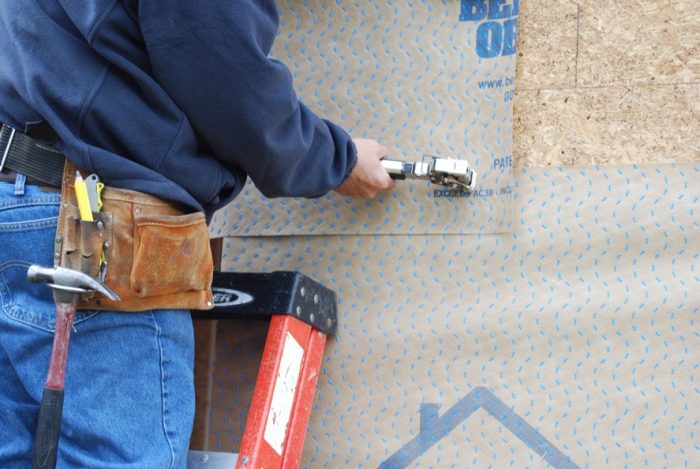
As a teenager, I worked for a small general contracting company. In between a lot of grunt work and coffee runs, I learned to do some carpentry. On two jobs, I helped install siding. When we installed cedar shakes, the carpenters taught me to offset each seam as much as possible to keep water from getting behind the siding. When installing clapboards, we backed up all of the butt joints with flashing, which has long been best practice.
Fast forward 20 years: I’m working at Fine Homebuilding magazine, visiting the job site of a high-performance home that was designed by a well-respected architect and is being built by an experienced builder. On the coast, where wind-driven rain is a regular event, the crew had just finished installing the “open-gap,” or “rainscreen,” siding—that is, siding installed over furring strips with an intentional space left between the boards.
How did we get from laying a healthy bead of caulk where siding meets trim to leaving a wide open space between each course? When did we stop relying on siding to keep water out, and start installing it to let water out? Perhaps it was the mold explosion in homes at the turn of the century and the work of architects, building scientists, and educators like steve Baczek who showed us that even the best siding installation is no match for water, and that every house needs a dedicated and effective water-resistive barrier, or WRB.
“Mother nature has a perfect record,” said Baczek, “Water is the number one killer of buildings.” The International Code Council agrees. Section R703.1.1 of the International Residential Code (IRC) calls for a WRB behind siding and only allows exceptions for some masonry walls and wall assemblies that have been specifically tested to show resistance to wind-driven rain.…
Weekly Newsletter
Get building science and energy efficiency advice, plus special offers, in your inbox.
This article is only available to GBA Prime Members
Sign up for a free trial and get instant access to this article as well as GBA’s complete library of premium articles and construction details.
Start Free TrialAlready a member? Log in
11 Comments
A comprehensive and excellent overview.
While I'm greatly indebted to Steve Baczek for the work he puts into thinking about these subjects, share his views on WRBs and building assemblies, I just can't go all the way down the path he suggests and think of open-cladding as a well-performing first layer of protection for ventilated wall cavities.
By opening up the siding to bulk water intrusion you both put too much emphasis on the underlying WRB, and make the cavity work harder than it needs to. Detailing the cladding to stop the vast majority of water leaves a well-detailed WRB and flashing to perform the roles that Brian has catalogued so well in the article.
To me the only legitimate reasons to use an open-cladding are aesthetic. In most climates that may be reason enough, but in marine-coastal ones I just don't see it.
Hey Malcolm,
I'm kind of a modernist, so I love the look of open-gap siding, but I share your hesitations and I'm not sure if I'd do it if I were building my own home.
Steve's not the only one using it, of course. I've seen quite a few homes with that siding detail all across the country over the last decade or so. Steve's a smart and thoughtful architect though, so I've asked him to write something on the topic for GBA. More to come...
Always enjoy anything Steve contributes.
I've been looking for some discussion regarding penetrations (particularly fasteners ) in WRB's. There's very little discussion of this issue that i can find. Martin mentions it on March 19, 2013 in a comment in an article back then on WRB's
"The issue seems to be fasteners and sandwiching. Once you staple or fasten a membrane to a wall, and pinch it between the siding and the sheathing, most membranes leak. The solution is to include an air gap between the WRB and the back of the siding."
That air gap would typically be a rainscreen, or a WRB with dimples or such, but I would think there's still going to be moisture finding it's way behind battens or clips or whatever and reaching the nail or screw penetrating the WRB. While the amount of moisture might be minimal and might do little damage to the sheathing as a whole, might not that moisture eventually work its way around the fastener and create decay and loss of holding power.
So is this an issue to be concerned about? If so, there are some WRB"s touted to have "self-sealing" properties, especially fluid applied WRB's. I would be interested in some comments on the efficacy of various WRB's in this regard...especially self-sticks like VaproShield, Blueskin, etc. and if there are any non-selfsticks that work well (Mento?).
Hugh,
Although I've never heard of any type fasteners causing problems with WRBs situated in rain-screen cavities, manufacturers have addressed the potential problems by specifying that WRBs must be secured by cap-nails or cap-staples.
As I alluded to above, as a general approach I think it's mistake to move the primary barrier against bulk water penetration to the WRB from the cladding. Keeping it as a secondary layer of protection makes the detailing much more forgiving, and the consequences of minor failures much less severe.
yes...making it the secondary barrier makes sense, but tell that to those who are doing "open" rainscreens, but the need to introduce vent slots above and below window/door openings in many cases will essentially make the WRB and flashing the primary barrier.
The type of fasteners that I was thinking of causing potential problems wasn't the fasteners to secure the rain screen, but the possibly thousands of penetrations fastening on battens, nailers, etc.
Hugh,
I think the best approach it to maintain the integrity of the cladding layer. We don't introduce any openings at the window sill for ventilation, rather we keep the battens down so air can travel horizontally to the cavities on both sides. We do the same at the head, flashing the window and only leaving a 1/8" gap for bulk water to exit.
As far as the thousands of fasteners that as you point out penetrate from the cladding layer back to the framing: In the absence of any real world experience that these are causing problems, I don't think it's something to worry about.
I guess that's one of the reasons I've always like cedar shingles. It's the primary barrier and every fastener gets covered a couple of times by lapped shingles.
Some roofers are working on our new Pretty-Good-House at this very moment. As I read the article and it mentioned how common it is for builders to incorrectly put step flashing over the WRB, I had to wonder how the roofers on my job were doing. Went down to check and sure enough they did it wrong! I believe all the areas of concern have already been shingled. I suppose the easiest fix is to put another layer of house wrap on those walls. Another idea would be to slit the WRB a little above the step flashing and slip a new piece of WRB underneath and overlapping the flashing. It does amaze me a bit how many tradesmen don't really do certain things correctly, sometimes because maybe their experience says it isn't necessary, but other times out of plain ignorance.
Dennis,
If they secured the step flashing to the roof, not the walls, you may be able to just pull the house wrap out from behind.
Good point Malcolm. In this case there was first the roofing felt continuous from the roof sheathing and lapped up the side walls on top of WRB and then the step flashing on top of that. I don't think we'll be able to pull the WRB out from under both layers since the felt was also stapled down.
I asked the roofers about this and they are subs for the actual roofing company I hired. They told me they called the roofing company who said they could just tape the WRB to the step flashing. I think I prefer slitting the WRB up a little ways and tucking another piece under to overlap the flashing.
The good news is that they are not as far along as I thought and there are still some areas where they can do it right the first time.
Also seems like no one around here has heard of kickout flashing !!
Log in or become a member to post a comment.
Sign up Log in