1/2″ interior foam board for thermal bridging?

I’m in Long Island NY, in the northern reaches of Climate Zone 4.
I discovered termite damage in a room with two exterior walls. The moisture and termite issues have been resolved, and in repairing damage to the framing, many of the studs were sistered. With all the extra studs, I’m concerned there will be a lot of thermal bridging. To counteract this, I’m considering installing rigid foam board on the interior side of the wall framing. Immediately exterior to the wall framing is exterior gypsum (house was built in the 1960s, when exterior gypsum was apparently popular), and then there is a small gap and then brick veneer.
1. The plan is fiberglass insulation bats in the stud bays (trimmed down given the narrowed stud bays caused by the sistered studs) – I guess this should be unfaced since the foam board will function as a vapor retarder?
2. Then 1/2″ foam board attached to the framing. I’m thinking 1/2″ to minimize loss of interior room space and also because I only need to break the thermal bridge of all those studs to the drywall (and I suppose I get better air sealing as well) since I’m using fiberglass insulation in the stud bays. Is 1/2″ thickness foam board sufficient to break the thermal bridge?
3. Then drywall screwed through the foam board and into the studs. This is another reason for my leaning toward 1/2″ foam board – no need for horizontal strapping.
4. The only 1/2″ foam board available at local Home Depots is FOAMULAR 1/2 in. x 4 ft. x 8 ft. R-3 Square Edge Rigid Foam Board Insulation Sheathing. This is XPS, so while it’s not green-ideal, will it work? Also, this is faced, so I guess faced/vapor retarder side should face interior of house?
5. Is this a reasonable plan of attack? There shouldn’t be any issues drying to the outside. Would condensation on the outside face of the foam board in the summer (AC on in the house) be an issue?
Thanks,
Joe
GBA Detail Library
A collection of one thousand construction details organized by climate and house part
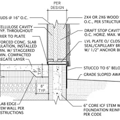
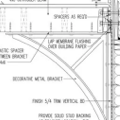
Replies
Here is some generic vapor retarder advice. Air sealing is always important.
Joe,
A realistic R-value for 1/2 inch rigid foam is R-2.5. That's not much.
I don't think it's worth doing with less than 1 inch of rigid foam; of course, 1.5 inch would be even better. For more information on this approach, see this article: "Walls With Interior Rigid Foam."
Martin,
Let's assume the fiberglass batts (for 2x4 stud wall) are R-13, and the studs are R-1.2. I guess your point is that adding rigid foam only boosts the studded area to ~R-3.7 (1.2 + 2.5), meaning the studded area is still a huge thermal bridge relative to the fiberglass filled stud bays. Going to 1" rigid foam board (R-5) boosts studded area to ~R-6.2. Still a thermal bridge, but less so. I'll give this some thought, as it does increase installation hassles (I've got a window and baseboard heat on one of the walls). Also, this is only one room in an old house, so the overall difference between 1/2" and 1" rigid foam will be very small, though it may make this room more comfortable in summer and winter.
1. Should the fiberglass insulation be unfaced since foam board will function as a vapor retarder (and not vapor barrier)?
2. Would condensation on the outside face of the foam board in the summer (AC on in the house) be an issue?
Thanks,
Joe
>"Let's assume the fiberglass batts (for 2x4 stud wall) are R-13, and the studs are R-1.2."
How about we assume something more realistic for the framing, such as R1.2 PER INCH, which would make a 3.5" deep stud R4.2. Adding half-inch polyiso (R3) would reduce the framing fraction heat flow by better than a third, and 3/4" polyiso would cut it by more than half.
Half inch XPS could eventually drop to about R2.1- which would still be cutting the heat flow through the R4.2 framing fraction by 1/3. Not nothing, but also not great.
With additional depth added to the stud bay an R13 won't be a compression fit, and the risk of voids and convection paths around the batt are pretty high. If you can tolerate 1" polyiso on the framing and compress an R19s into the 4.5" deep cavity the compressed batt would perform at about R15, and it would be a compression fit, easier to install with minimal voids.
Alternatively, installing cut'n' cobbled polyiso up against the gypsum sheathing to restore the cavity depth to 3.5", installing R13s would bring the center-cavity R up to R19, almost meeting current code-min on R-value basis, and with the R6 thermal break on the framing it WOULD meet code on a U-factor basis, even with the higher framing fraction of the sistered studs. Better still would be to install R15 batts, which are firmer and easier to scuplt to a perfect fit. With 1" polyiso against the sheathing it would then be R21 at center cavity, meeting code on an R-value basis. If it's worth preserving an extra 1/4" of interior space, with R15 batts it would still meet code min with 3/4" polyiso.
