2 inch XPS rigid insulation in garage

At the moment, I’ve got a 20′ x 24′ attached garage that shares the rear wall and ceiling with conditioned space. The rear wall is 4′ anove slab elevation, sharing a wall woth the crawlspace. I’m sealing that part later, currently fixing bulk water issues.
The garage and house are made of 2 x 4 framing with vinyl siding, thermoply and R-13 Kraft paper fiberglass batts. I have 96 sheets of 2″ XPS that I got for free. The garage has no drywall, just exposed fiberglass. I used the garage a lot as a shop and just keep the garage door closed with the living space door open. The A/C unit is a 4 ton unit for the whole 2200 SF living space, I think it’s oversized. The garage door is one of the most tight and insulated I’ve seen and the garage holds temp pretty well. If I attached the 2″ XPS over the studs on the inside (Kraft paper faces inward) and air seal th seams, could I have later moisture issues? Any other forseen issues? I know I could use this for the siding when replaced or roof, but they’re both pretty new, having been replaced by the previous owner in the past 2 years.
GBA Detail Library
A collection of one thousand construction details organized by climate and house part
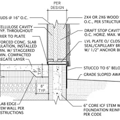
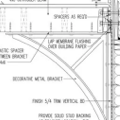
Replies
Pretty sure you would need sheetrock over the foam.
Hi Matt,
I don't see why this would cause any moisture issues and it would give you an opportunity to do some air sealing. You may find this article helpful:
Walls with Interior Rigid Foam
And, you'll have to check with your building inspector, but I think Keith is right about the need for a thermal barrier. Check out Section R316 of the International Residential Code to see if that requirement applies to your situation. You can find it here: https://codes.iccsafe.org/content/IRC2018/chapter-3-building-planning#text-id-11634974
Brian,
I had already looked into its use in my crawlspace. Per NFPA 286 Special Approval, you can use it in crawl spaces in a thickness up to 3". I thought by the flame spread and smoke tests I would be okay in the garage as well. Below is regarding the crawl space:
"6.5 Use in Attics and Crawl Spaces:
FOAMULAR XPS insulation boards may be used on walls of attics and crawl spaces, without the
coverings listed in Section 2603.4.1.6 of the IBC or Sections R316.5.3 and Section R316.5.4 of the IRC,
as follows:
1. Entry to the attic or crawl space is limited to service of utilities, and no storage is permitted.
Utilities include, but are not limited to, mechanical equipment, electrical wiring, fans, plumbing,
gas or electric hot water heaters, and gas or electric furnaces.
2. There are no interconnected crawl space areas
3. Air in the attic or crawl space is not circulated to other parts of the building.
4. Under-floor (crawl space) ventilation is provided when required by Section 1203.3 of the IBC or
Section R408.1 of the IRC, as applicable.
5. Combustion air is provided in accordance with International Mechanical Code(IMC) Sections 701
and 703 (2006 IMC) or Section 701 (2012 and 2009 IMC).
6. Foamular XPS insulation boards are limited to a maximum thickness of 3 inches (76.2mm) and a
maximum density of 2.0 pcf (32 kg/m
3
)."
Since I'm exhausting from the living space to the crawl space and out the crawl space, I should be good with one layer on the exterior crawlspace walls. I could use it as rafter dams for additional blown-in in the attic as well after air sealing.
Doing more research, it would be acceptable in a detached garage, but not an attached one. This is 2" Foamular 250. Right now I've got exposed Kraft paper in the stud cavities, so the existing is a code violation as well. Not sure what I will cover with, but at least I'm a little more comfortable knowing I shouldn't introduce moisture issues. Thanks for the responses.
OX Thermo Ply is less than 0.6 perms, which is getting down there a bit. At 2" XPS is more vapor open than that. Is it on the exterior, under the vinyl siding? What climate zone?
In the garage the XPS would have to be covered with the thermal barrier. In the crawlspace, maybe not- you might be able to get away with intumescent paint.
Exposed kraft facers are also quite flammable, and indeed a pre-existing code violation.
