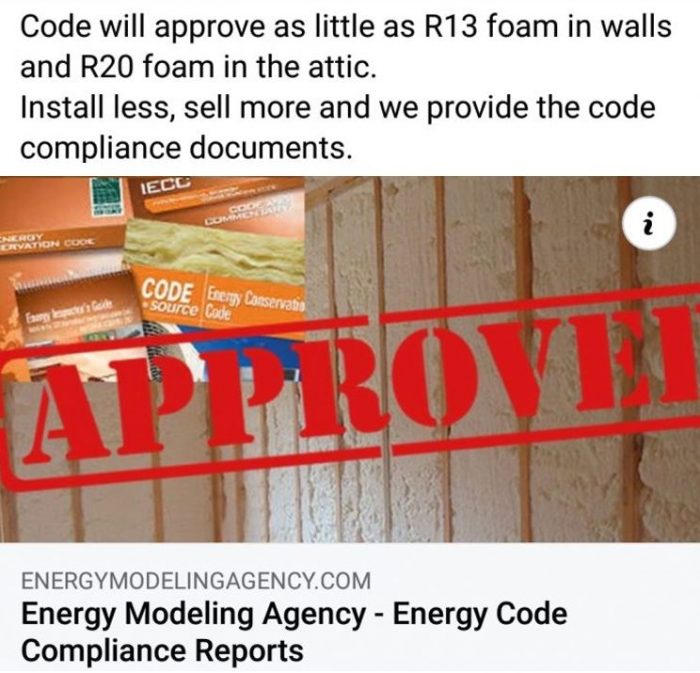
Spray polyurethane foam insulation performs very well, but it’s expensive. Spray foam contractors who bid on insulation jobs—especially those who install enough spray foam to meet the minimum prescriptive code requirements for R-value—know that their customers will get sticker shock.
Spray foam installers have used a variety of approaches to tackle this basic marketing challenge. While some of these approaches have been ethical, others have been based on misleading statements or outright fraud. Most of these marketing tactics start by trying to convince homeowners, builders, or naïve building inspectors that it’s possible to get away with installing spray foam with a lower R-value than is required by prescriptive tables in most building codes.
Companies that have used questionable marketing approaches range in size from small contractors like like J. Anderson Insulation of Belleville, Illinois (as explained in my 2019 article, “Another Deceptive Letter About Spray Foam R-Values”) to industry giants like Icynene (as explained in my 2015 article, “It’s OK to Skimp On Insulation, Icynene Says”).
Spray foam marketers often argue that fiberglass-insulated homes tend to have higher rates of air leakage than homes insulated with spray foam. The main problem with this argument is that modern building codes have established mandatory airtightness targets for new homes, regardless of what type of insulation is installed. These days, building codes insist that new homes be tested with a blower door, and that fiberglass-insulated homes achieve exactly the same maximum air leakage targets as spray-foam-insulated homes.
“How can I compete with the cheap cost of fibrous insulation?”
The latest company to join the spray foam rogues’ gallery is the Energy Modeling Agency in Gilbertsville, Pennsylvania, a consulting firm that produces and sells reports based on energy modeling software. (GBA readers were first alerted to claims made by the…
Weekly Newsletter
Get building science and energy efficiency advice, plus special offers, in your inbox.
This article is only available to GBA Prime Members
Sign up for a free trial and get instant access to this article as well as GBA’s complete library of premium articles and construction details.
Start Free TrialAlready a member? Log in
14 Comments
Great explanation of a huge problem. ICC, Code Officials and most Municipalities, have known of this problem for years, and neither have done a thing about it. ICC should take a look at the reality, and use, of the Performance Code around the country. It has been used as a way to cheat by insulators and Builders, while the homeowner gets shafted.
I wish some needy-greedy Attorneys go around the country creating class action lawsuits to insulation companies, retailers and applicators, and Builders, who corrupted and skimmed the system.
