Adding rigid insulation on top of an existing cathedral roof
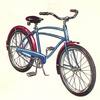
I’m dealing with an existing, 60-year old building with a 12:12 cathedral ceiling. It’s actually a small church. It has a simple gable roof with no odd geometries or significant penetrations. Just a couple of plumbing vents and a masonry chimney.
The original drawings show 2×6 rafters with 4″ of “balsam wool” insulation and a 1-1/2″ air gap between the insulation and the 3/4″ decking. There were – and are still – asbestos shingles installed over the decking, and continuous soffit vents at the eaves. NO ridge venting. 20 years ago, someone talked the church into installing foam roofing over the top of the existing asbestos shingles. It looks pretty bad, as you might imagine. We’re going to tear off the existing foam/asbestos mess and build back up from the original 3/4″ roof decking.
I’m proposing 3″ of EPS and a 1/2″ plywood coverboard, then stone-coated steel shingles with underlayment. We’re planning to install new vented soffits to replace the tired-looking ones that are there now. But again, there’s never been any ridge venting, and it doesn’t seem to have caused any issues. The roof looks terrible because of the sagging, nasty foam application, but there have never been any leaks or problems inside, and so my thinking is that what we’re putting on in place of the foam & asbestos shingles could only improve things, not create any new problems. Am I thinking about this right? Will the added insulation in fact cause some new problem? While we have everything stripped down to the decking, should we install some ridge venting? Some other type of roof vents? Would really appreciate your assistance!
GBA Detail Library
A collection of one thousand construction details organized by climate and house part
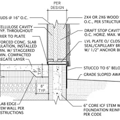
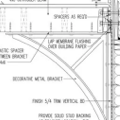
Replies
Hi Sarah.
When you install exterior insulation on the roof, the roof shouldn't be vented (even if there is not ridge vent). I suggest you start with this article: How to Build an Insulated Cathedral Ceiling.
Thanks Brian. I did read and highlight that article but got a little turned around because I'm dealing with an existing condition (a vented roof) that has been performing fine. When I read: "A vented cathedral ceiling only makes sense if the geometry of your roof is simple. You need a straight shot from the soffits to the ridge." I thought, Okay, well maybe we're in business! That's why I included the note about the geometry we're dealing with. Also there's this: "If a roof has only soffit vents and no ridge vents, most codes require 1 square foot of net free ventilation area for every 150 square feet of attic floor area." (ok, fine) But then this: "Remember: if you choose to install rigid foam on top of your roof sheathing, don’t install ventilation channels under the roof sheathing; these two practices are incompatible." If I have vent channels NOW, do I seal them up? Or can I fall back on, "A simple gable geometry is ok to vent." ??
Sarah,
The talk of venting simple geometry is for roofs that do not have exterior rigid foam insulation. When you insulate the exterior, you do not want vent channels--you are switching to an unvented roof.
I'm not sure if it would be adequate to block off the soffit vents, I think you'd need to insulate and air seal from the top plate to the underside of the sheathing so that you don't have exterior air short circuiting your insulation. Also, you may consider using polyiso instead of EPS to get more R-value outside of the roof. Where are you located (I don't think your post said...)
Perhaps someone who has dealt with this specific situation before will see this and chime in.
Okay, thanks Brian. This all makes sense. I appreciate the clarification on the simple geometry venting.
This is all being done on a rural church budget, so we're trying to do the best we can with limited funds. If either type (polyiso or EPS) would be an acceptable choice, we could price it both ways and see what we can afford.
The church is in climate zone 5a.
DIY opinion:
I would probably only go with polyiso if you were getting it used given likely cost increase over EPS and possible performance issues during the coldest temperature.
Given you said this was a church, any chance that a local roofing company would hook up you up with reclaimed polyiso or eps from a commercial building re-roof etc?
You could also consider a stackup of both EPS and polyiso. If you keep the polyiso warm than (IIRC) -5F by using EPS on top, I believe you don't have cold climate performance issues?
Is there a reason you are limiting it to 3"? Practical fastener length? Certainly your target R values won't be met with 3" of foam on top of 'balsam wood insulation'.
Have you put a camera into rafters to see if you have anything left in there at all? Is there any way you could blow loose fill into the rafters?
