A building science mystery in Hawaii

Aloha,
I read with great interest Martin Holliday’s recent blog post “Summertime Condensation Near the Peak of a Cathedral Ceiling” (09/28/18) and the comments it elicited. I have a very similar problem with a small house on Maui. The IECC unhelpfully puts the entire state of Hawaii in climate zone 1-A (Hot Moist). But the area where the house is located gets just above 15″ annual rainfall. Using the Koppen climate classification the area is more properly characterized as “As” (Tropical Savanna Dry).
Roof/Ceiling Construction:
The house consists of three linked pavilions, one larger than the other two. The pavilions have pyramidal, standing seam metal roofs with a relatively steep 8 in 12 pitch. The peak of the roof is 17′-9″ at the smaller pavilions and 19′-2″ at the larger pavilion. The roof sandwich is supported by 5 1/8″ x 12″ glulam hip rafters and 3 1/8″x 9″ glulam jack rafters at 3′-3″ o.c. These are connected with large, custom made steel brackets. The roof deck is 2x t&g Alaskan yellow cedar. All this is visible from below and forms the ceiling treatment. Above the t&g is 3″ of rigid insulation (Thermasheath-3) with an r value of 20.3 and foil on both sides of the sheet. Although the manufacturer recommends installing this product as a continuous sheet it was installed with 2x4s on side to form a 3 1/2″ cavity. The insulation is tightly butted up to the 2x4s. One half inch plywood is attached on top of the 2x4s creating an unvented 1/2″ air gap above the rigid insulation (a code requirement?). Above the plywood is a layer of roofing felt and a standing seam metal roof. The roof color is medium brown.
The Phenomenon:
In all three pavilions there is water dripping from the ceiling. The roof has been checked and re-checked for leaks. It is tight and dry above the t&g deck. The dripping tends to start at about 10:00 in the morning and pretty much dries up as the sun goes down. The dripping occurs under every condition we could observe, sunny days, cloudy days, dry days, humid days, air con on, air con off, windows open, windows closed, ceiling fan on, ceiling fan off. We have run a dehumidifier in the larger pavilion bringing the indoor humidity down to 40%. The ceiling still drips. We have inspected the underside of the ceiling and find no mold, rust, dry rot or water damage of any kind on any of the ceiling components. We have taped down rosen paper on the floor and have discovered that the dripping is most intense at the center of the ceiling and at the connections between the longest jack rafters and the hip rafters where there are not only metal connectors but also inside corners where hot, humid air could collect. Condensation definitely forms on the metal brackets, we have photographs of it, but it also forms on the t&g at the apex of the ceiling, beading up at board edges. The gaps between the boards at the apex of the ceiling are noticeably tighter than lower down indicating a higher moisture content in the wood.
Instrumentation:
We have instrumented the ceiling and taken spot readings of surface temperatures. Typically what we find is an air temperature of 82 degrees (un-airconditioned) at the lower part of the space and an air temperature of 90 degrees at the apex. The highest spot temperature of the ceiling surface is 90 degrees. The spot temperature of the brackets is 82 degrees. The relative humidity below, where the dehumidifier is running is 40%. At the apex it is 60%. I have only used approximations to derive the dew points for these conditions. The dew point below is 60 degrees +/- which seems about right. But the dew point at the apex should be 75 degrees +/- which is too low for condensation given the readings we are getting. Perhaps there is some problem with our measuring devices. In any case it is clear that surfaces at the apex are below the dew point of the surrounding air. it is also pretty clear that there is considerable air stratification both as to temperature and water vapor content.
What Should We Do?
There are other structures on the same property that have the same roof shape and material, but they are constructed differently. They have flat ceilings with vented attics and standard truss construction. The standing seam roof sits on roofing felt on 1/2″ plywood. Insulation is in the attic above the ceiling. We plan to add some more at the underside of the roof. There is no sign whatsoever of water intrusion or of condensation in the attic, even though the venting is only in the blocking between trusses. There is no venting at the hip or at the peak.
