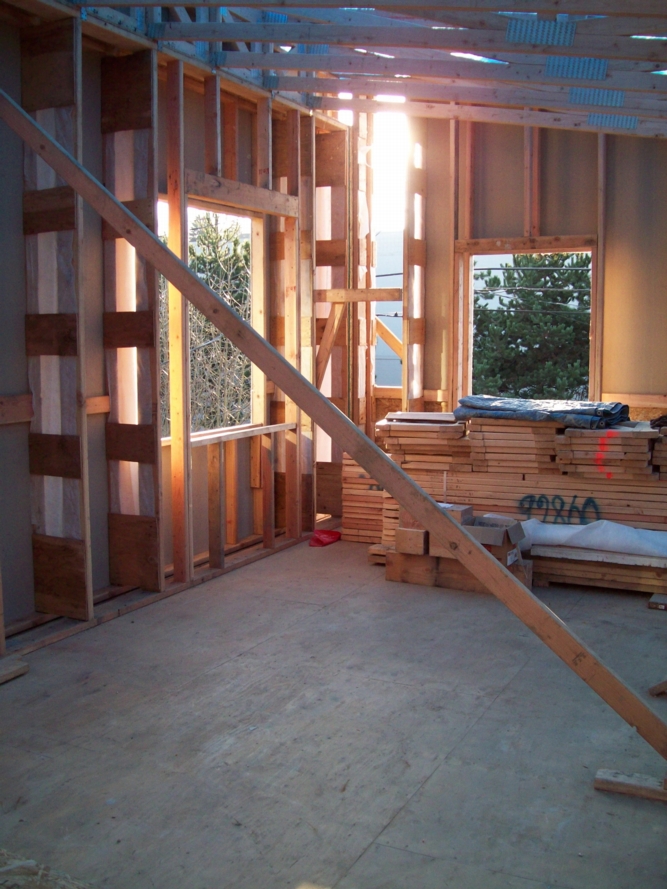
Image Credit: Dan Whitmore
When most people think about resilience — resilience to storms, for example — they think only about resilience during the event. Equally important, if not more important, I believe, is resilience in the aftermath of that event. Hurricanes, ice storms, blizzards, wildfires, tornadoes, and other natural disasters not only have an immediate impact, for which we may or may not be able to prepare, but they often have a much longer-term impact, usually through extended power outages.
The same goes for terrorist actions; some suggest that smarter terrorists of the future may target our energy infrastructure or hack into power system controls to wreak havoc (cyberterrorism).
In achieving resilience, I believe that our single most important priority is to ensure that our dwellings will maintain livable conditions in the event of extended power outages or interruptions in heating fuel. (I used to refer to this as “passive survivability,” but I came to realize that that term was too negative or dire-sounding to get much buy-in.)
Here in Vermont, a resilient home is one that will maintain temperatures of, say, 50 degrees Fahrenheit without supplemental heat. The most important strategy for ensuring that those livable conditions will be maintained is by creating highly insulated building envelopes. I will cover other strategies, such as passive solar heat and solar electricity, in future blogs in this series. Below are the key strategies for achieving exceptionally good energy performance.
Insulate extremely well
We used to think that 2×6 walls insulated with fiberglass or cellulose were perfectly adequate relative to R-value — even defining that house as energy-efficient compared with standard construction (insulated 2×4 walls). It takes far more insulation to achieve the level of resilience needed to ensure that the house will maintain livable conditions without supplemental heat or electricity.
Building Science Corporation, of Westford, MA recommends the 10-20-40-60 rule of thumb for insulation levels in homes in cold climates (roughly defined as homes north of the Mason-Dixon Line). This rule of thumb refers to R-10 for basement sub-slab insulation, R-20 for foundation walls, R-40 for above-grade walls, and R-60 for ceilings or roofs. That’s a lot of insulation, compared to typical practice in many parts of the country today, which might include no insulation under a floor slab, R-5 to R-10 on foundation walls, R-19 in walls, and R-38 in attics.
Getting to these insulation levels is not easy. R-10 slab insulation requires 2 inches of extruded polystyrene or 2.5 inches of expanded polystyrene. R-20 foundation walls require 4 or 5 inches on the foundation exterior or an insulated 2×6 wall on the interior.