Also, if that air gap under the deck isn't maintained structurally or mechanically I would personally guess that the existing batts or loose fill will have slumped and you probably have 5.25" of insulation at the bottom and not so much at the top. If that's true, your soffit vents might not be doing much. Again, I would think an inspection camera might help. Thermal camera images might also be very indicative if you have a resource available locally for that work as to whether there is any insulation at the top of the rafter bays anymore.
Ok, just some thoughts.
Yes, I was considering both affordability and cold-weather performance in proposing EPS. Hadn't considered a stackup, so that's interesting to me. Affordability is driving most of our decisions at this point, and so what I'm looking for is a solution that improves the performance for the current roof - doesn't solve every possible issue and create a Super Roof - and at the same doesn't cause any moisture issues. Thanks so much for your thoughts and feedback. It's really helpful!
I should note, the ceiling assembly on the underside of the rafters is as follows: 1x3 furring strips with 3/8" rock lath, then applied 1/2" acoustical tile, which have since been covered with T&G. Presumably the existing roofing system "works" because the rock lath provides an air seal underneath the roof sheathing, is that right? Thanks again!
Maybe. If everything you find when you strip the roof is dry without signs of wetting, if you don't have ice dams, etc. you may have an airtight ceiling.
What climate zone are you in? Churches sometimes can deviate from the rules as they are intermittently occupied (keeping indoor humidity down) and often not cooled or heated to normal room temperatures during the week . If the 3" of EPS is ok in your climate zone to hinder condensation on the bottom of the deck, I'd suggest you plug up the soffit vents.
Thanks for your input Joel. The intermittent occupancy is definitely a consideration.
The church is in zone 5a.
That's a good reminder Joel. I jumped to the conclusion that this was a church being remodeled into a home.
So far you're both recommending sealing up the soffit vents and Brian is suggesting air-sealing the connection where the roof meets the existing (masonry) wall. That will have to be done from the outside, when the existing soffits and fascias at the eaves are removed.
I'm happy to take product recommendations. :)
Also, do either of you - or does anyone else - think differently about this knowing that the church is Zone 5a? Thanks!
In addition to the cathedral ceiling link Brian posted, this one is helpful: https://www.greenbuildingadvisor.com/article/how-to-install-rigid-foam-on-top-of-roof-sheathing
If you have an airspace under your current roof sheathing, in addition to closing off the air access points (soffit vents) it's probably worth filling that void with insulation. Is cellulose used much in your area? That can be blown in (dense packed) from the roof deck once the roof is stripped by drilling holes in the rafter bays or prying back a board. Fiberglass could also be blown in.
Assuming you do fill the cavity with insulation, and if your rafters happen to be full dimension (6") you might be looking at something like R-20 below your roof deck. This means that you should technically have closer to R-14 above your roof deck (more than 3" of EPS). The rule of thumb is 41% insulation on the exterior (see the chart in the photo gallery on the above linked page).
As Joel mentioned, this may not hold for an intermittently used church, since its based on estimated indoor humidity levels, which is affected by occupancy habits. But I can't comment on this.
Dana (GBA contributor) or the like might have more precise advice on the foam stack-up. As in, it might be possible to use Polyiso on the bottom, topped with eps to get to your target R-value while still remaining below 3" total of foam (I'm fairly sure you could but I didn't do that math). You may even be fine with all polyiso in 5a, but don't quote me.
I would echo Brian too in the importance of sealing off the vent channel at the framing layers and not just at the soffit vent, which could leave all sort of leakage paths through the soffit materials.
Oh and... its hard to know if the rock-lathe is really that air-tight, so it would probably be worth air-sealing your entire roof deck once stripped down. This could be with an air-impermeable membrane, usually a peel and stick product like Ice and Water. (though I'm also curious what others suggest as an ideal product for this task that isn't too pricey). If it is a peel and stick, it can be wrapped down onto the walls to bridge your existing vent openings and seal it all up.
Thanks a lot, Tyler!
I have to admit, filling the rafter spaces sounds much harder & more expensive than simply adding rigid insulation on top. Maybe that's not the case. Still, at this point, I would not assume that that's going to happen. ;) What if we filled the rafter spaces *instead* of putting rigid on top of the existing sheathing?
