have approximately the same heat per dollar as a decent NG furnace.. It used to be closer to 3, but is creeping towards 4 as electricity prices are climbing faster than NG.
Personally regardless of rates I'm on a road to electrification. As you tighten and insulate a house more you become less sensitive to utility prices since you consumption is a lot lower overall. So it doesn't really matter if you theoretically pay a little more to heat with a heat pump than NG.
If rates really skyrocket that will incentivize self production (solar) and storage (batteries).
Around $25/month just to have a gas meter adds up too, $300 a year on you gas bill for zero btu's. That can offset some of the difference.
"A big key to energy efficiency is deep nighttime setback"
Not true, but would be interesting to see Dan's numbers anyway.
"Dan saw no real reason to connect the domestic water heating replacement issue with the HVAC system. "
One good reason is so that you don't have an orphaned water heater. This happens when the furnace is removed from a chimney/vent system and the water heater is left behind. The chimney/vent can easily be too large for the water heater, resulting in backdrafting (safety hazard) and condensation inside a masonry chimney (destroys the chimney). You're really supposed to reline/resize a chimney when changing the appliances. If you apply the cost of relining towards a new HPWH, the HPWH starts to look a lot more attractive.
In a non-orphaned case, why doesn't the safety hazard occur all Summer? Or during those frequent Winter periods when the furnace isn't running but the water heater is?
I only skimmed the GAMA venting rules, but it looks like a lined masonry flue can be 7x oversized, so up to 8x8" nominal is OK for a water heater with a 3" vent. Evidently an orphaned water heater isn't always a problem.
Not sure about your math. The area of a 3" round vent collar is 7 sq.in. The area of an 8x8 masonry vent is 64 sq.in., therefore, 9x the vent collar area. Not OK. Most 40 gallon water heaters have 3" vent collars, and few masonry chimney liners are smaller than 8x8, so this is a common issue. Also, the I-code series has removed masonry chimneys as allowable venting systems for single naturally-drafted appliances. Only B-vent is now allowed for venting single appliances, or listed relining systems installed in a masonry chimney.
In winter, masonry chimneys are heated by air escaping from the house and from the periodic firing of the furnace. Few masonry chimneys will completely cool off between furnace firings - at least in the past. With tighter houses and more efficient furnaces, that's changing and venting even combined appliances can get dicey. You're right that, in the summer, the furnace doesn't run at all. But the chimney is warmer in the summer, so less risk of internal condensation. More risk of backdrafting, though, since the temperature difference between the exhaust and outdoor air is lower. Just more reasons to move away from naturally-drafted water heaters.
> Not sure about your math.
The math works when you use the interior dimension, which GAMA lists as 6 3/4 x 6 3/4".
By George, you're right. Just below 7x. Not great, but not bad. Still doesn't help with the prohibition on masonry flues for single appliances though. What edition of the GAMA tables are you looking at? I'm only able to find editions from the early 1990's in my quick search.
I was looking at this one, which is old. I have no idea what rules/code one needs to follow if they are simply removing some equipment.
https://www.questargas.com/ForEmployees/qgcOperationsTraining/Misc/gama_venting.pdf
> I-code series has removed masonry chimneys as allowable venting systems for single naturally-drafted appliances
I'm interested in a link to that if you have one. IMC 801.18 sees to permit continuing use in the case of a removed furnace or water heater.
>In a non-orphaned case, why doesn't the safety hazard occur all Summer?
Because the average temperature of the idling flue is already a lot warmer in summer even without the additional BTU inputs of the space heating appliances, with a greater amount of natural stack draw.
The warmer average summertime flue temps is also why flue condensation risk from the water heater exhaust are lower when there is little or no space heating load, even though the heating appliances running at a very low (or zero) duty cycle.
Drafts are stronger in Winter, when the delta-T is greater. As Peter said in #5 above.
Your second paragraph makes sense.
In winter the flue (especially on an exterior chimney) is full of cold dense air that will be sinking unless/until an burner is putting hot exhaust into it.
It's worth mentioning that the GAMA rules I was lookin at only apply to interior flues. Which in my experience, rise in the Winter.
[deleted double-post]
This is the home owner. I wanted to give an update. I still don't have the system replaced yet. My usual HVAC contractor simply refuses to put in a 2 ton unit. I decided to pay for an independent manual J and used rescheck.info. It turns out the guy who does the calcs is right here in East TN as well as has a house about the same size as mine...and has a 2 ton unit and he says it's fine.
