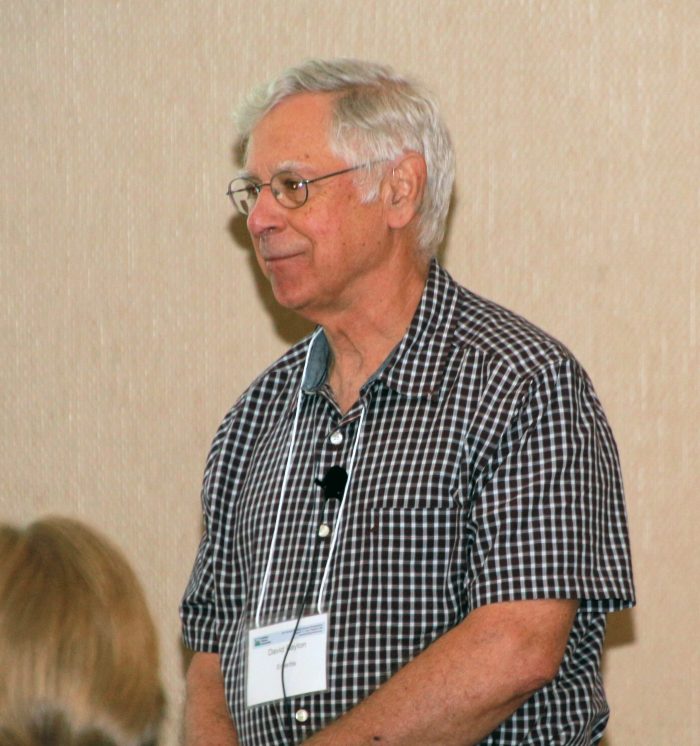
Since states began adopting energy codes in the 1980s, newer versions of the energy code continue to be adopted every few years, with each new version ratcheting up the stringency of energy requirements. As each new version of the code is debated, code advocates argue that the latest version of the code will save energy compared to earlier versions.
Now that we are several decades into the energy code era, it’s probably time to ask the question: Are energy codes saving any energy? That’s precisely the question that David Baylon set out to answer—specifically for commercial buildings in Oregon and Washington. Baylon is the founder of Ecotope, a consulting firm in Seattle that specializes in energy conservation.
Baylon gave a presentation on the topic at last August’s Westford Symposium on Building Science in Massachusetts. He started his presentation with a brief history of building energy codes in the U.S., after which he then said, “Did we make progress? The short answer is, ‘Well, not exactly…’”
A look at energy use in commercial buildings
Baylon narrowed his focus by looking at commercial buildings, in part because he had access to four giant datasets that provide utility billing information on hundreds of commercial buildings. The key metric that Baylon used for comparison—what he called “the figure of merit”—is Energy Use Intensity, or EUI. This is defined as the annual energy use per square foot of building, and is expressed in thousands of Btu per square foot. EUI includes electricity use (for all purposes) as well as all other forms of site energy, including any natural gas or heating oil burned on-site.
These were the datasets Baylon looked at:
Weekly Newsletter
Get building science and energy efficiency advice, plus special offers, in your inbox.
This article is only available to GBA Prime Members
Sign up for a free trial and get instant access to this article as well as GBA’s complete library of premium articles and construction details.
Start Free TrialAlready a member? Log in
19 Comments
Interesting, if not comforting. I would add a couple of additional factors to explain the lack of progress:
Glass: Most new commercial (and residential) buildings use way too much of it.
In a broader sense, better efficiency often leads to an increase in consumption, not a decrease; AKA the Jevon paradox. David Owen wrote the best article I've read on this topic in the New Yorker. It’s almost a decade old, but still very relevant. https://www.newyorker.com/magazine/2010/12/20/the-efficiency-dilemma
The Living Building Challenge house written about 4 days ago on this site is a perfect illustration. It comes with some good performing materials and building practices, but it is also a huge house, has a 3-car garage, and people probably expect to live in it at an always “perfect” 70 F.
This could be addressed much better by taxing (and dividend) carbon emissions, but there is no real appetite to do so in the general population. In relatively progressive MA where I live, in spite of very low energy prices, we can't even get our government to pass a gas tax that will keep up with inflation.
Vivian,
Thanks for your comment. If you are interested, you might want to read my two articles on the Jevons Paradox (both of which pre-date the article you cite from the New Yorker). Here are the links to my articles:
"Getting More Efficient, But Using More Energy"
"The Jevons Paradox"
Thanks Martin for the insights.
Did the topic of plug loads arise in any of the analysis? I'm wondering if the amount of computers and other plugged in devices has contributed to our lack of success in driving down energy use in office type environments.
Unrelated question: Any idea if these energy codes were enforced in any real way? States keep ratcheting up the code requirements, but they rarely invest in more oversight or enforcement.
