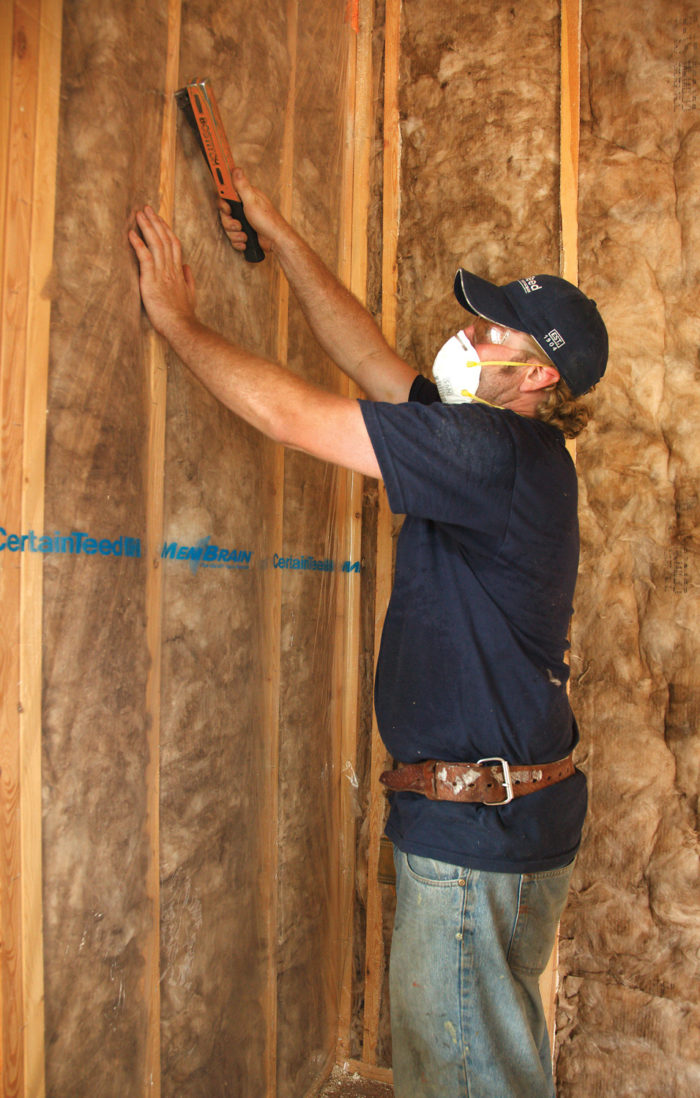
Image Credit: CertainTeed
Christopher Solar had a simple plan for an addition to his Ottawa home. The one-room structure would have a shed-style roof with a cathedral ceiling and vertical board siding. Solar liked a wall assembly he’d read about at GreenBuildingAdvisor, which consists of exterior foam, batt or blown insulation in the stud cavities and airtight drywall on the interior. An interior polyethylene vapor retarder never entered the picture.
And that’s where his story gets complicated.
“I have been warned by my designer that the building department here is not likely to approve anything that does not include the poly [vapor retarder],” Solar writes in a post at GreenBuildingAdvisor’s Q&A forum. “If that’s truly the case, what are the options for a better-than-average insulation system (average around here being stud cavity insulation only thermal bridging be damned)?”
If Solar is forced to install interior poly, he wonders whether it’s safe to install any amount of exterior foam on the walls or the roof for fear of trapping moisture inside wall and roof cavities.
“I know some foams are vapor-permeable, but if I have say 1 in. or 2 in. of exterior [extruded polystyrene] foam, is that really a wall assembly that can dry to the outside?” he asks. “My instincts say ‘no’ but if I’m wrong please let me know.”
Solar’s dilemma is the topic for this Q&A Spotlight.
Try a different type of interior sheeting
It may be tempting to think the local building inspector could be educated about the risk of trapping moisture inside walls with a poly vapor retarder. But, says GBA senior editor Martin Holladay, “many builders have found that it’s harder to educate a building inspector than it is to train a cat.”
An alternative, Holladay suggests,…
Weekly Newsletter
Get building science and energy efficiency advice, plus special offers, in your inbox.
This article is only available to GBA Prime Members
Sign up for a free trial and get instant access to this article as well as GBA’s complete library of premium articles and construction details.
Start Free TrialAlready a member? Log in
2 Comments
Air Tight Drywall
I am currently building a house in Winnipeg, MB and I'm using Air Tight Drywall. I showed that on my plans that were passed for permit and never had any problem with the plan examiner. We do not require a inspection for insulation/vapor barrier (go figure) so it never became an issue. If Christopher has a problem with his permit authority I would suggest that he purchase the latest addition of the "Canadian Home Builders Association Builders Manual. It has a section on Air Tight Drywall. It lists as a disadvantage that it is not well known by code officials although it is recognized by the NBCC. Good Luck.
Use Comfort Board
The solution is simple. Just use a better exterior insulation, which would be Roxul Comfort Board, and the interior vapour barrier is okay.
Log in or become a member to post a comment.
Sign up Log in