There's nothing wrong with going for code-minimum here, and putting vapor retardent foam board against the ultra-vapor-open gypsum sheathing will mitigate summertime moisture accumulation in the finish wall when air conditioning, and other issues related to the high exterior moisture drive of the
masonry cladding. The exterior grade gypsum sheathing is highly tolerant of that moisture, but the interior side wallboard is not.
If you haven't yet seen it, check out this video on how to make very clean precise cuts of foam board with minimal mess & fuss:
https://www.finehomebuilding.com/2009/01/29/theres-a-better-way-cutting-rigid-insulation
While the stud bays are still open, take the time to caulk the framing to the sheathing the full perimeter of each stud bay, and between the sistered studs with polyurethane caulk, as well as any other doubled-up framing such as top plates, jack studs, window headers, etc, as well as where the bottom plate meets the subfloor, etc. If there are any horizontal seams in the sheathing, tape them with housewrap tape before insulating.
Great tip on the “custom” insulation cutter.
I will definitely give that a try for my basement and rim joist insulation project.
Heading a bit off topic...Olfa 25mm knifes are good too. Working on sawhorses like shown in the video is smart with a knife because working on a surface, you can miss cutting through the foil face as the tip of the knife dulls.
If you have a LARGE number of linear ft to cut into 1.5" strips for framing, a plunge track saw with an edge guide hooked up dust collection is the way to go. I can cut 1" sheets double stacked as fast as I can push the saw.
>With additional depth added to the stud bay an R13 won't be a compression fit, and the risk of voids and convection paths around the batt are pretty high.
I'm confused. What additional depth added to the stud bay? I'm talking about installing rigid foam board in sheets, i.e., covering the entire wall, not cutting strips to cover just the studs. So wouldn't the batts fit pretty much like they would as if I was installing drywall directly on top of the framed and batt-insulated wall?
With the foam board, I'd be getting some mitigation of the thermal bridging through the studs as well as additional insulation over the already insulated stud bays.
Thanks for correcting me on the R-value of the studs. So with 3.5" deep studs at R-4.2 and 1/2" Foamular foam board at R-2.5 or 1" Foamular foam board at R-5, I'd be looking at R-6.7 or R-9.2 for 1/2" and 1" rigid foam, respectively, at the studs. And R-15.5 or R-18 (R-13 batts + foam board) at the bays.
Great tip on the putty knife!
>While the stud bays are still open, take the time to caulk the framing to the sheathing the full perimeter of each stud bay, and between the sistered studs with polyurethane caulk, as well as any other doubled-up framing such as top plates, jack studs, window headers, etc, as well as where the bottom plate meets the subfloor, etc. If there are any horizontal seams in the sheathing, tape them with housewrap tape before insulating.
I was going to use Great Stuff gap/crack insulating foam sealant to seal the junction of the framing to the sheathing. Is polyurethane caulk better for this?
Good point re: sistered studs, doubled up top and bottom plates, jack studs, and where bottom plate meets concrete - I will seal all of those as well. Ditto on using housewrap tape on the visible seams in the sheathing. Thanks.
>"I'm confused. What additional depth added to the stud bay? I'm talking about installing rigid foam board in sheets, i.e., covering the entire wall, not cutting strips to cover just the studs."
The original statement was:
>"2. Then 1/2″ foam board attached to the framing. "
That's perhaps ambiguous. I was interpreting that as "framing-only", not a continuous layer, since the rest of the discussion only refered to thermally breaking the framing.
>"I was going to use Great Stuff gap/crack insulating foam sealant to seal the junction of the framing to the sheathing. Is polyurethane caulk better for this?"
In general, yes, caulk is better than expanding foam for sealing those seams. Expanding foam doesn't always adhere smoothly, and won't force it's way into the tiny gaps between sheathing and stud edge as easily as PU caulk will. The expanding foam is also a bit bumpy and uneven, making it hard/impossible to get the batt to snug perfectly into the edges & corners without voids. Expanding foam is great when there is an actual gap to fill, but it's slower, messier, and less effective than caulk in this application. Don't cheap out and use a painters caulk, which would be guaranteed to fail (and quickly) in this location. Polyurethane caulk stays pretty flexible and have good adhesion for life and is highly tolerant of the moisture & temperature cycling it will experience there.
Yep, apologies for not being clearer in my original post.
Thanks for the explanation of why PU caulk instead of expanding foam. Is there a PU caulk you prefer for this application?
