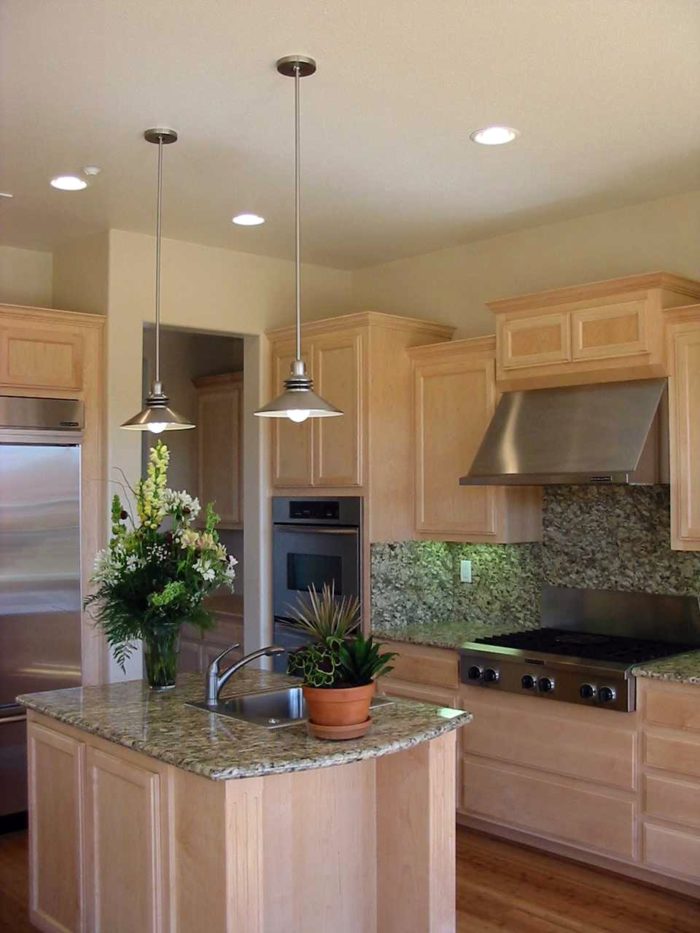
Image Credit: National Renewable Energy Laboratory
Justin Brown has moved into a house with lots of recessed lighting fixtures, including 10 six-inch Prescolite non-airtight fixtures on the second floor ceiling, and another 11 mounted in cathedral ceilings. He may have plenty of light in those rooms, but he’s more concerned about all the air that’s leaking into the attic and rafter bays and the heat loss that goes along with it.
In a Q&A post at Green Building Advisor, Brown writes, “I have explored all the options. The attic is covered with (I believe) R-30 batts and about 12 inches of blown-in cellulose on top of that. They put additional batts all around the fixtures like a moat but not on top of them — not sure why, since they are IC [insulation-contact] rated.”
In the attic, he’s considered building airtight boxes around the fixtures, but access there is difficult. Most of the fixtures are next to joists, and building the boxes would require a lot of fussy work. A more attractive option is an LED retrofit kit, which the manufacturer claims is airtight.
“I assume that will greatly cut down on air flow to the attic,” he writes. “If I install those and add some insulation directly over the cans in the attic, is that a good solution for cutting air passage and bolstering insulation in those areas?”
The retrofit kits are also IC-rated, and Brown wonders whether he can stuff some fiberglass insulation into the fixtures before installing the LED kits. That, at least, would cut down on some of the heat loss through the fixtures.
“Lastly,” he continues, “I know there are a lot of factors at play here, but can anyone help ballpark for me annual heat loss costs per can in a situation like this? I’ve seen $5 to…
Weekly Newsletter
Get building science and energy efficiency advice, plus special offers, in your inbox.
This article is only available to GBA Prime Members
Sign up for a free trial and get instant access to this article as well as GBA’s complete library of premium articles and construction details.
Start Free TrialAlready a member? Log in
12 Comments
Recessed Lighting Dilema
I'm one of those unfortunates who bought a house with recessed fixtures. They were very popular apparently for quite some time. To me, they are a head ache. Sympathy doesn't help much but is accepted gratefully.
