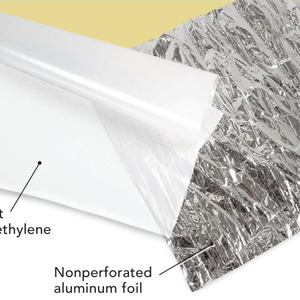
The question “do I need a vapor barrier?” is flawed from the start.
When this question is asked, there are a few possible interpretations. One is that the questioner wants to know if they need polyethylene sheeting in their assembly. Polyethylene sheeting is conversationally referred to as a “vapor barrier.” The second possibility is that the questioner doesn’t understand that “vapor barrier” is not a technical term, that their assembly may need some sort of “vapor retarder,” and that in the building codes even polyethylene sheeting is considered a “vapor retarder”— a class I vapor retarder, to be specific. But even if they did ask the question right—does my assembly need a class I vapor retarder?—the answer from building scientists is no, probably not. Unfortunately, building inspectors often disagree.
And so, vapor control is the topic of this episode of The BS* + Beer Show. Our panelists are Doug Horgan and Christine Williamson. Doug is a highly credentialed builder, speaker, author, educator, and vice president of best practices at BOWA. Christine is a building scientist, educator, and creator of @buildingsciencefightclub on Instagram. After Doug presents a few case studies of building failures that resulted from inadequate vapor control, Christine makes a case for mostly vapor-open assemblies, and we take questions from attendees. Enjoy.
The next show is Thursday, June 19, from 6 to 7:30 pm: A deep dive into dehumidification. Our panelists are Nikki Krueger and Kristof Irwin.
Nikki is the Industry Manager for Therma-Stor’s residential moisture control products (including Ultra-Aire whole house ventilating dehumidifiers and Santa Fe freestanding dehumidifiers); a RESNET certified home energy rater; she sits on the RESNET SDC 200 and the NGBS TG-3 consensus committees; and is a board member of the Maryland Building Performance Association and a member of the ACCA Manual Low Load Homes (LLH) Advisory Committee.
Kristof Irwin, P.E., M Eng., is the principal of Positive Energy. Kristof’s background includes 12 years of experience as a custom builder (including deep energy retrofits and zero-net energy projects) and 11 years as a building science consultant. He worked for 14 years as an engineer, research scientist, and physicist for government and university research labs. And he is the host of the Building Science podcast.
Use this link to register for The BS* + Beer Show.
Brian Pontolilo is a former editor at Fine Homebuilding magazine and Green Building Advisor.
Weekly Newsletter
Get building science and energy efficiency advice, plus special offers, in your inbox.
19 Comments
More interesting is "should I use a Class II vapor retarder even where code allows a Class III?". The answer is often yes.
Foam behind bathroom tile is a good point.
Doug, the basement situation sounds like a mess. Hard to believe the code still allows insulation on the interior of basements without some serious protocols in place.
If you can properly insulate on both sides of an impermeable vapor barrier the risks go down considerably. The idea is, during climate extremes keep the vapor barrier warm enough to keep it from becoming a condensing surface. Insulating on both sides of the vapor barrier is necessary for this approach; in a warm climate you'll want the barrier closer to the outside of the insulated assembly, and in a cold climate you'll want it closer to the inside.
With predicted worst-case dewpoints of both outdoor and indoor environments (plus some safety factor) you can estimate the temperature at the vapor barrier by using the assembly R-values on both sides. Make sure it never spends significant time collecting moisture, allow one-way drying on both sides (vapor open construction at drywall and sheething).
I suppose if you have little confidence in the builder to adequately detail the assembly you could use a permeable vapor retarder as well for piece of mind, but they cost a fortune compared to good old poly and that's real money that could be used to upgrade windows etc.
This show topic started out with Doug suggesting that northern designers and builders should be thinking about how our climate will change--reports I've read say that within 30-50 years, New England's climate will be similar to Virginia's, so having a vapor retarder in the right place now won't necessarily be the right place in a few decades. While a few decades seems like a long ways out, our building envelopes are fixed elements so it makes sense to plan for those changes.
Very true. With this in mind, the approach I suggest should still be sound if we err on the side of favoring a slightly warmer climate down the road.
I'm going out on a limb here because I'm only a few minutes in to this episode but I have never heard anyone recommend using paint primer as the vapour barrier and why not? in the PNW we have been doing this for years now because it saves the labour of poly and the painter is going to prime the drywall anyways and now he just need to apply 2 coats instead of one to meet the requirements. I think once we learned that there was a better way to get an air barrier without poly we stopped using it because it wasn't necessary. Under a slab I get that its a vapour barrier and air barrier for most applications but on the walls and ceilings I don't see why people wouldn't change. Thanks, enjoying the shows.
Mike, vapor barrier paint restricts drying to the interior. Although in the PNW you are known for wet weather, because it's also cool most of the time (assuming you're coastal) the dewpoints are relatively low. When it's 90° and humid, vapor drive is to the interior and moisture could accumulate against the back side of the paint.
So I guess there’s a lot of problems down south where people have multiple layers of paint on their walls. I don’t recall the exact number but something like 3 coats of oil or 6 latex was a vapour barrier years ago in the code. That’s scary. As far as where I am on the coast, the primer works well so I just wanted to pass it on because it’s a great time savings.