Also, glad to hear there's consensus on sealing of the vent channel if we do add insulation to the top of the sheathing. Although, now I'm not sure if that's the best approach to take here. If our pockets were lined with gold, we'd try to give this little church the best cathedral roof in all the land! ;) But honestly, on the GOOD-BETTER-BEST spectrum, we are solidly looking for GOOD.
I still would like to know people's thoughts on what kind of issues we would encounter if we did what I originally proposed: added 3" of rigid insulation and left the vent channel intact. Would it simply not perform efficiently, or would we be creating moisture issues?
What if we could only do one thing: EITHER fill the rafter spaces with insulation OR add rigid insulation on top. Which would be better?
Thanks again, everyone. Lots of good info here!
The IRC says you should have R-20 above the decking to control insulation in zone 5. I would argue that if your roof hasn't had problems with condensation before, that your plan to add any amount of insulation above the deck should not be a problem. I agree that filling the existing void would be a pain. If you only did that it might work, but maybe that mostly unvented void is somehow helping.
If it were my building, I'd strip to the deck, repair the deck as necessary, add ice and water over the whole surface, then add insulation (in two layers with joints staggered), install plywood, and install underlayment and roofing. The labor for 4" of insulation is no more than 3" so I'd aim for that if I could afford it. There are several advantages of the ice and water, including being dried in immediately. You'll have to decide on fasteners appropriate for the depth of insulation and whether or not you want to try to hit the rafters, which is a good idea. It helps you have a 3/4" deck.
Thank you, Joel. I was inclined to argue that very thing, but wanted to bounce it off people who know more than I! I really appreciate your opinion and input!
Getting the insulation and venting (or non-venting) figured out is my primary concern here, but another question that's popped up: Do we install the stone-coated steel shingles over a radiant heat barrier underlayment instead of felt to improve the R-value of the shingle installation. Felt definitely seems like it's more in-keeping with the GOOD level of roof performance we're shooting for, unless it's a flat-out mistake to use felt. I've not seen or read anything that would lead me to believe it would be. I also haven't investigated cost yet. Product literature states that using a radiant barrier underlayment would move us from a combined R-value of 1.4 to 3.5 using a product like Sharkskin Radiant Barrier. (That's the combined R-value of the air gap under shingles + underlayment.)
Just wondered if any of y'all had some knowledge to drop.
Insulation above the deck without blocking the vents means the rigid insulation will not be doing much. Essentially you are gaining only a very small amount of extra R value as the vent channels bring in cold outside air between the layers making the exterior insulation ineffective.
This setup does work, but won't save you energy.
If you are going the rigid route, you need to seal up the vent channel. Blowing in insulation is usually the best way to do it but blocking the vent openings above the walls and at the ridge could also work although not as well.
For the underpayment, follow the instructions of the metal tile manufacturer. Most are OK over felt, some need a synthetic underlayment. Radiant barrier does very little in this application, it generally is not worth the cost as you would have to strap out the roof to create a gap for the radiant barrier to actually work (gives you around an R2 bump, so mostly not worth the cost). Without a gap, sandwiched between the roof tiles and roof deck the radiant barrier won't do anything.
Thanks a lot, Akos. I understand exactly what you're saying.
re: radiant barriers
The product literature says that the radiant barrier does, in fact, provide a benefit under stone-coated steel shingles, presumably because there is an air gap created under the shingles due to their shape. They supply testing lab results, but I understand you still have to consider the source of the information. Maybe they're playing a trick on us.
It seems like you're on the right track.
The biggest point, which I think you understand, is that the venting needs to be closed off tightly if you're adding or keeping insulation to the exterior.
If you're really trying to do this on a budget, simply closing off the vents with the existing stack-up might be the best bang for your buck, so to speak.
Assuming you want to do a bit more work... could you possibly reuse that foam at least?
Fluffy insulation in the rafters alone likely won't get you the performance of the exterior foam. Adding some fluffy in the rafters in addition to the foam might make sense simply because its generally cheaper than foam. But if it means another specialized contractor on-site and/or you already have the foam, perhaps it doesn't pay off, I can't say.
