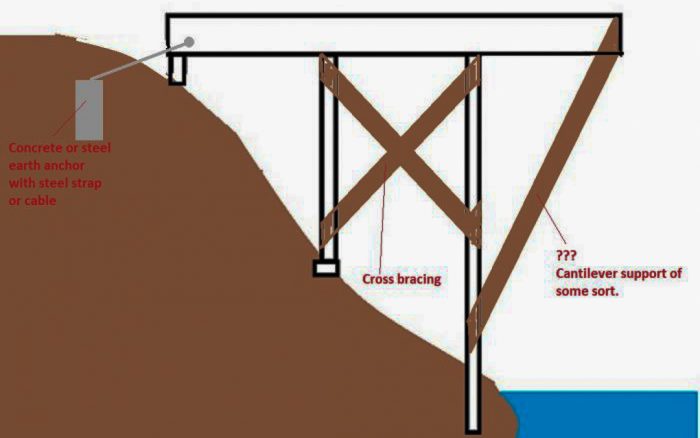
Mikeysp has just visited a friend’s lakeside cabin and come away with serious reservations about an attached deck built over a steep embankment. Scenic, possibly, but in Mikeysp’s view, a disaster waiting to happen.
The design includes a 4-foot cantilever of the 2×8 framing, structural posts that seem inadequately anchored at the ground, and a lack of lateral support.
“I warned him that it is unsafe,” Mikeysp says in a recent Q&A post. “If that were to fail, it could go down, into the water, and really harm someone, whether elderly, young, or rendered incapacitated from the impact with debris or entangled in the mess.”
The problem might be put on hold, except that the owner is planning to have 20 family members over for Thanksgiving. He wants to know whether anything can be done now to make the deck safe. Says Mikeysp,”If that thing went into the water with half his guests on there, it would surprise me if it did not end in at least one fatality.”
Among Mikeysp’s ideas are to add cross-bracing for the 4×6 support posts, find a way to anchor the posts to the ground, lift the deck up and put in new posts, or find a way to eliminate the cantilever with new bracing.
Or should the whole thing just be ripped down?
That’s the topic for today’s Q&A Spotlight.
It’s time to call in a pro
This is no time to rely on advice from an online forum, says Akos.
“There are a lot of structural issues here,” Akos writes. “You are right to be worried. Finding a fix through an internet forum is not the best way to go. I would get a structural engineer to spec the details.”
At a minimum, Akos…
Weekly Newsletter
Get building science and energy efficiency advice, plus special offers, in your inbox.
This article is only available to GBA Prime Members
Sign up for a free trial and get instant access to this article as well as GBA’s complete library of premium articles and construction details.
Start Free TrialAlready a member? Log in
11 Comments
Of course, there is an entire TV series dedicated to engineering disasters.....
The welcome breath of constructive optimism that is But Why.
I was quoted in the article!
I am Someone!
Safety first!
Good day, Malcolm
Yeah, well Scott picked this day to directly quote my somewhat tongue-in-cheek post about anonymously performing repairs. Yours was more professional, if less entertaining.
Say I build a new deck that is structurally sound. But wood decays and at some point, it will be unsafe. So what is needed - periodic inspections by some expert?
This isn't theoretical - I have a deck with a little bit of rot at the base of the support posts.
Regarding bolting wood - my understanding is that the purpose of the bolt is to press the wood together such that friction takes the shear stress (not the bolt). Glue may have a similar but perhaps more reliable effect (is it ever used in deck construction?).
Jon,
Prescriptive deck design guides and the IRC both generally prohibit bolted friction connections in wood decks, or pretty much any other wood connections. Bolted friction connections work fine for metals and some other materials, but not for wood. The problem is that wood creeps under load. So, the connection that starts out as a friction connection clamped together by the bolts ends up being a pure shear connection over time. And when you look at the local bearing stresses on a wood shear connection, you start to get scared. Not good. You easily exceed the shear stress capacity of the wood around the bolt holes. Proper wood connections require the wood members to sit on each other, directly transmitting the primary loads. The bolts are there just to hold the joint together.
FWIW, this is why nails are no longer permitted to make primary load connections in decks. It is too easy to pull them out once the deck gets a bit of age on it.
In response to your question about inspections, yes. Decks should be inspected periodically just like any other components of a house, and probably more frequently than most. When a rotting column becomes "unsafe" is always a tough call, even for experienced inspectors. This is definitely a judgment call.
For my own practice, if I find maybe 5%-10% of the cross section of a structural member is getting soft, that gets a warning but not really too much concern if everything else is OK. There is generally lots of safety margin in wood structures. If I can stick an awl full-depth into a column or timber, it's time to replace it.
Finally, glue is not used much in deck construction because the wood adjacent to the glue line is the first to rot, probably because the glue acts as a moisture stop and tends to hold moisture close by. The only exception I can think of is with PT laminated beams. These are rated for weather exposure. They use waterproof glues and the lumber is treated against decay. There's also PT plywood but you don't see it used much for decks, generally for aesthetic reasons.
Define a little bit of rot....building codes have a built in tolerance for material not being as it should be...within limits..........
Couple years ago finally got around to changing my heavy construction[4x12 and 4x6] deck stairs
Grabbed a tape and pad of paper to measure for replacement timbers and my foot went right through the top step
Got my money out of those stairs I guess
I wish there were more pics of the original deck, it looks like currentish code, but probably 80's 90's before the series of deck collapses that either changed codes or tightened enforcement. A lot cannot be seen that would decide between whether a chainsaw or a screw gun would be the appropriate tool
Material specifications also allow for variable of the parameters. All the span tables for floor joists are conservative on purposes, for example. If you design for a 10 pound per square foot load and put 12 pounds per square foot someday for a week or two, your floor won’t fail catastrophically. Everything has a little bit of margin built in for safety, but that doesn’t mean you should push the limits.
For rotted wood, I’d use the “pole test” that utility crews do: whack the post with a hammer and listen. Good, solid wood will have a bit of a ring to it. Rotten wood has a more dead sound due to the softer rotten wood. It takes some practice to know what you’re hearing though. Another test is to poke the wood. Good wood can be dented, but not punctured — you can push a pointy nail in more than enough to just make a dent. Rotten wood you can generally push a nail into much more easily.
Knowing how much rot is too much takes practice. For a fence post that isn’t critical, it’s not that big a deal if you’re a little off in your “is it ok” analysis. For something like a deck support that is critical for the safety of people on the deck, if you have ANY doubts CALL SOMEONE qualified to check it. The other option is to just replace any suspect posts. A treated 4x4 or even 6x6 isn’t all that expensive, and replacing a deck post isn’t usually all that difficult if you know what you’re doing.
Don’t take chances with safety. Be safe. Always err on the side of caution.
Bill
Any tips on removing rot weakened posts that extend 4' down with concrete at the base? It seems quite difficult.
From a design perspective, my advice to clients is always that if you can avoid the potential problems that come with decks by substituting a patio instead, it's worth doing.
https://www.finehomebuilding.com/2019/02/27/patio-vs-deck-throwdown
This. After constantly getting splinters, fixing, stripping, priming, and painting my parent's wooden deck I opted for a patio. No regrets and I would recommend it to anyone who could. If your backyard is more than 6" down from the door sill, a couple of decorative steps go a long way.
Log in or become a member to post a comment.
Sign up Log in