Joe Lstiburek likes to talk about warm-climate hotels, which all use interior vinyl wallpaper, and all have mold problems. Similar with mobile homes & FEMA trailers, which are at a worst-case-design-scenario in Florida/Louisiana.
It works fine in places that you're not using air conditioning. It should hypothetically cause far fewer problems in buildings with low organic content in the walls - but since gypsum drywall adds a few percent cornstarch as a binder, and we use it ubiquitously for fire resistance in steel and wood buildings, that doesn't apply much in the US.
I suppose the temperature delta across the insulation is the issue, so if your air conditioner is being used as an isothermal dehumidifier, as it might in the PNW...
Mike, using the "airtight drywall method" (ATDM) and using paint as the vapor retarder/barrier is something I've seen much discussion about here.
In any climate cold enough that warm humid interior air could condense inside a wall cavity, I personally don't understand the ATDM. To properly execute, and by properly I mean goal = zero exfiltration, requires a lot of planning and careful technique with drywall application. This is something drywall crews are typically (as far as I'm aware) not concerned with, meaning the job of air sealing falls on someone else after the fact to detail all the panel edge-to-bottom plate connections, as well as any penetrations for plumbing, electrical and mechanical systems (which are not easy to get right, I might add).
Using a dedicated vapor retarder/barrier at least takes that responsibility away from the gypsum panel and paint, and is a separately applied system that can be inspected and tested independently of the gypsum covering.
In warmer climates where the consequences of poor air sealing are less severe, absolutely it could make sense to avoid the unnecessary costs providing all the climate-specific Building Science rules are followed.
I’ve never done the airtight drywall before myself and I don’t believe its a long term solution. Just as with interior poly used as an air barrier as soon as you hang pictures on the wall or do a renovation you’ve messed with the continuity of that barrier so that’s why we moved our air barrier to the exterior sheathing. Since the vapour barrier/retarder does not need to be 100% continuous is why the primer works for us. It does the role which is important but not that important. If you hang pictures or rip apart a wall it doesn’t cause any major issues and is easily repairable by the primer
If your air barrier is at the exterior sheething and is properly air tight, yes, you dramatically reduce the ability for air/moisture to move through the assembly. Now your vapor barrier/retarder only has to limit the transfer of moisture. Smart.
But keep in mind that an exterior air barrier won't stop air flow from the interior, to the cold sheathing (depositing moisture) and then back to the interior. Convection can cause such a flow.
Jon,
Most houses with the sheathing as their primary air-barrier also have a second interior one in the drywall or other wall finish. That it isn't sealed or continuous doesn't matter as much when the primary air-drives are stopped by exterior one. I think the concern over convective moisture movement is a theoretical one that doesn't materialize.
https://www.greenbuildingadvisor.com/article/one-air-barrier-or-two
https://www.greenbuildingadvisor.com/question/interior-vs-exterior-air-barrier
Apparently Joe L and Energy Star think it is more than theoretical.
https://www.buildingscience.com/documents/reports/rr-0403-air-barriers/view
https://basc.pnnl.gov/resource-guides/continuous-air-barrier-exterior-walls
Agreed, more data is needed.
Yes. I wish we had more definitive information around how important both convective loops and wind-washing are both for the degradation of insulation and moisture movement. I'm largely working on hunches.
Thermally, wind washing behind vents has been shown to be a minor issue. But in summer (and with no exterior air barrier), agreed, it could move a lot of moisture to cool interior drywall.
There is a lot to be said for the air blocking abilities of cellulose.
Is there a tool or calculator out there that helps determine how to develop different systems. There are so many products, the layering could be changed up in so many ways.
Given a wall assembly as such:
Main wall assembly from inside to out: (2 coats paint, drywall, 2x6, R23 rockwool, ZIP sheathing)
I want to consider Continuous Insulation (CI) 1/2" Insulfoam on the exterior, with siding on rainscreen. I want to consider this for an easy slight boost to R-value, to help keep the sheathing on the warm side and provide a small thermal break at the sheathing to stud connection. Not related, but one of the things I read about ZIP and its limited life expectancy is in the adhesive of the tape, so it seems like adding the CI to the ZIP would eliminate that concern (but so would a house wrap). The ZIP conversation is likely a whole separate topic...
To meet code in Climate Zone 5, I would need a class II Vapor Retarder (VR) unless the exterior CI is > R5 (IRC702.7(4)).
I could go up to R5 for the CI, but the that cost gets too high (on this current project). So, perhaps the 1/2" is not even worth the consideration and worth the money?
I could use faced fiberglass batt, but I really want to use the rockwool. In this case would the use of a smart VR (DB+) on the inside make the best sense?
This is an assembly I am considering now but help in figuring this out might help me in figuring out how to build other assemblies in the future.
Where I build inspectors are very lax and check little, and in one county there are no building inspections. So, while I want to meet code, my priority is a better building.
You can use a tool like WUFI Passiv to model what happens with moisture and temperature within a wall over time. But you need someone experienced in modeling to make sure the inputs are correct. I, and most of the practitioners at GBA, use the IRC building code as a baseline of what makes a safe assembly. We discuss the options here frequently.
Log in or create an account to post a comment.
Sign up Log in