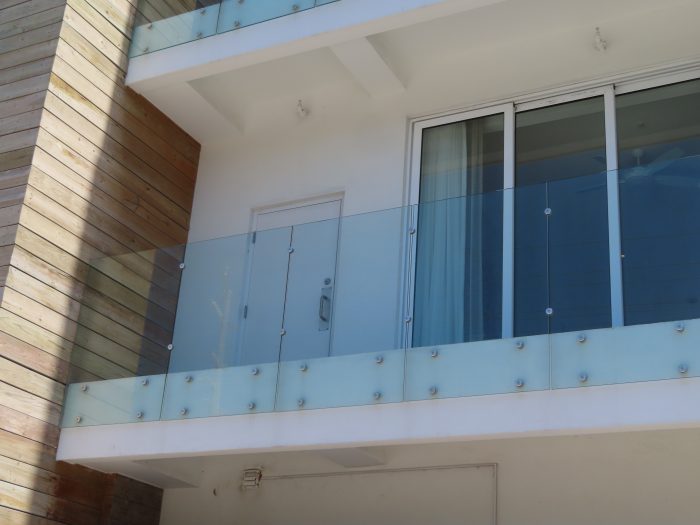
If a deck, balcony, or stairway is more than 30 inches above grade, most building codes require that a guard be installed. (The term “guard” refers to the structure that prevents people from falling off the edge of a building part. A “rail,” on the other hand, is either the top of a guard or a graspable item—usually called a handrail—that people can hold or grab to steady themselves. Balusters are vertical sticks that are components of some, but not all, guards.) Such a guard needs to be at least 36 inches high.
Guards come in all flavors, including simple pressure-treated guards made from 4x4s, 2x4s, and 2x2s; stainless-steel systems that include see-through horizontal cables; and all-glass guards.
To my eye, glass guards often look insubstantial. I decided to research guard requirements, in order to answer the question: is a glass guard strong enough and durable enough to meet code requirements?
A nearly invisible guard
The photo at the top of the page shows the balcony guard that inspired this article. The guard consists of a series of glass panels, each about 4 feet high by 3 feet wide. Each panel is attached at its base by four bolts. In essence, each glass panel is cantilevered vertically from these four bolts. At each vertical seam between adjacent glass panels there are two small stainless-steel clips to keep each panel aligned with its neighbors.
This type of glass guard does not include any type of steel rail at the top.
If someone pushes against the top of this type of guard until failure—something that I fervently hope is hard to achieve—failure will occur in one of two ways: the glass will break, or the bolts will fail.
Holding the glass with just four bolts
I shared this photo…
Weekly Newsletter
Get building science and energy efficiency advice, plus special offers, in your inbox.
This article is only available to GBA Prime Members
Sign up for a free trial and get instant access to this article as well as GBA’s complete library of premium articles and construction details.
Start Free TrialAlready a member? Log in
10 Comments
Prioritizing making the railing as invisible as possible over all the other things you want it for is dumb. One of the chief pleasures of standing on a deck is leaning on the top railing and enjoying the view. The railings themselves are architectural elements that form part of the building facade and should add beauty.
Colour largely determines whether the eye will stop at the railings, or look past them - which was widely known in the past, and why most metal railings were traditionally painted back.
The fascia-mounted panels are also a maintenance nightmare in any climates. Debris and mold soon fill the space, which is impossible to access to clean.
I will say that I'm glad this article has been posted as these changes take time to trickle down through an industry that is used to doing what they have always done. A paragraph including more information about the laminated glass and challenges associated with that would be important for those needing/considering designing this type of railing system.
Commercial (and all but the smallest multifamily) will follow ICC not the IRC and require the laminated glass if there is a walking surface exposed below, but there are different inter-layer types. The traditional one is PVB (also EVA) which will provide adhesion to contain a glass break, but is not structural enough to hold the glass together without the top rail. There are structural inter-layers SGP or Ionoplast ones that can hold the glass in place even in the event of a breakage. (https://media.licdn.com/dms/image/C4D12AQHnGc5bfP3AKQ/article-inline_image-shrink_1000_1488/0/1520145332313?e=1689206400&v=beta&t=YMPrWPloMz5FhPPAL-hwoZXDJNRrzG3hrnrik8bJuyM)
That is what the code is referring to with the ability to still have a glass railing without a top cap, but it does get more complicated. The other issue that architects, owners, and specifiers need to understand is the deflection of the top of the glass under the prescribed loads. Even under lighter loads the glass can deflect quite far due to the lever effect as noted in the article. You will likely need thicker glass than just for the ultimate failure, because you cannot allow the glass to deflect more than it's thickness or fingers can get between adjacent pieces of glass. Basically two pieces can act like scissors or shears.