You might be fine with any amount of rigid insulation above the deck, but if you want to play it safe, you should shoot for 41% or more of the R-value above the deck compared to below. (The R-20 Joel sites is based on hitting this percentage when there is enough total insulation to meet code minimum.)
Thanks for that overview, Tyler.
Here's what I've got at this point:
Strip everything down to the original decking;
Replace any decking that may be deteriorated, leaving the rafter insulation below the decking (balsam wool batts) in place;
Air-seal? By applying peel & stick to the entire roof deck (?);
Apply a 3"-4" stack-up of rigid insulation, using that to also seal the roof-to-wall connection (?);
(btw, a local roofer has said their preference would be to use a 4" polyiso nail-bed product)
Then apply our 1/2" plywood coverboard (if we don't use the nailbed insulation);
Then apply underlayment, including 3' (?) water & ice at the eaves (?);
Then our metal roofing panels.
And finally, and I know you all keep saying it, but really? No venting in the soffits and no vent channel? (that's why I questioned the above step, too, that seals of the wall-to-roof connection)
Still plenty of question marks, I guess, so bear with me.
My gut is still nervous about what happens to any water vapor that goes up through the ceiling into the rafter spaces. I'm imagining a cold day, the sanctuary has sat empty and kept at 60 deg. most of the week, and then come Sunday morning, we shock the system, crank up the heat and add 100 people who are mostly singing. Right now, the rafter spaces with the original balsam wool batts are connected to a (questionably effective, I suppose) vent channel. But what happens when we seal that off? Is the fact that we have much better insulation on top of our now-sealed roof deck making it so there's no real potential for a problem? Does this whole system only work if we have a well-sealed ceiling?
I'm still very much in learning mode here, so if I'm wrong to have this concern, I will gladly accept the scientific explanation for why that is.
Thanks again for sticking with me here!
As far as the venting, I think you're missing a crucial piece of the puzzle when it comes to your understanding of the risks.
The reason it works not to vent is by way of keeping the roof sheathing warm enough (via the exterior insulation) to not be a condensing surface. The physics at play is that warm air holds more water vapor. When all those church-goers are there singing, their breath, perspiration, etc. adds humidity to the air according to the ability for that air (warm) to hold it. When that air contacts a surface that is cold (below dew point) that moisture cannot be held in the air and therefor transfers (condenses) onto/into the material. In this case, the roof sheathing, if it is too cold.
I'm not sure if the dynamics of extreme temp swings in the church create odd conditions in this way. Perhaps someone else can comment if they see an issue there.
The purpose of the 41% exterior insulation I've cited is to ensure that the sheathing stays warm enough, i.e. above average yearly dew-points based on typical indoor humidity level.
https://www.greenbuildingadvisor.com/article/understanding-dew-point
Might be helpful. Also:
https://www.greenbuildingadvisor.com/article/combining-exterior-rigid-foam-with-fluffy-insulation
There's lots of information on these concepts here and a place like Buildingscience.com
Thank you! And you're right, while I do understand the whole, "water vapor condenses on a cold/below dew point surface," I do NOT understand how you know what the dew point IS under different conditions and how it might fluctuate in a space like this. So, hopefully I'll brush up on that -- thank you so much for the resources -- and then I'll be good to go.
"Is the fact that we have much better insulation on top of our now-sealed roof deck making it so there's no real potential for a problem? Does this whole system only work if we have a well-sealed ceiling?"
Pretty much, yes, and yes. Keep in mind, that if you KEEP your venting below your nice expensive exterior insulation, the value of that insulation is being undermined by cold exterior air getting in beneath it. Don't do it.
Although the ceiling plane might arguably be the best location for an air tight layer, you can do it at the roof sheathing layer since you will have access to it during your project.
This is perhaps even more true if you're using nailbase the full thickness of your exterior insulation since the layers won't be staggered and air that works its way through the roof sheathing and nailbase cracks CAN be reason for concern (condensation at the joints in the top layer of the nailbase). So yes, work to make your sheathing layer air tight. Or at the least, if you're using staggered layers of foam, tape the first layer of foam, but I don't think this would be considered as robust.
Thank you!