I'm curious why only LED lights are discussed. Is there a place for CFL in the discussion? For example, is there a heat output difference? or other safety related differences? If the cans were designed for incandescent bulbs, surely they are over designed for lower power and lower heat designs like LED or CFL. Further, heat convection is not the only form of heat transfer. Can conduction/radiant heat transfer handle most or all of the load for LED?
Like other retro topics, the recessed lighting fixture one is of interest to many homeowners. Trouble is, it's like trying to get usable advice from a lawyer. You hear more about what not to do than what to do or what's been tried.
Response to W.D.
W.D.,
An LED retrofit kit is not just a type of bulb. It is a kit designed to provide a solution to leaky recessed can fixtures. LED retrofit kits provide (a) a lamp that is thin; (b) a lamp that is efficient; (c) trim that has a gasket, thereby reducing air leakage.
LED retrofit kits are now the most common way to address the recessed can problem. But this solution is not ideal, and it's not the only solution.
If you are willing to remove the recessed cans, improve the insulation, and install an airtight electrical box that isn't very deep, that's a better solution. If you do this, you can then install any type of pendant fixture, surface-mounted fixture, or track lighting you want -- and you can use CFLs in these new fixtures if you like CFLs. The main disadvantage with this second approach is that it's more work.
It's also possible to repair the ceiling with drywall plugs, so that there are no electrical boxes at all in your ceiling. If you take this approach, you can come up with a better lighting design that uses wall sconces or indirect cove lighting that bounces light off the ceiling.
For more information on lighting design, see Martin’s 10 Rules of Lighting.
It's complicated
CFLs are going away, losing market share to LED. CFLs have a shorter lifecycle and somewhat lower efficiency than LEDs, which is probably why the discussion is primarily around LEDs. Watts are watts- a 13 watt CFL puts out as much heat as a 13 watt LED, but most 13 watt LEDs put out more light than most 13 watt CFLs, and usually a somewhat higher quality light, as measured by color rendering index (CRI).
A typical ~15 watt R30 form factor CFL used in recessed lights delivers ~45-50 lumens of light output per watt or about 700-750 lumens, and has CRI of about 80. A typical retrofit R30 LED runs about 55-70 lumens/watt, and are typically 10-12 watts, putting out as much light as a 15-16 watt CFL, and the CRI is typically 85+.
Recessed cans designed for incandescent lights intentionally limit the conducted heat transfer for fire safety reasons, and are designed to convection cool the incandescent bulb. That's exactly the opposite of what you want with a CFL or LED, which is why early failure rates are high when installing CFLs & LEDs in recessed cans. So convection is really the bulk of the cooling capacity available. Incandesecents tolerate the high temps just fine, but it cooks LED & CFLs. With a base-up configuration the temperature sensitive power supply/ballast components in the highest temperature air inside the fixture, mounted to a relatively thermally isolated socket. The higher the wattage of the LED/CFL assembly the quicker the components will fail. That's another reason why purpose-made LED fixtures are a better solution than retrofit assemblies.
Stuffing insulation inside the fixture might slow down the heat escape from the house, but it also raises the temperature of the Edison-base LED assembly, and will shorten it's service life. You may be able to insulate tight to the fixture (or even inside it) without causing a fire, but it's not really the ultimate solution to anything.
Fixture such as the ~5" diameter 10 watt SlimSurface Philips low profile surface mount fixtures (comparable to R30 recessed cans in appearance) run about 65 lumens per watt, and the 90 CRI flavor isn't much more expensive than the 80 CRI version. At $50-55/pop it might be twice as much money as an Edison base retrofit assembly, but it's probably going to last more than twice as long when the old recessed can is both air-tight and insulated.
Why do LEDS fail in light fixtures
Is the heat build up the same reason LEDs fail inside enclosed light fixtures? Are there some LEDS that last longer or cool better in enclosed fixtures and recessed lights or are they all equal?
Yes it's the elevated temperature, but no, they're not equal.
There are distinctions between vendors in terms of how well they tolerate the elevated tempertures, and it's usually a function of the quality of the heat sinking on the LED retrofit assembly.