So he did the manual J. We fudged some numbers as I'm planning on more insulation, windows, etc long term. His calcs came out with a 2 ton system as well. Based on the comments of Akos on the original post I decided to have the Carrier guy come out and give me a price on a Greenspeed unit.
He took a look at the Manual J and said it all looked pretty good except for the indoor and outdoor temps he used at 75 degrees inside and 90 outside. He knew off the top of his head how many cooling days we had the last two years that were well over 90 and wondered if the 75 degree indoor temp was really what would keep me comfortable (and I do like to sleep in a cold house).
So...I emailed rescheck.info back and asked him to raise the outdoor temp to 95 and drop the indoor to 70. That was enough to bump things to 2.5 tons. As you know 2.5 ton systems are only available in single speeds. If I want a multi speed system I'd have to go to 3 tons. The Carrier guy also says that the Greenspeed system won't work with my ducts. He says there's some sort of sensor that checks the static pressure and mine would be (I really don't remember if it was too high or too low, but it wouldn't be right) off and the system just wouldn't run right.
I think he gave me some good insight on the furnace part of the deal. If I am running a heat pump the furnace just isn't going to be on much at all so having a modulating, multi-speed system might not make a lot of sense from a cost perspective based on how little it would run.
As far as the heat pump portion of it I could go with a 2.5 ton single speed system where the ductwork would need a bypass or a 3 ton multi-speed (I don't remember if it would need a bypass or not to keep the duct pressure in the right range...remember currently I have a single zone for the whole house, but am planning on putting in another thermostat and dampers to have 2 zones).
The 3 ton would have a nice dehumidification feature that the 2.5 ton would not...but it would add about significantly to the price for the multi-speed unit.
This is making me want to pull my hair out. I wish I had the money to do all the energy upgrades I want up front and maybe get the manual J back down to 2 tons, but I just don't have the budget.
To address Peter Yost's comments about why I'm doing the HVAC first before working on the building enclosure...we've lived in the house for 5 years. The condenser has gone out every single year and both I and my wife are sick of that. So the replacement has to come first.
Any additional input is gladly appreciated. Thank you all. Andrew
(Dan Cautley) "So long as the new HVAC system is multi-stage or modulating, that takes a lot of pressure off the needed level of accuracy for the load calculations and sizing."
More than one HVAC installer has pushed back at me when I have suggested this. "Call me when you finish air sealing and windows" is a familliar refrain.
I can't really blame them since they are the ones on the hook for warranty service. Even if I finish air sealing floors and ceilings first and then do HVAC, as planned, I would hope to do windows gradually. I still hold out hope that modulation will give the house both comfort and room to improve. Any opinions on how to proceed?
Just as I favor the idea of having an independent professional Manual J, I thought of using an independent designer. But not sure how the designer would get along with the contractor. If anyone thinks this is a good way to go, I wonder if there are any words of wisdom about managing the project so that the contractor willingly provides warranty support, not grudgingly.
This is the homeowner again. Here's where things landed. We are going with a Carrier 14 Seer Single speed 2.5 ton heatpump and a 92% gas furnace to have a dual fuel system. I doubt the furnace will be used much, if at all. In the long term the gas just isn't used then we'll just have the gas turned off so that we don't have the monthly fee.
That will also be facilitated by moving to an electric water heater, likely a Marathon by Rheem. We had one of these in a past house and it seemed to work fine and be as efficient as an electric tank water heater could be.
The water heater won't get replaced for another month or two so I'll still be researching the HPWH's to see if I can be convinced of their efficiency and durability. The installation of said water heater will be in the garage where the current unit is. I've gotten mixed messages about HPWH garage installations so any input there would be appreciated as well.
I do want to note that in general the replacement of the water heater is in no way related to the HVAC system. They are just both original to the house (1991) old, worn out, and I happen to have the budget to do both at the time.
Thank you all for the input.
Andrew
We finally have the new unit in! Right away the house has become much, much more comfortable. It's not real hot yet so we will have to wait and see what cycle times are for the new unit, but regardless the house just feels better. With the old unit we ran the fan 24/7 because if we didn't it just felt schmarmy within a few minutes of the unit cycling off.