Sam,
Thanks for your comments. In his presentation, David Baylon didn't mention whether plug loads were a significant contributor to increased (or, for that matter, decreased) energy use.
I don't know much about code enforcement in Oregon and Washington. But your observation is a good one: in the vast majority of U.S. states, energy codes are very poorly enforced.
Here in MN our energy code has not improved appreciably since the late 1980's when 2x6 walls were required. 2x4 walls with R-5 sheathing was considered equivalent I believe. In the mid 1990's advancing the code was discussed to include a continuous air barrier with all penetrations sealed. This was quite an advancement in improved efficiency but along with this came the requirement for mechanical ventilation. We had for a time what was called Category 1 and Category 2 homes, with Category 1 being the most stringent for energy conservation. A study was undertaken by the MN Department of Commerce of 21 Category homes as I recall and the average energy use was 3.45 Btu's/sf/hdd. This study was undertaken in the early 2000's and is kind of the benchmark for me as to the average efficiency of a MN Code built home.
Were these Category 1 homes efficient? Not really. My own house built in 1978 by others with 2x4 walls and R-5 continuous with some air sealing, added attic insulation and a 95% forced air furnace has been averaging about 2.4 Btu's/sf/hdd for the last 12 years. The double wall homes I built in the 1980's averaged between .90 and 1.5 Btu's/sf/hdd.
With the fact our homes in MN are essentially the same today as in the early 2000's in terms of energy efficiency, we have left a lot on the table. Resistance to change and cheap natural gas have made efficiency improvements low on the priority list. Production builders build the majority of the new homes in the Twin Cities and surrounding area and some do quite a nice job of insulating and air sealing. It would take a noticeable upgrade to our energy code to cut energy usage for heating in half for new homes. Thicker walls, lower U-value glazing, sub-slab insulation, lower air infiltration rates to name a few. At what cost is the public willing to pay for these efficiency improvements? Carbon footprint and doing the right thing seem to be second tier discussions these days.
Is the desire for building pressurization in order to reduce water entry?
I'm trying to figure this one out: "We should decrease envelope leakage to 0.25 cfm/sf. If you do that, now you don’t have to pressurize the building."
Does reducing leakage rates make it so pressure differentials will be minimized? It doesn't seem like it would. It seems like it would only isolate further the two environments. What it does seem like it might do is 𝘢𝘭𝘭𝘰𝘸 pressurization to happen at reduced ventilation rates (saving energy). Am I confused on this?
Tyler,
Here's my philosophy: neither deliberate pressurization nor deliberate depressurization of a building is desirable, assuming you have a good building envelope, a good HVAC system, and a balanced ventilation system.
With a leaky envelope -- all too common -- some HVAC designers recommend deliberate pressurization of the building. This reduces infiltration, which is one way (not a particularly good one) of preventing humid air from entering the building during the summer.
David Baylon is pointing out that if you design a good envelope, a lot of problems go away, so you don't need crude solutions (like deliberate pressurization) anymore.
Martin,
I agree with your sentiment, but my understanding from the MEs I work with is that they need to be able to control building pressure so doors can open/close properly, and to avoid wind tunnels in long corridors. In commercial buildings the stack pressure can get tremendous, so they need to make it so the self-closing fire doors, for example, (or chemical container room doors) are actually able to close. I believe my firm does this variably (controlled by pressure sensors). We do this even on <0.1 cfm75 buildings.
Check out Robin Rader's article "Building Static Pressure in Cold Climates" in the February 2017 ASHRAE Journal.
User...003,
I thiink the context of Martin's comments - and the general discussion around pressure differences here, is one of small residential design. Large or specialized buildings behave in a completely different way.
Malcom,
But, the story is about commercial buildings. Which are not mostly small residential buildings. No?
Steven,
In retrospect i have no idea why I made that comment in this discussion. Probably just lazy reading.
User-7625003,
Mechanical engineers need to design heating, cooling, and ventilation systems for a wide variety of buildings, including leaky buildings. Leaky buildings are far more common than tight buildings -- a reality that mechanical engineers can't easily change. So of course mechanical engineers resort to building pressurization when they are called on to design an HVAC system for the typical leaky commercial building.
David Baylon is imagining a future in which building codes raise the bar on envelope airtightness, and in which building inspectors manage to enforce the code. If we can ever achieve these goals, there will be myriad benefits -- including a reduction in, or the elimination of, the need to deliberately pressurize buildings.
The two main factors discussed in the ASHRAE article you linked to are wind pressure and the stack effect. In a leaky building, these two forces are indeed major forces acting on the air inside a building. If the building has a tight envelope, however, the effects of these forces fade away.