Here are two options for achieving R-40 walls: double 2×4 walls held apart enough to achieve a ten-inch cavity and insulated with dense-packed cellulose; or insulating 2×6 studs with cellulose and then adding 3 inches of polyisocyanurate on the exterior. R-60 in an attic floor requires about 18 inches of cellulose.
For more on insulation materials (a lot more!), you might be interested in my recently published report: Insulation Materials: The BuildingGreen Guide to Products and Practices. It’s available as a downloadable PDF file for $129.
Install top-performing windows
This level of energy performance calls for windows that achieve a unit insulating value of R-5 — that’s not the center-of-glass R-value, but the average R-value for the entire window, including edges and frame. National Fenestration Rating Council (NFRC) window energy performance labels list U-factor rather than R-value. (U-factor is the inverse of R-value.) Look for an NFRC-rated U-factor of 0.20 or lower.
To achieve such superb energy performance typically requires triple glazing (three layers of glass or two layers of glass and a suspended plastic film) and at least one, but sometimes two, low-emissivity (low-e) coatings and low-conductivity gas in the space between the layers of glass. You can find windows today with unit U-factors as low as 0.15 (R-6.7). Such windows aren’t cheap, but they are increasingly available, and they do a great job at keeping energy consumption down and ensuring comfort.
Very tight construction
Really well-insulated buildings should also be airtight. We don’t want uncontrolled air leakage bringing outside air in through the walls or basement; we want to be able to control where fresh air is brought in through a properly designed ventilation system. The Passive House certification program, which originated in Germany but is gaining traction worldwide, including in the U.S., requires airtightness of 0.6 air changes per hour at 50 pascals of pressure difference. (We measure air tightness using a “blower door” and often report that air tightness as an elevated pressure of 50 pascals.) I think a reasonable airtightness level for new construction is 1 to 2 air changes per hour at 50 pascals — not quite as tight as the Passive House standard.
In the event of loss of power so that the ventilation system stops operating, windows can be cracked to provide fresh air, but most of the time ventilation systems should be operated to ensure good air quality in the home.
New vs. existing homes
Achieving highly insulated building envelopes is much easier with new construction than with existing homes. To achieve such performance with an existing home requires what is often referred to as a “deep energy retrofit.” More on that in a future blog.
_ _ _ _ _
In this resilient design series, I’m covering how to achieve resilient homes and communities, including strategies that help our homes survive natural disasters and function well in the aftermath of any event that results in an extended power outage, interruption in heating fuel, or shortage of water. We’ll see that resilient design is a life-safety issue that is critical for the security and wellbeing of families in a future of climate uncertainty and the ever-present risk of terrorism.
Alex is founder of BuildingGreen, Inc. and executive editor of Environmental Building News. To keep up with his latest articles and musings, you can sign up for his Twitter feed.
Weekly Newsletter
Get building science and energy efficiency advice, plus special offers, in your inbox.
5 Comments
Concrete and Insulation
My food for thought or thought for food, depending on how it is interpreted, refers to the R-40 above grade rule of thumb....and my thought is: how does one determine the R value of a wall system containing concrete/gunite, for example:
Above grade wall of Faswall block ICF (very basically a 12"W x 24"L x 8"H block made from cementized shredded pallets with 3" mineral wool inserts), cores filled with 4000psi concrete, and the entire exterior sprayed with gunite (3-4 inches) as final finish.
I think mineral wool batts have a 3.5 per inch R value, which would be an R value of 10.5 in this case. I hardly believe that a 15-`6 inch wall with 3-4" of outer gunite and the concrete fill in the form blocks can be thermally compared to a 2 x 4 fiberglass bat-filled wall...Is this sort of like the windchill factor, where It may FEEL like it's -12F outside, but it really IS 27F? Do I really have an R-12 wall that feels like an R-35? How should I look at this?
Response to Deniz Bilge
Deniz,
I've never seen a report from an independent laboratory that shows the measured R-value of a Faswall wall. While the company claims R-21 for their walls, others have estimated the R-value as closer to R-11. The walls include concrete and thermal bridges, neither of which help, and the insulation inserts are not continuous.
The R-value of 3 to 4 inches of Gunite is easier to calculate: that would be between R-0.2 and R-0.3. Almost nothing.
Faswall
Martin & Deniz, just to get more specific:
Faswall - made by Shelterworks in Philomath Oregon uses 6 or 8lbs density mineral wool from Thermafibre. I can't recall which, but it's not low density batt material. At both 6 or 8lbs density, it's around R 4.5/inch.