Our most promising solution at the moment is to introduce an attic between the roof and the living space at all three pavilions. The attic would be configured to slope the ceiling at a pitch lower than the pitch of the roof, perhaps 4 in 12. The ceiling would consist of one layer of taped gypboard and a finish layer of cedar t&g. We would drill holes at the existing blocking between jack rafters and back these with copper screen. And we would provide an exhaust vent at the apex, which could be either a passive or a powered vent. And, of course, we will add additional insulation at the new attic to bring the total r value up to r 30 or 40. r 20.3 is totally inadequate.
Will this work?
And are there other thing we should do? Remove the rigid insulation? Reinstall it with no air gap (raises r to 24). Reinstall it with no 2x4s as the manufacturer recommends? Apparently a plywood nailing surface is not even required when installing standing seam. Should we thermally isolate the metal brackets by spraying them with closed foam insulation (like a thermal sleeve for a beer can)?
Or do we need to rip off the entire roof structure and start over?
Any advice would be most welcome.
Mahalo!
Susan
GBA Detail Library
A collection of one thousand construction details organized by climate and house part
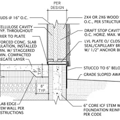
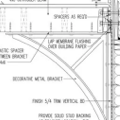
Replies
In the thread you mentioned, lots of us joined in with guesses, but I'm not sure we reached any conclusions. I'm also not sure we know the answer to your problem. Stratification is certainly part of it. Moisture buoyancy might be part, but might not. Same with radiant cooling from above or below. Have you tried installing a ceiling fan in the peak? I think the most unusual part of your measurements is that the dewpoint of the air in the peak is so much higher than in the room below. That sort of suggests that the moisture is stratifying even more than the air. Circulating the moist air down from the peak and mixing it into the room might be a solution and would be far less expensive than the attic idea. It's also an easy test to run. Plus you get the bonus of the cooling breeze. If you're already running ceiling fans, then nevermind.
Thanks!
We are running fans. But they are not in the center of the ceiling. It's hard to attach a fan at this location because of the hulking steel bracket holding 4 glulams hip beams together. But I tend to agree. My sense is that a fan at this location, running backwards (i.e. directly up at the apex) might have a chance of working. We'll see if we can jury rig something up as a test. The problem will be finding a way to support the fan. The other problem is that I would strongly prefer a solution that still works in a power outage.
> there is considerable air stratification both as to temperature and water vapor content. What Should We Do?
Temperature stratification is helping (it reduces %RH), water vapor stratification is hurting. Sloped ceilings increase stratification.
One easy to try option is to disperse/dilute/de-stratify the vapor. Ie, use a fan blowing towards (not away from) this area to mix the 80-90F dew point air there with drier, ~55F dew point air from below.
You could also look at where the moisture is coming from. Once mixed, stratification doesn't occur - so you have a warm, wet (probably 90+F and ~100% RH) moisture source feeding the peak (without mixing) . A possible example would be a wet wall heated by the sun. It's not outside air (dew point of that is too low, < 70F where you have condensation at 82F).
Edit: I type too slow.
Susan,
If you want a solution that doesn't require electricity, and if you are willing to experiment, here is what I would do: construct a horizontal ceiling measuring about 3 feet by 3 feet directly under the apex of the ceiling, so that most of the ceiling remains sloped. Build this new horizontal ceiling carefully using multiple layers of rigid foam, carefully sealed with tape or canned spray foam. The finished (visible) ceiling can be either drywall or boards -- your choice.
Worth a try.
Thanks Martin and Jon for the suggestions!
We will try two experiments in different pavilions, one to see the effect of blowing air directly at the apex of the ceiling and one to install a solid insulated flat ceiling directly below the condensing surfaces. Will report back on the results.