The bottom line, the laws of physics do not care what codes you use.
I think that the DOE should create a new position, the Undersecretary for Insulation Scam Enforcement (UFISE) and that Martin should be appointed as the first holder of the UFISE office.
This appears to be a garden-variety fraud. A formal complaint to the appropriate State Attorney General seems warranted.
Granular,
I don't disagree with you, but don't expect that your complaints will lead to fast resolution. When I was editor of Energy Design Update, I regularly reported R-value scams to the Federal Trade Commission, and one of the FTC lawyers, Hampton Newsome, became quite familiar with my emails and phone messages. (R-value scams are federal crimes, because of the existence of a federal law -- 16 CFR 460 -- called the R-value Rule.) In spite of my well-documented complaints about obvious fraud, prosecutions were very rare, due to the technical nature of these cases and limited government resources.
That's why R-value scammers appear to operate with impunity. It's easy to find R-value scammers any time you want, if you know what words to Google. It's so depressing that I rarely do it anymore.
I did my first foam project over 30 years ago .... I'm an old house guy and there is really no product that works as well .. really old buildings leak and there is often no space for another easy solution. That said ... it seems that the foam industry ... especially the open cell side is always trying to skirt the truth ... or bad mouth other products.
Do wish there were more real world studies of various homes done with different foam thicknesses in different climates. Back in the mid 00's we did a flash and batt when adding a 2500sf framed addition to a house in NJ. They foamed a heavy 2" just before one of the hotter summers in memory .. it was 100 for some days. I was really impressed ... it had me thinking. What is the real world performance of foam?
It's the same if you have the chance to inspect a development where they are doing both full foam and flash and batt as upgrades. Difference between the fiberglass and the foam is large -- between the two foams .... really could not tell. That was in PA ... Why has the DOE not had a few of these around for study -- or have they and I missed it ?
My current project is a church -- stand under 4" or so of foam in a 90 degree day with a slate roof and there is no heat gain way up at the peak. It would never work with fiberglass. Also -- I have been around when they blower door housing. Reminds me of the famous meat inspection with Mike Wallace and 60 minutes a generation ago (or was it two!) Same with the Zip system .... how is the tape going to look in 25 years ..especially how I see much of it done
Yeldog,
You're right, of course, that spray foam can perform very well. The fact that spray foam is an effective air barrier as well as an insulating material means that it is tremendously useful for solving problems, especially in older buildings.
That doesn't mean, however, that builders or insulation contractors should skimp on R-value. The performance of a variety of insulation products has, indeed, been intensively studied by researchers, and the relevant performance factors are well known. Passivhaus builders who pay attention to airtightness have achieved very high levels of energy performance, even without any spray foam.
In some retrofit situations, achieving code-minimum R-values is difficult -- no matter what type of insulation you choose to install. That's OK. Most codes don't require older homes to meet modern code targets for R-value.
All of that said, spray foam installers and distributors should stop lying to customers, and they should stop using deceitful spreadsheets that purport to be based on energy modeling software.
Martin,
Can you address this subject within the context of retrofitting existing homes? I often hear a arguments for the performance path when specifying the replacement or installation of insulation where none previously existed -- and where no modifications are being made to the siding, sheathing or, roofing.
The performance path argument appeals to existing homeowners seeking to reduce their cash outlay/maximize their return-on-investment. In the face of this argument, I encourage the homeowner to airseal then insulate as much as the existing space permits -- striving to meet or exceed code minimums -- letting the space constraints and environment dictate the insulation choice for the location.
Did the performance path argument for existing homes originate as a sales closing tool that is now being inappropriately linked to the performance path in ICC codes?
In the case of existing homes, are we also butting up against a policy/philosophical argument as, it is still better to make a moderate improvement in an existing home's performance than no improvement at all?
