Adding Insulation to a Metal Building

Long-time lurker, first-time poster, but finally have a question I can’t sort out…
I have a large metal building (22,500 sf) in (always humid) Houston, TX and plan to wall off, to the roof deck, 7000 sf of the warehouse interior to create an air-conditioned work area – targeting to be around 80F and will have a couple HVLS fans.
As is typical here for this type of building, the only ceiling/roof insulation is a 3″ fiberglass blanket faced with vinyl, that is sandwiched between the metal roof purlins (joists) and the metal roof panels. The vinyl facing faces the inside of the building. The unfaced side of the insulation is against the metal roof panel.
What I typically see done here to add insulation is that metal straps are run on the underside of the purlins, and then additional insulation (also faced on one side with vinyl) is used to fill the purlin “cavities”. The vinyl on the new insulation would also face the inside of the building, and the tabs would tuck up against the purlins.
My concern with this approach is trapping moisture between the two layers of vinyl facing. Most contractors here say you just need to slash the facing on the original vinyl-faced blanket, so moisture can “escape”. However, my understanding is in Houston vapor typically tries to flow into the building, not out.
If I slash open the facing on the original insulation blankets, I would think exterior moisture would now be able to reach the purlins, which potentially would be cool from the AC, it would seem I would have a trapped condensation problem? Should I instead just leave the existing vinyl-faced blanket intact? Any thoughts would be much appreciated.
Photo attached of the current configuration – blankets on top of the purlins, and a photo of what I typically see done around here to fill the purlin cavities.
GBA Detail Library
A collection of one thousand construction details organized by climate and house part
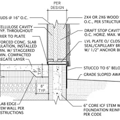
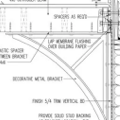
Replies
Hi Will,
If you haven’t read this article on Insulating a Metal Building, you may want to check it out. And here is Certainteed’s Recommendations for Installing Fiber Glass Insulation in Metal Buildings.
You may also find this article interesting.
https://www.greenbuildingadvisor.com/article/insulating-pole-barn
Is the plan to condition all 22500 sqf?
If not then you need to build a tight well insulated building inside your steel building.
The way I see it when anyone chose to build this style of building they decided the only thing that mattered was the cost per square foot of dry floor space and the cost of heating and cooling will always be totally irrelevant.
Walta
I'm insulating 7000 sf of the 22500 sf, constructing insulated walls inside the building. But I can't add a dropped ceiling because 1) need the height and 2) the building has an ESFR sprinkler system and changing it to accomodate a dropped ceiling is $$$$ (and would create huge permitting difficulties).
I put together some drawings to better explain the question. On the first drawing I have shown how these buildings are built, and how extra insulation is typically added. To me, both the way the building is built and the way insulation is added, IN HOUSTON, is completely wrong, since vapor flow will typically be from outside to inside, due to the warm humid climate. The "the way it's done" approach would just cause the insulation to stay wet, and potentially cause building corrosion issues.
My thought is to NOT slice the the existing vinyl facing and instead just loosely tuck the tabs of the new insulation up against the purlins. (the insulation is held up by metal strapping every 18").
So then the question should I cram in 8", to completely fill the cavity (note the existing blankets typically sag at least an inch in the center), or just add 6" with a bit of air space between the existing blanket facing and the new insulation. And if so, should I try to "vent" this air space to the interior by intentionally allowing gaps in the insulation at some interval? Or since I'm not sealing up the tabs would there likely be enough air movement. The interior of the building will always be kept at most in the 55& - 60% RH range.
Any thoughts would be greatly appreciated!
In your climate, your two moisture issues at your roof line is night time condensation on the underside of your metal roofing from radiation cooling and humidity from exterior air leaks condensing on a cold surface.
The first source is already happening, so adding extra insulation won't effect it. It is not the greatest idea to have soggy insulation up there but it should dry during the day. The problem you might have is that lot of times a bit of water makes it through the vinyl, this is not a problem over concrete floor but will be if there is a ceiling or finished floors bellow. There is no easy fix for this short of adding extra ventilation, or even better also an underlayment under the metal roofing.
For the second source, the vapor barrier near the roof deck is actually a good thing, I would not slice it. What you don't want is a vapor barrier right at your ceiling. I would go with unfaced batt insulation covered by an air tight but vapor open ceiling. Drywall is great, OSB is also fine. Definitely not vinyl. Make sure to air seal this ceiling as much as possible (taped+mudded seams) and tie it into the air barrier of the walls of your building. Also make sure this air barrier is continuous across the main roof beams.
A note about the Z grits you are planning to add. With typical spacing and size you loose between 50% to 60% of the R value of the batts from the thermal bridging of the metal. Sometimes if you need non-combustible, there are no options, however if you don't, going with wood strapping would significantly increase the R value of the assembly. The problem is that it is pretty hard to hang 2x8s under metal purlins, so might not be worth the effort.