Any general purpose PU caulk is fine. Stay away from goopy-soupy "self leveling" caulk used for sealing concrete cracks.
Some of the batt vendors have purpose-made sealants for this application, some are low-expansion latex foam (eg Owens Corning EnergyComplete® ), but it's a MUCH lower expansion ratio than gap-filler can foams, even low-expansion "Window & Door" type can-foams.
Your existing wall with R13 batts works out to R12 (you get a bit of R value boost from the brick veneer and the air gap behind).
With the new double studs that drops down to R11.
With 1/2 xps under the drywall you end up with R14.
Going up to 1.5" polyiso you get to R22.
With 1.5" polyiso strips over the studs with R23 batts in the wall you end up with around R19 wall.
Overall, if not too much work, a layer of continuous foam (slightly more than 1/2") is worth it. The last wall is the best $/R value but more labour.
I haven't done, or redone, the math lately. But when I built our (for the time) state of the art, passive solar house back in 1982, we installed 3/4" Polyiso (R5) on the interior (taped) with 1x3 strapping creating an additional insulating air space with a reflective surface. then gyp board....It's performed really well over the years...it probably uses a bit more interior space than you want, but that's my two cents. My recollection is that the reflective air space is worth another R2 or more.
A couple of questions that seem to have gotten lost in the shuffle:
1. When using rigid foam board sheets on the interior (covering the entire wall), my understanding is the fiberglass batts I'm planning on installing in the stud bays should be unfaced. Should the rigid foam board also be unfaced, or does it not really matter since this will be the last item in the stack before the drywall?
2. For a stack consisting of brick veneer > exterior gypsum > fiberglass batts and 3-1/2 studs > rigid foam board > drywall, would there be a condensation issue in the summer when the AC is on? Or is rigid foam board sufficiently permeable that this isn't an issue? With respect to the condensation issue, does it matter if the foam board is 1/2" or 1" thick?
Thanks,
Joe
>"When using rigid foam board sheets on the interior (covering the entire wall), my understanding is the fiberglass batts I'm planning on installing in the stud bays should be unfaced."
Consider that a misunderstanding. Whether the batts are faced or unfaced it simply doesn't matter when the interior side is low-permeance foam.
>"Should the rigid foam board also be unfaced, or does it not really matter since this will be the last item in the stack before the drywall?"
In zone 4 it really doesn't matter, as long as there is a path to drying toward the exterior(such as a vented gap between the sheathing and a brick veneer.)
>"For a stack consisting of brick veneer > exterior gypsum > fiberglass batts and 3-1/2 studs > rigid foam board > drywall, would there be a condensation issue in the summer when the AC is on?"
In most of zone 4 there wouldn't be an issue unless you were air conditioning the house down to 60F or something. The R value of the foam (rather than it's permeance) is what keeps the average temperature at the exterior side surface of the foam high enough to avoid serious condensation issues. Even if it's impermeable foil faced foam it is superior to no-foam and a interior side polyethylene vapor barrier, since the exterior side facer of the foam will average several degrees warmer than the conditioned space temperature. With only fiber insulation and interior polyethylene the polyethylene sheet will be pretty much room temperature, and below the dew point of the outdoor air much of the summer in a zone 4A climate.
>>"Should the rigid foam board also be unfaced, or does it not really matter since this will be the last item in the stack before the drywall?"
>"In zone 4 it really doesn't matter, as long as there is a path to drying toward the exterior(such as a vented gap between the sheathing and a brick veneer.)"
OK, thanks. There's a definite path to drying to the exterior: through the fiberglass bats > exterior gypsum > wall void > brick veneer.
>"In most of zone 4 there wouldn't be an issue unless you were air conditioning the house down to 60F or something. The R value of the foam (rather than it's permeance) is what keeps the average temperature at the exterior side surface of the foam high enough to avoid serious condensation issues. Even if it's impermeable foil faced foam it is superior to no-foam and a interior side polyethylene vapor barrier, since the exterior side facer of the foam will average several degrees warmer than the conditioned space temperature. With only fiber insulation and interior polyethylene the polyethylene sheet will be pretty much room temperature, and below the dew point of the outdoor air much of the summer in a zone 4A climate."
Thanks. So I should be good here since I'm in the northern edge of Zone 4 (Long Island, NY), and we don't keep our AC anywhere near as cold as folks in the south. 76*F in the daytime is as cool as we set the AC in the summer. So plus a few degrees on the other side of drywall + foam board, and sounds like that would be above the dew point of outside air.
Thanks again for the explanations!