With the Taperloc/Panelgrip systems the longer the piece of glass the more support they will have and less deflection you will see per panel. This helps with the deflection issue above, but without a top cap you will expose the laminated edge including the inter-layer. These layers do not always align perfectly so that exposed edge can look bad. A railing design with square pieces allows installers to rotate the piece of glass to expose the best of the 4 edges instead of just 2 options with rectangular pieces.
Overall I agree with the sentiment that these should be use with care in spaces only when required and preferably with the top cap unless the design requires it to be cap less.
Aaron,
I appreciate the additional details and technical information that you have provided. Thanks.
Commercial architects may or may not have the experience and engineering knowledge to properly specify these guards. Now that I know how complicated the issue is, I know that I will always be wary of these guards.
For all GBA readers who feel more confident than I do about all of the technical issues raised in this article, feel free to specify these guards. For those who share my level of expertise, my advice is to avoid any involvement with this type of guard.
For background, prior to my retirement in 2019, I was the quality manager for the largest residential laminated glass manufacturer in North America. Beyond basic quality concerns, our primary focus was on product reliability, product development, testing, etc. The company was serious enough about those areas that the quality department included a 3,000 square foot laminated glass product test lab within the factory.
At the time of my retirement (and still true I believe), as a company we were the largest user of SentryGlas in the world as well as largest producer of non-automotive PVB laminated glass in North America . The first year that we introduced EVA into our mix, we used more of that product than was used in all of North America combined the previous year.
Although part of the smallest (at the time) division in a primarily residential corporation, we were heavily into architectural and commercial, besides our residential priority, because of the products we manufactured.
Our first significant foray into the glass railing/balustrade market was when we were contracted to replace all of the tempered glass railings from the Toronto fiasco, possibly because no one else had the laminating capacity to do it in a reasonable timeframe(?). Beyond Toronto, we have also replaced tempered glass balustrades in a number of other projects, as well as becoming a supplier for new construction.
The tempered glass used in the Toronto failures came from China and as mentioned, it failed due to nickel sulfide inclusions. Glass floated in North America does not contain nickel, so it doesn't fail due to nickel sulfide inclusions, but glass tempered in North America may very well be imported because of both availability of North American raw glass as well as it might actually be cheaper for a tempering company to import glass from China than to buy raw float here.
As mentioned several times in the references that Martin linked, the glass used in the Toronto replacements was heat strengthened laminated, while many of the newer codes require tempered laminated. Heat strengthened laminated glass makes great sense, tempered laminated much less so.
While laminated glass alone meets all safety codes, annealed laminated glass would have to be thicker (and heavier) to meet even basic structural or wind-load requirements. It's much easier and more effective to meet those requirements by using thinner tempered or heat strengthened glass. Bit the downside is that when installing tempered laminated glass using PVB interlayer there is a risk of the glass folding up like curtain if the glass is broken and not either top or both sides supported. While SentryGlass will stay in place and not fall over like PVB when broken, and while there could be, I don't know of any codes that specify interlayer, unlike codes that do specify glass type.
Unlike tempered glass, heat strengthened glass does not break into tiny pieces, so that if broken, even when using PVB interlayer, heat strengthened glass has a significantly better chance of staying in place than tempered laminated panels. Also unlike heat strengthened and annealed glass, with tempered glass a relatively slight ding to the edge of the exposed top surface could likely result in a total failure of the lite rather than just a small chip in either annealed or heat strengthened.
Another potential problem is that since tempered glass can't be processed after tempering, there is the potential for two lites in the finished laminated panel to be slightly offset after lamination. While this is primarily an aesthetic issue, there is also the chance that there could be a slight depression of the interlayer between the two that could allow moisture to accumulate and in a freeze/thaw cycle, this could create a problem. Annealed laminated panels can be edge polished after lamination resulting in an edge almost comparable to a monolithic glass edge, and if careful heat strengthened panels can also be edge polished after lamination as well.
Technically it is possible to polish even tempered glass panels after lamination, as long as very little material is removed, but there is the risk that polishing after lamination may result in panels that are no longer as strong as panels that were untouched. This is controversial in the industry and I know of two two larger laminators that were vehement about it being a bad idea, so much so that they were pushing to mandate a code now allowing the process, but I also know of one other who felt that the benefits outweighed potential risks that they saw as minimal. We did our own extensive testing of that option but stayed out of the debate and kept our results proprietary.