As a general rule, the lower the wattage, the longer it's likely to last, since the more watts you dump into the recessed fixture, the higher the temperature will be.
It's also true the higher the lumens per watt, the longer it will last all else being equal, since a larger fraction of the power used is being emitted as light, not heat. So a 700 lumen LED that's only 9 watts (78lm / W ) will be pumping less heat into the recessed can than a 9 watt LED that's only 500 lumens (55 lm/ W ), but it takes a dramatic difference in efficiency before that's a factor.
I'm with Martin- downlighting has low visual-efficacy due to the glare factor, and shadow casting. You can see better (even at even lower light levels) when the ambient light is being set by up-lighting, using the ceiling as a diffuser, such as cove-lighting, wall valences, or wall sconces. The bright-spot-in the ceiling approach is just shadow-casting glarey-bit, which is why it takes a whole sea of them to be able to see anything well. A predominance of downlighting only makes sense when the ceilings are too low to take advantage of uplighting (or if your spouse is totally infatuated with the 1950s lounge look. :-) )
For taking Selfies
Portrait photographers will tell you that people look best when lit from the side. To put your best face forward remove the recessed fixtures and add wall lights or standing lamps. See how many more likes you get on Facebook.
Simple and Not so Simple
New Construction- Don't install them
Old Construction- Spend the money get rid of them
Airtight Recessed Trim
If the lights use a socket holder type trim this may help in reducing air leakage.
http://www.totalrecessedlighting.com/6-inch-recessed-lighting-air-tight-par-38-r40-white-baffle-white-trim.html
Following up on my retrofit
Hi Gang,
I went ahead and installed 36 of these LED retrofits. They are tight to the drywall and have definitely cut down tremendously on air leakage.
In my cathedral ceilings, where 12 cans are directly below a roof, I did cut squares of rock wool and stuff them inside the cans, leaving about 4" between the rockwool and the top of the LEDs. I did this because I cannot access the area on top of the cans.
I am second-guessing this now -- should I remove the rockwool? I'm not worried about shortening the LED life -- they don't get very hot at all at 11 watts. I just don't want to do anything that increases a fire risk. These cans are the coldest since they are in a vented roof with no insulation over them.
I did the same with stuffing rockwool in the cans between my 2nd floor and attic. I then climbed into the attic and laid fiberglass batts over the cans themselves which are IC-rated / thermally protected. The rest of the attic is blown-in cellulose but the previous owners kept all insulation away from the light cans, even though they have IC-rated tags on them. Odd.
Would it be safer with the fixtures that lead to the attic to remove the rockwool from in the cans, and substitute the fiberglass laying over the cans in the attic with rockwool laying over the cans to be extra safe? For the cathedral cans, the rock wool in the can is my only real option, but if we think it's risky I will remove it.
What makes this all the more confusing is that the LED retrofits themselves are also IC-rated.
Thanks for turning this into an article and for all your help!
Response to Justin Brown
Justin,
I don't think I can add to all of the opinions that have been expressed so far. The official answer is that you should remove the insulation from inside the cans.
A more nuanced (but perhaps more risky) answer would be that you can use common sense: leave the lights on for an hour, and then open one up and determine how hot the light feels, to see whether you are getting a dangerous buildup of heat.
Response to Martin
Hi Martin,
Thank you I appreciate your reply. I barely even use the lights under the cathedrals. I will do as you say -- I assume if I can touch all surfaces comfortably that's not excessive heat build up. So far it seems these 11-watt units put off very little heat.
Also, the cans are IC-rated, do you think subbing the fiberglass batts I laid over the cans in the attic for r-23 rockwool batts is prudent (from an air permeability and safety standpoint) or totally not necessary?
Thank you so much!!
Response to Justin Brown
Justin,
If you have installed fiberglass batts on top of your IC-rated cans, I would leave the batts as they are. It's probably not worth changing the fiberglass batts for mineral wool batts -- especially since every trip to the attic disturbs the existing insulation in some way.
Log in or become a member to post a comment.
Sign up Log in