We obviously didn't get top of the line equipment and in retrospect I'm glad we didn't.
Think about the "pretty good house" concept. It's about putting things together well in proportion. High efficiency equipment works best in a high efficiency home. A regular home needs regular equipment.
I will work, over a period of time, to make the home a "pretty good house" and by the time it gets there maybe it willbe time to get pretty good equipment to go with it. For now...the house is more comfortable and I bet my utility bill will drop some too.
Thank you all for your input
Another update from the owner. About a week after the install I noticed that the unit was not keeping up with the heat load upstairs. In addition the air handler and ductwork in the garage have had a ton of condensation built up. I let the installer know a week after install (late May).
About 3 weeks ago he sent out one guy who initially tried to say the outdoor coils were dirty...brand new coils...really? Then he measured the temp coming out of the vents. Downstairs there was about a 8-10 degree Delta, but upstairs it there was virtually no Delta. Temp coming out of the vents was 69. Temp was set at 68. Actual temperature was about 74.
Finally, after multiple calls and emails he sent out a couple of more guys last week. They kind of looked at a few things and figured they might have a air leak somewhere.
They finally came out today ready to actually do some work. They started cutting back the insulation (sopping wet insulation) from different components and found their own installers didn't tape joints well....at all.
The guy actually doing the work said there were gaps you could stick your fingers through. Interestingly, they did not use the semi-liquid mastic, but a mastic tape. I watched them do a lot of the work, but not all of it.
Even with gaps sealed better the airflow is mess. But the better sealing definitely helped the air speed coming out the upstairs vents.
Final issue. The reason the guy didn't come out forever is because 1. He refused to think there was a problem with his install. 2. He thinks we undersized the unit and that's what the key problem actually is.
We have a 2.5 tonne system (single speed), zoned (with a bypass), and almost 1900 square feet. So we have well under 1000 square feet per tonne. According to everything I've seen or read here or on Allison Bailles Blog that should be gobs of plenty.
For instance if the upstairs zone is open and downstairs is closed thats almost 2.5 tonnes for around 1000 square feet (it's not really 2.5 tonnes since the bypass pulls sone of that air off). So I kind of refuse to believe that the sizing is the issue.
Wanna hear the crazy part? This was the 4th or 5th firm I spoke to when getting estimates. They actually knew what a manual J was, looked at the one I had done by a 3rd party. When they did the install there was a bunch of them. They poured out of their trucks, we're organized, everyone semed to know their role. By every measure I could ask for they seemed to know what they were doing. It took them months to get back out here which was infuriating.
With all that I still think they were the best of any HVAC contractor I spoke with.
Sorry to hear about your experience. By any chance, was pulling a permit an option for this project? Knowing a third party inspection was in their future might have motivated the supervisors to check the shoddy work done by some of their staff. The risk of a complaint being filed with his licensing agency is another motivator for the business owner. Not that an inspection will guarantee a quality installation. The only cure for that is knowing exactly what the contractor should be doing. A great information source is YouTube - but be sure to read all the comments. The competent tradespeople will usually flag errors made by the video poster.
Adding another case to the discussion. (zone 5a, Ann Arbor, MI) I had the same problem where some guys refused to believe 2 ton A/C was enough. One even said 3.5 ton or something apparently ludicrous like that. I used an online Man J an got 2 ton. Someone convinced me to go 2.5 for the A/C unit, and it's fine, but I think it doesn't run enough and I bet a 2 ton unit would have run more and helped reduce humidity. Next cooling season I'll see if running the ERV more can help. If not, I'm facing questions about whether 65+ % humidity is okay and should I get a dehumidifier.
So, yes, independent Manual J is a good idea and I'd also add that some targeted interview questions might help sort the wheat from the chaff as far as MECH contractors go.
Seemed like the only thing holding OP back on dealing with the crawl is the mask availability. Seems like the cheapest of the improvements you have planned. I'm really into the idea of building to reduce exposure to the HVAC-research-analysis vortex of doom. And it really works. I know I won't have to bother wrangling the flaky local gas company to provide gas to the next few houses I build (by itself that's enough). I'll just insulate, airseal, and ventilate. Seems like minisplits or other alternatives are not as easy DIY as a furnace, but I bet I'll find a path that I like. Do the crawlspace, friend!
Log in or become a member to post a comment.
Sign up Log in