You obviously can see what is happening, condensation on the metal bracket. Cooler night time air cools the metal overnight, then the warm moist air of the morning enters and condenses on the cooler metal, accumulating then dripping and running down your ceiling. Martin's idea of a ceiling at the apex should work, but I would just make the ceiling temporary for now so you can monitor the location to see if it is still condensing and dripping and determine if it needs some type of small vent just as any other concealed area. Perhaps spray foam around the bracket itself first may help if the problem continues, or test one apex bracket with the foam and leave it open and observe.
If Tom’s theory is correct, a simple solution might be to mill some pockets into a piece of rigid foam and use that foam to cover the bracket. Even some R3-ish 1/2” foam would probably be enough since you only need a little bit of therm isolation to keep the condensation from forming in this case. Paint the foam to match the ceiling and it will look like an architectural detail.
Bill
Hi Susan -
It would be great to get images to go with this puzzle.
It sure sounds as though warmer, moister, lower-density air is getting up into your roof assembly and hitting surface at or below dewpoint. Sure sounds like night-sky radiation is the driver for the problem.
I use a phone app called PsyCalc to get quick accurate temp/RH/DP relationships. I think you can get the app for Android phones for free, but on an iPhone it's $7.99: https://itunes.apple.com/us/app/psycalc/id420172439?mt=8.
Peter
Thank you all.
I have attached a few photos. I can't figure out how to interweave the images and the descriptions so I hope this works.
1. The first image is the ceiling (underside of the roof) of the larger pavilion. You can see how the deep roof beams create inverse pockets where they meet. In the photo north is down and west is to the left.
2. The second image is the rosen paper beneath the apex showing about a week's worth of drips. You can see how the drips collect under the metal brackets and also along the joints in the t&g at the apex. In the photo north is up and west is left. Note that the photo cuts off the drip collections under the southeast and southwest brackets but they are there and look very much like the drip collections under the northeast and northwest brackets.
3. The third is a closeup of the center bracket. You can see the condensation streaming on the bracket and beading up along the t&g boards. This image looks south with west to the right.
4. The fourth is a thermographic image of the apex. The surface temperature variation is from 82 degrees F (the purple) to 90 degrees (the orange). The yellow is presumably hotter but the area is hard for us to get an exact read on. I suspect there may be gaps in the insulation but it is hard to inspect this area. North is down and west is left. The third and forth images were taken at about the same time of day, ca 3:15PM on a sunny day, air temperature 82 degrees. The relative humidity in the room was 40% at the bottom. The apex had not been instrumented yet so I don't know the air temperature or the humidity at the apex but later readings under similar conditions suggest 90 degrees and 60% humidity. Both may have been even higher in the inverse pockets.
A few more images of the roof. We removed the standing seam metal from one quadrant of one of the smaller roofs and then kept going.
1. The first image shows the roofing felt and the plywood nailing surface.
2. The second shows the rigid insulation (Thermasheath-3).
3. The third shows the t&g boards.
Everything was dry but the boards do show some discoloration at the joints, perhaps from past moisture moving upwards?
4. The fourth image shows the roofs in their intact state.
Mahalo all,
I totally agree about temporary. Everything is an experiment right now. I broached the idea of insulating the brackets to the contractor and I think he thought I was a little nuts. It's an easy experiment to do and if it's temporary we can disassemble to make sure the brackets aren't still sweating inside the insulation. If we enclose the whole underside (which we may want to do for aesthetics) we can a) add some ventilation and b) add some more insulation. R-20 is insufficient in the first place and, as you can see from the thermographic image, we have significant hot spots.
Is the condensation ONLY forming on those metal brackets? If so, is it only on the brackets with vertical bolts into the roof assembly, or is it on all of them (some brackets appear to connect beams with through bolts that are entirely within the room and not penetrating into the roof).
If only the brackets with bolts into the roof are an issue, I’d suspect the thermal conductivity of the bolts is the issue. That’s a thermal bridging issue that can probably be solved with some strategically placed rigid foam, or possibly some spray foam on the top side of the roof on the “other end” of those bolts.