>"The A/C unit is a 4 ton unit for the whole 2200 SF living space, I think it’s oversized. "
D'ya think, maybe just a tad? :-)
While there are exceptions on both sides, most 2200' houses would come in around 1.5-2 tons of cooling in a Manual-J if all the ducts are inside of conditioned/semi-conditioned space (as in "... not up in a hot attic above the insulation...") Measuring it's duty cycle on afternoons at or above the 1% outside design temp would be one way to infer the load, using the air conditioner as the measuring instrument. See:
https://www.energyvanguard.com/blog/air-conditioner-sizing-rules-of-thumb-must-die
https://www.greenbuildingadvisor.com/article/four-ways-to-find-the-size-of-your-air-conditioner
Dana,
Yes the Thermoply is on the exterior. Brand name is Enermax or something like that. Just a thin corrugated plastic. This is in climate zone 4a. The old owner just replaced the HVAC before we bought as well. May be greatly oversized, but it's a 18 SEER Lennox with variable blower, smart HUB and all that, so I'm not complaining B-)! Better than what 95% of people would have chosen from an efficiency standpoint. HVAC and water heater are in attic, furnace and water heater are gas.
I can get pretty much anything from Hohmann and Barnard for free as well. Textroflash, MightyFlash, Term Bar, Drip Edge, Mortar Net, 2-Seal Barrel Masonry ties. Any idea where I could use some of this stuff? We've got partially used rolls/cases at work that most likely won't make it back to a job. We've got H-B sealant, Hilti epoxies and QSI/York sealants as well. I could use these for air sealing I suppose. These are commercial products, so I'm sure they're overkill for most applications I have.
Thanks for the responses everyone!
Garages are supposed to be fire rated and usually use 5/8” type X drywall to accomplish this. You’re supposed to do that even without any insulation. With that XPS on the walls the drywall becomes more important. If you put 5/8” drywall over all the XPS and tape/mud it the normal way you should be good. I’d recommend at least priming the drywall too, just to give you an easier time in the future if you want to paint it.
Bill
Exposed interior foam is not just a code violation it is a matter of life and death. Should a fire accrue when the foam burns it releases toxic smoke that is likely to incapacitate you before you can exit the building. So it is important that the foam be covered with a 20 minute fire barrier to give you the time you need to escape.
Even if the current HVAC system is large enough to condition the garage it would be bad idea and a code violation to connect the garage to the house. Because it could allow exhaust fumes from a car to poison your family or a garage fire to quickly spread to the house.
Walta
The garage originally had drywall on the walls that are shared with conditioned space. The rear wall above 4' is the first floor and the ceiling is a spare bedroom, both 1/2" drywall. The codes have changed a fair amount since the 2000 IBC. It's a puzzle to figure out what exactly is and is not original in the house. The builder will not let me purchase plans or specs either.
I would not want to permanently condition the garage, I simply leave the door open sometimes so it's not 90 degrees in there. We seldom park cars in there anyways, and when I do I never idle them in there. All power tools and OPE is battery powered as well. Carbon monoxide/smoke sensors in every bedroom, large room and attic. I'm not too worried about it.
I may just hang 1/2" plywood over it and paint with intumescent paint to give me a good nailing surface for hanging/attaching things and the plywood would be much easier to hang than drywall. I hate taping/mudding drywall. It'll cost almost double, but maybe worth it. Could I hang the plywood over the drywall? I guess I would have to tape/mud in either case. I would probably leave the 4" CMU/brick foundation stem wall up to 4' exposed. To cover that with the rigid and then drywall would be quite a pain. I could just fur out and then attach the drywall over the rigid?
>" We seldom park cars in there anyways, and when I do I never idle them in there."
Garages are really utility sheds, eh? :-)
In the shed you might be storing thing such as cans of gasoline for lawn mower (if yours is electric, great!), insecticides/herbacides, etc. all sort of things unrelated cars.
How does your EV create a carbon-monoxide hazard even if you WERE parking it in there? :-)