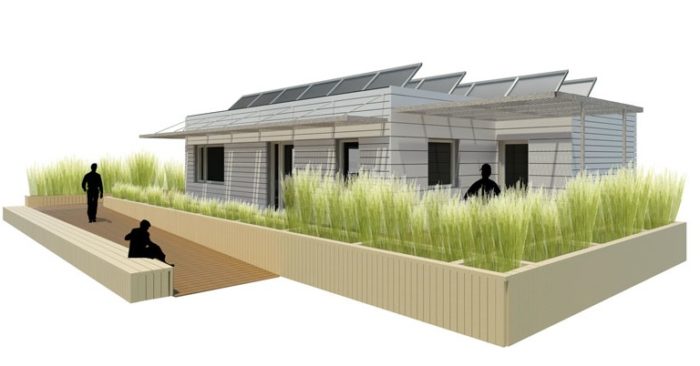
Image Credit: University of Illinois at Urbana-Champaign
Image Credit: University of Illinois at Urbana-Champaign Re_home includes about 780 sq. ft. of interior space. The main living space, like those of many Decathlon entries, features an open design that is contiguous with the kitchen area. Team Illinois originally considered using structural insulated panels (SIPs) for the roof, exterior walls, and floors, but worried that plan changes might require cutting new channels into the panels for pipes, wires, and other components. The team instead opted for the shell systems described here. Shading on the west side of the house. Exterior-wall panels were insulated with spray foam in late April. This Re_home progress photo was taken on May 10. Progress as of June 23, 2011.
A flood, tornado, hurricane, or earthquake might dissipate relatively quickly, but the damage it causes can last for years. That concern is at the heart of Re_home, the Solar Decathlon project developed by the University of Illinois at Urbana-Champaign. Re_home is essentially two rectangular modules compact enough for transport on a single-flatbed truck. Photovoltaic panels preinstalled on the modules’ flat roofs can be lowered to make transport easier and, once the modules reach their destination, the panels can then be raised on their mounting racks for optimal solar exposure. The modules themselves can be assembled quickly into a 780-sq.-ft. two-bedroom single-family home. The University of Illinois team says the rapid-deployment strategy for Re_home, and its affordability and energy efficiency, make it “an immediate and sustainable solution for a family left without a home. By combining good design, smart planning, and low-cost solutions, the Re_ home responds to the physical and emotional needs of impacted families while bringing environmentally aware living to the forefront of a community-led recovery effort.” Land of Lincoln, tornadoes, and a prefab prototype With its front porch and canopied entry, Re_home is a linear, modernized take on Midwestern architectural tradition. Canopies also shade deck areas on the east and west sides of the structure, whose two main modules were built in part at a plant operated by prefabrication specialist Homeway Homes, based in Peoria. In mid-May, the modules were trucked to the Urbana-Champaign campus, where construction continued.
Live at the International Builder’s Show
The team originally considered using structural insulated panels for the roof, exterior walls, and floor, but instead went with a stick-frame system because of concerns that re-channeling SIPs to accommodate modifications in the home’s wiring or plumbing might prove too cumbersome. The R-41.2 walls are insulated with 3 in. of spray foam on the inside and 4 in. of rigid foam outside the oriented strand board sheathing. Exterior paneling is a composite – 60% rice husks, 22% common salt, and 18% mineral oil – that the team says can be personalized with different finishes. The bays of the roof’s 10-in. trusses, which are tapered a quarter-inch per foot to give the top surface a slight drainage pitch, are filled with 6 in. of spray foam that is covered on the inside with 5/8-in. OSB and 5/8-in. drywall. A 5/8-in. layer of OSB on top of the roof trusses is covered with Sure-White EPDM (ethylene propylene diene monomer), bringing the total R value to R-37.
MORE INFORMATION Re_home Web page DOE Web page for University of Illinois at Urbana-Champaign GBA Resource Guide for 2011 Solar Decathlon
The R-40 floor also is built on 10-in. trusses (minus the taper), with 3/4-in. rigid foam on the underside. Should it prove necessary, a layer of spray foam could be added to the system to further insulate and seal the floor, the team points out. Power, comfort, and price Twenty-four SunPower E18:230 photovoltaic modules and six Sanyo HIT Double bifacial modules provide a total capacity of 5.52 kW and 1.17 kW, respectively. Some of the panels double as a shading canopy on the south-facing portion of the house. An air-source heat pump and an energy recovery ventilator will serve the home’s HVAC needs. Because Illinois is among the nation’s most tornado-prone parts of the country, there is a real possibility that, after its debut in the Decathlon, Re_home could be offered to a family displaced by one of the storms. That, at least, would fulfill the team’s primary vision for the house, the second Decathlon entry for University of Illinois, whose Gable House took second place overall in the 2009 contest. Another goal for the current project is to come in strong in the Decathlon’s affordability contest, which awards as many as 100 points for homes whose construction costs come in at $250,000 or less. Back in January, the Team Illinois project manager, Beth Newman, told Fine Homebuilding that Re_home costs were at that point well under the $250,000 mark. “The lower we can get our price, the better,” Newman said.
Weekly Newsletter
Get building science and energy efficiency advice, plus special offers, in your inbox.
One Comment
Roof R- vs. Floor R-
Does a R-37 roof with a R-40 floor strike anyone else as a strange choice? Is there a some calculation that says the shading provided by the panels reduces summer heat gain enough that less insulation is ok?
And for affordability, so much spray foam seems odd too...
I find myself wondering if for locations at risk of disaster (by tornado, at least) we should only use bio-degradable products: a dusting of blown cellulose wouldn't hurt the corn at all, right?
Which raises a question about the tilted panels too...I suppose the assumption is that it's incredibly unlikely that another tornado will hit in the same exact place, and this proposal is for replacement housing. Perhaps existing housing, or new housing in a place where a tornado hasn't hit recently could be considered differently? Raising the question of the value of building a high embodied energy building that can roll with the punches, vs. a 'light' building that is 'designed for replacement'.
For flood-prone areas, I can see an argument for encasing a building in foam...but put the doors and windows high, and tether your (boat) house to some pile / cap foundations....? ;) And plug the floor drains...
Log in or create an account to post a comment.
Sign up Log in