Anyone have experience with CCSPF with HFO blowing agent?

An improved blowing agent for ccSF applications (“Demilec Spray Foam”: 2019 Feb 28 Green Building News) has had favorable comments since its publication, but I’m wondering if others have had additional field experience with the product since then.
We are in Boston area (zone 5)
Our intended use is interior flash coat for ZIP walls and roofing panels, to be followed by oc spray or net and blow cellulose. The idea here is to use the the cured flash coat to retain all the positive features of HFC (thermal, structural, and air/water vapor barrier, while adding the more positive climate-friendly features of HFO.
Any new information on application, pricing, or curing gotchas from users?
(I did see Paul Pfeiffer’s comment on softness of Heatlok Soy 200+ foam in the referenced article, but that might not apply to the Heatlok HFO High Lift ).
Looking for advice from the front-runners using this product.
Thanks in advance.
GBA Detail Library
A collection of one thousand construction details organized by climate and house part
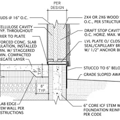
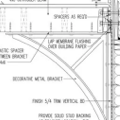
Replies
In a zone 5 location there's far better (financial & environmental) bang for buck to use just open cell foam in framed walls. An inch if 2lb foam uses the same amount of polymer of 4" of half-pound foam.
What is the rationale for using it in walls? In zone 5 rainscreened siding or inherently back ventilated siding is sufficient for protecting OSB sheathing like ZIP using only Class-III vapor retarders ( or smart vapor retarders) on the interior, and the assembly would have more drying capacity if the closed cell foam were omitted.
At the roof deck at least 40% of the total center cavity-R would have to be closed cell foam to have sufficient dew point control, not just a flash-foam.
There's nothing particularly "green" about 2lb foam, even though HFO blowing agents are dramatically less damaging than HFC blowing agents.
Dana,
On this subject, in another thread, you previously said "As long as it's reasonably air tight to the interior (5.5" of open cell foam is extremely air tight) the moisture risk to the sheathing is very low when using standard interior latex paint as the vapor retarder." questions:
1. In the comment above, you indicate that rain screened "siding is sufficient for protecting OSB sheathing like ZIP using only Class-III vapor retarders..." Can we assume that this would be also true of plywood sheathing?
2. Assuming the Class-III vapor retarder is latex paint (over gypsum board on 2x6 studs with 5-1/2" open cell foam), is any special treatment or sealing required to seal any gaps or penetrations around outlets, and at perimeter of gypsum board at floor and around windows and doors (which would typically be covered with wood trim)?
3. Regarding the roof deck, to achieve R49 with foam, you would need 7,5" of closed cell.. or 5-1/2" of closed cell + 3.75" open cell for a 2x10 roof... or 3" closed cell + 8-1/4" open for 2x12 roof. For a 2x10 roof, do you think it worthwhile to split the foams for a 2x10 roof or just go all closed cell? For a 2x12, it looks worthwhile to split.
And thanks for teaching me the difference between "absorption" and "absorption." The dictionary helped also. I'd never even realized there was such a word. But one thing, even with adsorption on the sheathing surface, doesn't absorption then occur if the drying is to the exterior?
>"1. In the comment above, you indicate that rain screened "siding is sufficient for protecting OSB sheathing like ZIP using only Class-III vapor retarders..." Can we assume that this would be also true of plywood sheathing?"
Yes. Plywood is more vapor permeable than OSB, and able to pass-through more moisture if there's a rainscreen.
>"2. Assuming the Class-III vapor retarder is latex paint (over gypsum board on 2x6 studs with 5-1/2" open cell foam), is any special treatment or sealing required to seal any gaps or penetrations around outlets, and at perimeter of gypsum board at floor and around windows and doors (which would typically be covered with wood trim)?"
Half pound open cell foam is already inherently air tight, so penetrations of the wallboard, sheathing or framing don't need further detailing. Seams between doubled-up framing like top plates, jack studs, headers etc, or between the bottom plate and subfloor still need to be caulked though. Those long skinny holes are much bigger than they look.
>"3. Regarding the roof deck, to achieve R49 with foam, you would need 7,5" of closed cell.. or 5-1/2" of closed cell + 3.75" open cell for a 2x10 roof... or 3" closed cell + 8-1/4" open for 2x12 roof. For a 2x10 roof, do you think it worthwhile to split the foams for a 2x10 roof or just go all closed cell? For a 2x12, it looks worthwhile to split."
In new construction making the split at the roof deck layer, with rigid foam board above the roof deck and open cell or fiber under the roof deck. That keeps the structural roof deck warmer & drier, with a much better path to drying. At 7.5" many closed cell foams are getting close to Class-I vapor retarder (= true vapor barrier) territory.
>" But one thing, even with adsorption on the sheathing surface, doesn't absorption then occur if the drying is to the exterior?"
Adsorption isn't a surface phenomenon at the macroscopic sheet of sheathing, but rather in/on the microscopic wood fibers, deep into the wood. Water molecules are very small, and can can form adsorb layers even on the interior of the hollow structure of cellulosic fibers. So while it's on the surfaces of the fiber at the microscopic level, it's not on the surface of the sheathing in a macroscopic sense. Water can and does move through wood as adsorb, not liquid.
The term "absorption" usually refers to liquid water filling interstitial spaces of larger structures, capable of remaining in place due to surface tension of the liquid, as happens with the visible macroscopic holes in a sponge, or spaces between threads of a rag.
Best, most succinct explanation of the two terms--adsorbed and absorbed--in porous building materials from this BSC resource by John Straube (BSD-138: Moisture and Materials):
"Many surfaces in contact with water vapor molecules have the tendency to capture and hold water molecules because of the polar nature of the water molecule; this process is called adsorption. These materials are called hydrophilic, whereas materials that repel water are called hydrophobic. Most building materials are hydrophilic. As water vapor molecules in the air adsorb to the internal surfaces of these materials, the materials' water content increases significantly. Such materials are described as hygroscopic. Materials such as glass, plastic, and steel do not have internal pores and therefore are not hygroscopic — they do not pick up moisture from water vapor in the air. (Desiccants are a special type of hygroscopic material. They can absorb a very large amount of moisture, typically several times their dry weight at high relative humidities).
When a material has adsorbed all the moisture it can, further moisture will be stored in the pores and cracks within the material by capillary suction, or by absorption. For example, wood will adsorb vapor from the air up to approximately 25 or 30% moisture content at 98% relative humidity, but fully capillary saturated wood wetted by liquid water may hold two to four times this amount of moisture. Once a material is capillary saturated it will generally not be able to store any more moisture. When this moisture content is exceeded, a material is called over-saturated, and no more water can be wicked into the material and drainage mechanisms, if available, will begin to remove the excess moisture.
In summary, liquid water is absorbed into capillary pores, and significant amounts of water vapour can be adsorbed to the surface of pore walls."
Peter