While interesting, I think the study and findings are fairly flawed (based on the summary here). Assuming the envelop has really improved and there aren't any offsetting penalties (e.g. increasing the the amount of glazing, I believe other factors are coming into play. In particular is the utilization of the building. For example, in retail grocery, I believe that there has been increases in the amount of refrigeration in the store. Increases in electronics, computers, etc are also probably driving up energy consumption and offsetting any gains in building efficiency.
Brad,
While you are emphasizing somewhat different factors than David Baylon emphasized, you are making precisely the same point that Baylon made: namely, that increases in energy use over the years have offset most or all of the savings from improved envelopes. That's a serious concern for targets like the 2030 Challenge, which is why the topic is worthy of discussion.
Thanks for the clarification Martin. I agree that there are certainly concerns to hit targets for energy savings.
Average temperatures have increased significantly since 2005 and we are experiencing extreme temperatures at a higher rate.
Is it a significant omission in the analysis to ignore the impact of these factors on the increased thermal deltas to which energy was applied?
Of course, in doing this additional analysis, one would want to try to separately isolate changes in interior temperature preferences from the effects on energy use from changes in outside temperatures.
John,
Heating and cooling energy use comparisons of single buildings -- especially comparisons of just two or three years -- do require weather normalization. This study looks at all energy use, not just heating and cooling energy use, and it involves large datasets of hundreds of buildings over long time periods. In most cases, weather normalization would be less useful with such large datasets and long time periods -- but with global climate change, it's a topic worth discussing.
I want to start our saying I am speaking from a QA position. I work in CA, which is widely considered a front runner in establishing energy efficient standards for residential and non-residential buildings. BUT establishing policy, and enforcement of that policy are two different matters, and policy without enforcement is mere words on paper.
I want to commend those architects, contractors, inspectors, manufacturers, and public officials that strive hard to fulfill their responsibilities, follow adopted policy, and build code compliant energy efficient properties.
It has been experience that the two biggest factor that have to be overcome to meet the Energy 2030 Challenge is Education and Enforcement. I have spent countless hours in conversations with architects, contractors, city officials, building inspectors, and property owners regarding IECC, NFRC, and State Energy & Building Codes. I am not an expert and still a student to others, but find myself educating those that should be knowledgeable, but are not. Although I am located in CA, my company mfg, and sells NFRC Certified Glass Garage Doors in all 50 states as well as internationally, so I have become well versed in Energy and Building Codes for most States. It is alarming how little most people know, or care about energy efficiency.
In my opinion, I believe the initial focus (which is long overdue) is the Education of all disciplines needs to be required and enforced, with applicable penalties applied for non compliance. And more importantly ENFORCEMENT of adopted policy, at the National, State, and local levels, is paramount. Once again, policy without enforcement is a waste of paper upon which it is printed. The respective, State Building and Energy Commissions, with the backing of the IECC and NFRC need to take the lead on this matter, and Cities and States that do not abide by policy should first be penalized and should not be considered "Green" or "Energy Conscious or Efficient".
The KISS principle has gotten lost as we explore the requirements of better air sealing and insulation for buildings made with layers of vulnerable dissimilar materials that can harm one another if arranged incorrectly or not integrated properly, and as the wooden materials we build with become thinner, more highly processed, and more vulnerable to moisture. We get roof decking rot, sheathing rot, damage to wooden subfloors, moldy basements and crawlspaces, termite damage, damage to drywall, and so on. I think the ever more elaborate detailing required to make these assemblies work is simply too complicated to expect of the average tradesman, and it's time to evaluate whether we're using the wrong materials in the first place.
Modern engineered masonry materials are far less vulnerable to damage when installed without great care, and the overall enclosure is far less complicated and harder to mess up with fewer layers of dissimilar materials to integrate. Throughout Europe, they build with thick AAC and insulating terracotta blocks that give you the whole wall in one material--structure, air barrier, insulation, and drainage. All you need to do is plaster the interior and finish the exterior with whatever material the client wants. Look up "porotherm". It's amazing stuff. And for roofs, they often use engineered panels with insulation and finish roofing built right in, or with pre-grooved surfaces for attaching the finished roofing materials. It's all so different from the typical American style of building which exposes a vast surface area for errors.
A few years ago when I started voicing these opinions, it was mostly academic for me. Since then, I've traveled to Europe many times for work, and gotten the opportunity to seen these buildings and their construction methods in person. They work, they're safely buildable by tradesmen with basic skills and poor attention to detail, and they result in durable, comfortable buildings. It's not a pie-in-the-sky fantasy; it's a reality for hundreds of millions of people.
If we're going to try to modify builders' behavior using laws and building codes and the like, I think we'd have better success mandating the use of simpler and better-engineered materials that are more tolerant of jobsite errors rather than trying to teach better practices regarding the use of existing complicated, flimsy, low-quality materials the demand perfect installation or else fail catastrophically.
Log in or become a member to post a comment.
Sign up Log in