If all the brackets are showing condensation, I’d suspect either the beam itself is the thermal bridge, or possibly it’s a thermal mass issue holding a cooler temperature long enough for the air to warm up enough for dew to form (similar to morning dew outdoors). That would be a more complex issue to solve.
Bill
Thanks Bill,
The brackets are entirely within the room and below the t&g. There are no connections between the brackets and the upper side of the assembly. The bolts only go laterally through the roof beams. The condensation occurs on all five sets brackets that you can see in the first photograph. It also occurs on the t&g at the very center of the ceiling. There are four more sets of brackets, lower down on the hip connecting another set of jack rafters. There is no condensation whatsoever on these lower brackets.
I do suspect, however, that there is a 2x4 (or multiple 2x4s) running up the hip on the upper side of the t&g and gaps in the insulation there. The insulation was not installed per the manufacturer's instructions. These instructions say to install as a continuous sheet and tape. This installation used 2x4s on their sides to create 3 1/2" deep cavities in which the 3" insulation was placed. This left a 1/2" air gap between the insulation and the plywood nailing surface for the standing seam metal. I'll bet this was done because of some code issue at the time of construction. This kind of installation is bound to leave some insulation gaps at the hip. There is definitely some kind of bridging going on. This shows up clearly on the thermographic image taken at 3:15PM which shows the t&g at the hip having the highest surface temperatures in the assembly. I need to get another thermographic image at 3:15AM. It will be interesting to see if this reverses.
Every measurement so far shows the brackets (and the roof beams) to have the same temperature as the ambient air at the lower portion of the room. It's the t&g that shows huge variation. Even so, there is nothing up there that could be described as cold. It's just hot and hotter. At least in the daytime. But apparently it is cold enough for condensation.
Susan, with those pictures I would say yes some thermal bridging going on. Heat is definitely moving through the gap near the top of the beam. I'll wait to see your AM thermos. Probably some poor insulation mistake, or wood shrinkage, letting cooler night time air into the peak cooling those upper brackets....just as the hottest air is escaping / entering......
So you may just have to seal between the T & G and the beams....??
Out of curiosity , What is the detail on the peak outside?
Hawaii insulation & airsealing practices are... not extensive. It's a place you can pretty much live comfortably in an open-air pavilion. Midcentury & earlier houses are typically framed with 'single-layer walls', which is basically 3/4" board-and-batten structural framing, without insulation or drywall or studs or sheathing or any other form of interior or exterior cladding. The last several decades have seen a successful attempt to upgrade that to 'double-layer walls', the 2x4 continental US stick framed standard.
By which I mean to say: We can't really assume that any of the normal construction methods we're used to in the continental US have been followed here (what does a foundation damp-proofing or drainage look like in Hawaii? I don't know; What even is the foundation type in the house in question?), and there are likely more extensive indoor-outdoor airflows going on than just the roof. While you have the thermal camera, get a shot of the roof from outside, get a shot of the ceiling, get a shot of the walls, the floor, everything. Then do it again in the afternoon.
It would help to have RH & temp of indoor-room, indoor-ceiling, and outdoor air. It would help more to have a measurement of those, say, every 6 hours.
Given the *timing*, if your house does actually have any decent airsealing, I would also check out what specifically the sun is shining on inside the home at around 10AM. Check if putting exterior shade fabric on those windows fixes the problem. It takes energy to evaporate water into the air so that it can be transported to the rafters and condense - if it's sunlight supplying that energy, you have a big clue as to where the water is coming from. Normally in a tightly-sealed and well-waterproofed house we would guess about showers and cooking, but 10AM through dusk every day is suspicious, and it's the opposite of what I would expect out of clear-sky radiative cooling at night.
Hi Susan
Did you ever Come to a conclusion on your leaking roof situation?
Thank you
Jacob