Also, the real opportunity with the Faswall block is exterior insulation. I sat with the company owner recently at the Northwest Eco Building Guild retreat (at which Alex Wilson was presenting Resilient Design) and we discuseed their interest in developing a specification plan for adding exterior mineral wool to Faswall structures.
Personally, I think it could prove to be an excelent choice for "Resilient Design":
- Structurally bullet proof.
- Lots of mass inside for heat storage.
- Easily capable of reciving 10" of mineral wool on the outside to get a wall up to R 45 at the insulation layer alone.
- Airsealing is possible with todays membranes and adhesives.
I think there is enough here to develop an extremely resilient structure in both storm survivability and lack of services aftermath. I like it a lot even though i'm a total "wood head".
Thermal mass
I strongly question the benefits of thermal mass for Faswall or Durisol? I haven't read anything that suggests that the the thermal mass benefit of an 12" thick R20 Faswall/Durisol wall is a better return on effort and investment than say an R40 Remote or Persist wall (you can build those with 2x4 as Thorsten Schlupp does)
Having used Durisol, I suppose I'd use it again for a foundation but wouldn't use it for above ground walls. It's so much easier to get high wall R-value using other wood framed approaches. Approaches that I'd still consider pretty resilient.
While we're on the Faswall system
I'm currently using the Faswall blocks for my home, and after having the opportunity to weigh the advantages and disadvantages of the block from first hand experience (two stories above grade installation personally), I can't say I'd use this system again.
Firstly, I'm with Martin here (unfortunately for my project) in that the lack of continuous insulation really defeats the purpose for this semi-insulated concrete form. The step I thought I was saving in terms of having to insulate the wall after putting it up really isn't so. If I wanted to put 10" of Roxul on the outside of the house, I could have built a stronger CMU wall (to be filled solid) for about 1/3 the cost (including labor) and half the time (contrary to claims) and purchased the insulation separately, which would have still brought me to less than half the cost.
Secondly, the material (85% shredded wood, 15% portland cement), while a great way to recycle pallets, is not as easy to work with as it was presented. Sure, it can be screwed into and cut like wood and doesn't require mortar between joints, which is a plus, but: some blocks are more delicate than others, meaning when cutting for window and door openings, the weaker blocks either crack or break apart or both. The problem with cracked blocks is that you don't see the cracks until the concrete blows out the back half-wall of some of these cores (of course, no lower than 16' up).
Next, the cement cannot penetrate the wood. In other words, after cuts, there is fresh wood exposed which, on more than one occasion, I have found a couple of worm holes in. Also, while screws may suck into one block, they don't bite into others (this is where you'd trade anything for a Tapcon screwed into a CMU). All this adds up to a royal pain in the boot.
The final kicker (no pun intended) is all the bracing, mainly corners and door/window bucks. I am convinced that any time and money saved in the labor of installing the morterless Faswall blocks was more than made up for in the labor intensive work of finding places for screws to grip, then leveling, bracing, and installing temporary window/door bucks, as well as all the extra rebar both horizontally and vertically as compared to traditional CMU. .....Although Faswall suggests that it's fine to drop in the verticals every OTHER course above grade after the wall has been erected, I've never seen rebar installed in that way in my whole life--In my book, there should not exist a 12 foot high concrete column without reinforcement. Also, rebar should always be tied in order to facilitate proper vibration of concrete while pouring and also for strongest performance over time......The bottom line is that the time saved using Faswall vs. CMU is much less than the time spent with all the extra prep work that a successful Faswall system requires.
Finally, a question for Andrew. I don't understand why you would use a breathable icf below grade. The whole point to the Faswall/ Durisol block is the vapor permeability attribute. Obviously, below grade, this is no longer important. Also, some other things:
Firstly, there's the extra step of parging the block in preparation for receiving waterproofing treatment vs a foam icf block---rough surface vs. smooth--. A nice polysteel foam ICF (with the steel webbing and solid fill features) would be a more consistent, stronger solution for a great below grade foundation wall, AND for cheaper. This is what I did below grade for my house. What a great product. Goes together QUICKLY ( 3 days by myself all said and done for 1560 sq feet of wall), like leggos, filles completely with concrete (no cores), and is continously insulated with no organic material to worry about.
Log in or create an account to post a comment.
Sign up Log in