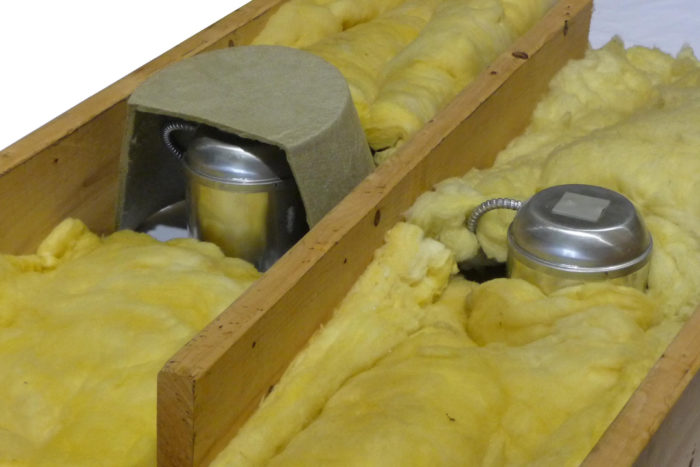
Image Credit: Tenmat
In this new-product roundup, I’ll look at a cover for recessed can lights, a new caulk for polyethylene, and several new water-resistive barriers (WRBs) that promise better performance than Tyvek or Typar.
A fire-resistant hat for recessed can lights
A Delaware manufacturer named Tenmat is selling an airtight hat for recessed can lights. Tenmat light covers are made from mineral wool; according to the manufacturer, they are fire-resistant.
Tenmat covers are installed from the attic. After making a slit in the cover to accommodate the electrical cable, the cover is pushed down to the drywall ceiling. The cover should be glued to the drywall with canned foam or thermal caulk. Needless to say, the slit or hole made for the cable needs to be sealed with housewrap tape or canned foam.
Once the Tenmat covers are installed, the ceiling can be insulated with almost any type of insulation, including fiberglass batts, cellulose, or spray polyurethane foam.
Tenmat covers come in two sizes: “regular” (9 inches high and 14 inches wide) and “oversized” (10 3/4 inches high and 16 inches wide). Energy Federation Incorporated sells regular size Tenmat covers for $19.65 each.
Besides the high price, there’s only one catch to Tenmat covers: the covers can only be used for recessed can fixtures equipped with CFL or LED bulbs. If a homeowner inserts an incandescent or halogen bulb in the fixture, it can overheat.
Dow Corning 758 caulk
Dow Corning has come out with a new caulk that sticks to a great variety of materials, including polyethylene.
The new sealant, Dow Corning 758, is a silicone caulk that the manufacturer claims will stick to polyethylene, polypropylene, vinyl, polyolefin housewrap (for example, Typar), peel-and-stick flashing (including Vycor and Tyvek window flashing), and peel-and-stick membrane (including Ice and Water Shield). The broad range of materials to which it…
Weekly Newsletter
Get building science and energy efficiency advice, plus special offers, in your inbox.
This article is only available to GBA Prime Members
Sign up for a free trial and get instant access to this article as well as GBA’s complete library of premium articles and construction details.
Start Free TrialAlready a member? Log in
11 Comments
WRB behind open joint cladding
The open joint cladding system which is commonly referred to as a "rainscreens" in local architectural circles is a very popular look these days. There was always a question about what to put beyond the "rainscreen" apart from another siding product, so the Delta Fassade S option is good to know about.
I have read health and environmental concerns regarding "fire retardants" and "blowing agents". Any known concerns with "UV inhibitors"?
How do the felt papers and Grade D building paper hold up to UV light? Are these products known to fail behind open joint cladding installations?
Thanks
Response to J Chesnut
J Chesnut,
Neither felt paper nor Grade D building paper are suitable for weather exposure or exposure to UV light. That's why people living in tar-paper shacks have to buy a roll of tar paper every 6 months.
Can light covers
Well, that's great for CFLs and LEDs - any products out there for everyone else? Or what's the best way to make your own? I've got ICE (I think!) can lights throughout the dining room and front area, and would love to make them a bit more airtight.
Thanks,
Response to Tom
Tom,
If you have access to the can lights from above (the attic), you can build a box out of drywall or rigid foam. The seams of your box should be made airtight with housewrap tape or canned foam.
The larger you make the box, the less likely the fixture will overheat (and trip the overheat sensor on the light). Of course, once the box is installed (with canned foam sealing the cracks between the box and the drywall ceiling), cover the box deeply with insulation.
can light dams
I'm a professional insulation blower and sometimes I will have an attic with 10-20 can lights which are not IC rated. The material I used to use to easily build a dam around the cans before blowing was recently deemed unacceptable by our local utility provider, who offers rebates on insulation and therefor gets to call the shots. I have not been able to get a recommendation from them, however. Any ideas for something easily installable (they're frequently in all-but-inaccessible places) which will cost my customers less than $20 per unit? Thank you.
Blueskin
Can I put the blueskin primer over top of tar? A building supply store in the area sain it make the tar gummy, and blueskin would come off eventually.
Response to Anonymous
Anonymous,
I'm not sure what you mean by "tar." You should direct your question to a technical representative at Henry Company (800-486-1278 or 800-598-7663).
airtight hat for recessed can lights
A solution posted on an insulation site awhile back, said that he used cheap styrofoam insulation coolers to cover the lights and caulked or foamed them in place. He used coolers large enough to exceed the 3" minimum contact with insulation that his inspector required. I thought is was brilliant at the time.
hat for can lights
A contractor showing a home on a parade of homes recently said he uses foam winter rose covers as can hats. Any comments about this material and method?
Response to Anonymous
Anonymous,
I've never seen a "foam winter rose cover," but if it's an airtight cover made of EPS, and if it's big enough, I don't see any reason why it wouldn't work.
Instead of can light covers, use LED LR6 lights
I spent hours and hours building drywall boxes, moving insulation, cutting the boxes to fit, and foaming them to the ceiling, only to be disappointed as to the air seal achieved. By the time I was done, I probably had nearly 1 hour into each box built, installed. For that cost including the time and materials, it cost the owner over $125 each and they still had the old can lights. Later, I discovered the LR6, a light manufactured by Cree, which is an airtight LED canlight retrofit fixture, that installs in minutes. They cost around $100 each, but considering the reduced labor costs to install them, I'd say they are well worth it. A bead of caulk around the rim, snap it in and you're good to go, for 15 years. They are dimmable too.
Log in or become a member to post a comment.
Sign up Log in