Keeping in mind that while edge polishing tempered laminated glass after lamination might affect the structural strength of the product, it does not affect the safety aspects. Some people, even in the industry, have this notion that tempered glass is necessary in the laminated glass make-up because tempered is safety glass. Whereas in reality, tempered glass is safety glass because of its break characteristics and not additional strength or break resistance which is due to surface compression when the glass is tempered. Once the glass is laminated, the break pattern of tempered glass becomes a liability, and not an asset. The safety application is now 100% on the lamination and zero on the tempered
One quick comment on mounting the laminated glass panels is to never, under no circumstance, mount the panel in concrete, because it is going to fail. There are substances in concrete that are incompatible with all laminated glass interlayers and will result in delamination, especially in wet areas. I had the opportunity to inspect a few of these in the field and was told that in some places it was a relatively common way to mount tempered railings.
Exterior when the railing is tall (6' +), such as around a roof perimeter, I am personally comfortable with no top rail, and in any interior application as long as the sides are supported (even if it is another laminated glass panel) I don't see the need, but exterior balcony I wouldn't lean on it (lor get particularly close) without a top rail, unless the sides were fully supported by something other than another glass panel.
Oberon,
Thanks for providing so much technical information to GBA readers. I'm grateful.
For most of us, your key point is made at the end of your comment: when a glass guard is installed on an "exterior balcony, I wouldn't lean on it (or get particularly close) without a top rail, unless the sides were fully supported by something other than another glass panel."
Hmm - while I agree that glass guards can be trickier to design and build than other guard types, they are most likely safe or at least not even close to the riskiest thing people will encounter in the built environment.
Proper egress, occupant load, door hardware, fire door assemblies, and even things like residential wood decks probably all contribute to a much higher risk to the general public than glass guard rails (to note - I don't have specific data about it, but I'm fairly sure it is out there).
I would also say it is also important to not install something that unnecessarily risky either, but there are use cases for these glass guard. I would be interested to think about the lifecycle of these different materials as well. Glass typically would be fairly recyclable, but I'm guessing laminated glass would be harder to recycle. IDK how that would compare to a steel, aluminum, or wood guardrail (in carbon intensity either for that matter).
Thanks Martin,
To clarify my final comment a bit, it's not that I am overly concerned that the panels will fail, it's more the perception of possible failure...i.e. even if they aren't, they look flimsy without a top rail, and it scares the heck out of me to see people leaning on them when there is a long drop to the ground. Of course there are a lot of wood decks that give me the same concerns (but they aren't 30 stories up).
If I had a say in code requirement for these railing systems, they would use SentryGlas (or equivalent) as the interlayer, and heat strengthened (never tempered) glass as standard. So far as I know, unless something has changed, that isn't the case.
Aaron, laminated glass can be recycled, but since it's obviously much more involved than regular glass recycling, unless things have changed in the past couple years, most manufacturers don't have the option to recycle laminated glass.
Since the plant where I worked is very large and also there are several other laminated glass manufacturers within 100 miles or so, there is enough laminated glass locally to make it worthwhile for a local recycling company to add that capability.
Martin, You did mention installation quality in your piece, but I think it needs a bit more emphasis. I am currently working on a residential case where there are exterior glass panel guards with no top rail. The railings failed under moderate (about 30 mph) wind conditions, shortly after the home was occupied. Fortunately, nobody was injured but the large(ish) glass panels caused significant damage to other parts of the house as they fell. The failure was a simple pull-out failure of the fasteners that connected the base shoe to the deck structure. There were far too few fasteners and they were simply fastened into the plywood subfloor of the deck structure. There would have been no way for a code inspector to determine this, even if the inspector knew enough to look for it.
Considering how sensitive these systems are to the quality of the installation, I share your concerns about them. Even with top rails, it is far too easy for the installers to mess them up.
Peter,
I agree. I examined a glass guard at a hotel where I stayed. The glass guard had a cylindrical stainless-steel rail near the top, on the interior side of the glass, that provided stability to the guard. The steel rail was supposed to be fastened at each end to concrete posts, using a proprietary piece of hardware to secure each end -- but one end had already come loose, so the entire rail was wiggly. This appeared to be an installation error.
Even assuming safe as needed, I’d be concerned with having to keep it clean. But for viewing I am strongly considering cable railing with metal posts and top rail.
Log in or become a member to post a comment.
Sign up Log in