Paul,
I'm not sure I understand your question. In retrofit situations, when weatherization contractors are tightening up an older home, code officials aren't usually concerned with whether the contractors meet prescriptive code targets for R-value. Older homes are generally exempt from modern building codes -- yes, there are exceptions, but my statement is true in most cases -- which is why weatherization contractors aren't required to use performance path software to prove anything to a local code official.
I’ll have to dig a little to determine if there is a regulatory requirement in my jurisdiction, Washington, DC (to my knowledge there isn’t unless your stripping a roof to its sheathing, building an addition or, performing a gut rehab (paraphrased for simplicity) — but the sentiment I’ve heard expressed by some of my insulation subcontractors with regard to retrofits is similar to your quote from the Energy Modeling Agency website:
“Generally speaking, an R-20 of Spray Polyurethane Foam will provide a 96% heat flow reduction. If that thickness is doubled to achieve an R-40…. [it] will double your cost of the insulation and only save you a couple dollars in energy per month….That equates to a ROI [return on investment] in the hundred+ year range.”
The argument goes that if heat loss is reduced by XX%, the homeowner and insulator do not need to insulate further as the return on investment for each additional inch of insulation rapidly decreases. I’ve heard this referred to as the performance path by some of my insulation subcontractors whether we’re talking about replacing or adding insulation to a residence.
So, I guess my question is whether semantics, definitions, word choice and, perhaps, misappropriation of terms are confusing this issue further among builders, remodelers, code officials and even insulators? I’ll even add architects to that list as, they’re not often the ones doing the modeling, they’re leaving it to the engineers for that lift.
Paul,
If you have an uninsulated building, the first inch of insulation you add to an assembly saves more money annually than the second inch. If you add three inches of insulation, the third inch of insulation you add will save even less money annually than the second inch.
So it's certainly true that there are diminishing returns for thicker and thicker insulation.
Building codes strive to require an amount of insulation that makes sense -- for the planet, for the homeowner, and in terms of expected lifetime energy savings. Less insulation is a poor investment, because eventually the annual energy costs -- higher than they would be if you had added more insulation during construction -- cost more than the insulation savings.
When retrofitting insulation in older buildings, the cost considerations differ from new construction, and the optimal insulation levels depend on many factors, including local energy costs and how long the homeowner expects to own the house before selling it. The cost of the insulation is also a factor -- and clearly, $1,000 of spray foam insulation has a significantly worse payback than $1,000 of cellulose insulation.
All of that said, doubling insulation thickness always cuts the rate of heat flow through the assembly in half.
Spray foam marketers often offer misleading scenarios -- generally comparing their preferred assembly (perhaps R-10, perhaps R-20) to the performance of an uninsulated tent. But no one wants to live in an uninsulated tent, so these types of comparisons ("the first few inches of insulation reduce heat flow by 96%") are deceptive. It would make more sense for these spray foam marketers to compare their preferred assemblies to a code-minimum assembly -- but then they would have to report that "heat will flow through our preferred assembly at twice the rate of a code-minimum assembly," and that doesn't sound very good.
I would be willing to bet that most local jurisdictions do not require the blower door test even if the IECC does require it. Especially in rural areas.
Lawrence,
You're right that code enforcement varies widely from jurisdiction to jurisdiction. I live in the state of Vermont, where code compliance is mandatory but unenforced (except in one or two larger towns). That said, spray foam marketers should not be making false claims based on comparing a very tight home with an illegal, extremely leaky home -- chosen for no reason other than to give the false impression that a poorly insulated house with spray foam will perform adequately.
Martin,
I definitely agree with you that spray foam manufacturers should not make false claims. I personally think they should be financially penalized or otherwise sanctioned for deliberately trying to skirt the code and deceive their victims.
Do you all ever watch spray Jones on YouTube? He preaches this exact point in favor of spray foam, that 2 inches is satisfactory and r value is obsolete. Though I’m not buying what he says, the data hr provides can be convincing
Log in or become a member to post a comment.
Sign up Log in